Parts, whole, and complete
By Staff Report December 31, 2024 3:00 pm IST
From precision-engineered fasteners to cutting-edge EV batteries, the automotive components industry is changing the face of mobility with lightweight materials, advanced simulations, and sustainable innovations. The vehicles of next-gen vehicles are no less than a wonder to watch with the auto-operated doors and sensors for advanced safety. Automotive components are also evolving with these changes, and we learn about the progress with this article.
The automotive industry is going through a massive technological transformation, propelling the component manufacturing industry to follow the same path. From the rapid growth of EVs and the push towards smart vehicles, the industry’s transformation requires rapid technological advancements, increased scalable computing platforms, and new business models to work together.
The auto components industry in India is a rapidly growing sector, with a turnover of Approx $70 billion in 2022-23, representing a 33% growth from the previous year. The industry is expected to reach $200 billion by 2026 and is one of the backbones of the Indian Economy. Vishal Bhatnagar, CEO & Managing Director, MVD AUTO COMPONENTS Pvt Ltd, shares that, “There is a growing presence of global automobile Original Equipment Manufacturers (OEMs) in India with companies like Daimler, Toyota, Honda, Kia, etc setting up factories in India. Companies like Suzuki are exporting cars made in India back to Japan. The localisation of components is increasing with high technology components now being produced here.”
We have also witnessed the rise in exports of auto components, which are targeted to grow fivefold in the next ten years. The current geopolitical environment is pushing many big companies, especially in the USA and Europe, to look for alternatives to China in countries like India.
The aftermarket segment is expected to reach $14 billion by 2028 because more and more people are buying personal vehicles due to increased disposable incomes. Also, the government has shifted its focus on Make in India. The auto components industry is in the limelight with schemes like PLI (Production Linked Incentives), which provide financial incentives to boost domestic manufacturing of advanced automotive technology products.
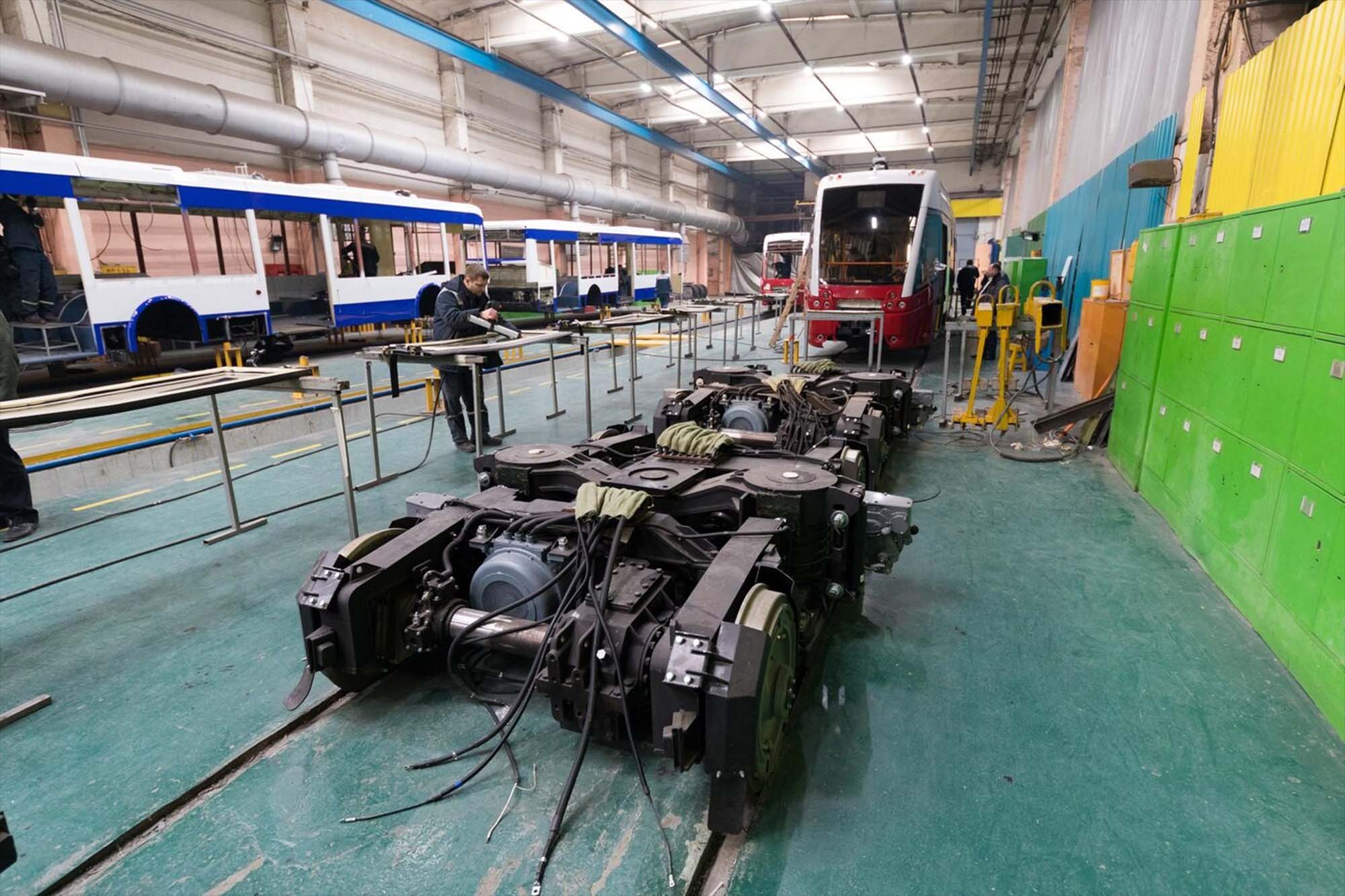
Simulation
When we talk about technological advancement, simulation becomes one of the major aspects of automotive component manufacturing. Himadri Sen, Regional Operational Excellence Head (GM), Piramal Pharma Ltd., shares, “In the automotive component manufacturing industry, we adapted the latest tools of Industry 4.0, Quality 4.0, to enable greater productivity and quality in manufacturing a while ago. This also helped manufacturing processes het leaner and set the foundation for long-term competitiveness. We leveraged advanced manufacturing technologies — such as Artificial Intelligence (AI), automation, robotics, simulation, digital manufacturing, and others —to deliver differentiated products at scale with efficiency, agility, and speed.”
