Inside the Chitale Bandhu factory
By Staff Report April 8, 2025 5:08 pm IST
Chitale Bandhu’s iconic bakarwadi from Pune needs no introduction. But behind this beloved snack lies a rich legacy that dates back to 1939, when the Late Bhaskar Ganesh Chitale started a milk distribution business in the Sangli district. In the 1950s, Raghunath Chitale extended to establish Chitale Bandhu Mithaiwale. Chitale Bandhu envisioned meeting the growing demand for food products and reducing the need for expensive foreign investments.
OEM Update had the opportunity to step inside the heart of this legacy—the renowned Chitale Bandhu factory—alongside Indraneel Chitale, Managing Partner at Chitale Bandhu. We got an exclusive look at how tradition meets technology, as they have fully automated their bakarwadi-making process, ensuring consistency, efficiency, and the same irresistible taste that has won hearts for generations.
As we step onto the sprawling 20-acre Ranje manufacturing unit of Chitale Bandhu in Pune, Maharashtra, the aroma of freshly prepared sweets and snacks fills the air. This is no ordinary facility—it is a testament to decades of resilience, innovation, and an unwavering commitment to quality. From its humble beginnings in 1939, when Bhaskar Ganesh Chitale founded Chitale Dairy, to its evolution into a globally recognised brand present in 65+ countries, the company has embraced change while preserving its traditional essence.
Automating future of FMCG
Our journey begins at the bakarwadi production unit, where an astounding 17,000 kg of bakarwadi is manufactured daily. What is surprising? The lack of human intervention. The entire process is largely automated—a handful of workers feed raw materials at the start, and another few oversee packaging at the end. Everything in between, from shaping to frying to quality control, is handled by high-tech machinery. Adjacent to this facility is the sweet-making unit, where traditional delicacies like gulab jamun and kaju katli are produced. Here, too, human intervention is limited to the initial and final stages—ensuring that the process remains efficient, consistent, and error-free.
