Faith and confidence key for young women in Manufacturing
By Staff Report January 16, 2025 12:06 pm IST
In this edition of the OEM Update series on women in manufacturing, presented with WIMA—Women in Manufacturing and Associated Industries, Vikas Marwah, CEO of Lumax Auto Technologies, takes the spotlight. Neelam Pandey Pathak, Founder and CEO of Social Bay Consulting, talks with Marwah about the challenges women face in manufacturing workspaces.
Neelam: The Indian manufacturing sector has lower women’s participation, at around 18%, compared to the global average of 28%. The skill gap significantly contributes to this disparity, with 40% to 50% of women lacking industry-relevant skills. According to World Bank data, many women do not have access to skilling programs, which has led to about 20% to 25% of women in the mid-career range leaving their manufacturing careers. Why is it critical for women to develop their skills, and what global and local impacts does this have in India, particularly in the manufacturing sector?
Vikas Marwah:
We must promote diversity, equity, and inclusion policies that complement government programs that assist women’s skill-building programs if we want to support women in manufacturing. Upskilling women in the workforce should be based on their skills and abilities rather than only being seen as a moral, ethical, legal, or compliance need. We may begin encouraging women’s participation right away by consistently hiring them for operational engineering positions and diploma engineering programs.
Women play a crucial role as primary caretakers at home, and their responsibilities often begin early in life. In India, a deeply entrenched patriarchal mindset creates the expectation that women should prioritise family duties. However, if women are able to join the mainstream workforce during their formative years—ideally a five- to eight-year period before settling into marital life—they can adapt and excel in the professional environment.
Companies, industry sectors, and professional organisations need to establish supportive policies to facilitate and ease this transition. These measures will enable women to work in safer, more accommodating workplaces.
Neelam: From 2022 to 2023, the women’s participation used to be 25-30%, and now it is around 18 to 23%. So, what challenges are women facing in accessing the right skills and job opportunities in manufacturing?
Vikas Marwah: I have worked in both the service and manufacturing sectors. Manufacturing jobs have clearly defined working hours. However, the shop floor often presents unique conditions that are predominantly male-dominated, especially in the automotive sector, where many positions are physically demanding. This environment can pose challenges, especially given societal and domestic responsibilities, safety concerns, and the fact that there are generally more men than women on the shop floor, which contributes to gender disparities.
Women still hesitate to enter the manufacturing sector, even though changes are underway. For example, in my own company, we have about an 18% female workforce, but we ideally want that number to be closer to 30% and even more. Our 18% representation at Lumax Auto is primarily on the shop floor, which has increased partly because our manufactured parts and operational processes do not require physically demanding work. We focus more on assembly operations than heavy manufacturing, and we are increasingly moving towards more automated assembly processes.
We operate in states that have successfully developed an automotive ecosystem, such as Haryana, Maharashtra, Gujarat, Karnataka, and Uttarakhand. Within these states, we have achieved an 18% female workforce, which we aspire to increase to around 30%.
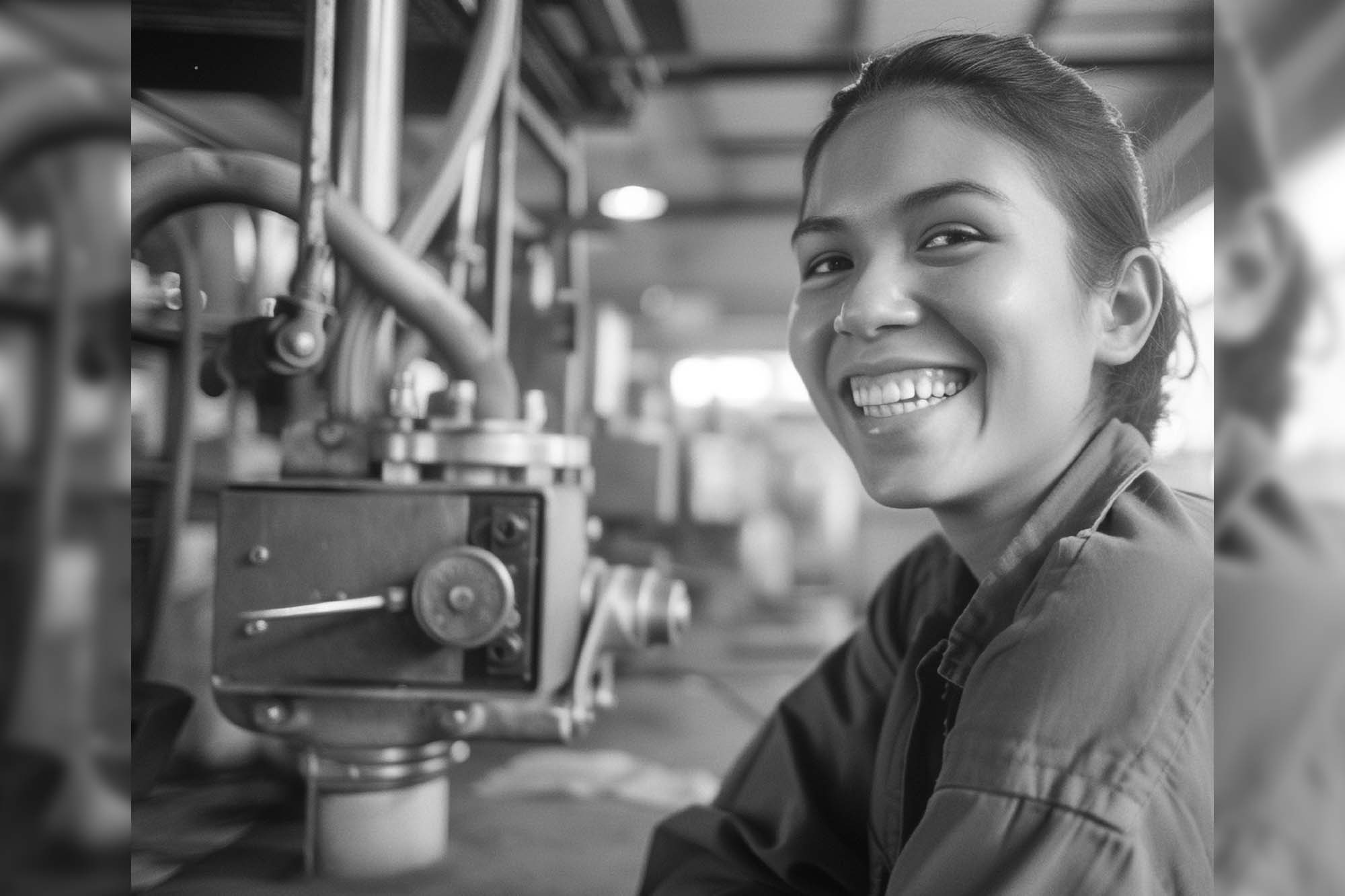
