Lower costs and higher productivity for shot peening processes
By Staff Report August 9, 2024 6:26 pm IST
Shot peening, the “hammering” of workpieces with precisely defined blast media, is an indispensable operation in industries such as automotive and aerospace. By inducing residual compressive stress into the workpieces, shot peening substantially improves their long-term resistance against tensile and bending loads.
The process is used for treating toothed steering and transmission components, as well as for springs, drive- and crankshafts, and all kinds of turbine blades. A significant advantage of the shot peening operation is that the component weight can be reduced without impacting its mechanical load capabilities. This is particularly beneficial for electric vehicles because it increases their operating range and reduces energy consumption. E-mobility frequently necessitates changes in manufacturing processes due to altering workpiece structures and shapes. Moreover, the customers demand significantly higher energy, resource, and cost efficiency. In other words, improvements in productivity and sustainability are required. Rösler provides comprehensive support for such optimisation projects.
Lower energy consumption by using turbines
Compressed air blast systems have been the dominant shot-peening tools. It is for consistently achieving the specified residual compressive stress values. A downside of the compressed air method is that it requires abundant energy. Today, innovative technical improvements in turbine technology allow the precise and high-quality shot peening of a broad range of components with energy-efficient and highly productive turbines. For many peening applications, costly compressed air blast systems are no longer required. The most important factors to be considered in peening operations are the workpiece shape and size, the peening results, and the blast media. Based on these factors, Rösler runs computer simulations of the blast pattern and the entire process. Actual peening trials follow the Customer Experience Centre (CEC) simulations. Since the CEC has a broad range of turbine and compressed air blast systems, the shot peening trials can be conducted under actual production conditions. With an in-house X-ray diffractometer, the peening trials can be quickly evaluated to determine which process parameters and blast media will generate the required results.
A joint optimisation project between a leading European automobile manufacturer and Rösler resulted in 30 percent energy savings and a 50% increase in shot blast capacity. Based on the convincing project results, the same customer purchased four peening machines equipped with turbines.
Less equipment wear and higher productivity
