Real-time data and sensor integration in CNC tech impact cutting parameters
By OEM Update Editorial June 5, 2024 4:45 pm IST
Indraneel Bhattacharya, Vice President of Sales and Marketing at LMW, emphasizes that CNC machines are not just tools, but catalysts for efficiency and precision. The integration of multi-axis machining, adaptive control systems, CAD/CAM, and AI/ML is revolutionizing processes. Moreover, the power of IoT connectivity is unlocking the potential of predictive maintenance and data-driven decision-making, ushering in a new era of manufacturing.
How do CNC machines improve precision and accuracy within manufacturing processes?
CNC machines are not just about precision, they are about delivering results. They play a crucial role in enhancing the efficiency and quality standards of industries. Their capacity for high precision and repeatability is a game-changer in industries like Die and mould, Aerospace, Medical, and Electronics, instilling confidence in the manufacturing process.
Another advantage of CNC machine tools is their flexibility. They can be reprogrammed to produce various components, making them adaptable to changing production requirements. This flexibility reduces setup times, streamlining the transition between different parts or product runs.
How do multi-axis machining and adaptive control systems contribute to increased efficiency?
In the world of manufacturing, CNC machine technology continually evolves to enhance precision, efficiency, and productivity. Recent advancements in CNC technology have ushered in a new age of manufacturing, leaving a profound impact on various industries.
Now, modern CNC machines offer multi-axis capabilities, enabling intricate and complex machining tasks. Traditional 3-axis machines are complemented or replaced by 4, 5, or even more axes. Multi-axis machining allows for the production of highly intricate components in a single setup, reducing error margins and streamlining manufacturing processes. Industries like medical devices, aerospace components manufacturing and precision engineering have seen significant benefits from this advancement.