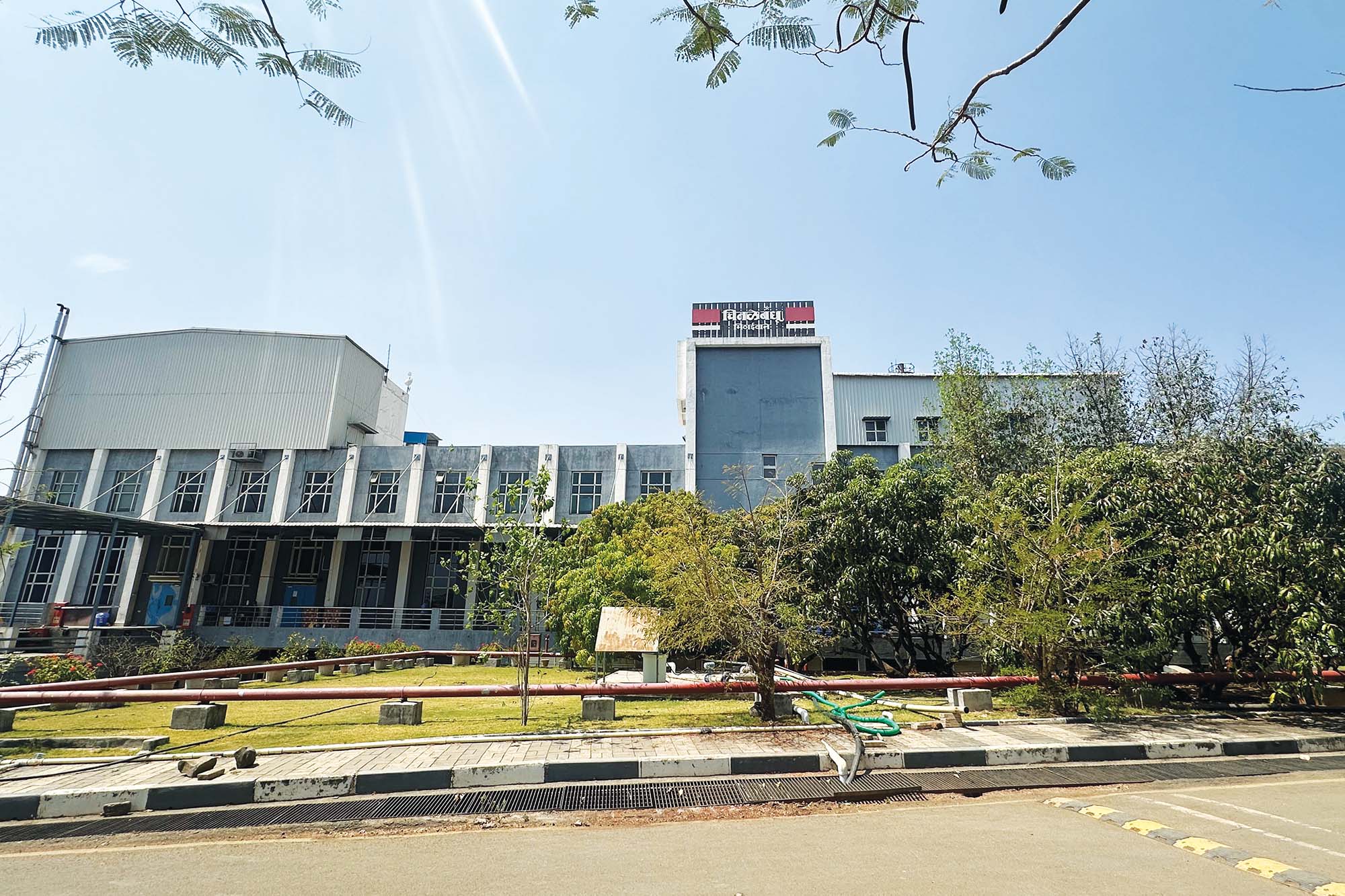
Pioneers in automation
Chitale Bandhu is the first company to fully automate the bakarwadi production process. Indraneel Chitale, Managing Partner and the third-generation leader, explains their approach: “Our focus is on automating processes prone to errors. The goal is not to replace human labour entirely, but to enhance quality assurance, consistency, and efficiency.”
While automation demands heavy investment, it pays off in terms of brand value and consumer trust. In the FMCG sector, where quality consistency is paramount, the investment in cutting-edge foreign-manufactured equipment ensures strict compliance with food safety regulations—something Indian manufacturers are gradually catching up on.
Data-Driven Decision Making
A remarkable 80% of the new facility is automated, requiring massive data collection and analysis. Every process, from ingredient input to packaging, is tracked via IoT sensors, PLC systems, and advanced analytics. This data helps Chitale Bandhu improve efficiency, optimise costs, and maximise profit margins.
The company partners with third-party industrial automation experts to maintain real-time visibility of every operational detail. Each machine’s efficiency is tracked as a key performance indicator (KPI) to ensure optimal production output and minimise wastage.
Inventory and Quality Control
Inventory management at Chitale Bandhu is a fine-tuned science. Unlike traditional FMCG businesses, they prioritise high inventory turnover over stockpiling. Through software-driven analytics, they determine what to produce, when, and how much—ensuring that customers always receive the freshest products.
