Temperature measurement solutions enrich productivity
By Staff Report November 30, 2024 5:26 pm IST
Inadequate temperature control equipment can compromise product quality, leading to defective equipment, unplanned downtime, costly repairs, and process inefficiencies. Prashant Sinha, Marketing Head at WIKA India, shares the importance of temperature measurement in manufacturing across different sectors.
What are the most effective methods for temperature measurement in manufacturing across different sectors?
We specialise in measurement technology, offering tailored solutions for pressure, temperature, force, and flow measurement. With diverse temperature measurement products, we ensure quality, safety, and efficiency in industries and cater to operational needs.
Resistance temperature detectors (RTDs) are highly accurate and stable tools for temperature measurement, essential in pharmaceuticals and food processing thermocouples. They have high durability and faster response times, which makes them ideal for extreme environments like metal processing and power plants. We specialise in customising these solutions for various industries and specific application needs. Each solution is carefully selected based on the required temperature range, response time, and environmental conditions, ensuring operational efficiency.
How can temperature measurement be integrated into manufacturing to ensure sensor and control equipment accuracy and reliability?
Integrating temperature measurement systems into manufacturing processes improves reliability, operational excellence, and product quality, reduces material waste, and ensures safety and regulatory compliance. Our sensors are installed at control points for real-time monitoring, enabling automation and IoT integration. This proactive response minimises deviations, maximises efficiency, and reduces downtime.
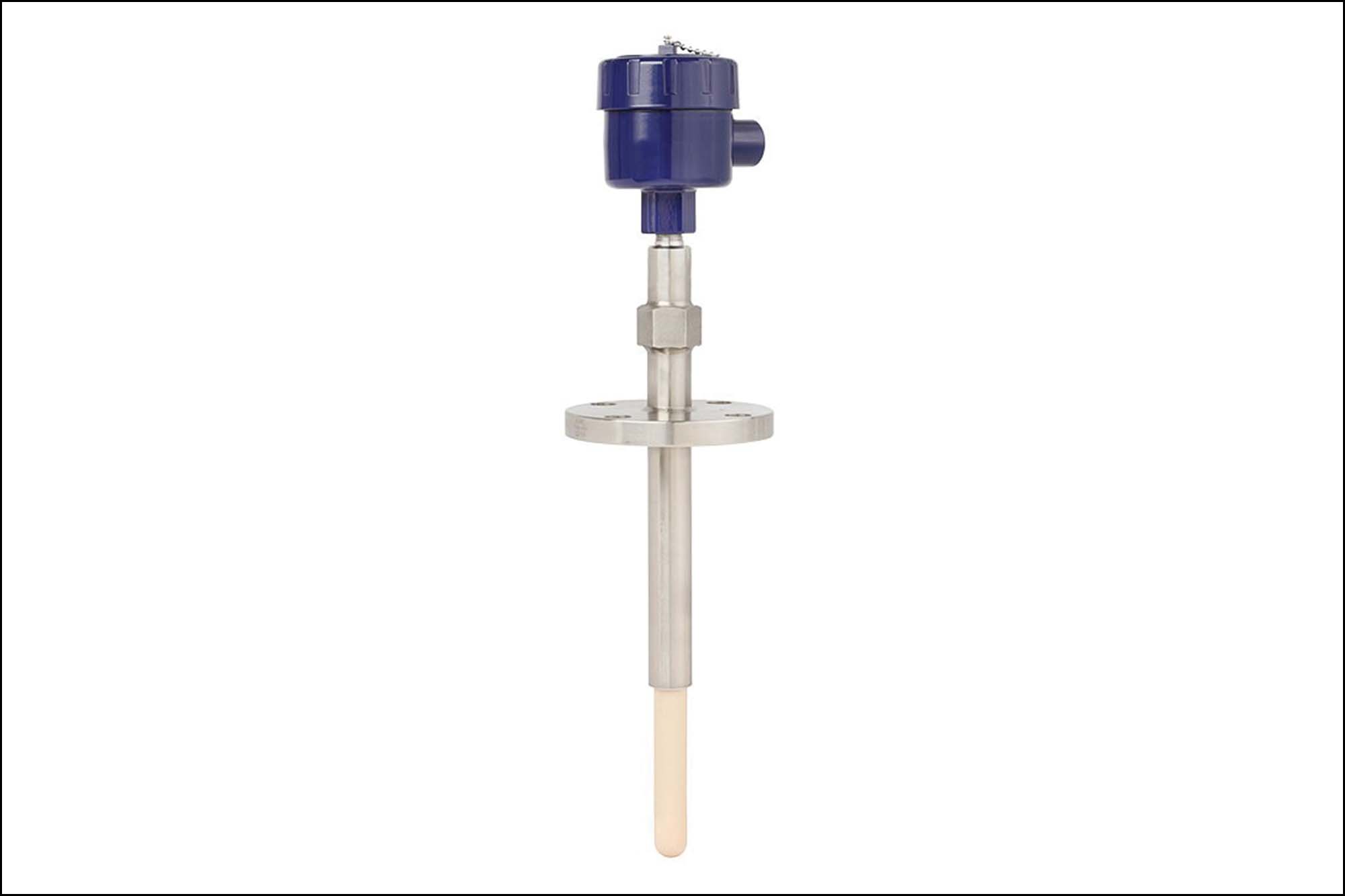
Regular calibration maintains the accuracy and longevity of measurement systems. A redundant design with multiple sensors minimises failure risks and makes operations uninterrupted. This dual-layer approach instils confidence in the process and reliability, enabling industries to stay ahead in operational precision. By adopting robust temperature measurement practices, industries can meet the operational precision and the demands of today’s fast-paced manufacturing landscape.
