Pharmaceutical quality and cost conundrum in modern manufacturing
By Staff Report December 18, 2024 6:24 pm IST
To meet quality standards, the industry uses advanced technologies and smart manufacturing to scale processes and improve efficiency. Deepesh Upadhyay, Assistant Vice President of Delair India Pvt. Ltd, discusses the challenges faced by the Indian pharma industry, including quality checks, high production costs, and strict regulatory environments.
The Indian pharma industry has become the largest global provider of generic medicines. However, there are certain challenges due to quality checks, high production costs, and a strict regulatory environment, despite promising prospects. Substandard drugs and medicines can impact the life expectancy of individuals. This mandate requires adhering to good manufacturing practices set by regulatory bodies like the FDA. Here, failing to conform to the quality standards can result in product recalls from the market, and with the country’s pharma exports reaching US$ 25.02 billion in 2024, the demand for high-quality medicines that meet international standards is increasing.
The industry is utilising advanced technologies to scale processes and incorporate smart manufacturing for efficiency and accuracy, leading to product cost-effectiveness.
Pneumatic machines
The pharma industry utilises pneumatic processes in manufacturing and packaging products, but these machines are constantly at risk of damage due to moisture-laden compressed air. Pneumatic machines rely on compressed air, and the slightest presence of moisture can cause corrosion, which can freeze during winters, disrupting smooth operations and causing sluggish functioning of valves and cylinders, as the presence of moisture can lead to a freeze. The pharma industry utilises desiccant dryers to enhance efficiency by removing moisture, dust particles, oil, and other solid contaminants from compressed air. It achieves quality standards of ISO 8573-1:2010 Class 1 and ensures optimal atmospheric dew point temperature range of (-40°C) to (-70°C) max. The dryers utilise the heatless regeneration principle, utilising the desiccant to adsorb and desorb water vapour, and the pressure swing/purge air principle is applied to facilitate the regeneration of the desiccant bed.
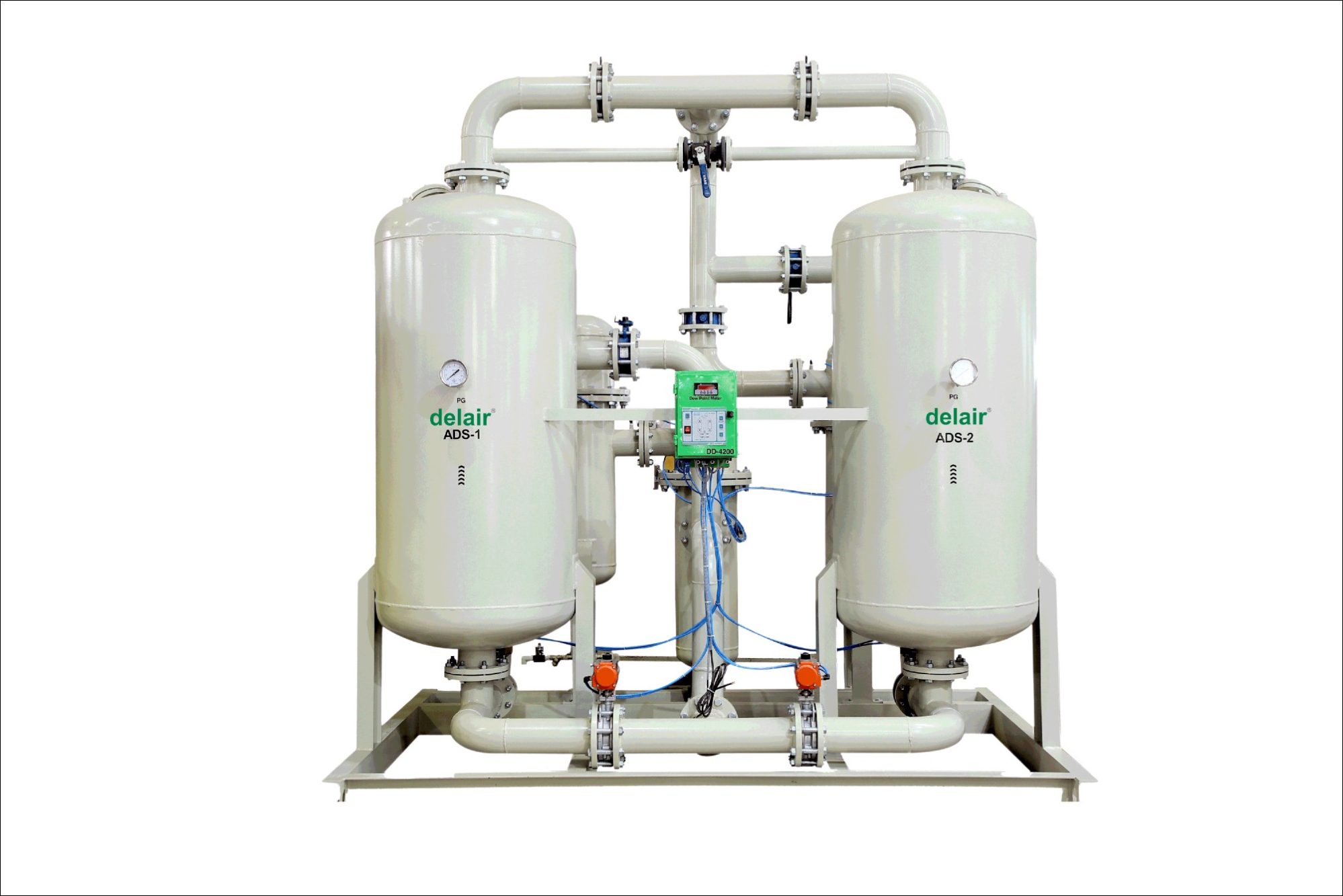
Understanding pneumatic processes leads to precise, reliable, and safe operation in the pharma industry to regulate processes with automated methods. Therefore, compressed air dryers can improve the efficiency of pneumatic equipment with optimal functioning.
Delair compressed air dryers offer numerous benefits, including efficient resource utilisation and reduced energy consumption. It has advanced systems that exercise precision in managing energy-saving drying cycles with the Dew Point Based Dependence System (DPDS) for purge optimisation. The technology reduces purge losses by extending the regeneration cycle time, leading to substantial energy savings. Moreover, the system has automatic condensate management and differential pressure gauges, enabling advanced filtration. This combination of various factors eliminates dust, oil aerosols, and vapours, ensuring high air purity and reliability.
Key trends in pharma manufacturing
Delair is continuously developing its technologies to improve offerings, and our industry advancements indicate the potential for digitisation and automation in the future. Advanced features like remote monitoring and predictive maintenance detect early faults to reduce downtime and save financial losses.
Cookie Consent
We use cookies to personalize your experience. By continuing to visit this website you agree to our Terms & Conditions, Privacy Policy and Cookie Policy.