Proper lubrication in hot forging boosts quality and productivity
By Staff Report October 8, 2024 7:22 pm IST
Lubrication is inevitable in the hot forging process to maintain quality and productivity. Hot forging is performed at extremely high temperatures (up to 1250-degrees C for steel, 360. degrees C to 520egrees C for Al-alloys, 700. degrees C to 800 degrees C for Cualloys). These temperatures are necessary to avoid strain hardening of the metal during deformation. So, the lubrication of the forging process is not easy; it depends on the right selection of lubricants for the right application areas to get the best results.
A lubricant for forging dies is a chemical compound with a formulation for the forging process to be carried out within the limits and parameters of the forging industry.
Characteristics of ideal lubricants are as follows:
• Reduce the sliding friction between dies and workpiece (Load and energy requirement will be reduced).
• Works as a parting agent between the die and workpiece (Prevents sticking).
• Works as an insulator.
• It should develop a balanced gas pressure (Especially in hammer forging with the impression, Which is called the dieseling effect).
• Should be Non-Abrasive and Non Corrosive.
• Should not create smoke (Pollution free).
• Availability with reasonable cost.
Depending upon application areas, profile and metallurgy of forging components, die lubricants can be divided into water- and oil-based categories. Each type is again divided into two subcategories: those with graphite and those without.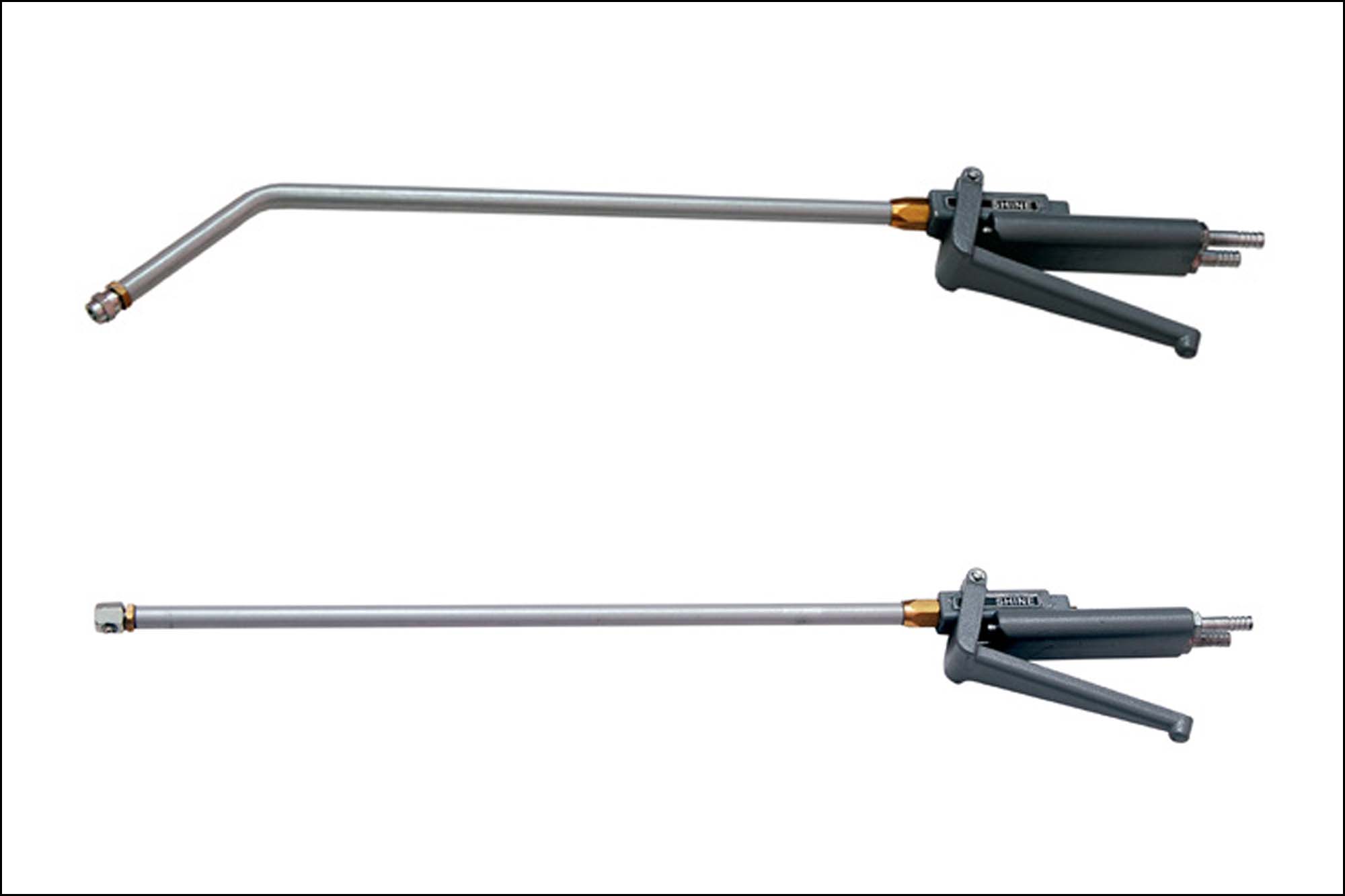
Water-based graphite lubricants: It is a suspension where water is added to ultrafine graphite powder and special additives. This die lubricant is the most familiar type of lubricant as it is highly consumed. This lubricant can be used as a spray, brush or a manual daubing. This is an apt choice if you are looking for heavy and critical press forging operations. This kind of lubricant has the highest dilution ratio in water and is pocket-friendly, as it cuts down per tonnage lubrication cost and gives a long life as a die.
