Cortec Advanced Films is increasing its capacity with a new extrusion line
By OEM Update Editorial January 11, 2024 2:27 pm IST
Cortec® Advanced Films (CAF) is revolutionising its production capabilities with a state-of-the-art co-extrusion line, E23, at the Cambridge, Minnesota, plant. This multimillion-dollar investment enhances efficiency, offering increased production volumes and technological versatility for specialty films, including corrosion protection and compostable options.
Cortec® Advanced Films (CAF) demonstrates a strong commitment to the production of Vapor Corrosion Inhibiting (VCI) films and bags, as evident from the substantial investment made by Cortec’s CEO in a cutting-edge co-extrusion line at the Cambridge, Minnesota, plant. The newly established multimillion-dollar line, named E23, is poised to bring advantages to both customers and employees. CAF’s dedication is evident as it pioneers innovative solutions with a growing range of specialty film and bag products.
Technology Upgrade
The new equipment will allow CAF to dramatically increase the production volumes of co-extruded films and will give workers the agility to change tolerances with the touch of a button. The previous co-extruder required manual adjustment and could only run at approximately 60% of the new extruder capacity. This improvement will greatly increase efficiency for both specialty films and any standard VpCI® product CAF may eventually choose to run on the equipment. E23 can extrude tubing up to 75 inches (190.5 cm) wide and sheeting up to 150 inches (381 cm) wide. CAF hopes to replicate the efficiency and greater control of the new technology by adding additional co-extrusion lines in the future.
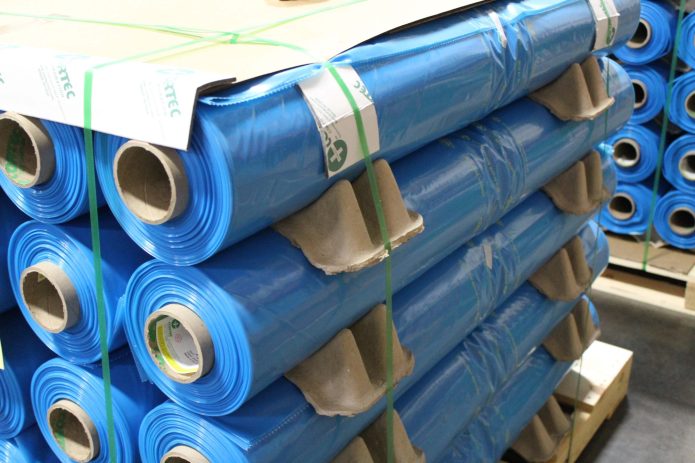
Benefits of Co-Extrusion
Although E23 can be used to make any type of Cortec® film, it is especially tailored to production of specialty films such as Cor-Pak® VpCI® Stretch Film, Eco Wrap® (certified industrially compostable stretch wrap*), and EcoSonic® VpCI®-125 HP Permanent ESD Films (dual corrosion + ESD protection). Each of these requires special resins that go in different film layers for better performance and/or cost-effectiveness of the final product. Certain characteristics also make E23 preferred for extruding CAF’s VpCI®-126 Top-Seal Bags with zipper closures for corrosion protection in WIP (work in process) cycle applications. E23 will also be ideal for new product development. Tim Bliss, Production Manager at CAF, commented, “Let’s just say it opens up a world of opportunities for research and development.”
Increased Capacity, Increased Morale
According to Cortec® CEO and Founder, Boris Miksic, this upgrade will result in “increasing capacity . . . to 40 million pounds of top quality patented VpCI® and compostable films and bags [at] the world’s largest VCI films plant fully integrated with its own compounding, extrusion, printing, converting and 24/7 quality control laboratory.” CAF employees are also enthusiastic about the new investment. According to their production manager, “[They] are super excited about it—super excited. It’s a gorgeous brand-new piece of equipment that’s [going to] make their job simpler.”
Cookie Consent
We use cookies to personalize your experience. By continuing to visit this website you agree to our Terms & Conditions, Privacy Policy and Cookie Policy.