AI, VR, and IIoT for the future of manufacturing
By Staff Report October 1, 2024 7:12 pm IST
“Integrating technologies like AI, data analytics, VR, IIoT, and 5G is transforming manufacturing. Companies that invest in these advancements today will lead the future, driving innovation and sustainable growth. Inovance Technology, with its forward-looking approach, is dedicated to helping manufacturers embrace Industry 4.0 and unlock its full potential, says Anil Kumar, Managing Director of Inovance Technology India.
How can manufacturers overcome the challenges of integrating AI, data analytics, and VR tools into production processes?
The key issues of integrating AI, data analytics, and VR into production lines are technological compatibility and data management. The massive influx of data requires a robust infrastructure to efficiently process, analyse, and convert it into actionable insights. Workforce readiness is crucial, as employees need upskilling to use these tools and technologies effectively.
Manufacturers can overcome these hurdles through modular, scalable solutions and partnering with providers like Inovance Technology. Inovance’s motion control systems and EtherCAT-based servo solutions offer the flexibility and speed required to integrate AI algorithms for real-time process optimisation. These systems can process large datasets for manufacturers to make timely, data-driven decisions. Inovance’s AI-powered analytics tools also enable enhanced machine learning models that predict failures, optimise production schedules, and minimise downtime.
What strategies can organisations employ to utilise IIoT data?
The Industrial Internet of Things (IIoT) has become a critical component of modern manufacturing. However, the real challenge lies in effectively using the vast amounts of data generated by these interconnected devices. Organisations can use centralised data platforms to create a single source of truth for consistent data flow and eliminate silos across the enterprise. Real-time analytics enables immediate data processing to provide actionable insights that help businesses make timely, informed decisions for their operations.
Inovance’s PLC and HMI solutions offer real-time connectivity between the shop floor and the enterprise level to transform IIoT into valuable operational insights. These systems empower operators with live information that can drive efficiency and flexibility.
How can a unified digital platform add value to manufacturing operations and achieve optimised processes?A unified digital platform consolidates all data sources, processes, and tools in one place for greater control over the entire manufacturing workflow. This centralisation enhances cross-departmental collaboration, as all stakeholders can access the same data, improving communication and decision-making. The platform also supports the automation of repetitive tasks by using AI and machine learning, which boosts productivity and streamlines operations for more efficient processes.
Inovance’s automation software suite unifies various operational layers, from machine-level control to enterprise resource planning (ERP) systems. This level of integration adds immense value by delivering a cohesive operational picture that contributes to lean manufacturing.
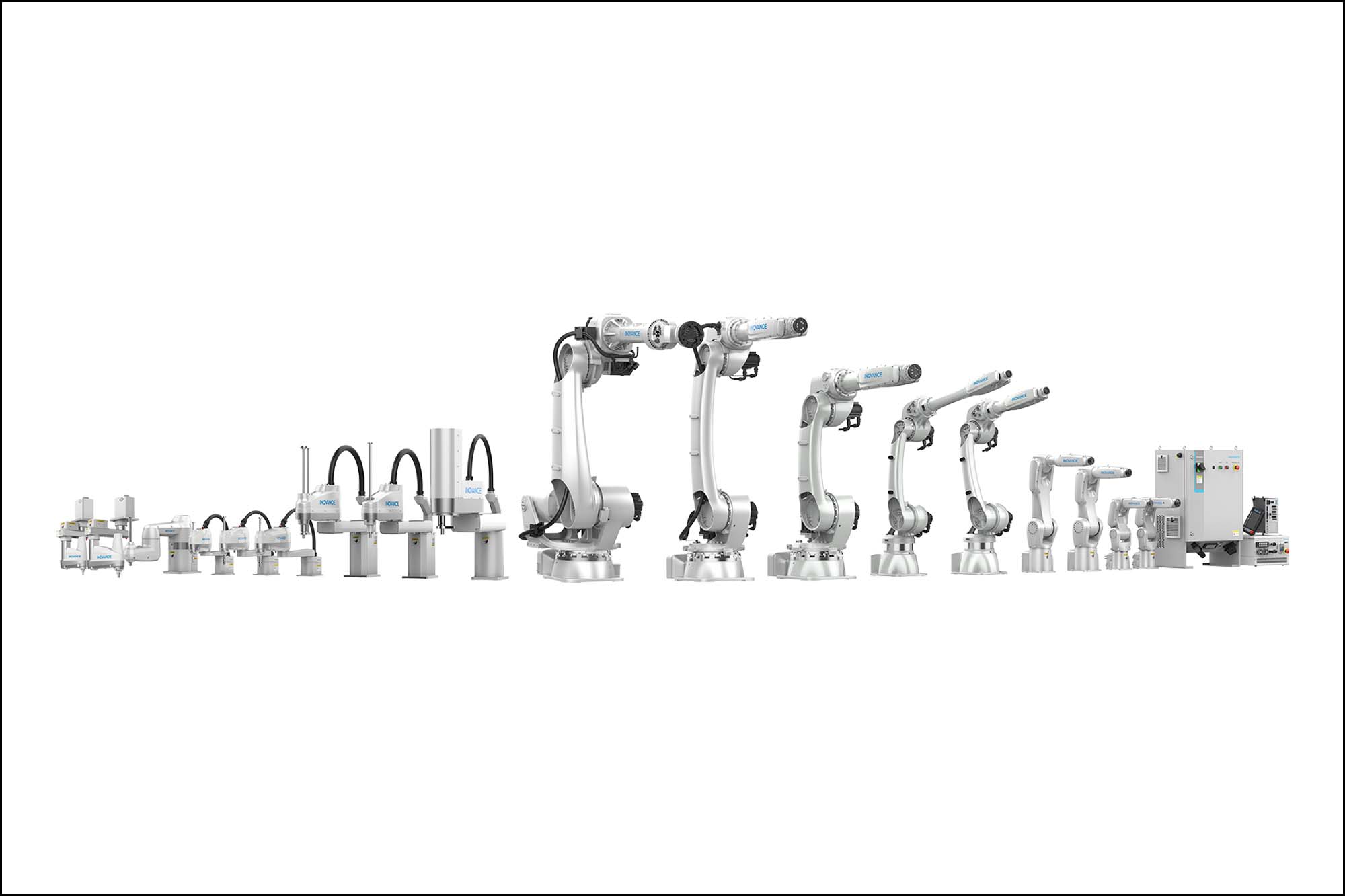
How do remote monitoring and predictive maintenance sensors increase value in manufacturing facilities?
Remote monitoring and predictive maintenance sensors help reduce downtime by using predictive analytics to detect potential equipment failures for proactive repairs before issues escalate. These technologies also contribute to cutting maintenance costs by optimising maintenance schedules based on real-time data, extending the lifespan of equipment and reducing unnecessary expenses. These sensors also enhance safety by continuously monitoring critical parameters, ensuring that equipment operates within safe limits and thus minimising risks.
Remote monitoring solutions, predictive maintenance sensors, and Inovance’s motion control systems give manufacturers real-time visibility into machine health. This allows for predictive maintenance schedules that drastically reduce unscheduled downtime and improve overall equipment effectiveness (OEE).
Cookie Consent
We use cookies to personalize your experience. By continuing to visit this website you agree to our Terms & Conditions, Privacy Policy and Cookie Policy.