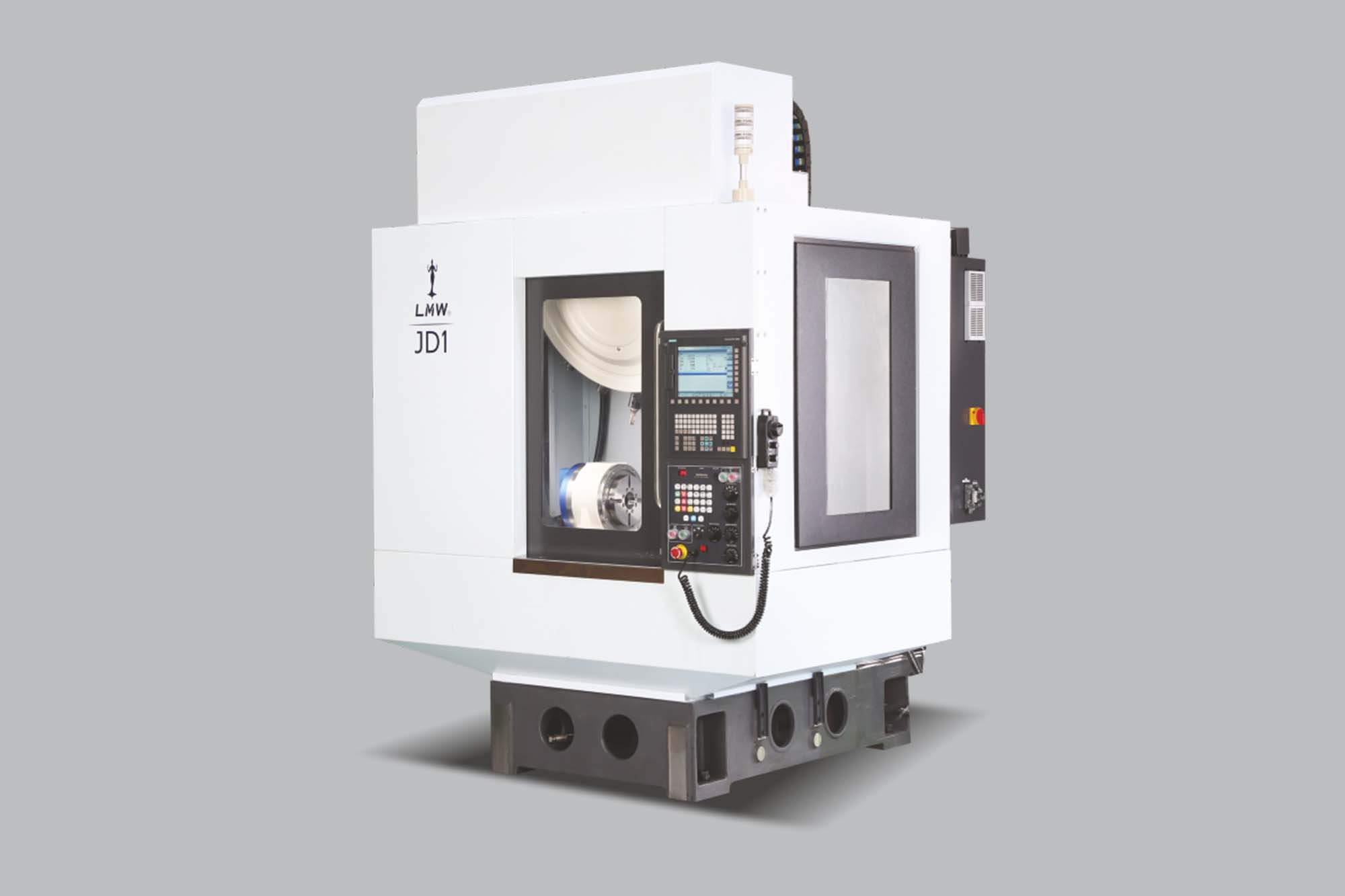
CNC technology has evolved to become more smarter through adaptive machining. This technology uses real-time data and sensors to adjust cutting parameters dynamically. It can compensate for tool wear, material variations, and environmental factors, ensuring consistent part quality throughout the production run. It impacts the die & mould industry, where maintaining precision is paramount.
How does integrating CAD/CAM software enhance the efficiency of CNC machining processes?
Integrating CAD/CAM software with CNC machining processes brings numerous benefits, enhancing efficiency in several ways.
Foremost, CAD/CAM software allows seamless integration of design and manufacturing processes. Engineers can design parts directly in CAD software and then use CAM tools to generate tool paths for CNC machining, eliminating the need for manual data transfer and reducing errors.CAD software enables precise design creation, ensuring parts are accurately dimensioned and fit for purpose. CAM software, on the other hand, can optimise CNC machining tool paths, reduce cycle times, minimise material waste, and enhance surface finish. For example, CAM software can automatically generate tool paths based on CAD models, eliminating the need for manual programming and accelerating the manufacturing process. This not only reduces lead times but also improves the overall efficiency of CNC machining processes.
To enhance machining capabilities, CAD/CAM software provides advanced tool path strategies and machining simulations that optimise cutting strategies, tool selection, and feed rates. It enhances CNC machine capabilities, efficiently achieving complex geometries, intricate features, and tight tolerances. Finally, by automating repetitive tasks such as toolpath generation and CNC program generation, CAD/CAM integration frees up time for machinists and engineers to focus on more critical aspects of the manufacturing process, leading to increased productivity.
