Advancements in automated MHE improving warehouse efficiency
By OEM Update Editorial July 1, 2024 12:43 pm IST
Introducing a paradigm shift in warehouse management, Sushil Kumar Rathi, Director at Allcargo Supply Chain, emphasises the impact of automated material handling systems. These advancements, integrated with AI and IoT technologies, optimise operational efficiency and space utilisation, lowering cost and enhancing precision in fulfilling orders across logistics settings.
What are the emerging trends in material handling equipment used in warehousing and logistics operations?
The landscape of material handling equipment is rapidly changing with technological advancements that aim to improve the efficiency, safety, and productivity of warehousing and logistics. Automated Guided Vehicles (AGVs) and Autonomous Mobile Robots (AMRs) are some innovations that automate movement between facilities. Robotic picking systems and smart conveyors increase accuracy and speed to fulfil requirements. Augmented Reality (AR) and Virtual Reality (VR) are used for immersive training and operational efficiencies. However, collaborative robots (cobots) work alongside human workers to improve productivity and safety. The RFID technology is used alongside drones for inventory management purposes, whereas global sustainability goals have led to the adoption of electric forklifts and other energy-efficient systems. Advanced Warehouse Management Systems (WMS) provide complete control over warehouse operations. As the rental of warehouses increases, LSPs are using 11-plus-meter high-reach trucks and articulated forklifts to optimise costs.
What advantages do advanced logistics and material handling solutions offer in enhancing supply chain efficiency and reducing operational costs?
Integrating advanced logistics and material handling technology can significantly improve supply chain efficiency and lower operational costs in Indian warehouses. Advanced automation machines provide efficient goods movement, cutting labour costs and increasing throughput. The use of IoT and AI allows for real-time monitoring and predictive maintenance. It helps to reduce downtime and optimise inventory management. Robotic picking systems and Smart conveyors boost order fulfilment, accuracy and speed, while RFID technology and drones help with inventory tracking. Also, using energy-efficient systems and sustainable practices lowers operating costs while supporting environmental goals. By embracing these technological improvements, Indian warehouses may improve efficiency, reduce costs, and increase competitiveness.
How do automated systems and real-time tracking impact distribution and order fulfilment processes?
Automated systems improve warehouse operations by eliminating manual labour and enhancing picking, packing, and shipping accuracy. Real-time tracking provides transparency and accurate cargo monitoring, resulting in faster delivery times and higher customer satisfaction. These technologies contribute to managing India’s complex and diverse logistics sector, solving issues such as road congestion and distant area delivery. As a result, they increase efficiency, lower costs, and provide a competitive advantage in India’s booming e-commerce and retail sectors.
How are advanced warehouse technologies improving logistics efficiency and competitiveness in India’s growing consumer and industrial sectors?
Advanced warehouse technology, such as conveyor belts, AGVs, stacker cranes, and autonomous robotic delivery systems, are revolutionising logistics in India. Conveyor belts boost material handling efficiency in industries such as FMCG and automotive by streamlining sorting and assembly processes. AGVs play an important role in autonomously delivering items, lowering labour costs and increasing safety, which is especially useful in fast-expanding e-commerce centres and large warehouses. Stacker cranes optimise vertical storage for maximising space in tight storage conditions like cold storage facilities. Autonomous robotic delivery systems increase productivity by automating order fulfilment processes. It improves operational flexibility and consumer happiness in India’s expanding e-commerce industry. These technologies jointly provide streamlined processes, cost reductions, and enhanced service levels, reinforcing India’s competitive edge in global logistics.
