Nandan Petrochem champions the sustainable production of VELVEX Oils
By Staff Report March 1, 2025 11:31 am IST
Nandan Petrochem prioritises sustainability and regulatory compliance throughout the production process and focuses on responsibly sourcing raw materials, adhering to global sustainability practices, and utilising energy-efficient processes. Vikas Gupta, CEO of Nandan Petrochem Ltd., discusses making VELVEX Rubber Process Oils, which are low in harmful substances like sulphur and metals. These oils are formulated to be safe for workers and the environment, ensuring compliance with international environmental regulations.
How does VELVEX Transformer Oil ensure superior insulation and cooling performance for transformers?
VELVEX Transformer Oil is engineered to provide exceptional insulation and cooling performance for transformers. Crafted from high-quality base oils and enhanced with advanced additives, VELVEX ensures superior dielectric strength, which is critical for maintaining the integrity of electrical systems. This high dielectric strength allows for reliable electrical insulation, preventing the risk of electrical breakdowns and minimising the chances of short circuits.
The oil’s low moisture content is important in enhancing its insulating properties. By reducing the presence of water, VELVEX Transformer Oil helps prevent contamination, which could otherwise compromise performance and lead to premature failure. In addition, VELVEX oil is designed with high thermal stability, effectively managing and dissipating the heat generated within the transformer during operation. This maintains optimal operating temperatures, prevents overheating, and ensures that the transformer continues to operate efficiently, even under heavy load conditions.
Another key benefit of VELVEX Transformer Oil is its exceptional oxidation resistance. The oil is formulated to resist oxidation, which minimises sludge and contaminants. This reduces the risk of varnish build-up and smoothens the operation, extending the transformer’s life. Reduction in sludge formation keeps the transformer free from harmful deposits. VELVEX oil prevents wear and tear, ultimately contributing to lower maintenance costs and longer equipment life.
What makes VELVEX White Oils suitable for use in pharmaceuticals and cosmetics?
VELVEX White Oils are refined to meet high purity standards, making them ideal for pharmaceutical use and cosmetics. Produced in leading-edge facilities with advanced refining techniques, these oils are ultra-pure, adhere to strict quality control standards, and are impure-free. This exceptional level of refinement makes VELVEX White Oils safe for direct use in skin and hair care products, as well as in medicinal applications, while fully complying with regulatory requirements.
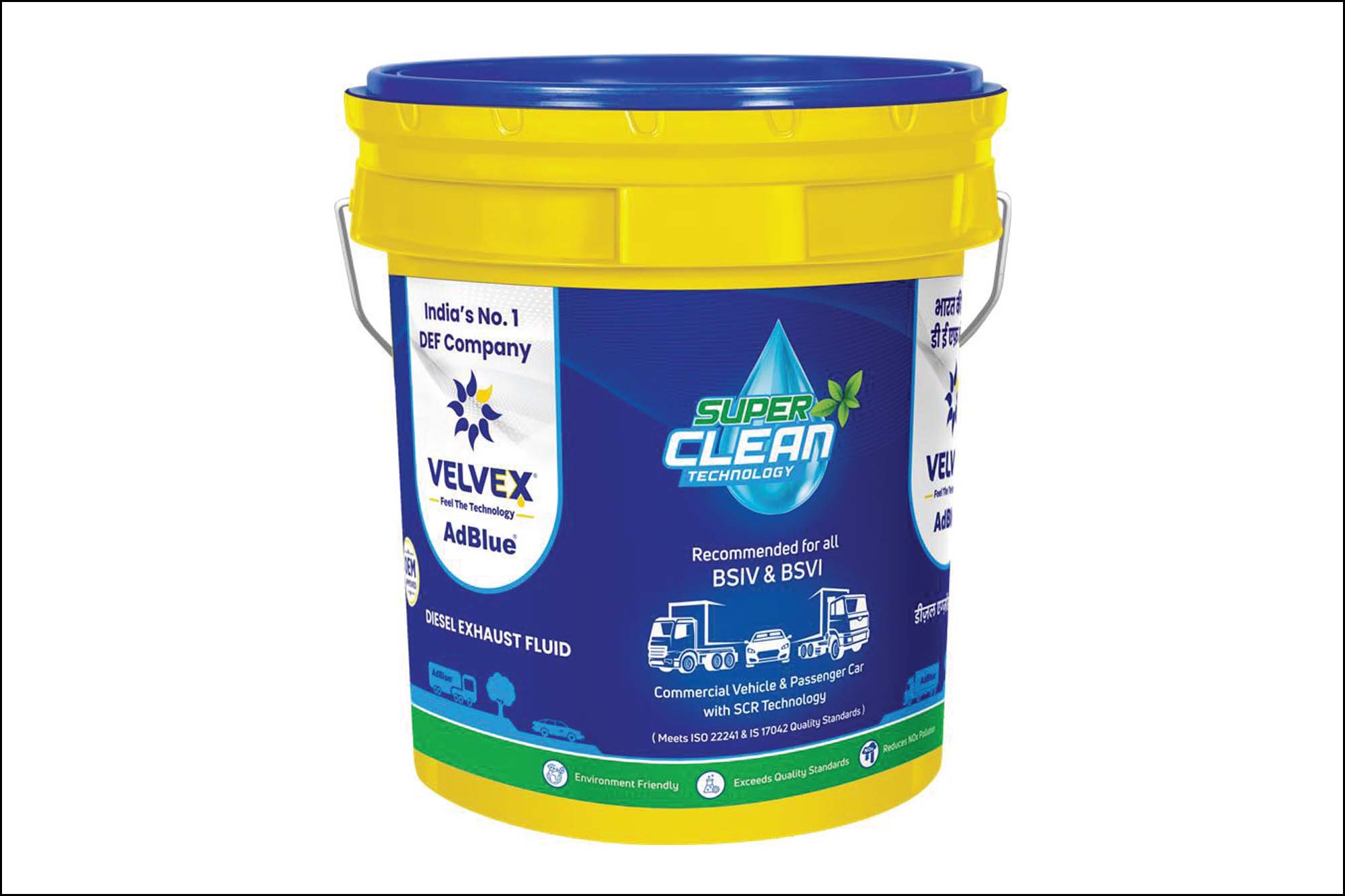
Colourless, odourless, and completely transparent, VELVEX White Oils have a neutral base in cosmetic formulations, used to maintain the final product’s integrity and effectiveness. Their high oxidation stability keeps them fresh and stable over time, enhancing the shelf life of both skincare and pharmaceutical products.
