Cloos prepares the workforce for welding industry
By Staff Report February 1, 2025 4:54 pm IST
Cloos has a core expertise in welding and offers customised automation solutions to meet customers’ specific needs. Simon Mitra, CEO of Cloos India Welding Technology Pvt Ltd., shares how they train the workforce to adapt automation and welding technology.
Could you share insights on India’s rising demand for automated welding systems and how your solutions address this shift?
Welding is our core expertise, which forms the foundation of our services. We offer customised automation solutions to meet our customers’ needs. We assess and determine the suitable welding technology for each client, design the appropriate automation solution, and execute it effectively.
We guarantee seamless implementation at the customer’s site, offering comprehensive training to their personnel. This holistic approach transforms the process into a success story. Our focus is not merely on selling products but on delivering solutions, which requires a skilled and dedicated team.
The industry faces a workforce shortage due to a shortage of people with the appropriate skills. This shortage of skilled workers has created a heightened demand for automation. Unlike a few years ago, when only heavy industries were adopting automation, today, even small-scale shop floors are seeking automation to address the challenges posed by the lack of skilled welders. We offer a diverse range of high-end welding products and solutions to meet this growing demand, catering to heavy-duty and specialised applications.
How do your cobots and robot applications cater to customers with small-batch productions and frequent design changes?
We offer a comprehensive package of cobots and robot applications for customers with batches using 2 to 10 different products or small batch productions with frequent design changes. Cobots offer advantages due to their quick programming, making them ideal for frequent changes in design and data.
After thorough customer analysis and discussion with them, we recommend the cobots or robots package. The cobots offer online seam tracking without a laser camera, making Cloos globally known. Their inbuilt technology provides an advantage for customers, making them a more effective choice.
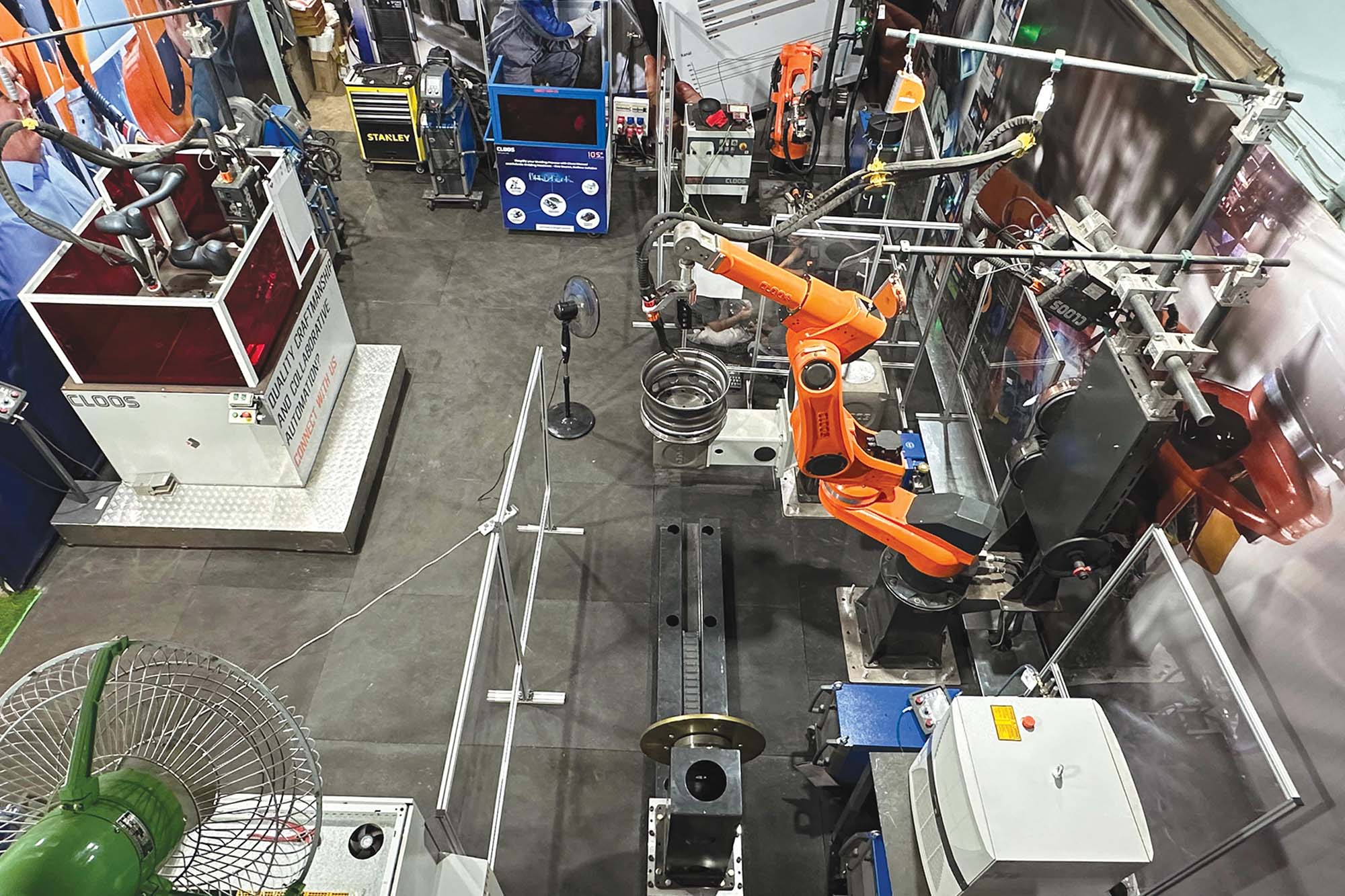
How does Cloos ensure its systems are compatible with Industry 4.0 standards?