The initiation of women into the automotive industry must also consider the number of women in senior leadership positions within corporate organisations. This situation is not due to corporations or the manufacturing sector not wanting women to participate but because many women are often pursuing careers in service industries, multinational corporations, or other non-automotive manufacturing organisations. For example, OEMs serve as our primary customers, and it’s worth noticing and recognizing the opportunities available to further promote diversity in senior leadership roles across the manufacturing and procurement hierarchies.
From a business perspective, we need to make the automotive industry more attractive to women by giving them a sense of empowerment. We are actively working to encourage more women to consider careers in the automotive sector, particularly on the corporate side. The increased representation of women leaders at the corporate level will pave the way for more women to join at every level and function. Women envision their own career paths when they observe others thriving in top positions. Instead of restricting them to blue-collar jobs or technical positions on the production floor, it is essential to demonstrate that a career in the automobile sector may rise to positions such as Vice President, Business Heads and higher.
Neelam: What initiatives is Lumax Auto implementing to help women enter the workforce and have longer careers in the automotive industry?
Vikas Marwah: We have prioritised gender sensitisation with a comprehensive POSH (Prevention of Sexual Harassment) program initiated about a year ago. We made this program mandatory for around 3,000 to 4,000 employees, ensuring that no one could advance their workflow or access IT systems without completing this awareness training and assessment. This important module was inclusive, reaching everyone from the MD and CEO to entry-level staff.
In addition, we have established supportive policies for women during every phase of their careers. Women taking maternity leave will automatically receive a performance rating of “Meeting Expectations” (ME). This approach ensures that their appraisals and potential increments remain unaffected by their time away, promoting a culture of fairness and inclusivity.
We have taken significant steps to enhance our policies for new mothers who must travel for work, offering a nanny allowance. Additionally, we provide Special On Duty (ODs) and leaves for women to help them better manage their work-family responsibilities. We have introduced the Springboard policy, also highlighted on our website. This policy allows women who have taken a sabbatical or temporary break from work to reintegrate into the workforce. We are open to hiring them on a retainer basis for up to one year, depending on the projects they are interested in and their expertise. This means that women returning from sabbaticals, even those from different industries, are welcome to join us. Our performance management system has been updated to ensure greater acknowledgement of female contributions.
Neelam: Future Skills on AI, IOT is becoming an integral part of the automotive industry, and this trend is true for many other industries, especially with the emergence of AI and data technologies. As we look towards the future, how do you see the role of women in this industry evolving, particularly with the necessary skills?
Vikas Marwah: Historically, there has been a mental block regarding women in manufacturing roles, which are often perceived as physically demanding. However, even the men in these roles do not rely on physical strength anymore; they use cranes and automated systems as assistance.
Initiatives like the National Skill Development Corporation (NSDC) promote various programs. Under the Skill India mission, Industrial Training Institutes (ITIs) are now focused on building essential skills for women. The National Apprenticeship Scheme also addresses this need without insisting that women take on the most physically demanding jobs.
