Blueprint to production
By Staff Report October 8, 2024 7:02 pm IST
Lead time is very critical in plastic mold manufacturing. By understanding the factors influencing lead time and implementing appropriate strategies, manufacturers can change their development processes, enhance customer satisfaction, and achieve sustainable growth.
Lead time determines the success of plastic product development. The speed at which a new product can be brought to market impacts its competitiveness, profitability, and overall success. Plastic mold manufacturing is a crucial step in the plastic product development process.
Understanding lead time in plastic mold manufacturing
Lead time in plastic mold manufacturing encompasses several key stages:
Design and engineering: Creating the mold design, conducting feasibility studies, and ensuring compliance with engineering standards.
Material procurement: Sourcing necessary materials, such as steel, resin, and other components for timely production.
Mold fabrication: The actual manufacturing process of the mold, including machining, polishing, and assembly takes place during this stage.
Testing and quality control: Rigorous testing and quality checks to ensure the mold’s functionality and adherence to specifications.
Production and delivery: Once the mold is approved, the commencement of production and delivery of the finished plastic parts are quick.
Why lead time matters in plastic product development
Time-to-Market: Shorter lead times lead to faster product launches, allowing companies to capitalise on market trends and gain a competitive edge.
Customer satisfaction: Prompt delivery of products meets customer expectations, fostering loyalty and repeat business.
Inventory management: Efficient lead time management helps optimise inventory levels, reduce storage costs and minimise the risk of stockouts.
Cost control: Minimising delays and rework can save costs and improve profitability.
Supply chain efficiency: Predictable lead times contribute to an efficient supply chain, reducing the risk of disruptions and allowing a steady flow of materials.
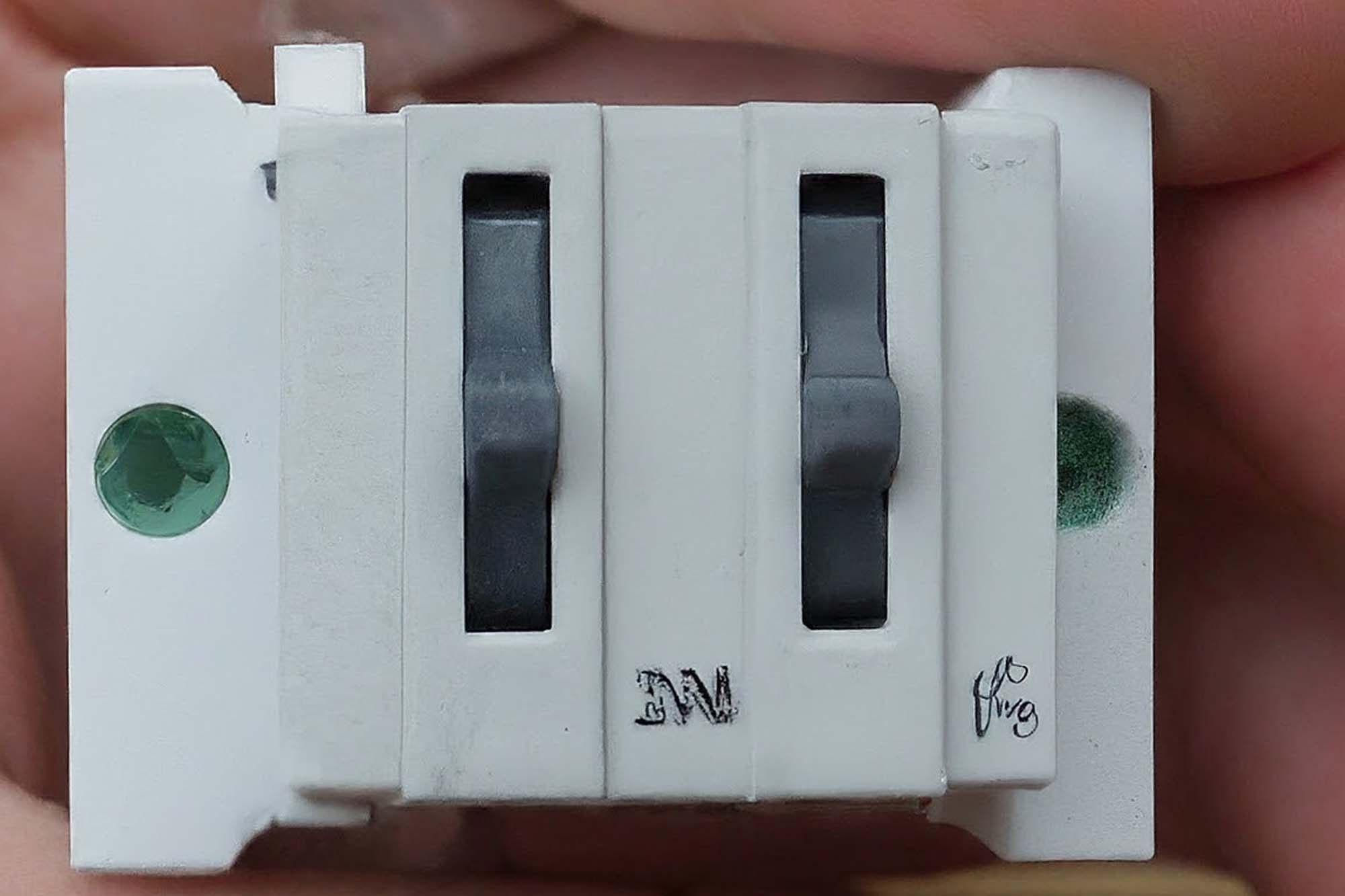
Factors affecting lead time
Several factors can influence lead time in plastic mold manufacturing:
Mold complexity: Intricate designs with multiple cavities or complex features can extend production time.
Material availability: Specific materials can impact lead time, especially for rare or specialised materials.
Manufacturing capacity: The workload of the manufacturing facility and the availability of equipment and skilled labour can affect production schedules.
Design changes: Late design modifications or revisions can cause delays in the production process.
Quality control standards: Stringent quality control measures require additional time for testing and inspection.
Effective lead time management
Lead times in plastic product development can be optimised if manufacturers can implement the following strategies:
Efficient planning and scheduling: Utilise advanced planning tools and techniques to reduce bottlenecks and maximise resource utilisation.
Supplier partnerships: Foster strong relationships with suppliers to ensure reliable material delivery and minimise procurement lead times.
Lean manufacturing principles: Adopt lean manufacturing practices to eliminate waste and improve efficiency.
Automation and technology: Invest in automation and advanced technologies to streamline processes and reduce production time.
Continuous improvement: Regularly assess and optimise the manufacturing process to identify areas for improvement and reduce lead times.
Thriam Toolroom
Website: https://thriam.com/thriamtoolroom/
Email: minu.madhukumar@thriam.com
Cookie Consent
We use cookies to personalize your experience. By continuing to visit this website you agree to our Terms & Conditions, Privacy Policy and Cookie Policy.