Electronica Plastic Machines innovates with servo systems and sustainable moulding solutions
By Staff Report December 30, 2024 7:56 pm IST
Electronica Plastic Machines Ltd, led by Aditya Ratnaparkhi, is known for its innovative five-point double toggle mechanism and pioneering use of servo systems in plastic moulding machines. Committed to sustainability, the company integrates recycled materials and collaborates on biodegradable solutions.
What innovations have shaped your company’s evolution in developing efficient plastic moulding machines?
We are renowned for our five-point double toggle mechanism. We have been continuously developing and improving them since the start of the company. The five-point double toggle machine was launched in 1997. It has a total mechanism with a very power-efficient design. It provides overall efficiency. We were the first to introduce servo systems in plastic moulding machines in India. These servo systems also encourage overall efficiency with their design aspect. The amount of current input versus the output is much better than AC systems in these machines. It has been in our DNA to make things as efficient as possible and provide value to our customers.
How does Electronica Plastic Machines incorporate sustainability into its solutions?
Sustainability is a key factor for Electronica Plastic Machines, and we ensure that we provide sustainable solutions to the machine-building industry. We utilise recycled plastic and offer specialised solutions for processing recycled materials, helping to minimise the amount of plastic sent to landfills. Recently, we worked on a few projects in partnership with certain start-ups to ensure that biodegradable plastic is processed using our machines.
How do you embrace cycle time and contribute to the circular economy?
The idea of a circular economy is that the virgin material is processed, and a product is developed. Once the product ends, it is recycled into raw material and reused in the production cycle. Since we manufacture machines, the scope of the circular economy is more for plastic processors, who are our customers. We regularly collaborate with businesses and start-ups who want to specialise in recycled products. One of the processes we recently collaborated on was discarded plastic used to manufacture the garden tiles.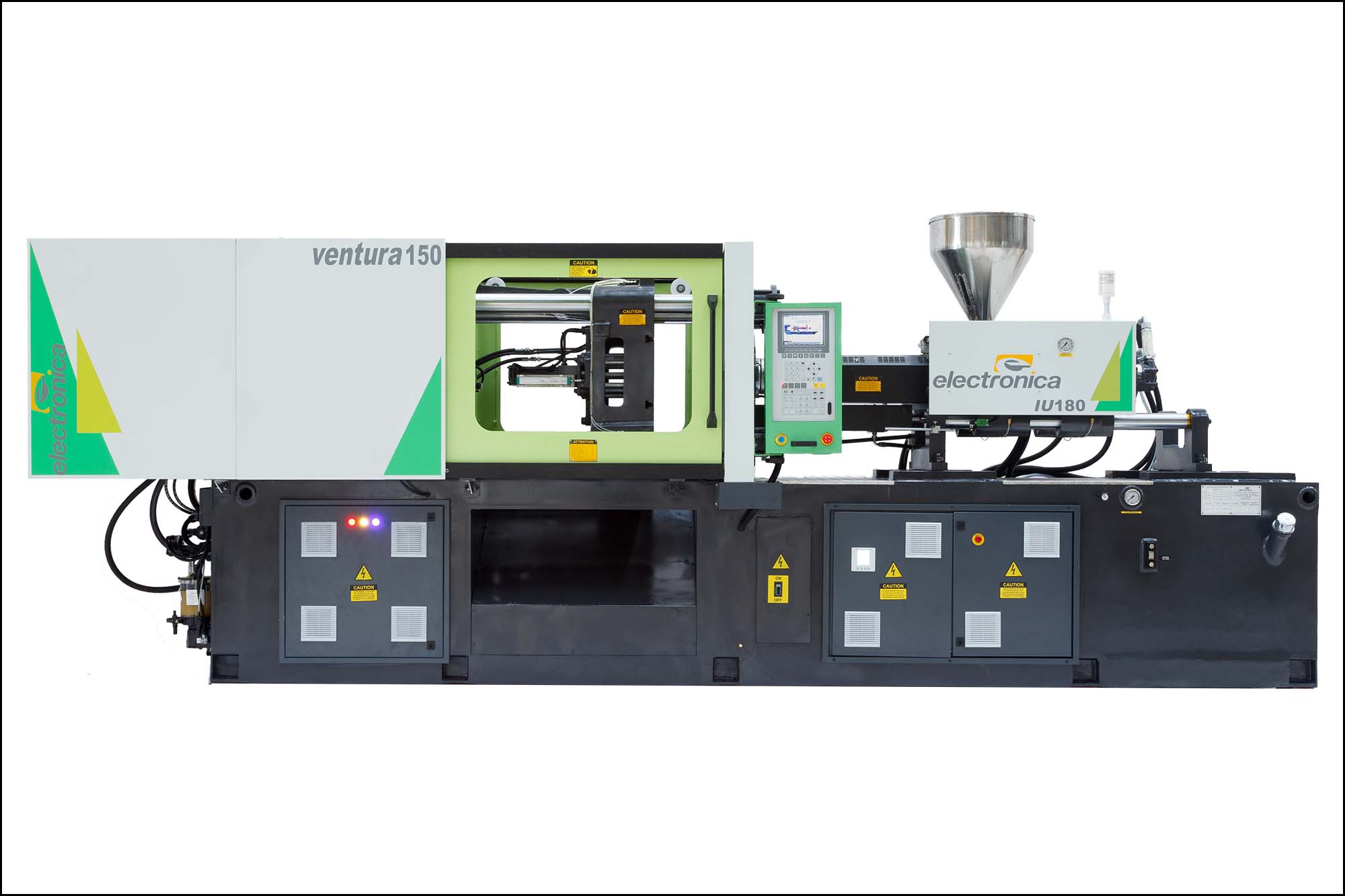
How is your R&D department structured to meet the growing demand for customised solutions?
We offer customised solutions to customers. If it’s a standard machine, we come into the picture at the end of the project. However, if it’s a customised solution, then it requires much more collaborative effort. Thus, we work closely with customers and get involved as a machine manufacturer right from the start. We have our own design and development team based out of the Pune factory, and going forward, we look to strengthen that as well.
The delivery time for a standard machine is usually less than a month, but it depends on the level of customisation required by the customer. We attribute this to our strong relationships with suppliers and vendors, whom we consider part of our extended family. This collaborative spirit enables us to offer tailored solutions more quickly than our competitors.
Please share the details about your foray into the medical segment.
A series of factors contributed to a recent market shift. Our involvement in the medical industry, particularly during the COVID-19 pandemic, highlighted supply chain challenges. Imports were restricted, and shops operated at limited capacity. During this time, many customers entered the medical sector to meet the urgent demand. This provided an opportunity for us, and the support and acceptance from our customers played a crucial role in our success.
Cookie Consent
We use cookies to personalize your experience. By continuing to visit this website you agree to our Terms & Conditions, Privacy Policy and Cookie Policy.