At companies like Tata Motors, Ola Future Factory, and Ashok Leyland, all-women workforces are now operating on heavily automated production lines. The expectations for these roles include a basic understanding of hand-eye coordination, the ability to read and understand dashboards and monitors, and the ability to handle tools effectively.Establishing large R&D and engineering centres has become critical for the auto component sector due to the emergence of new technologies. These R&D environments differ greatly from traditional manufacturing settings, and we have strategically located our R&D centres outside of manufacturing spaces. This shift is essential because we are not just competing with other auto component manufacturers but also tech giants like Accenture and Microsoft for top talent.
We are innovating through rapid prototyping and applying AI to develop software and 3D designs before formal production.
As we promote self-empowerment in STEM fields, R&D centres aim to have more than 30% female participation within the next three years. This increase in female representation will likely lead to more women in leadership positions within automotive manufacturing organizations.
In three to five years, we could see a female CEO of a major technology firm within the auto component sector. Among the top 20 auto component manufacturers, very few women are in CEO positions.
Neelam: There are many graduates, particularly in technical fields; what advice would you give to young women entering Manufacturing industry? How can they pursue a longer and rewarding career in this field?
Vikas Marwah: For young women entering the manufacturing sector, particularly automotive, having faith and confidence in their choice is essential. The automotive industry is resilient and does not typically experience attrition like tech-based businesses. The variable or contractual workforce is typically the most impacted during industry downturns. The automotive and manufacturing fields offer long-term sustainability and stability. While other industries might be vulnerable to market fluctuations and arbitrary decisions, the automotive manufacturing sector remains a safe and predictable place to work.
Additionally, the revolution in automotive manufacturing has only just begun, with an increasing focus on internal improvements in R&D. The design and development work happening in the automotive sector is remarkable, and the strong push for localisation by OEMs is enabling the development of advanced vehicles in India. Many parts are now being exported even to countries like Japan, which was once the epicentre of manufacturing.
Manufacturing is opening up significant opportunities in support functions that are moving away from traditional paradigms in HR departments. Historically, these departments have focused mainly on timekeeping and payroll. However, there is a stronger emphasis on attracting the right talent, investing in L&D, development of employees, and creating a positive and inclusive work environment that aligns with the organisation’s ideology.
Human Resources and Finance are evolving, and Information Technology is becoming increasingly critical since these fields are becoming more data-driven. The reliance of manufacturing and automotive on data and IT has increased by more than 60% in the last five to seven years, and this trend is likely to continue. New developments such as Industry 4.0, artificial intelligence, the Internet of Things, and machine learning offer vast opportunities for women in advanced and developed economies.

One of the obstacles that historically has deterred women from pursuing careers in manufacturing and automotive is the perception of limited opportunities for growth. However, this perception is changing. For at least the next five years, there will be a notable constraint on resources, and we will continue to combat the misconception that these industries do not provide a conducive environment for women to grow and thrive.
We acknowledge that we need to improve our outreach efforts to change this narrative. Collaborating with industry bodies and academic institutions is crucial. As a result, campus placements are expected to increase as the traditional methods of headhunting and resource acquisition no longer meet our needs.
Neelam: How do you see platforms like WIMA collaborating with industries or the manufacturing sector to support individuals and the industry?
It’s commendable that WIMA is taking the lead in identifying and bridging the skill gaps among women in manufacturing. There are five out of ten women in the cluster of job market but we can hire about 20 to 30% of them in our organization. Platforms like WIMA can collaborate with the industry to identify the in-vogue manufacturing needs and we can start with improving the right assembly processes in electronic-based environments, such as manufacturing PCBs, SMT processes, ESD control rooms, and clean rooms.
Additionally, platforms like WIMA can address external factors affecting women’s employment, such as the safety of work environments and transportation systems for these women. There’s a significant gap in the support from local bodies, including the government and police, in communicating the right messages regarding safety. For instance, do areas like Manesar and Chakan have all-women police stations? Manesar and Chakan are two major hubs for automotive component manufacturing in the country, and collaboration is key to sending the right message and fostering a suitable environment for women in the workforce.
About WIMA :
WIMA is a one-stop solution designed to empower women with industry-relevant upskilling, mentoring, coaching, and networking opportunities, ensuring access to the right employability across all positions and geographies ( Urban & Rural).
WIMA’s goal is to foster longer, successful careers and enable women to achieve a safer, sustainable livelihood.
For organizations, WIMA offers customized DEI (Diversity, Equity, and Inclusion) Hiring, Skill Analysis programs to enhance the retention & increase of women in the workforce, driving meaningful impact in the Manufacturing and Allied sectors
To connect to WIMA one can visit: www.socialbay.co.in/wima or write on wima.womeninmanufacturing@gmail.com or visit Social Media our linkedin page :
https://www.linkedin.com/company/wima-a-platform-for-women-in-manufacturing/?viewAsMember=true
Cookie Consent
We use cookies to personalize your experience. By continuing to visit this website you agree to our Terms & Conditions, Privacy Policy and Cookie Policy.