Modernise wastewater systems for sustainable manufacturing
By OEM Update Editorial April 30, 2024 7:31 pm IST
Anil Sethi, Chairman of Pump Academy, emphasises the crucial role of efficient wastewater treatment in manufacturing operations. Industries can enhance environmental sustainability and operational efficiency by offering inventive water utility solutions, leveraging advanced technologies, and complying with regulatory standards.
What is the importance of effective wastewater treatment in manufacturing processes?
Efficient wastewater treatment in manufacturing units is critical for environmental sustainability and regulatory compliance. Manufacturers can effectively remove contaminants from wastewater streams by implementing advanced technologies such as biological treatment, membrane filtration, and chemical precipitation. In India, industries should comply with the Zero Liquid Discharge (ZLD) policy, introduced in 2015. It aims to address water scarcity and pollution challenges by mandating industries to treat and recycle their wastewater entirely, leaving zero discharge. Under this policy, industries should adopt advanced treatment technologies to treat wastewater and recover resources such as water, salts, and other valuable materials.
Recycling and reusing treated water conserves resources, reduces discharge volumes, and minimises environmental impact. The active monitoring and maintenance of treatment systems ensure optimal performance and regulatory adherence. Overall, prioritising efficient wastewater treatment in manufacturing processes is essential for minimising pollution and promoting sustainable operations. Although ZLD was associated primarily with industries, there has been a growing recognition that it should extend to Indian cities as well.
What are the challenges in managing water usage and wastewater treatment, particularly in regions with limited water availability?
Managing water usage and wastewater treatment in manufacturing facilities presents several challenges.
Manufacturing plants in areas with limited water availability need help obtaining enough water for production and ensuring proper wastewater treatment. Industries such as chip and semiconductor manufacturing require pure water for precise production processes. Even the slightest impurities can result in defects and reduced functionality during production.
Manufacturing processes often require ultra-pure water, leading to high water consumption. Managing and reducing water usage while maintaining production efficiency is a constant challenge. Ensuring consistent water quality is non-negotiable in several cases. The manufacturing process gets stopped due to water scarcity. The volume and composition of wastewater generated by manufacturing processes can vary, making it challenging to treat them effectively. Contaminants such as heavy metals, organic compounds, and chemicals require specialised treatment methods.
Compliance with ZLD and other environmental regulations governing wastewater discharge is challenging for manufacturing facilities. Meeting discharge limits for pollutants and ensuring compliance with regulatory standards necessitates substantial investment in advanced treatment technologies and monitoring systems. Deploying and sustaining wastewater treatment systems can lead to operational costs, and effectively managing the balance between treatment expenses and production costs while staying competitive in the market presents an ongoing challenge. The issue becomes more critical for small manufacturing facilities as they lack the infrastructure and resources to implement advanced wastewater treatment technologies.
How does Pump Academy contribute to addressing the challenges in the water sector?
Pump Academy Private Limited addresses critical issues related to the performance, energy efficiency, and maintenance of high-capacity pumping systems. These systems play a crucial role in water and wastewater applications, and their efficient operation is vital for the water sector.
Pump Academy’s flagship product, iPUMPNET, is a groundbreaking invention that aims to revolutionise the operation and maintenance of pumping stations. By monitoring key performance parameters and implementing intelligent control algorithms, iPUMPNET can improve the overall efficiency of pumping stations by up to 35 percent. It also helps reduce energy consumption by 25 percent, resulting in significant cost savings for industries.
Pumping machinery is critical for water supply and wastewater treatment management and inefficient operation. Improper maintenance can lead to premature wear and tear, leading to the high cost of replacement. Pump Academy’s solution aims to enhance the total lifespan of pumping sets by approximately 50 per cent by optimising their operation and maintenance while reducing the overall lifecycle costs by up to 45 per cent. iPUMPNET’s real-time monitoring and predictive maintenance capabilities intend to eliminate downtime virtually, ensuring continuous and reliable operation of pumping stations. The innovative IIoT-based solution reduces carbon footprint, thus helping industries and utilities with stringent environmental compliance.