Now, we use Industry 4.0 technologies like modeling ( E.g. CATIA, PRO-E etc.) and simulation early in the product lifecycle to ensure that our automotive customers can be assured of greater efficiency and lower risk further down the line when they’re producing at scale. For example, within a design for manufacturing (DFM), modelling and simulation are used to determine how to achieve the highest yield with the fastest cycle times before a product reaches the manufacturing stage. DFM guidance helps companies ensure that product designs are manufacturable, eliminating scrap and bottlenecks while maximising product performance.
Another big benefit of simulation in the automotive industry is during the production part approval process (PPAP), which is a strictly documented process ensuring products delivered to customers meet their performance, quality, and delivery requirements. Now, we use simulation to speed this process, building out production flows in software iteratively until we can be confident that we have the required capacity and capabilities before we build products in real life.
This approach saves months of time and resources, enabling automotive manufacturers to accelerate next-generation mobility while maintaining quality, safety, and resiliency. We can streamline serial production by gathering early input into the process failure mode and effects analysis (PFMEA). By simulating production lines and processes, we can quickly identify areas of highest risk and key bottlenecks and then develop and implement risk mitigation strategies in advance.
Component design and production
EVs require fewer parts than internal combustion engine (ICE) vehicles, which has led to the obsolescence of some traditional components like fuel injectors and exhaust systems. However, there is a growing demand for EV-specific parts, such as battery systems and electric motors. Similarly, the focus has been on manufacturing with lighter and more compact parts. This has led to more innovation and opportunities in battery technology and faster charging.
Lightweight materials
Lightweight materials like carbon fibre and aluminium are revolutionising the automotive industry, offering several key advantages that significantly improve vehicle performance and safety. These materials streamline fuel efficiency and performance by reducing weight. Carbon fibre and aluminium are much lighter than traditional steel. This weight reduction improves fuel efficiency because the engine needs less energy to move the vehicle. In EVs, lighter materials can also extend range, as the vehicle’s energy consumption is reduced.
