Engineering ideal gear ratios for torque control
By Staff Report November 16, 2024 12:05 pm IST
A reducer motor uses mechanical transmission systems to achieve the desired output speed and torque. The gear ratio selection is influenced by the application’s requirements, design, and manufacturing costs of the gear motor.
Gear ratio in reducer motors
A reducer motor uses mechanical transmission systems like planetary, worm, and cylindrical gears to achieve the desired output speed and torque. The gear ratio, or reduction ratio, is the ratio of rotational speeds between the transmission system and the rotor on the motor output shaft. The gear ratio can be calculated using the formula: gear ratio = output shaft speed/input shaft speed, where output shaft speed represents the rotational speed after transmission and input shaft speed refers to the motor’s speed. This helps in gear design or selection reference.
Gear ratio refers to the change in motor speed output, which can vary depending on the application, as some motors typically output higher speeds. At this point, the gear motor reduces the output shaft’s speed through a reduction device, ensuring the appropriate speed is provided.
The gear ratio selection is influenced by the application’s requirements and the gear motor’s design and manufacturing costs. Generally, the gear ratio of a gear motor is determined by the required speed and torque ratio. A larger reduction ratio is needed for high-torque and low-speed output, while a smaller one is directed for high-speed and low-torque output.
The gear ratio selection affects the gear motor’s performance, as larger ratios increase size and weight, potentially impacting efficiency. Power requirements, size restrictions, weight requirements, and efficiency should be considered when choosing a gear ratio to ensure the motor’s optimal performance.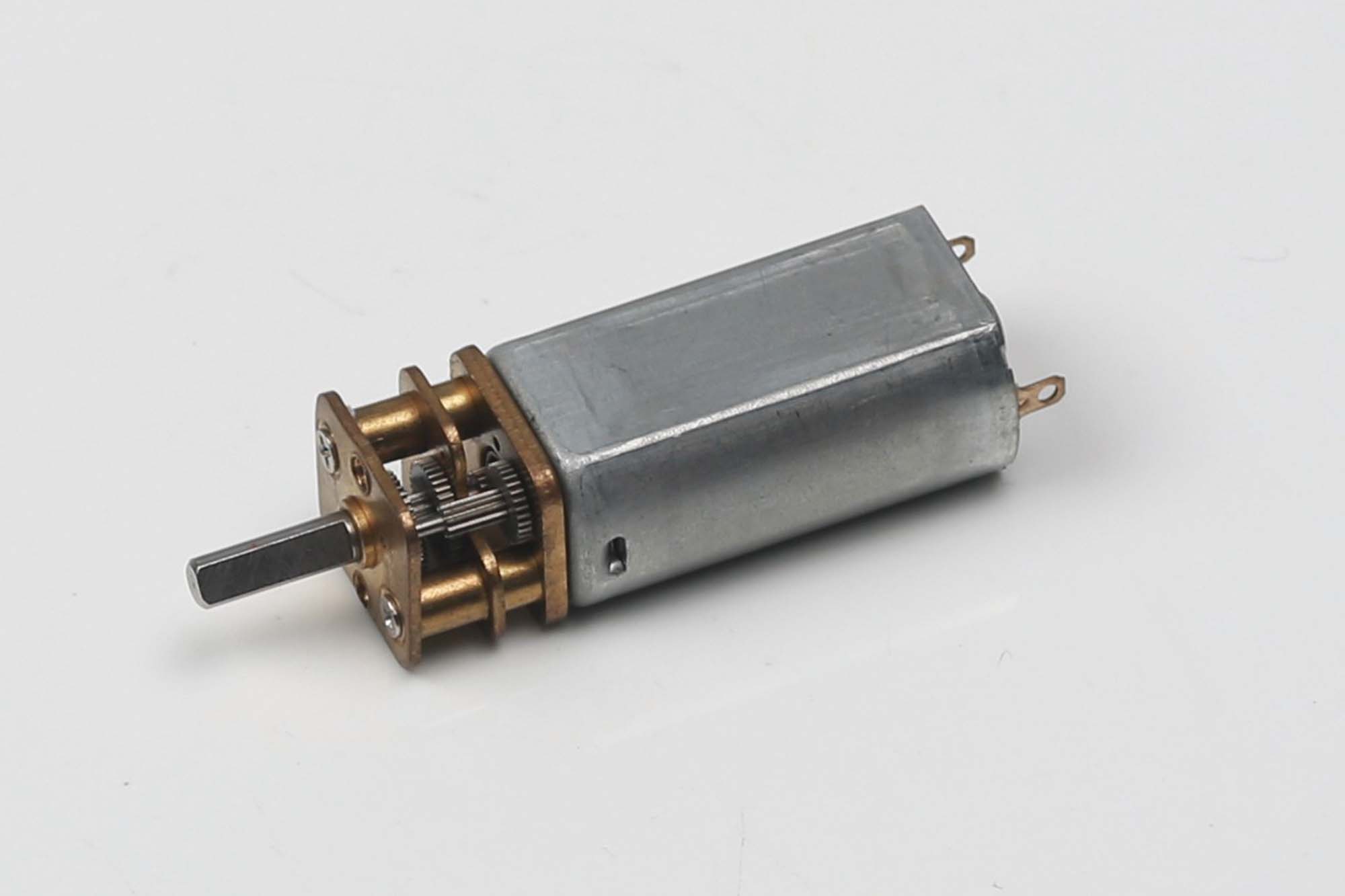
The ratio of a gear motor is typically determined by the gear ratio within the reduction device, which may include the number of teeth on the gears or worm gears. For example, if the output gear on the reduction device has 15 times more teeth than the input gear, the reduction ratio is 15. However, in some cases, some gear motors can be adjusted to provide different gear ratios.