How does inadequate temperature control equipment affect product quality?
Inadequate temperature control often compromises product quality, leading to defective equipment. Overheating or repeated thermal cycling can reduce machinery’s lifespan, leading to unplanned downtime and costly repairs. It can also lead to process inefficiencies as energy intake increases without sufficient heating or cooling, driving operational costs and reducing sustainability.
The success in such scenarios is an investment in high-quality temperature measurement solutions. We have a long-standing reputation as a leader in temperature measurement technology and offer precise and reliable temperature sensors, ensuring manufacturers can achieve accurate control. Our expertise in creating temperature sensors ensures manufacturers achieve precise control of processes, improved product quality, extended equipment life, and standard compliance.
What are the challenges for pharmaceuticals, semiconductors, aerospace, etc., in having precise temperature control?
Industries like semiconductors, aerospace, and pharmaceuticals face multiple challenges maintaining precise temperature control. This is primarily due to the tight tolerances required for their operations. Small temperature variations can disrupt sensitive production processes, impacting product quality and performance. In semiconductor manufacturing, environmental fluctuations, which often relate to variations in ambient temperature, affect the production processes and pharmaceutical manufacturing, necessitating precise temperature control for high-quality drug production.Many materials used in these sectors show temperature sensitivities. For example, active ingredients in pharmaceuticals can degrade if subjected to temperatures during storage and processing, resulting in ineffective or dangerous products. Temperature-reading sensors and control equipment can wear down over time, causing a drift in the readings. Advanced technology and proactive maintenance are important for addressing challenges in temperature measurement, with our high-quality sensors and stable calibration routines ensuring the long-term reliability of complex processes.
What is the role of calibration and traceability in temperature measurement?
Calibration with traceability determines temperature-measuring system characteristics by comparing sensor output to a known standard against national or international standards. This helps identify and rectify deviations, ensuring process or plant integrity, especially for sensors used in regulatory-sensitive applications.
On the other hand, traceability links measurement devices and globally recognised standards, ensuring consistency across different industries and locations. They provide the foundation for reliable and repeatable measurements.
Companies must maintain detailed records of the calibration of all measuring devices to ensure compliance. Accredited laboratories for recalibration services should be utilised, as these labs operate under strict quality systems such as ISO 17025. Manufacturers should look for dependable service providers with a solid market reputation who follow internationally recognised standards and have structured compliant processes.
How does developing non-contact temperature measurement technologies improve efficiencies and enhance safety?
Non-contact technologies like infrared sensors and thermal imaging are revolutionising the monitoring and control of temperature for manufacturers. Technologies improve safety by allowing individuals to measure temperatures in hazardous or hard-to-reach areas without direct exposure, minimising risks due to high heat, dangerous substances, or confined spaces.
Non-contact measurement systems offer fast, precise temperature data, enabling manufacturers to detect thermal anomalies early. This reduces energy losses and optimises system performance, improving energy efficiency and sustainability initiatives and reducing operational costs.
We offer a comprehensive range of non-contact temperature measuring solutions, from infrared sensors to precision and thermal imaging systems. Where direct measurement at proximity may pose risks due to exposure to extreme temperatures or hazardous conditions, infrared and thermal imaging technologies take over temperature measurement tasks and improve operators’ safety.
Cookie Consent
We use cookies to personalize your experience. By continuing to visit this website you agree to our Terms & Conditions, Privacy Policy and Cookie Policy.