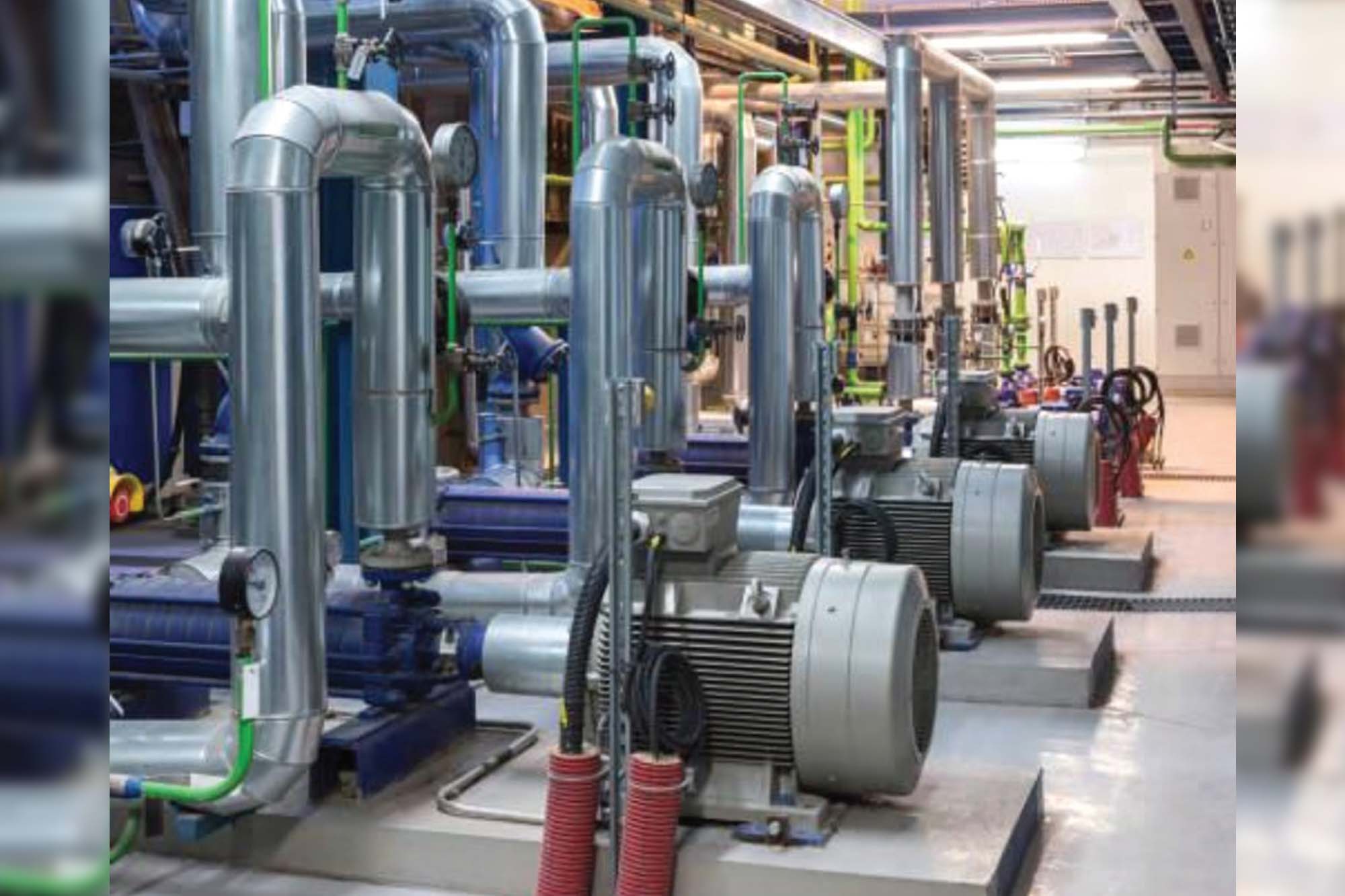
How can manufacturing plants effectively select water treatment methods aligning with the initial water quality and desired outcomes?
Manufacturing plants should select water treatment methods depending on the initial water quality and the desired outcome. Various technologies are available for treating wastewater and chemical discharge. Industries must assess the characteristics of the effluent, pinpointing pollutants like heavy metals, organic compounds, and suspended solids.
Consideration of regulatory requirements and discharge standards is essential, aligning with local or national regulations governing effluent discharge limits. Assessing the chosen technology’s removal efficiency and effectiveness, reliability, robustness, and operational requirements is crucial, especially regarding existing treatment infrastructure.
Moreover, evaluating energy requirements and operational costs, including the consumption of chemicals, additives, or other resources necessary for the treatment process, is paramount. Exploring resource recovery or reuse opportunities within the treatment system while reducing overall carbon emissions within permissible limits is also advisable. Choosing a treatment technology to meet future needs is advised, guaranteeing sustainability and flexibility in the long run.
In your opinion, what role do technological advancements play in improving wastewater treatment efficiency and effectiveness?
Technological advancements play a crucial role in improving the efficiency and effectiveness of wastewater treatment processes. Advanced treatment technologies, such as membrane filtration, advanced oxidation processes, and electrocoagulation, offer more efficient and effective removal of contaminants from wastewater than conventional methods. These technologies enable better removal of pollutants, including organic compounds, heavy metals, and pathogens, resulting in higher quality treated water.
Advanced monitoring systems and sensors provide real-time data using diverse metrics like flow rates, pollutant levels, pH, and temperature. This data aids automated control systems in optimising treatment processes, regulating chemical dosages, and sustaining ideal operational conditions. Real-time monitoring allows for the early identification of process disturbances and facilitates prompt corrective measures, thereby enhancing overall treatment effectiveness.
Energy-efficient pumps, motors, and aeration systems help reduce energy consumption in wastewater treatment plants, enhance energy sustainability, and reduce operational costs. Advanced treatment technologies make it easier to recover valuable resources from wastewater, such as nutrients (nitrogen and phosphorus), biogas (methane), and water, for reuse. Modular and mobile wastewater treatment systems fit with advanced technology and offer flexibility and scalability, allowing for quick deployment and adaptation to varying treatment needs.