Lightweight material enhances safety as it impacts absorption. In the event of a collision, these materials can absorb and dissipate energy more effectively, helping to reduce the impact forces experienced by occupants. In particular, aluminium crumple zones can be engineered to deform in a controlled way, while carbon fibre can be used strategically for reinforcement without adding much weight.
Aluminium is highly resistant to corrosion, which increases the lifespan of vehicle parts exposed to weather conditions, road salts, and other corrosive factors. Carbon fibre doesn’t rust, contributing to durability and longevity, especially for structural components or body panels exposed to the elements. Carbon fibre, in particular, offers exceptional design flexibility. It can be moulded into complex shapes with high precision, allowing for streamlined, aerodynamic bodywork that enhances vehicle efficiency. This is particularly beneficial in motorsports and performance cars, where aerodynamics is crucial. The use of lightweight materials opens up new possibilities in vehicle architecture. For instance, car manufacturers can optimise frame designs and internal structures to be lightweight and safe without compromising the vehicle’s integrity.
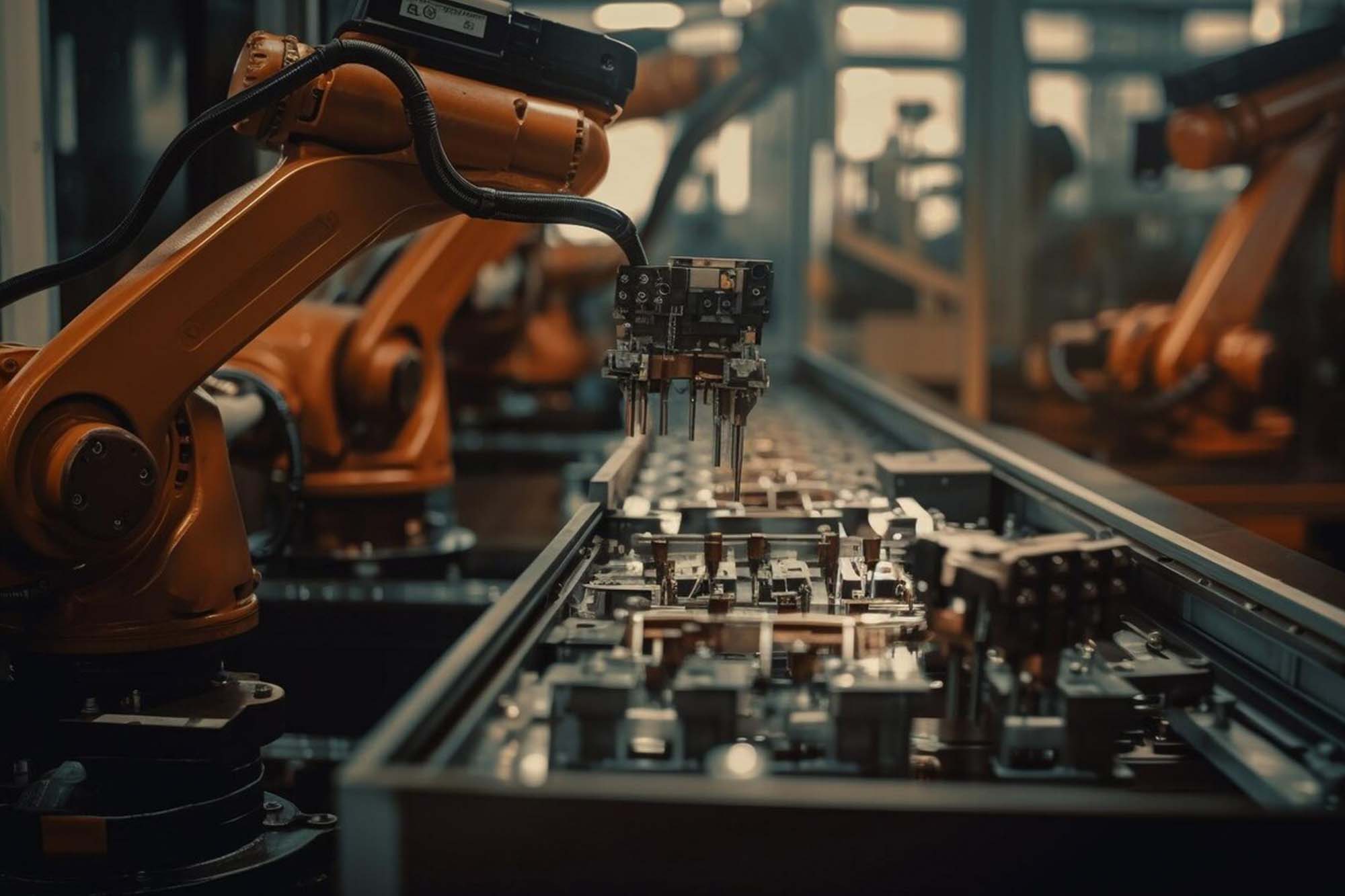
The main challenge with lightweight materials like carbon fibre is the cost. Carbon fibre, in particular, is more expensive than steel or aluminium, and the manufacturing processes can be complex and energy-intensive. However, prices are expected to decrease as technology advances and production methods scale up. While the upfront cost is higher, overall fuel efficiency, maintenance, and repair savings can offset the initial investment over time, particularly for high-end, performance, and luxury vehicles.