Additionally, VELVEX White Oils are non-comedogenic; they won’t clog pores, making them ideal for use in sensitive or acne-prone skin products. Their excellent moisturising properties provide superior hydration, leaving skin soft, smooth, and nourished. These oils contribute to a silky texture in formulations, improving the spreadability and feel of the product. Whether used in skincare, haircare, or medicinal creams, VELVEX White Oils deliver long-lasting performance and help create effective, safe, and luxurious formulations.
What are the advantages of using VELVEX Rubber Process Oils in manufacturing rubber products, and how does NPL ensure environmental compliance in the production of Rubber Process Oils?
VELVEX Rubber Process Oils improve the processing and performance of rubber products. These oils provide multiple advantages in the rubber manufacturing process.
VELVEX Rubber Process Oils improve the processability of rubber compounds by facilitating better dispersion of fillers and additives, reducing viscosity, and improving the workability of the rubber compound, thereby enhancing overall production efficiency.
VELVEX Rubber Process Oils enhance rubber’s physical properties, reducing curing time and improving flexibility, tensile strength, and elongation. Thus, they contribute to more durable products for high-performance rubber goods production.
Due to their ability to lower viscosity, VELVEX Rubber Process Oils can reduce energy consumption during manufacturing. This optimises processing costs and minimises machinery wear and tear, contributing to production cost savings.
These oils help to achieve a smoother and more aesthetically appealing finish in rubber products, which is required for consumer-facing items such as automotive parts, footwear, and industrial goods.
VELVEX Rubber Process Oils are formulated to deliver consistent results batch after batch, confirming that manufacturers achieve the expected quality standards and performance characteristics in final products.
We prioritise environmental sustainability and regulatory compliance throughout the production process. While manufacturing VELVEX Rubber Process Oils, we adhere to stringent environmental standards to ensure that our products are effective and eco-friendly.
We focus on responsibly sourcing raw materials for rubber process oils, as per global sustainability practices, and minimising the environmental impact of the supply chain.Our state-of-the-art manufacturing facilities incorporate energy-efficient processes, reducing energy consumption and minimising emissions during production. We utilise technologies that minimise waste production and encourage recycling.
VELVEX Rubber Process Oils are designed to be low in harmful substances like sulphur and metals, which could potentially have negative environmental effects. These oils are formulated to be safe for workers and the environment, ensuring compliance with international environmental regulations.
What steps does Nandan Petrochem take to maintain the quality and consistency of its lubricants?
We are dedicated to ensuring the highest quality and consistency of lubricants in all our operations. We implement advanced manufacturing processes and stringent quality control measures to ensure that every product meets the highest industry standards.
Our production processes are conducted in advanced facilities equipped with the latest technology. These facilities follow globally recognised quality management systems and standards, including ISO and IATF certifications, ensuring that each batch of lubricants is produced precisely and consistently.
We use the highest quality base oils combined with cutting-edge additive technology. This allows us to formulate lubricants with superior performance, durability, and efficiency. Our careful selection of raw materials ensures the optimal performance of our products across a wide range of applications.
Each batch of lubricant undergoes a comprehensive testing process in well-equipped NABL (National Accreditation Board for Testing and Calibration Laboratories) -)-approved laboratories. These tests measure viscosity, thermal stability, oxidation resistance, and wear protection, ensuring lubricants meet the required performance benchmarks.
We are committed to innovation, which drives continuous R&D efforts and improves lubricants’ performance and efficiency. By focusing on R&D, we anticipate industry trends, create new formulations, and improve existing products to satisfy changing customer needs and market demands.