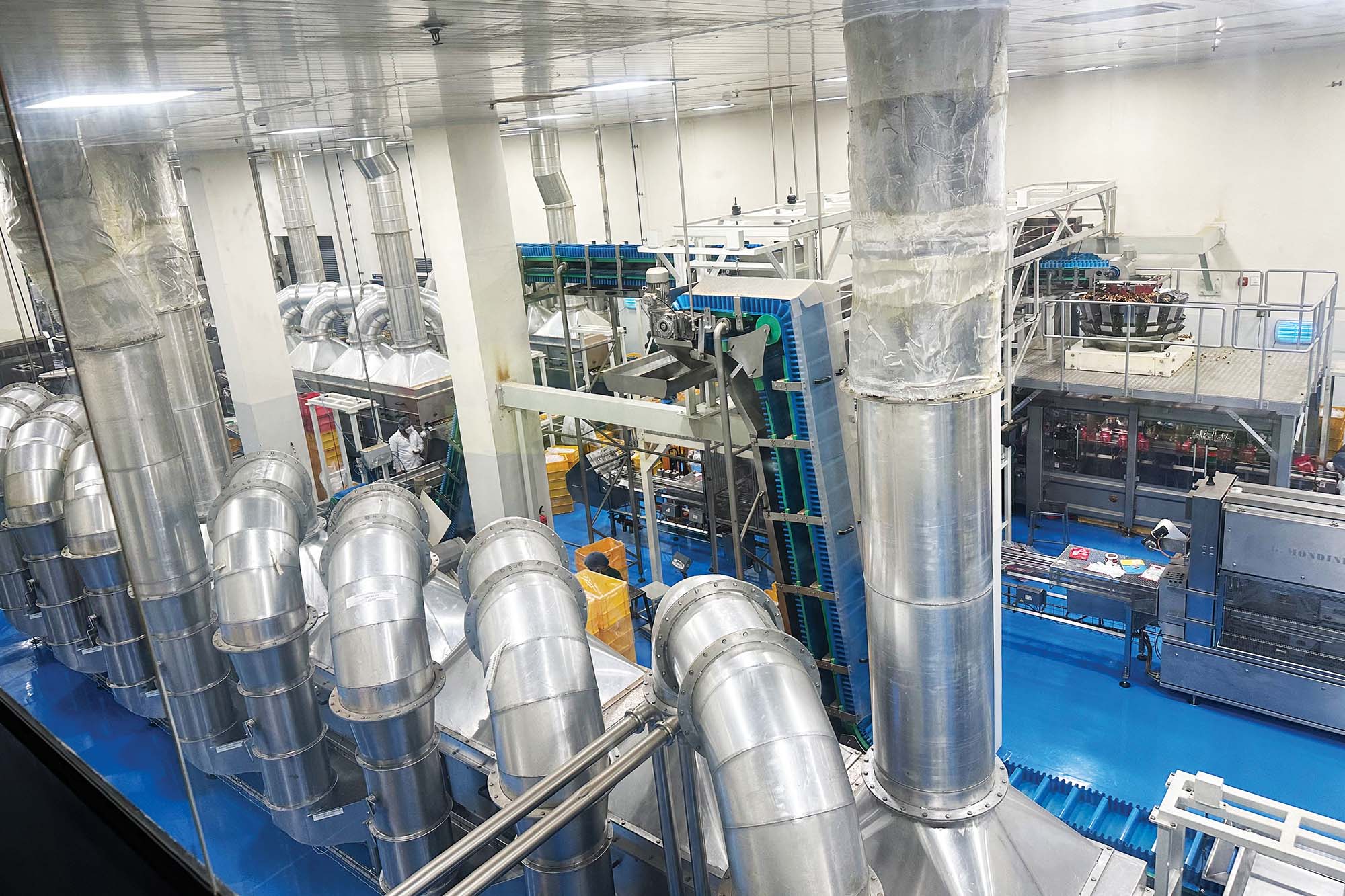
Their SAP-integrated quality control system tracks each batch from raw material procurement to post-sale analysis. Products undergo rigorous testing throughout their shelf life, with complete traceability—a feature essential in maintaining global standards.
Machine Maintenance & Performance Incentives
Machine uptime is closely linked to employee performance incentives. The maintenance team operates like a Formula One pit crew, ensuring minimum downtime and maximum efficiency. Preventive maintenance is prioritised over breakdown repairs, utilising IoT sensors to track wear and tear in real time.