As India’s consumer and industrial sectors expand, these technologies are increasingly used to manage large numbers quickly and effectively. They play a role in preserving competitiveness in changing market conditions. The technologies also improve supply chain efficiency, optimising resource utilisation and ensuring nationwide delivery. With continual improvements to logistics infrastructure, these technologies continue to play a critical role in redefining how goods are managed and dispersed across the country.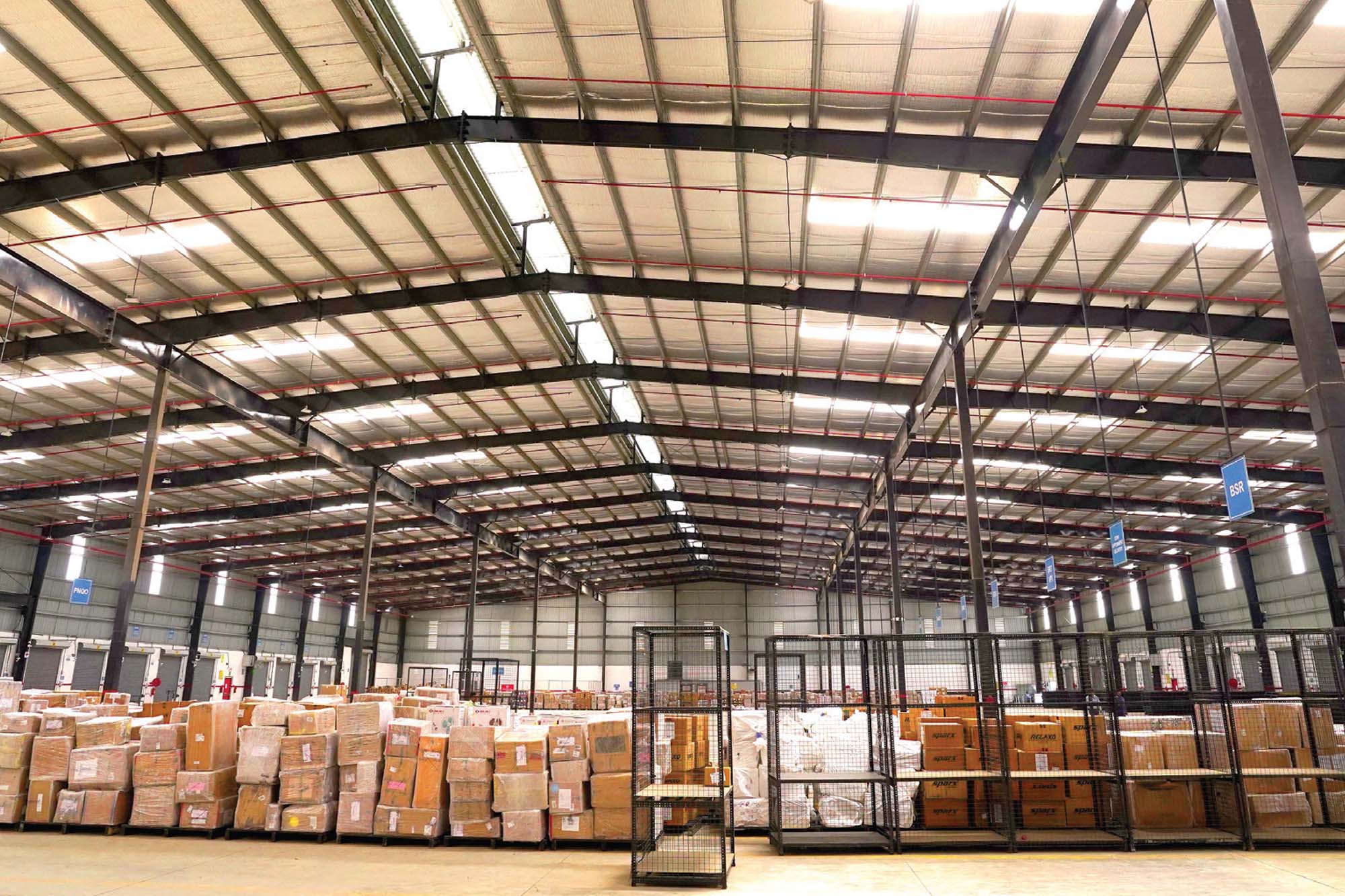
What benefits do AGVs and AMRs bring to logistics management?
Advanced logistics can be improved by automated systems that are easily deployed and flexible. They rely on an amalgamation of sensors, software, computation, and fast internet. Besides these robots handling and picking, the companies also use drones, AMRs or AVGs for material transportation. Being programmed for safety, AGVs and AMRs come with many sensors, cameras, and lasers, so they can move without colliding with people or buildings around them.
On the other hand, forklifts with other human-manned machines generally lack enough in-built safety mechanisms. They, therefore, depend on the operator’s judgement, thus making them prone to multiple dangers. Furthermore, these also contribute to a reduction in operational labour costs. Combining AGVs with a warehouse management or control system may lead to time savings in activities, like material ordering and inventory, through obvious faster accuracy and efficiency gains.
How do automated material handling devices improve efficiency and space usage when integrated with warehouse and inventory management systems?
Automated material handling systems reduce processing times and increase throughput by streamlining manufacturing and warehousing processes and automating tasks like picking and sorting. Further, material transportation helps organisations to maintain a constant flow of work while reducing bottlenecks and downtime. Automated solutions can better use its warehouse space, resulting in more effective operations and more accurate and timely order processing. Automated systems minimise errors associated with manual handling, leading to greater order fulfilment and inventory management accuracy. Optimised material flow and reduced handling requirements result in lower material handling costs.
What factors should warehouse operators consider when selecting MHE to optimise efficiency, productivity, and safety?
In warehouse operations, choosing the right material handling equipment is a factor to maximise efficiency, productivity, and safety. Survey the warehouse area to assess equipment needs, measuring aisle widths, ceiling heights, and storage configurations. Conducting a comprehensive examination allows you to calculate the equipment space that meets the customer’s needs, whether handling bulk commodities, fragile things, or specialist products.
Calculate the maximum load capacity of the equipment to maximise its lifespan and performance, considering factors like material density, size, and changes in packaging. Easy-to-use equipment enhances operational efficiency, reduces error rates, and fosters employee confidence and satisfaction.
Cookie Consent
We use cookies to personalize your experience. By continuing to visit this website you agree to our Terms & Conditions, Privacy Policy and Cookie Policy.