Sandvik Coromant’s ATC is redefining the manufacturing landscape
By Staff Report January 24, 2025 7:42 pm IST
Sandvik Coromant’s advanced Automatic Tool Change (ATC) system transforms manufacturing by enabling 24-hour operations with increased productivity, reduced waste, and optimised efficiency for resilient, sustainable production.
Consider a factory where the lights are turned off, not because no one is there, but because automated systems are working around the clock to keep production lines going with minimal human intervention. These futuristic configurations are rapidly becoming a reality, with touchless tool changes at the heart of the automated machine cell. Here, Peter Pettersson, Product Specialist at Sandvik Coromant, a leader in metal cutting tools and production systems, discusses the company’s most recent invention in autonomous tool changes.
Unmanned machining is a key advancement in manufacturing in which machines operate autonomously without the need for human supervision. These systems, powered by CNC technology, robotics, and automation software, may run constantly — in some circumstances, 24 hours a day — executing high-precision tasks such as turning, cutting, milling, and drilling. This method increases productivity, decreases errors, and enables efficient, round-the-clock operating.
While many people think of robotic machining as a futuristic method to manufacturing, Sandvik Coromant started reaping the benefits in the 1980s.
Going hands free
Sandvik Coromant’s production location in Gimo, Sweden, used automatic tool change (ATC) to facilitate machine tool changeovers without the need for human intervention almost 40 years ago. Customers were provided the remedy as a product, but it failed to gain popularity. Many people were unable to understand how ATC could save them time and increase production in their machine shops, therefore the offering was discontinued.
Fast forward a few decades, and Sandvik Coromant continues to see value where others cannot. This time, the business partnered with a machine builder to create a second ATC system. It was again deployed at the Gimo production site and is still in use in numerous machine cells today.
Using traditional tool management procedures, a lathe may operate without human intervention for four to eight hours. After that, the tool would have reached the end of its useful life, and a human worker would have to stop what they were doing to manually replace it with a new one. The ATC technology allows machines to function for up to 16 hours without the need for an operator to monitor them.
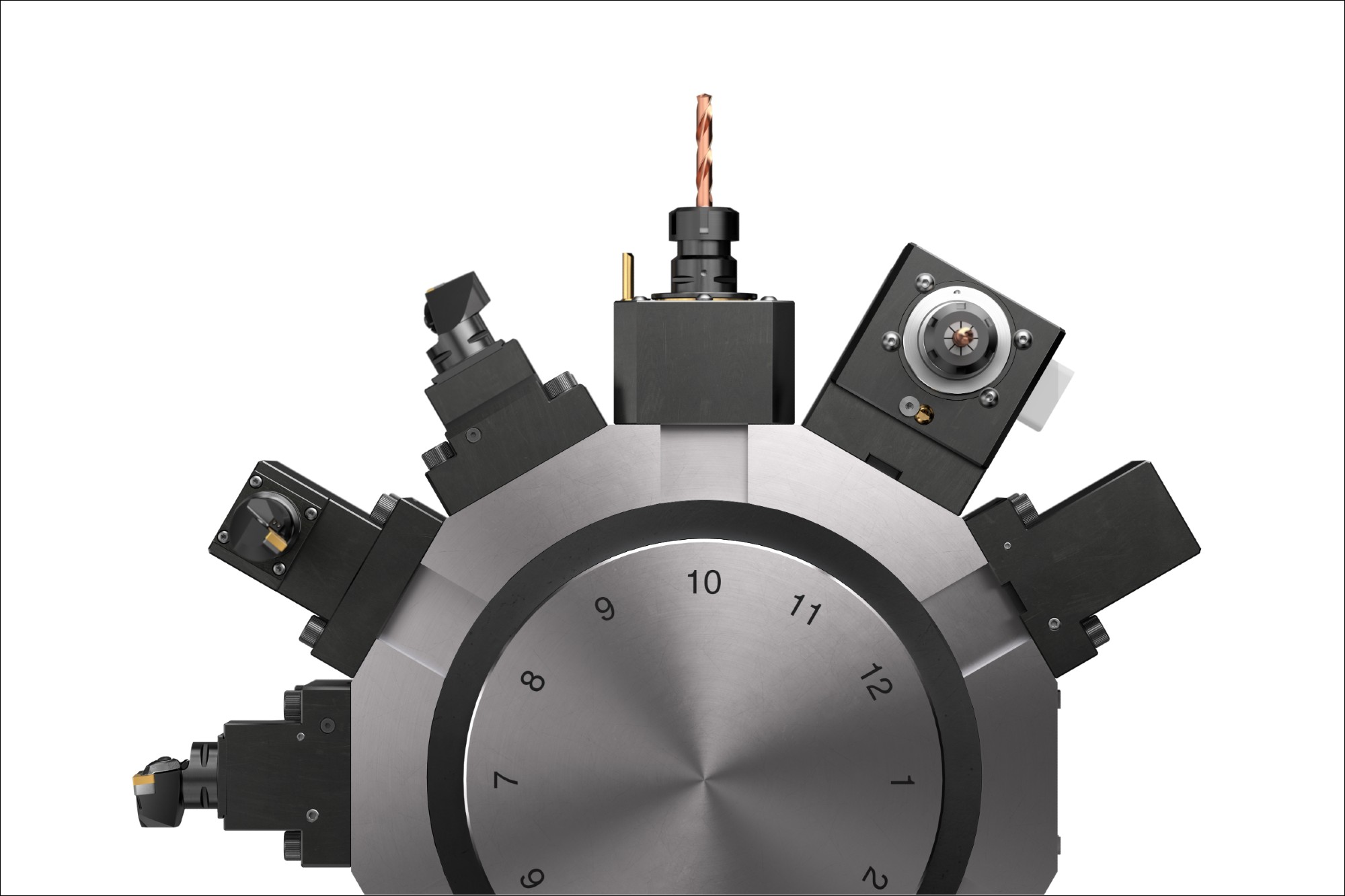
A new take on turning