The choice of gear ratio is crucial for the specific applications of gear motors. Gear motors are widely used in various mechanical equipment, such as machine tools, conveyors, printing machines, wind turbines, etc. Different application areas have different requirements for the gear ratio. Some applications require a larger gear ratio to provide greater torque, while others need a smaller one to offer higher speed.
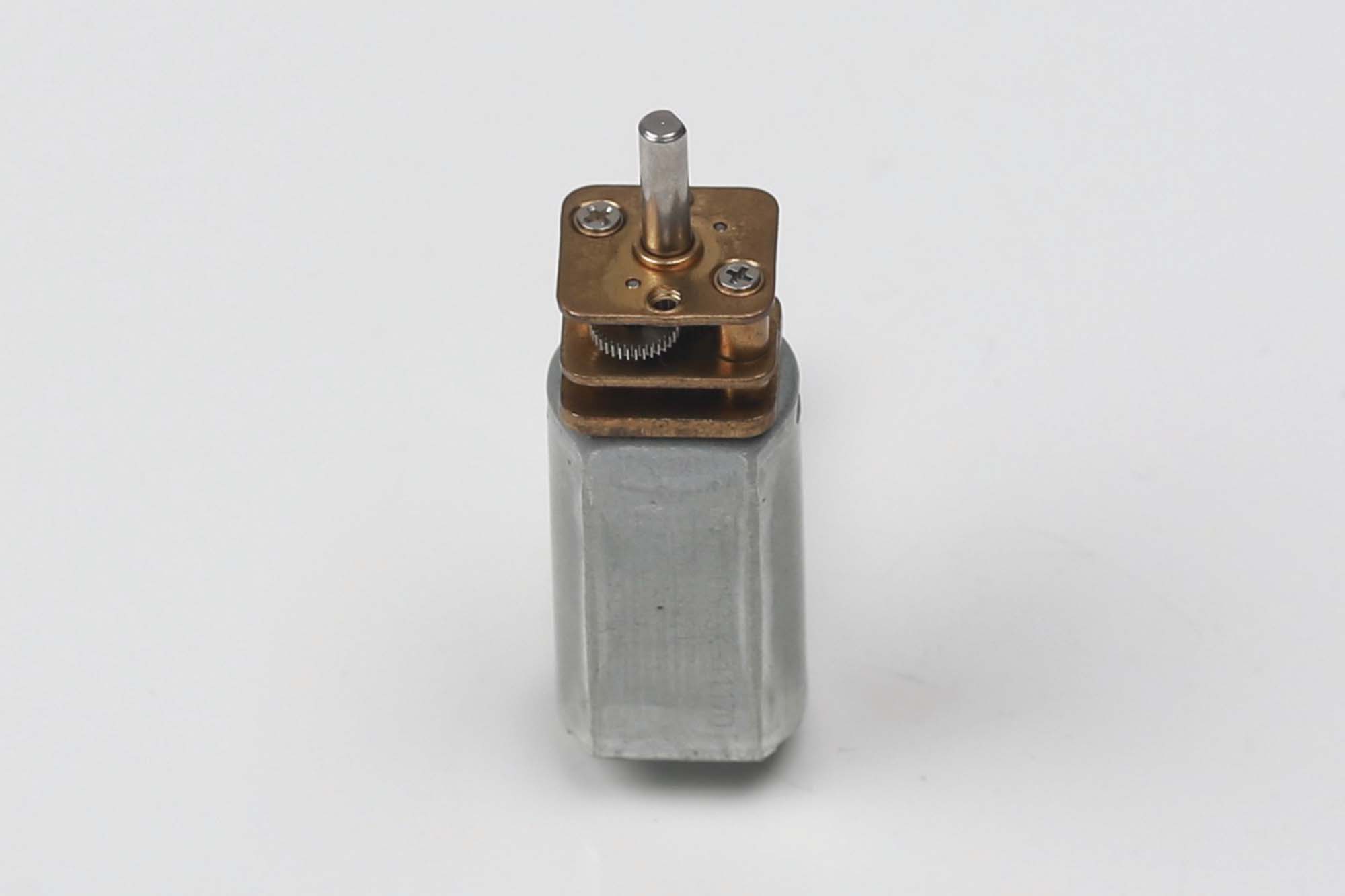
Gear motors possess performance parameters like rated speed, power, torque, and gear ratio. When choosing a gear motor, it’s important to consider all parameters comprehensively, including gear ratio and other performance parameters, to ensure it operates properly under specific application conditions and meets the user’s needs.