He says, even during the off-season, machines operate 18–20 hours a day, with just four hours of downtime. During peak seasons, downtime is reduced to two hours daily, solely for deep cleaning and maintenance.
A Culture of Safety and Excellence
At the heart of Chitale Bandhu’s success is its deep respect for food—a philosophy rooted in Indian tradition. Every visitor and worker follows strict hygiene protocols, wearing PPE kits to prevent contamination. Their food manufacturing process reflects the ethos of purity and quality, ensuring that customers receive nothing short of the best.R&D and Future Vision
Chitale Bandhu’s in-house Research & Development (R&D) team focuses on three key areas: researching new technologies to improve production methods, developing new products to meet evolving consumer preferences, and innovating critical processes to enhance quality and efficiency. Over the past five years, the company has invested over ₹200 crores in expanding operations, upgrading technology, and generating employment. What began with just 20 employees has now grown to a workforce of 600, with a vision to reach 1,000 shortly.
Betting on Bars
Looking to the future, Chitale Bandhu is focusing on bars—a format expected to dominate the snacking industry in the coming decade. Their namkeen bars, health bars, protein bars, and fruit bars are already gaining traction.
“Our goal,” Indraneel shares, “is to make Chitale Bandhu a gateway brand—one that appeals to diverse nationalities while enhancing nutritional value.”