Sometimes, reviewing the existing shot blasting parameters can help the entire peening process. Once they are established, the process parameters are frequently no longer questioned. Such carelessness can result in high equipment wear and unused potential for process improvement.Perfectly calibrated process parameters, including the optimal media selection, guarantee high peening qualities, less equipment wear, and low operational costs. Retrofitting can be the right solution if a review of the shot blasting parameters in an existing machine is insufficient. This includes upgrading the machine with more productive components, such as more powerful turbines or workpiece fixtures for new or modified workpieces. The optimisation of the blast pattern must always be one of the considerations.
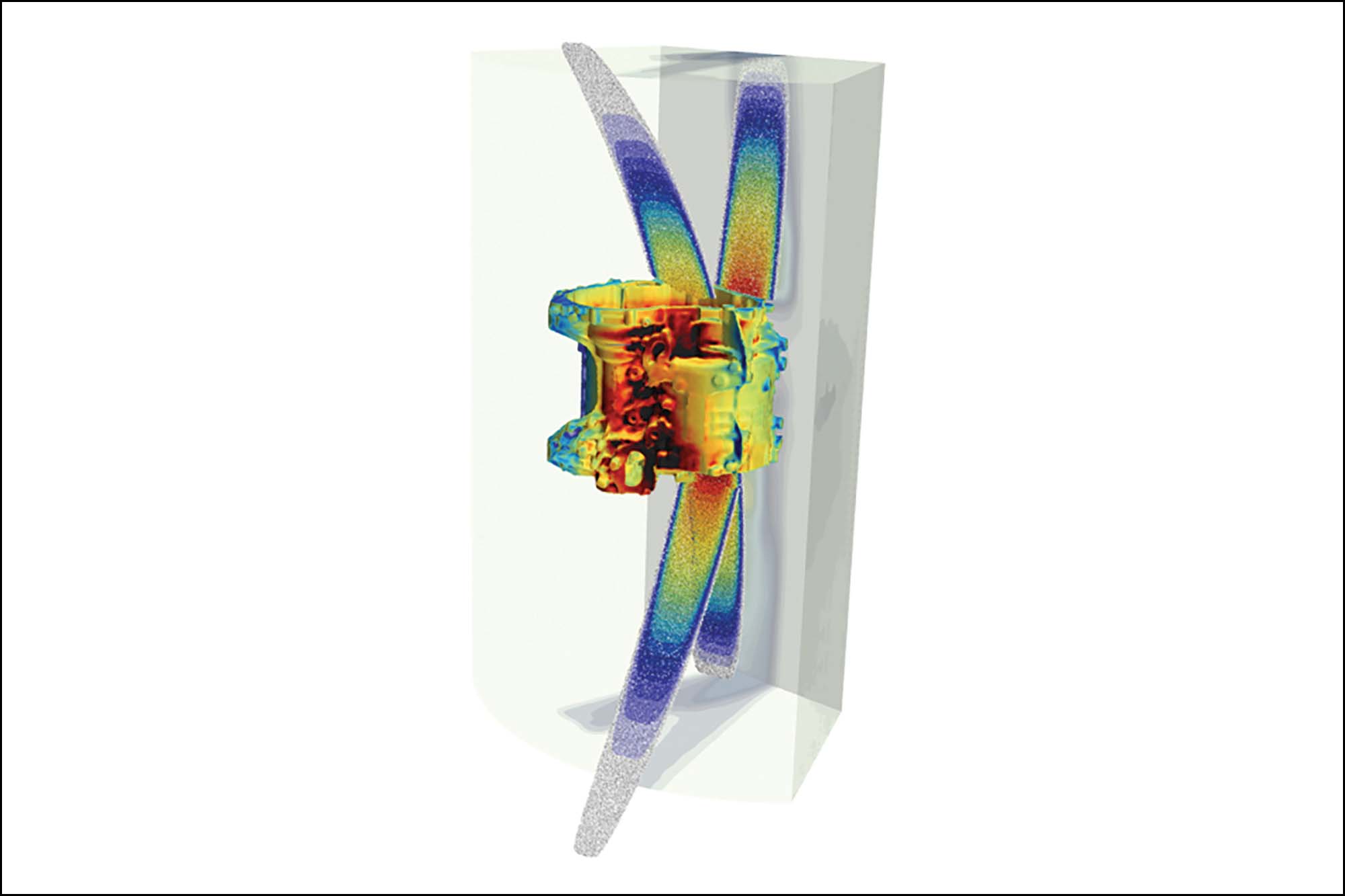
In all instances, shot peening trials in the CEC, along with evaluating the results by X-ray diffraction, special tests of the peening coverage, and, if needed, surface roughness and light-microscopic measurements, will ensure that the required peening specifications are achieved. The LOWER COSTS AND HIGHER PRODUCTIVITY FOR SHOT PEENING PROCESSES Shot peening, the “hammering” of workpieces with precisely defined blast media, is an indispensable operation in industries such as automotive and aerospace. By inducing residual compressive stress into the workpieces, shot peening substantially improves their long-term resistance against tensile and bending loads. SHOT BLASTING August 2024 n 39 selection of the right blast media is important for the resource and cost efficiency of the process. A blast media analysis will always help to determine if the current media is right for the respective application.
Wet or dry shot peening?
Shot peening with compressed air blast guns can be run as a wet or dry process. The advantages of the dry peening method are a higher blast intensity and targeted blasting of specific surface areas. In addition, the entire process and the blast media can be precisely controlled. The wet blasting technology prevents the media from being embedded in the workpieces and produces a lower surface roughness. Since wet blasting is gentler than dry blasting, it is ideal for treating delicate work pieces with thin walls without warping them. Each of the two peening methods has its advantages. Therefore, the chosen method must be a perfect fit for the respective application, especially in terms of cost-efficiency and quality of the peening results. Rösler offers a broad spectrum of different machine types. This allows for an objective equipment selection and ensures customers get the best solution for their requirements.
All steps regarding process alteration and optimisation, including the processing trials and process evaluation, can be modified, and the shot peening equipment can be adapted to change production conditions. This ensures consistent, high-quality peening results throughout the entire equipment life and guarantees that all energy, resources, and cost efficiency demands are fully met
Cookie Consent
We use cookies to personalize your experience. By continuing to visit this website you agree to our Terms & Conditions, Privacy Policy and Cookie Policy.