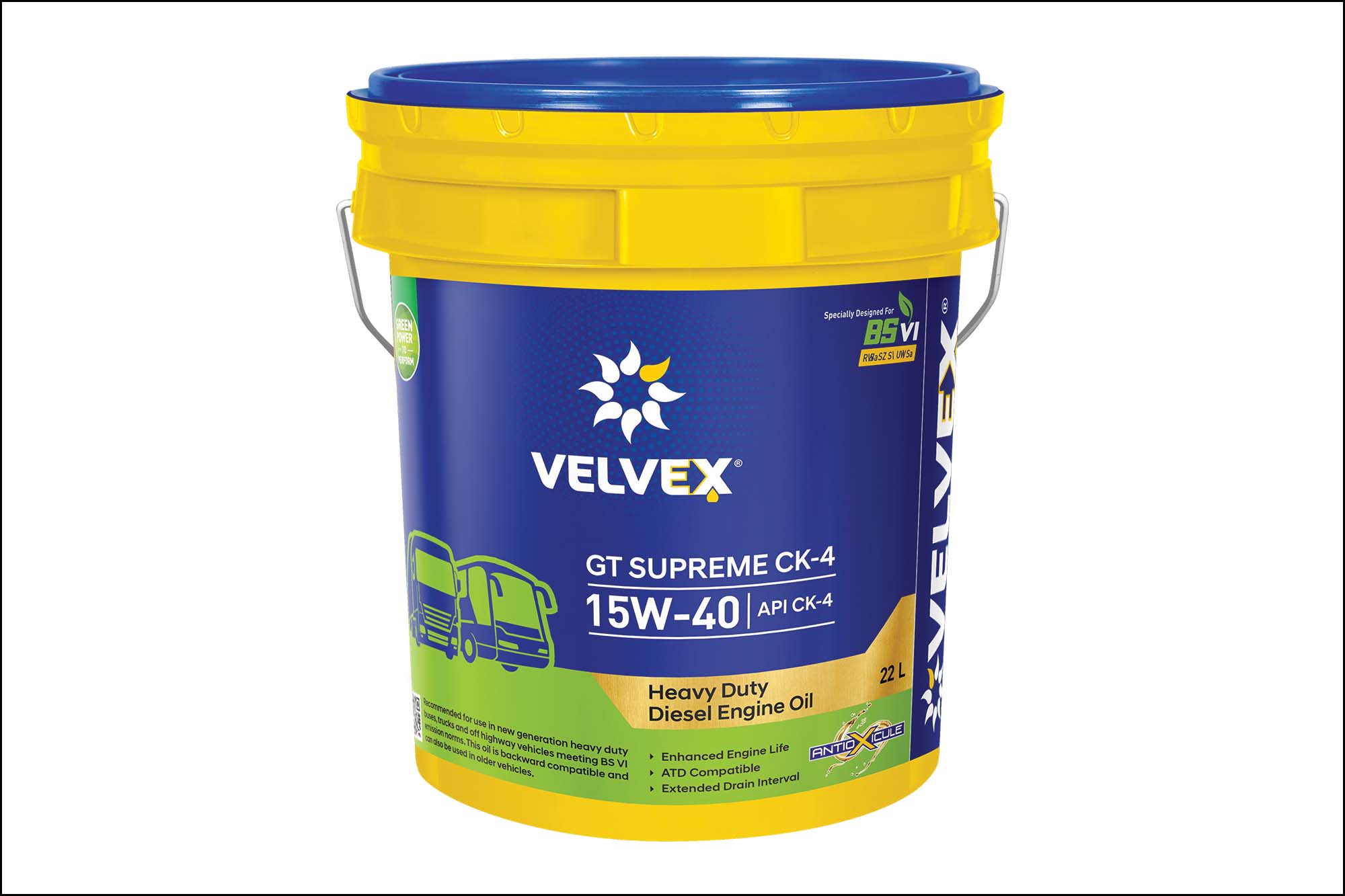
Our products comply with the most up-to-date regulatory requirements and environmental standards.
We formulate industrial lubricants based on industry-specific needs, considering operational requirements and environmental conditions of different sectors like automotive, manufacturing, and food processing. We also customise lubricant formulations to address these specific needs, whether that involves extreme temperatures, high loads, or compliance with hygiene standards. We tailored products to provide optimal performance under the unique demands of each sector.
To ensure optimal performance and prevent damage to machinery, we verify that each lubricant is compatible with a wide range of materials, including metals, rubber, and plastics. This prevents wear, corrosion, and forms of degradation, enhancing the longevity and efficiency of the equipment.
We design lubricants that maximise machinery performance, reduce energy consumption, and improve operational efficiency. We ensure formulations offer reliable, consistent results in even the most demanding environments, facing high-pressure, high-speed, or high-temperature conditions.
At NPL, we are committed to sustainability. In line with ISO 14001 certification, we develop lubricants with minimal environmental impact, focusing on biodegradability, reduced toxicity, and safe disposal.
We value our customers’ feedback and use it to improve products. By staying engaged with clients and actively addressing their challenges, we refine formulations to ensure that our products remain reliable, safe, and high-performing, even in extreme conditions.
Cookie Consent
We use cookies to personalize your experience. By continuing to visit this website you agree to our Terms & Conditions, Privacy Policy and Cookie Policy.