Water-based non-graphite lubricants: These are special water-soluble polymer-based lubricants. This lubricant is the best choice for shallow cavity dies. It is regarded as the most cost-efficient solution because it provides excellent cooling and lubrication.
Other Products
Oil Base Lubricant: According to your demand for the forging process of lubrication, special additives are added to the graphite with either base oil or vegetable oil. Such suspensions are made this way. There are a few grades that come without graphite as well. These lubricants have excellent release properties and provide a better flow of material. They can be used for several purposes: deep cavity hammer forgings, heavy stainless-steel forgings, critical brass and aluminium forgings, and deep extrusions.
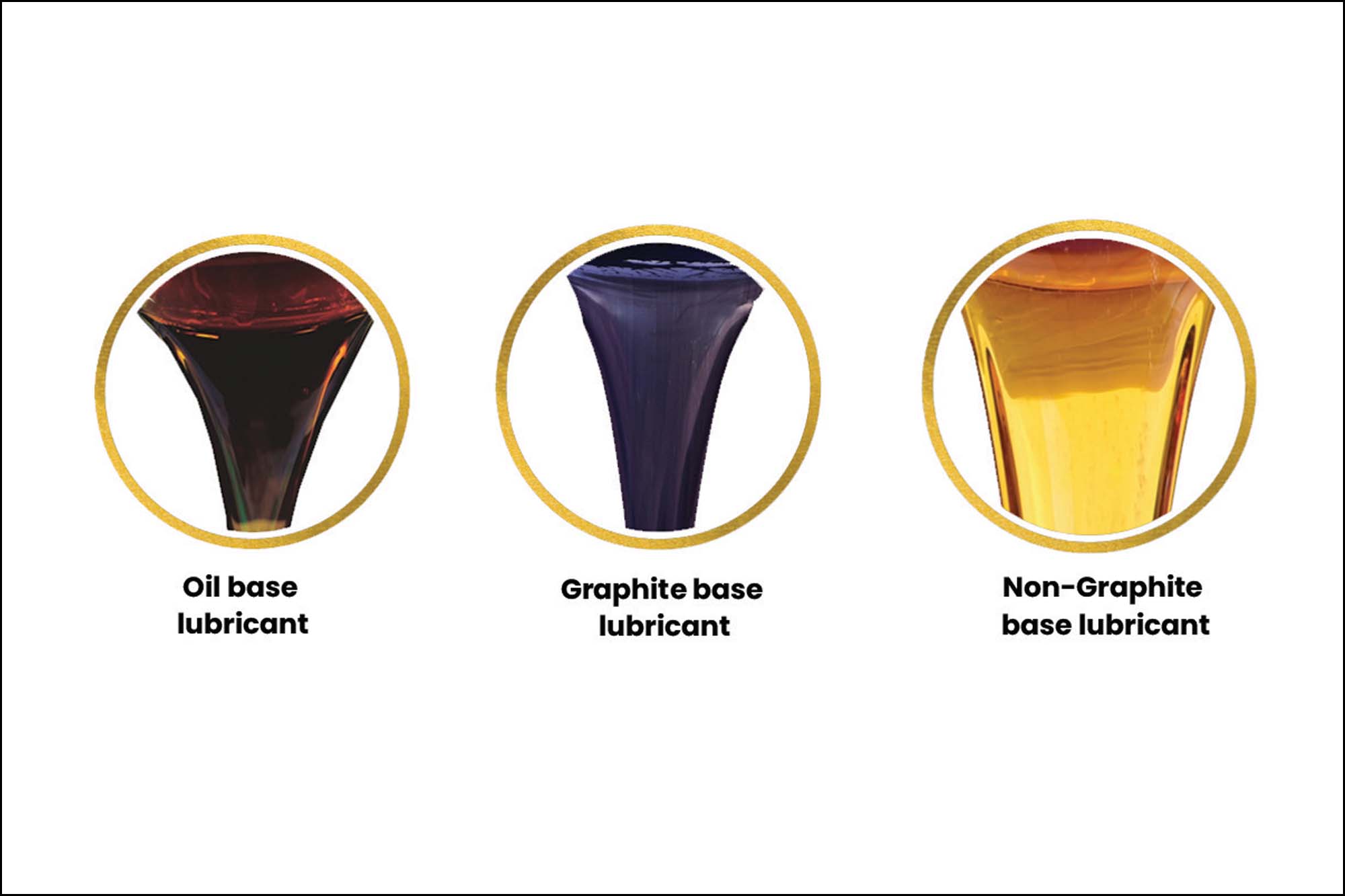
Spray Guns & Spraying Equipment
Along with its complete range of die lubricants, SUNLUB TECHNOLOGIES offers its clients an economical solution for these die lubricants through Spray Guns & Spraying Equipment. The range includes single & dual side spray guns, spray systems with pressure feeder tanks having capacities of 45 and 75 litres, spray systems with open tanks having capacities of 100 & 200 Litres and AODD pumps.
For better service & minimum response time, Sunlub Technologies has a sales network in India.
Contact Us:
Sunlub Technologies
Plot No. L-89, MIDC Industrial Area,
Ahmednagar, Maharashtra – 414111
www.sunlubtechnologies.com;
info@sunlubtechnologies.com
Contact: +91 8181 819 531
Cookie Consent
We use cookies to personalize your experience. By continuing to visit this website you agree to our Terms & Conditions, Privacy Policy and Cookie Policy.