As we conclude our tour, we are left mesmerised by the seamless blend of tradition and modern innovation. The automation, IoT integration, precision tracking, and sustainability initiatives make Chitale Bandhu a benchmark in the global FMCG industry.
What once started as a small dairy business is now a pioneering food-tech enterprise—continuing to uphold its rich legacy while shaping the future of food manufacturing.
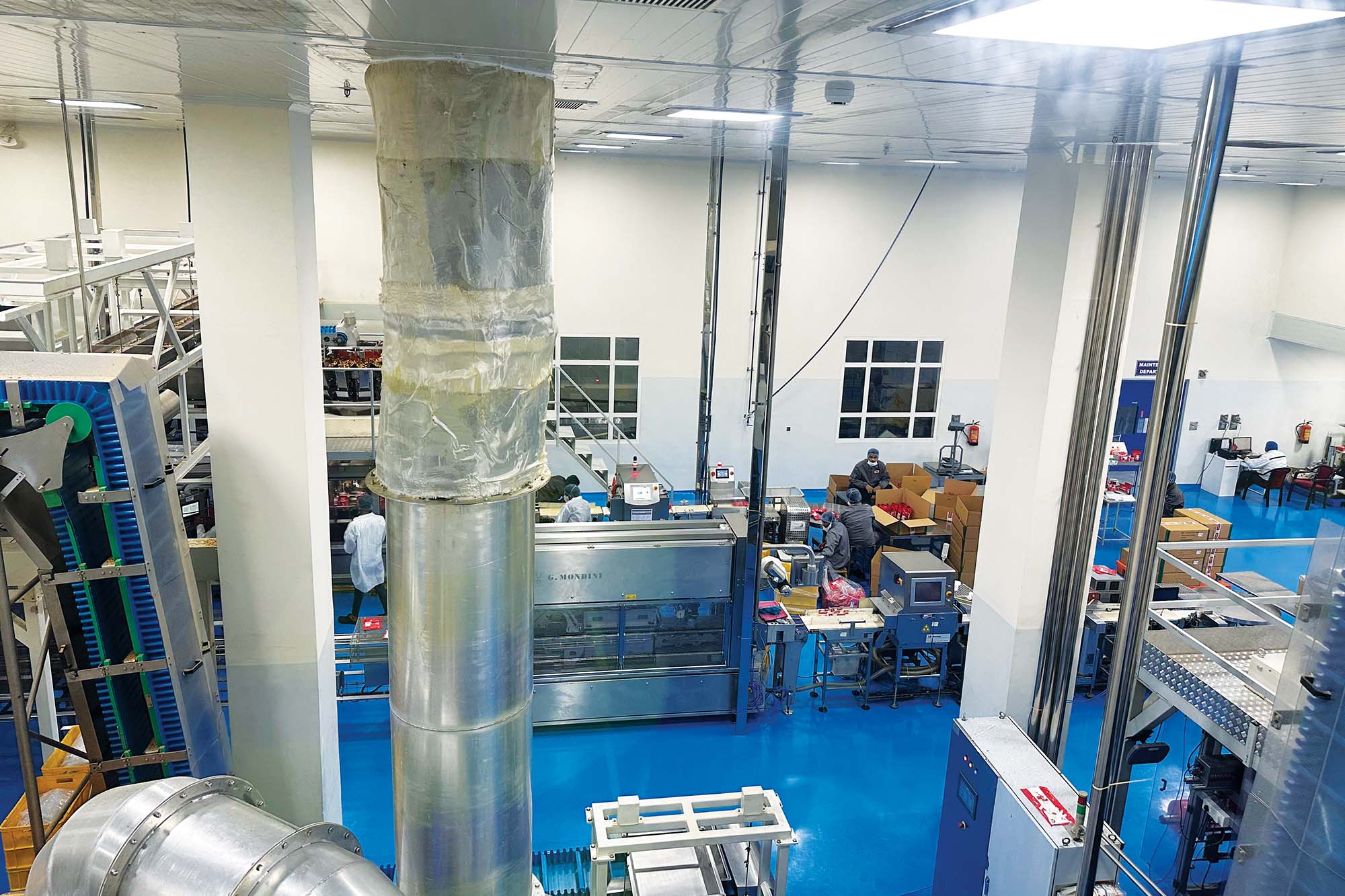
———-
Sustainability is a growing focus in the food industry. How does Chitale Bandhu incorporate circular economy principles to manage its production processes?
Wherever food is produced, there are likely to be many rejections after the completion of the product due to various issues that may arise. Some of these problems are unavoidable process errors, and they are addressed by the team. We at Chitale Bandhu follow the concept of the circular economy. The approach involves a mix of solutions to ensure that waste is not completely lost. Every process will generate a certain amount of waste, and one of our key performance indicators (KPIs) focuses on how we can keep that waste within manageable limits. Another KPI is how we can utilise this waste productively. Instead of throwing it away and rendering it unusable, we strive to find ways to give it a second life.
There are three key factors to consider. One is product wastage. Some items can be reused, while others cannot. It’s essential to manage product waste and keep things under control.
Another aspect is water treatment. A significant amount of water is used to clean food equipment. At Chitale Bandhu, this water is treated properly and released in a controlled manner.
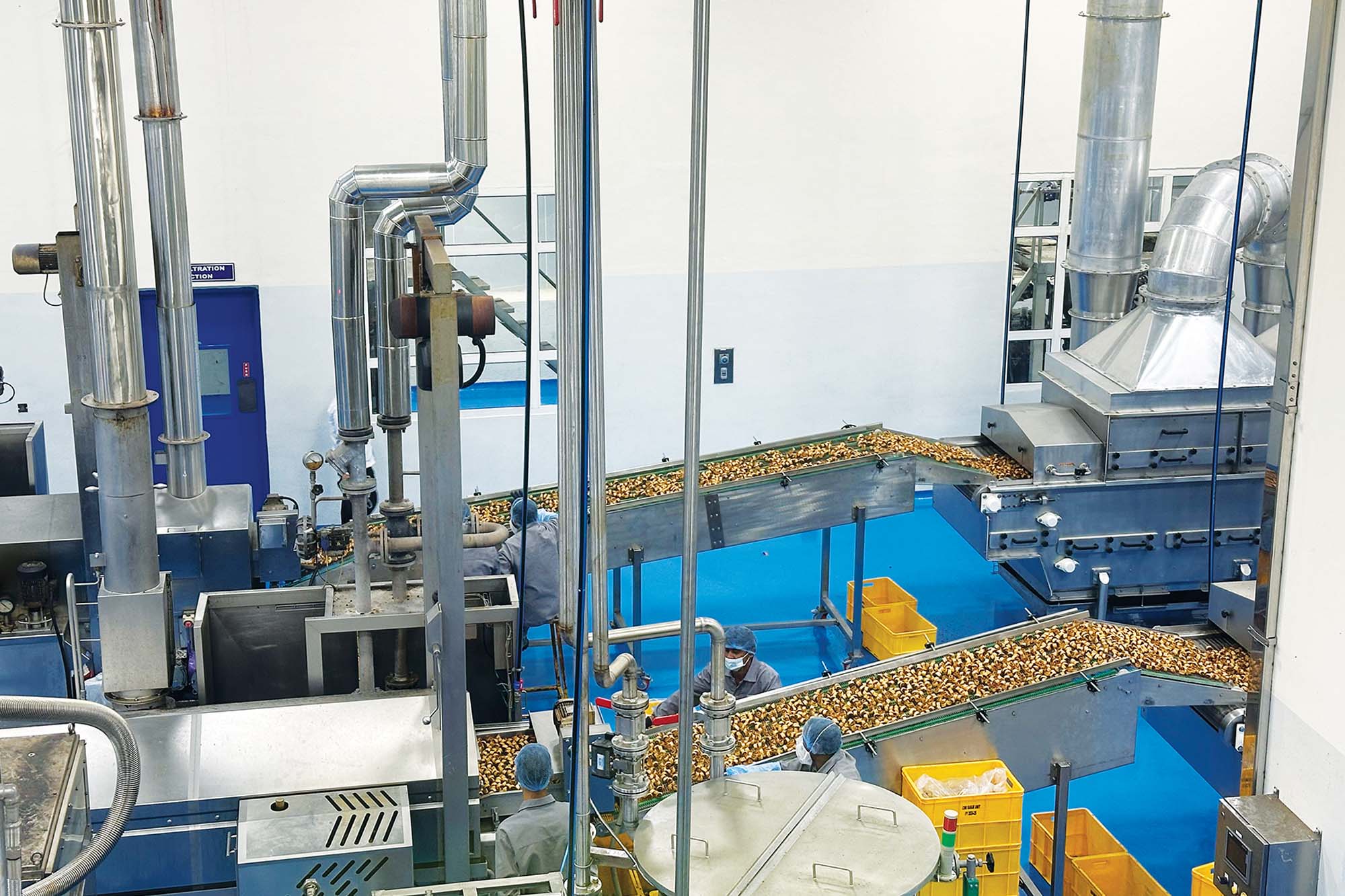