After several years of employing ATC technology, Sandvik Coromant has created a solution for its customers that allows for hands-free tool swaps during turning operations. The new ATC system for machine-adapted clamping units (MACU) in turning centres completely automates the tool-changing procedure, removing the need for human interaction. This leads to increased machine utilisation and production.
The immediate benefit is that it saves time for human workers. Running machines for up to 16 hours — four times longer than before — without operator intervention frees up operators to focus on other duties rather than constantly inspecting tool wear.
ATC also helps optimise tool wear. When operators manually change tools while juggling numerous other jobs, they often replace tools prematurely, before they’ve attained their full capability. With ATC, tools are replaced only when they are completely worn, extending tool life and saving waste. ATC also provides major environmental benefits, such as reduced energy usage, increased resource efficiency, reduced waste, and improved overall equipment efficiency. By keeping machines running at peak efficiency, ATC lowers idle time and energy waste, enhances productivity with less resources, and reduces the frequency of breakdowns and downtime.
Taking a holistic approach
ATC is a critical component in creating a future-proof shop floor, whether the lights are on or off. The necessity of a holistic approach to production is central to Sandvik Coromant’s Manufacturing Wellness project, which seeks to promote healthy behaviours in future-ready manufacturing facilities.
In modern manufacturing, a complete plan improves efficiency, productivity, and sustainability. Companies can improve operational performance by optimising the entire process, including materials and equipment as well as environmental effect. Advanced technologies and cross-departmental collaboration are critical to attaining these objectives. This comprehensive method not only improves quality but also ensures long-term success in a competitive marketplace.
ATC forms a central part to this holistic take on machining, but Manufacturing Wellness is about more than just individual innovations; it’s about creating a seamless, resilient production ecosystem. ATC plays a key role in this broader vision, enabling factories to go beyond isolated efficiency gains to achieve true operational harmony. By automating routine tasks like tool changes, ATC frees up human operators for more strategic roles, while ensuring machines run at peak efficiency with minimal downtime. This integration of smart automation within a larger, wellness-driven framework positions manufacturers to thrive in an increasingly competitive, resource-conscious world.
For more information, visit: https://www.sandvik.coromant.com/en-gb
Cookie Consent
We use cookies to personalize your experience. By continuing to visit this website you agree to our Terms & Conditions, Privacy Policy and Cookie Policy.