Aluminum is one of the most recyclable materials on the planet, and using it in vehicles helps reduce the overall environmental footprint. Carbon fibre is more challenging to recycle, though research into circular economy solutions and recycling technologies is ongoing, and new methods are being developed to reuse carbon fibre efficiently.
As the auto industry shifts toward EVs, lightweight materials optimise battery range and performance. Reducing weight allows EVs to travel farther on a single charge and enhances overall efficiency.
Performance and reliability of components
We can reduce the weight of the components, but that cannot happen at the expense of performance. Ajay Tanwani, MD of Kanal Enterprises, shares that they have adopted automation for the rapid production of components such as washers, clips, screws, and bolts and achieved high output rates per minute. They redesigned parts and processes for high-temperature and high-torque applications for superior performance. Their expertise in clipping, clamping, PVC coating, special fasteners, and spring steel materials has been instrumental in addressing the toughest anti-vibration and high-torque requirements across various industries. Focusing on high-performance materials has ensured their exceptional durability and reliability in every solution. He shares an instance where an industry OEM manufacturer faced fastener loosening in high-torque assemblies, causing downtime and increased maintenance. Kanal Enterprises engineered custom conical washers using high-strength materials and optimised geometry for load distribution and torque resistance. Advanced in-house testing replicated customer assembly conditions, ensuring performance reliability. They used specialised coatings for improving friction and slippage prevention, and iterative prototyping incorporated client feedback. The solution reduced fastener failures by 95% and enhanced uptime.
Customer expectation
This brings us to what customers expect from the product manufacturer. The prime expectations of any customer are quality products, competitive prices, and timely deliveries. Vishal Bhatnagar shares that when it comes to the automotive industry, customers expect components to meet and exceed OEM specifications and industry standards. Consistent quality, delivery, and performance should be consistent across all supplies and deliveries. Continuous innovation and improvements in products, materials, and manufacturing processes give the manufacturer an edge.
Comprehensive warranty, dedicated customer support, and after-sales service should be strong. On-time delivery and flexible logistics solutions are bonuses, as they assure customers that their requirements are met promptly without burdening them with excessive stores. JIT (Just in time) deliveries are the expectation for most.
Customers must be able to customise products as per their vision and developments. As sustainability becomes a standard expectation, products should be eco-friendly, feature sustainable packaging, and be manufactured in compliance with industry certifications and regulations.
—————————————————————
Vishal Bhatnagar, CEO & Managing Director, MVD AUTO COMPONENTS Pvt Ltd.
“Localisation, exports, and government initiatives like PLI fuel the Indian auto components industry. It is poised for exponential growth with customers expecting quality, innovation, and sustainability.”
Himadri Sen, Regional Operational Excellence Head (GM), Piramal Pharma Ltd.
“Advanced simulation and lightweight materials are very prominent moving ahead in automotive components for producing sustainable solutions for next-generation mobility.”
Kanal Enterprises, MD, Ajay Tanwani
“CNC machining and material innovation delivers zero-defect automotive components for the scalability of the evolving demands of electric vehicles and high-torque applications.”
Cookie Consent
We use cookies to personalize your experience. By continuing to visit this website you agree to our Terms & Conditions, Privacy Policy and Cookie Policy.