Aerospace manufacturing prefers multifunctional machine tools
By OEM Update Editorial September 1, 2023 3:35 pm
Aerospace manufacturing trends emphasise precision and multifunctionality. Machine tools evolve to meet strict requirements, handling advanced materials and enhancing efficiency while maintaining safety standards.
What are the emerging trends in machine tools for aerospace manufacturing processes?
In the dynamic landscape of aerospace manufacturing, several emerging trends are revolutionising the capabilities and roles of machine tools. One prominent development is the unyielding drive for exceptional precision. Aerospace manufacturers are increasingly imposing stringent requirements on machine tools to achieve levels of precision that align with the industry’s rigorous quality and safety standards. Aircraft components must adhere to remarkably stringent tolerances, prompting machine tools to evolve to deliver essential accuracy.
Another significant trend is multifunctionality. Aerospace manufacturers are adopting machine tools capable of executing various tasks, such as milling, turning, and drilling, all within a single setup. This versatile approach reduces the duration of operational cycles and elevates overall efficiency in the production process. By minimising the necessity for frequent machine changes and setups, manufacturers can streamline their operations and decrease the likelihood of errors.
With aerospace materials continuously progressing towards lightweight composites and advanced alloys, machine tools are adjusting to handle these materials effectively. Lightweight materials hold immense importance for augmenting fuel efficiency and curbing emissions within the aerospace sector. Consequently, machine tools must be equipped with specialised tooling and cutting methods to engage with these materials while maintaining precision and quality.
How do machine tools designed for aerospace applications differ from those used in other industries?
Machine tools designed for aerospace applications exhibit distinct characteristics to fulfil the industry’s specialised requirements. Aerospace parts demand heightened precision, characterised by highly narrow tolerances and rigorous benchmarks. This precision is of utmost importance to guarantee aircraft safety and performance. Machine tools give primary importance to sturdiness and steadfastness within the aerospace sector. They are crafted to be more resilient, effectively managing tough and demanding materials while upholding accuracy even during high-speed machining tasks.
Furthermore, due to the dimensions of aeroplane components, aerospace machine tools frequently showcase spacious work areas, enabling the production of sizable parts without compromising precision. Adherence to industry-specific quality and safety standards stands as an uncompromising prerequisite for aerospace machine tools. These devices must fulfil stringent criteria to ensure the dependability and safety of aerospace parts, which frequently hold critical roles in aircraft operations.
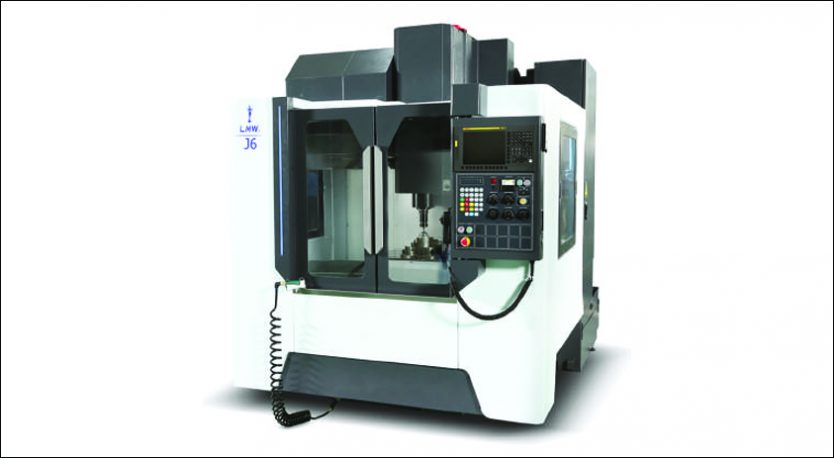
What are the main challenges in machining aerospace materials, and how are specialised machine tools designed to overcome these challenges?
Machining materials used in aerospace applications present distinct challenges that demand specialised solutions. Firstly, the hardness of substances like titanium and advanced composites can significantly impact the durability of cutting tools. These tough materials lead to accelerated wear of cutting tools and reduced lifespan.
Secondly, the high-speed machining of aerospace materials generates considerable heat, which can jeopardise the soundness of the workpiece. Efficient heat management prevents material distortion or alterations in its microstructure. Approaches like optimising coolant usage and implementing advanced cooling systems are employed to uphold stable temperatures throughout the machining process.
Thirdly, controlling vibrations is a crucial concern, as excessive vibrations can detrimentally affect machining accuracy. Customised machine designs integrate damping methods and heightened structural robustness to curtail vibrations and guarantee consistent cutting forces.Lastly, attaining the necessary surface finish on aerospace components can be particularly demanding due to the distinctive attributes of these materials. The hardness and abrasive nature of specific aerospace materials can complicate the attainment of precise surface finishes. Advanced strategies for toolpaths and the use of tools resistant to abrasion are frequently employed to surmount these hurdles, ensuring that the end products adhere to the exacting quality standards mandated by the aerospace sector. Overall, effectively addressing these challenges is imperative to preserve the calibre and performance of aerospace components during the machining process.
Please discuss the indigenous production of complex aerospace components, such as turbine blades or aircraft fuselages.