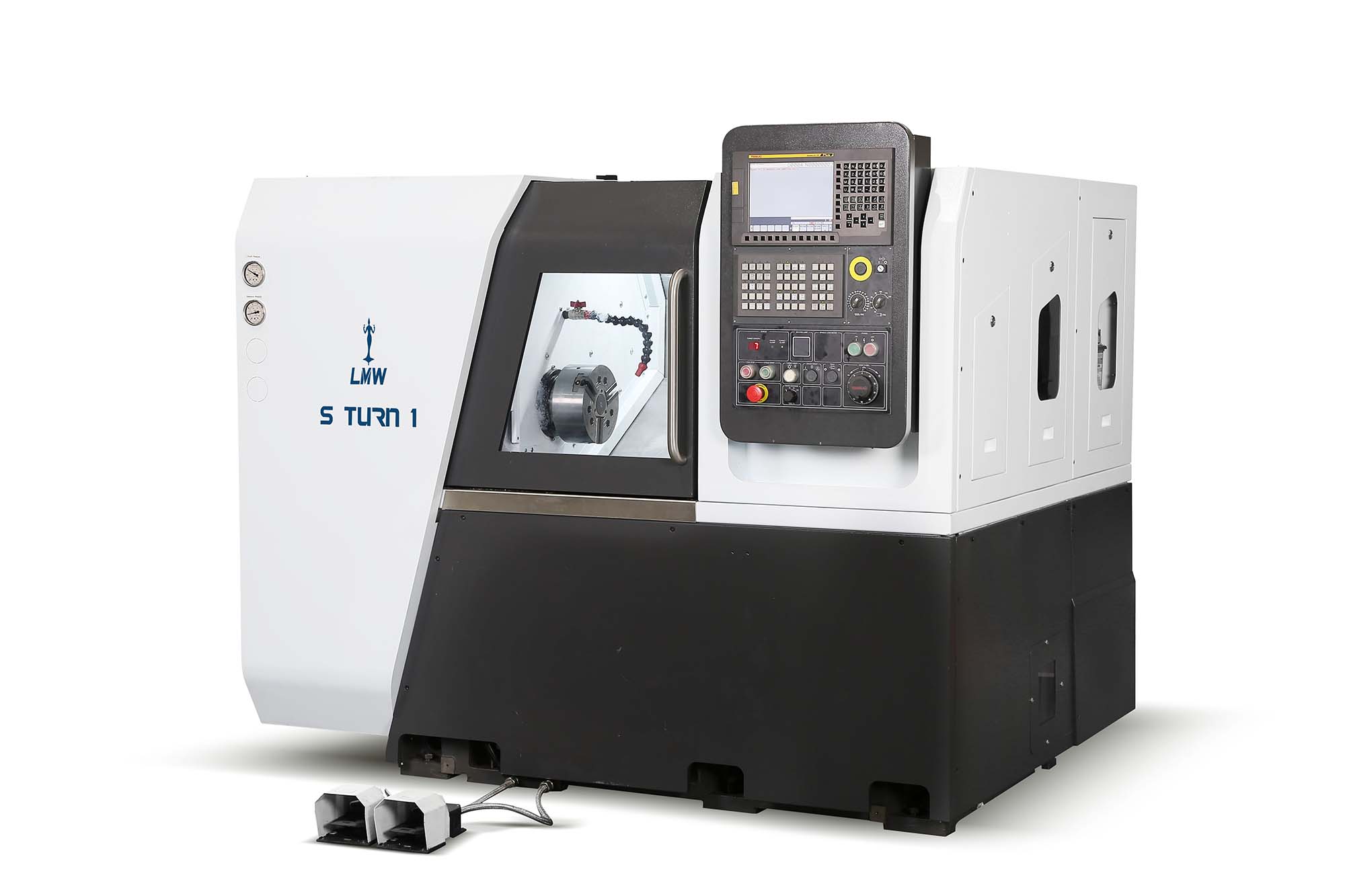
How are AI and ML integrated into CNC systems to optimise machining processes and enhance efficiency?
AI and machine learning are finding their way into CNC technology. These capabilities allow machines to learn and optimise their processes. CNC machines can adapt and fine-tune themselves based on historical data, enhancing efficiency and precision—industries ranging from aerospace to medical manufacturing leverage AI-driven CNC technology for greater automation and quality control.
With the rise of Industry 4.0, how is LMW leveraging IoT connectivity in CNC machinery to enhance manufacturing efficiency and optimise operational performance?
The rise of Industry 4.0 has brought about significant developments in CNC machinery connectivity and data analytics that profoundly influence manufacturing workflows. In the context of
Internet of Things (IoT) connectivity, CNC machines equipped with IoT sensors can collect real-time data on machine performance, tool wear, temperature, vibration, and other parameters. This data is then transmitted to centralised systems for analysis, enabling predictive maintenance, performance optimisation, and overall equipment effectiveness (OEE) monitoring. At LMW, all our machines are IOT-ready.
Big data analytics and advanced analytics tools can process large volumes of manufacturing data generated by CNC machines to identify trends, patterns, and anomalies. This enables manufacturers to optimise machining processes, improve product quality, and reduce production costs.
Manufacturers can predict when CNC machines experience failures or require maintenance by analysing machine performance data in real-time. This enables proactive maintenance activities to be scheduled, minimising unplanned downtime and maximising machine uptime.
Cookie Consent
We use cookies to personalize your experience. By continuing to visit this website you agree to our Terms & Conditions, Privacy Policy and Cookie Policy.