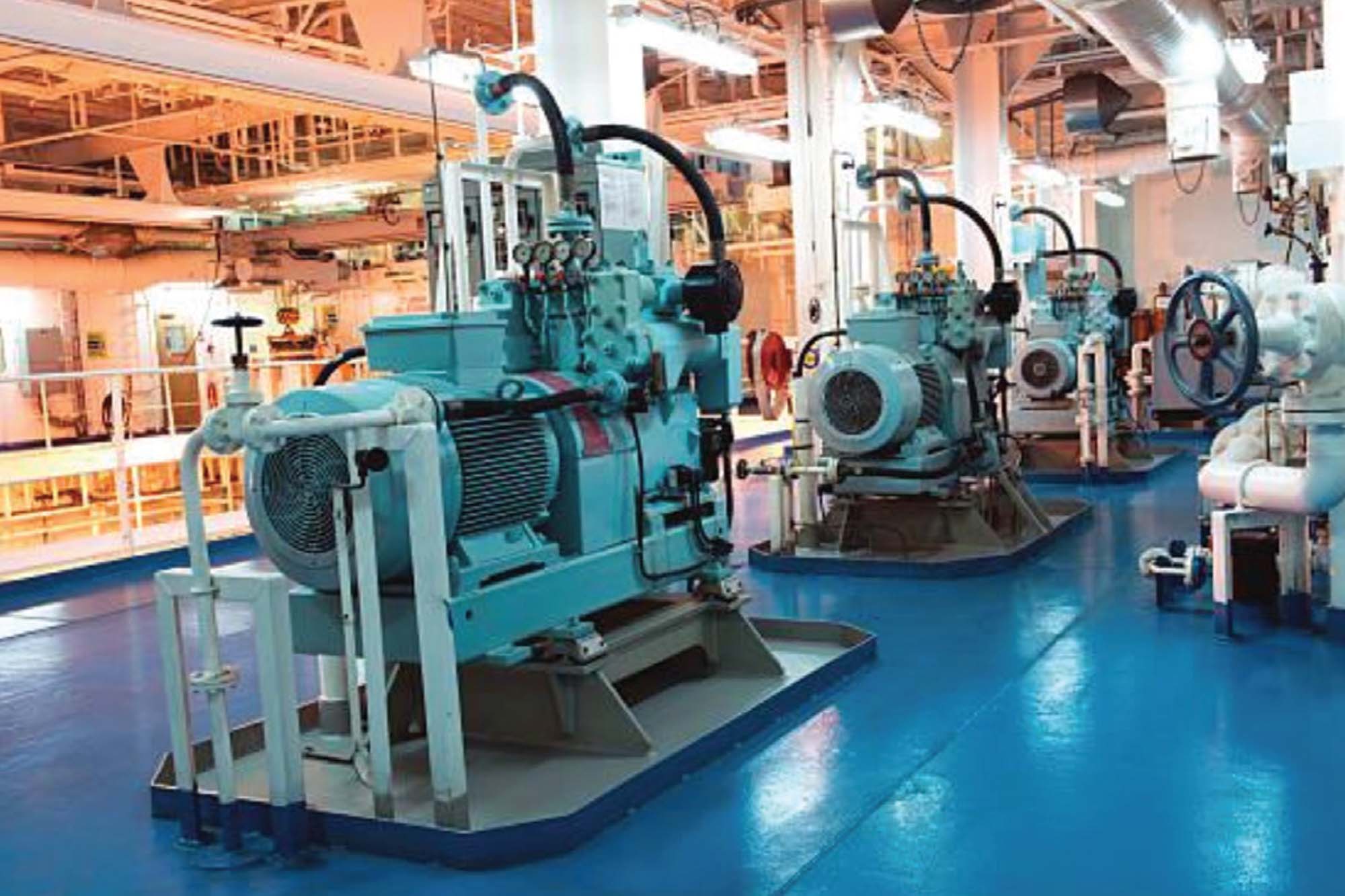
How do manufacturing facilities enhance water sustainability for better output?
Water sustainability is vital for manufacturing facilities and industrial operations, as water is a crucial resource in various manufacturing processes, cooling systems, and cleaning operations. Ensuring sustainable water management practices is essential for maintaining business continuity, reducing environmental impact, and promoting long-term resource availability.
Implement water-efficient technologies and practices to achieve better water sustainability. These include utilising low-flow fixtures, water recycling and reuse systems, and optimising processes to reduce overall water consumption in manufacturing operations. Adopting advanced wastewater treatment technologies to treat and recycle wastewater for reusable water recovery is crucial. Zero Liquid Discharge (ZLD) systems play a significant role in conserving water resources by maximising water reuse and minimising discharge volumes.
Implementing a circular water management approach entails continuously recycling and reusing water in industrial processes, thereby minimising freshwater intake and wastewater discharge. Moreover, implementing measures to reduce the overall water footprint of manufacturing facilities, including direct and indirect water consumption throughout the production process, can significantly contribute to long-term water sustainability.
Cookie Consent
We use cookies to personalize your experience. By continuing to visit this website you agree to our Terms & Conditions, Privacy Policy and Cookie Policy.