The Indigenous production of complex aerospace components such as turbine blades or fuselages necessitates a blend of dedicated machine tools, a proficient workforce, and stringent quality control protocols. Numerous aerospace manufacturers collaborate closely with engineering and research establishments to formulate and enhance their production methodologies. Indigenous manufacturing bolsters self-sufficiency and reduces dependency on foreign suppliers.
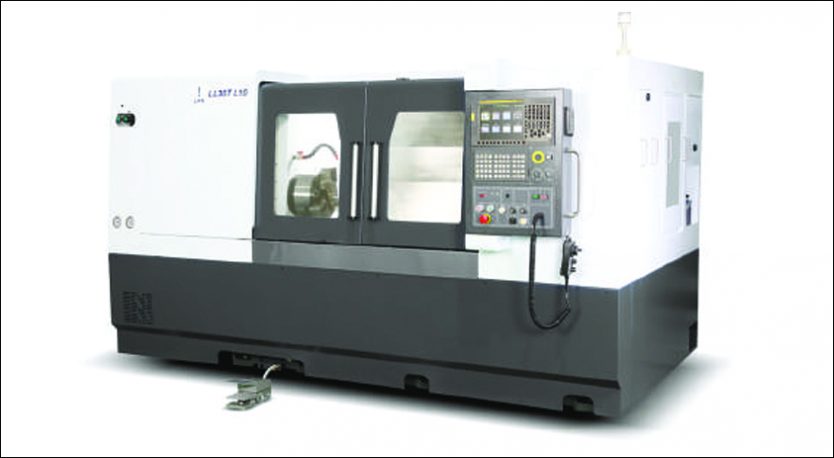
What role do CNC machine tools play in manufacturing, and what are their advantages?
In aerospace manufacturing, CNC machines are indispensable, presenting various benefits that contribute to the industry’s effectiveness and quality benchmarks. Among the primary advantages is their capability for elevated precision. CNC machines deliver remarkable precision and consistency, a pivotal necessity in aerospace, where strict tolerances are essential to guarantee the security and effectiveness of aircraft parts.
Flexibility is another key advantage of CNC machine tools. They can be reprogrammed to craft diverse components, showcasing remarkable adaptability to evolving production demands. This adaptability diminishes setup durations, streamlining the shift between distinct parts or production batches.
Furthermore, CNC machines supply valuable data for overseeing processes and quality control. Manufacturers can monitor the machining process through sensors and data recording capabilities in real-time. This data can be evaluated to identify anomalies, optimise machining variables, and ensure that each part meets the aerospace sector’s rigorous quality criteria.
CNC machine tools are the cornerstone of aerospace manufacturing, presenting outstanding precision, automation, adaptability, and data-driven insights. Their integral role in forming crucial aircraft elements underscores their significance in upholding the industry’s elevated safety, performance, and efficiency standards.
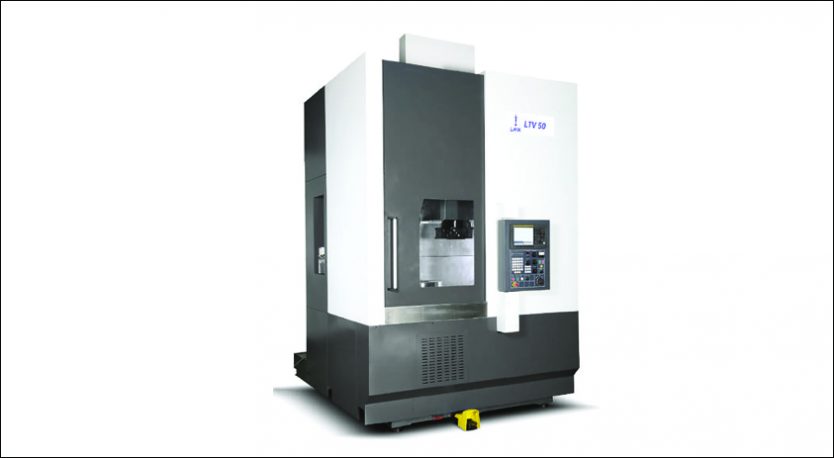
How do automation and robotics integrate with machine tools in aerospace manufacturing, and what benefits does it offer?
Automation and robotics have become essential components of aerospace manufacturing, offering a range of invaluable advantages. Firstly, they enhance efficiency by reducing cycle times and elevating production rates. Mainly, robots execute repetitive tasks with exceptional precision and uniformity, minimising errors and elevating the general quality of aerospace parts. Safety is another pivotal benefit since automation can take on hazardous tasks, shielding workers from potential dangers. Integration with CNC machines allows for uninterrupted operation, facilitating lights-out manufacturing, optimising efficiency and lessening periods of inactivity. Moreover, automation substantially contributes to ensuring quality by guaranteeing consistent processes, ultimately yielding higher-quality aerospace products that satisfy stringent industry benchmarks. Overall, automation and robotics have transformed aerospace manufacturing, amplifying efficiency, safety, and the overall quality of aerospace components.
Cookie Consent
We use cookies to personalize your experience. By continuing to visit this website you agree to our Terms & Conditions, Privacy Policy and Cookie Policy.