Packaging helps Chitale Bandhu reach its consumers, but materials designed to preserve products are often not biodegradable. More sustainable packaging that is reliable and possesses adequate rigidity is under consideration. This includes ensuring a reasonable thickness so that it can be handled by recycling equipment. Additionally, we are exploring options for co-extruding layers that will allow us to reuse plastic, thereby reducing waste.
Chitale Bandhu has made significant strides in energy efficiency and sustainability. Can you share how your Ranje unit is achieving an energy surplus?
From an energy perspective, our Ranje unit is operating at a surplus. In terms of water use and achieving zero discharge, we are nearly 90% of our targets. However, we are yet to work on effectively addressing plastic waste and zero-discharge state. Our goal is to improve efficiency and comply with the requirements of net-zero manufacturing over time.
The premise sources nearly 60% of its energy supply from solar power. We are also investing in wind farms and utilising open access to lower electricity costs, which is a significant expense for us as manufacturers, especially in Maharashtra.
By being efficient in our manufacturing processes, we can reduce our overall costs. Utilising renewable energy is the primary way we are managing these expenses. All entities within the Chitale Group are actively engaged in initiatives related to renewable energy.
Cookie Consent
We use cookies to personalize your experience. By continuing to visit this website you agree to our Terms & Conditions, Privacy Policy and Cookie Policy.