Industry 4.0 necessitates a hardware system that can transmit data and be accessed on a single screen, accessible from anywhere. QIROX is our robotics system, QINEC is our welding system, and QNEC is the complete process data bank of welding. We offer industry-ready hardware systems with sensors, and customers can access Cloos C Gate industry 4.0 software on their mobile phones at any point, allowing them to monitor their system remotely. Even if the welder exceeds the set parameters, this software will enable authorities to receive notifications on their mobile phone, and you can ensure the quality. Furthermore, if customers have their software, we can provide the same data in the OPC way. Industry 4.0 software is designed to adapt to the specific needs and circumstances of the customer.
How does Cloos address welding challenges and provide tailored solutions for various industries?Any robotic system’s core strength and heart lies in its welding process. While robots, peripheral devices, and other automation components are crucial, the primary focus when discussing solutions with customers is understanding the welding challenges that can be addressed and delivering the right product based on the Welding Procedure Specification (WPS).
We offer advanced welding processes tailored to various needs, like thin-sheet or heavyduty welding. Our capabilities include precise current and voltage control, and we are pioneers in tandem welding technology. This allows us to achieve continuous deposition rates of 20–30 kg per hour, making us leaders in the field.
We excel in thin-sheet welding with motion welding, achieving travel speeds of up to 4.5 meters per minute on 1 mm sheets. We have gained success in the rapidly growing aluminium industry, particularly in heat exchangers and battery manufacturing. For example, a customer encountered difficulties achieving adequate penetration using conventional methods for a heat exchanger product. We introduced an innovative AC MIG/MAG power source using alternating current technology, resulting in high-quality results for the first time for customers. We have already delivered two systems to this client, and more enquiries are expected from similar industries.
Additionally, our Mix Weld technology addresses the challenges of partial welding in industries dealing with large, immovable products. This process allows seamless switching between pulse and non-pulse modes for effective welding without rotating products into a horizontal position.
How do your training initiatives contribute to the skill development of the workforce?
Training and skill development are important aspects of our approach, as the customer needs to operate the system effectively after we have implemented the solution. Our robotic systems are user-friendly and require specific skills but are designed for ease of use. All operations are controlled via a single teach pendant, eliminating the need to access power sources or components individually. Welding parameters and online seam tracking are fully accessible on one screen.
To ensure smooth operation, we provide training in two ways. First, training is conducted at the customer’s site where our system is installed. Second, we offer additional training at our tech centre in Pune. This facility welcomes customers, college students, and institutional trainees, allowing us to share knowledge and build expertise. This approach helps run the systems and make informed decisions about robotic welding solutions.
Our training sessions aim to educate customers and potential users on the important factors to consider when choosing the right robotic welding system. We encounter trainees, customers, or engineers—they often realise during the training that previous decisions about automation were misguided due to a lack of knowledge about available technologies and options during training. Through our programs, users gain the understanding needed to make effective decisions. Our training aids current robotic system users and those considering automation by enabling them to select suitable solutions for their requirements.
Cookie Consent
We use cookies to personalize your experience. By continuing to visit this website you agree to our Terms & Conditions, Privacy Policy and Cookie Policy.