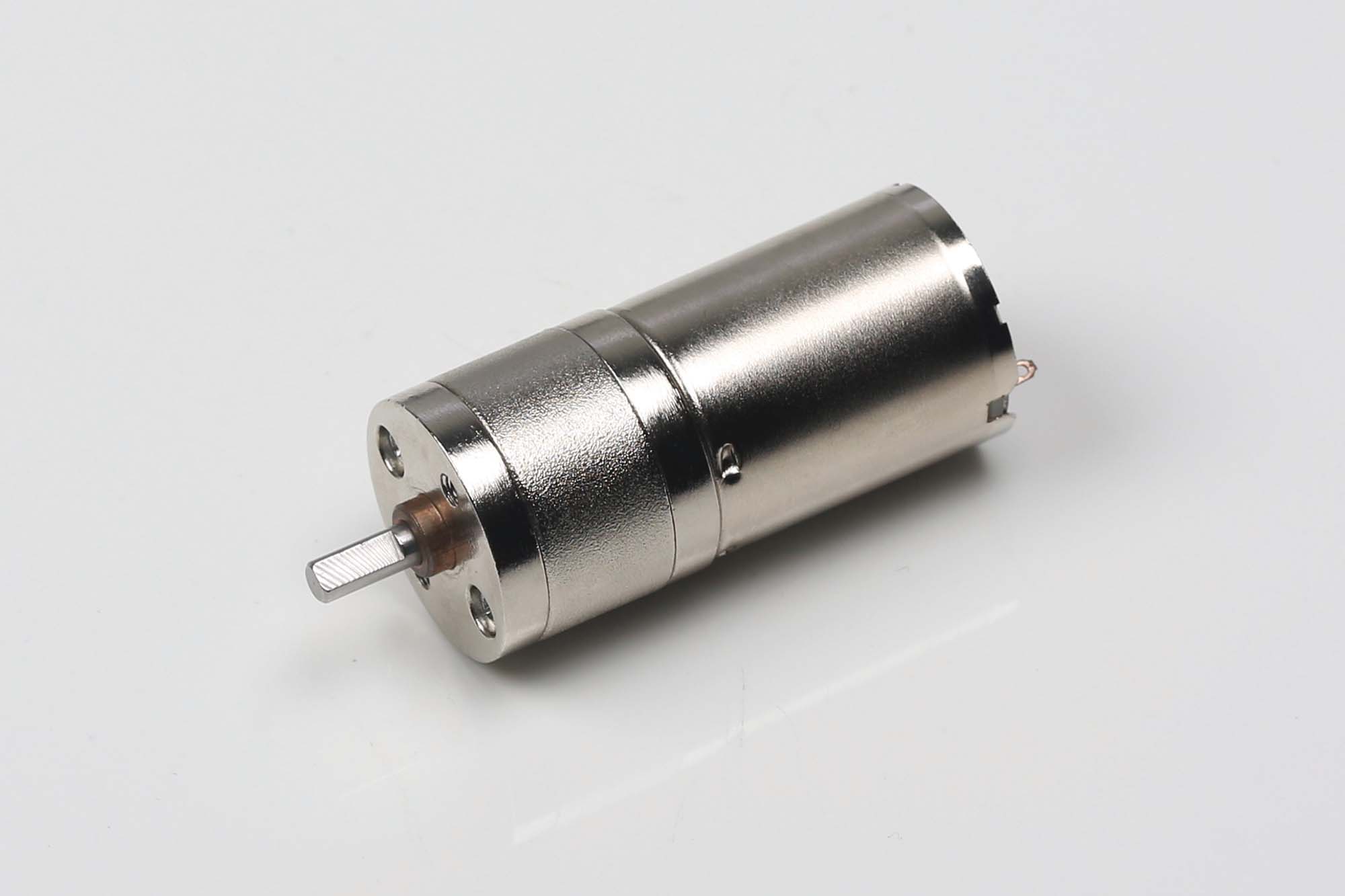
The gear motor’s ratio is also the rotational speed ratio between the reduction device and the rotor on the motor’s output shaft. The selection of the reduction ratio needs to be based on application requirements and a systematic consideration of its impact on performance. The gear ratio is an important factor influencing output speed and torque and significantly impacting the operation and performance of various mechanical devices.
Cookie Consent
We use cookies to personalize your experience. By continuing to visit this website you agree to our Terms & Conditions, Privacy Policy and Cookie Policy.