We prioritise lean practices as the cornerstone of our digital evolution
By OEM Update Editorial November 30, 2023 1:57 pm IST
Shailesh Sharma, Director of Operations at SKF India, offers insights into India’s manufacturing potential, innovative digital transformations, and pioneering solutions driving industry efficiency. He discusses SKF’s vision and strategies, propelling sustainable growth and technological advancements.
What is your perspective on India’s potential to become a manufacturing hub, and how is SKF aligned with this vision?
India is poised to emerge as a global manufacturing centre, supported by initiatives like ‘Aatmanirbhar Bharat’ and ‘Make in India’ and targeted efforts such as Production Linked Incentives. Advancements in infrastructure, including industrial corridors and better connectivity, are set to amplify the sector’s expansion.
SKF has actively contributed to this vision by establishing robust manufacturing operations in India. Our investment in local production facilities has enabled us to cater to the domestic market in both automotive and industrial domains. Looking ahead, we are committed to bolstering our manufacturing capacities, ensuring top-notch product quality and cost-effectiveness, and meeting timelines as expected.
What innovations are reshaping manufacturing to enhance productivity and efficiency?
Innovations like IoT for immediate monitoring and predictive maintenance, AI and machine learning for analysis and enhancement, and robotics for accuracy and speed are transforming manufacturing. Technologies such as 3D printing minimise waste and accelerate product development. Digital twins provide live simulations, while AR and VR assist in training and upkeep. Supply chain digitisation increases transparency, renewable energy sources reduce expenses, and blockchain enhances traceability. Edge computing allows real-time decision-making, collaborative platforms, predictive analytics, and efficient manufacturing. When strategically combined, these innovations empower manufacturers to boost efficiency, reduce expenses, elevate product quality, and swiftly adapt to market shifts, enhancing competitiveness.
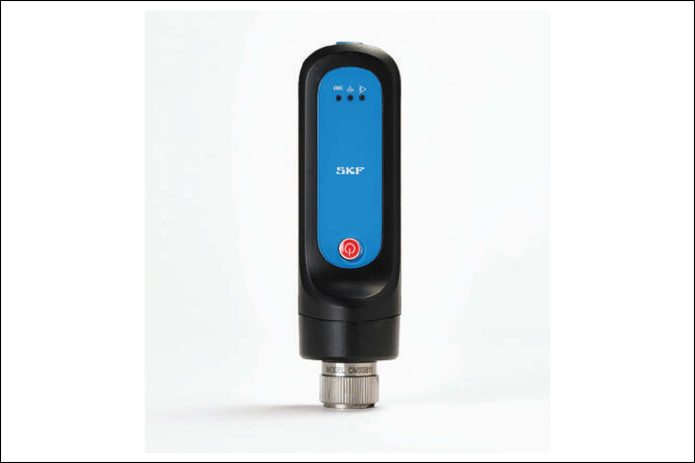
Please share insights into the company’s experience adopting digital technologies and how it transformed ball-bearing manufacturing operations.
Digitalisation is a key enabler on the journey to world-class manufacturing. Our emphasis on lean, green, digital (LGD) manufacturing in India underscores our commitment to intelligent, eco-friendly growth. We prioritise lean practices as the cornerstone of our digital evolution, implementing various strategies to streamline operations and ensure speed, reliability, quality, cost-efficiency, and competitiveness.
Our ongoing focus involves ramping up automation in our production centres to maintain a competitive edge and enhance our environmental footprint. Leveraging our talent pool, current engineering expertise, and dedication to digital adoption, we aim to consistently meet customer needs and establish new industry standards for future-ready factories.
What advantages does SKF India bring to smart manufacturing, and how does it impact overall operations and efficiency?
SKF India has leveraged strategic investments, process refinement, and workforce enhancement to embrace the potential of smart manufacturing. We aim to create an organisation centred around customer needs, achieved by continually enhancing technology to support our processes and the individuals driving them forward.
Empowering our employees with enhanced analytics tools and improved performance visibility facilitates quicker decision-making. Furthermore, we are actively implementing a vision aligning with a dependable, efficient, eco-friendly digital value chain to expedite top-tier manufacturing. Prioritising digitalisation has fostered innovation, enabling us to respond swiftly and insightfully to remain competitive and fulfil customer demands while emphasising speed, reliability, and cost-efficiency.
How do we address the challenges associated with integrating technologies such as IoT, robotics, and AI in manufacturing?
Manufacturers are facing substantial challenges stemming from the growing digitalisation of various aspects of the value chain, from design to maintenance. Adopting cutting-edge technologies like Industry 4.0 faces hurdles due to differing capabilities, limited understanding of practical applications, a need for more design thinking, and a shortage of skilled labour. These obstacles significantly impede the progress and modernisation efforts for bearing manufacturers. Having a well-defined strategy that aligns technological advancements with manufacturing processes is crucial. Additionally, manufacturers need to strategise on how to train their workforce to adapt to the evolving digital landscape. Beyond budgeting, change management, and meeting regulatory requirements, it is equally important to emphasise collaboration, communication, risk management, and selecting dependable vendors to integrate these technological changes effectively.
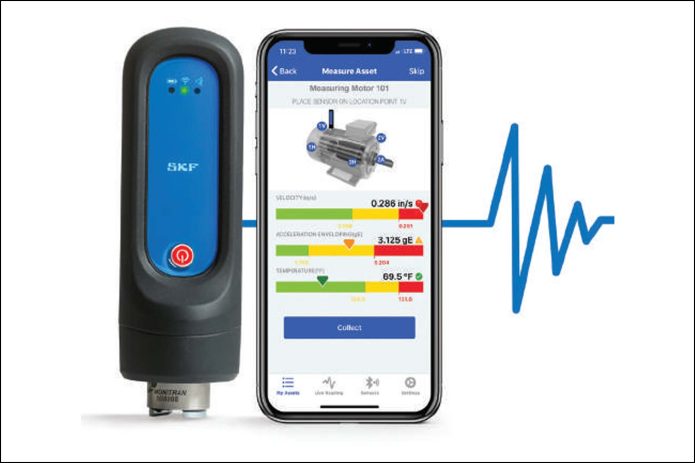
How does SKF India implement predictive maintenance concepts in its manufacturing processes, and what benefits do these practices offer?
We’ve invested in digital tools like IoT, Data Analytics, and Cloud computing to boost operational efficiency, product excellence, and customer contentment. These resources are pivotal in our digitalisation journey by enabling real-time monitoring of production processes and equipment. Our manufacturing setup incorporates sensors, robotics, SCADA systems, and upgraded machine control systems with advanced PLC features. Additionally, we conduct regular Kaizen sessions involving employees at every level to foster incremental improvements in manufacturing processes, resulting in heightened productivity, reduced downtime, and a smaller environmental footprint.
Please discuss innovative solutions that SKF India has introduced to enhance manufacturing processes in industrial sectors.
SKF India has introduced specialised solutions tailored to different sectors, including:
• CO2 Bearing-Select Tool: This freely available tool assists industries in comprehending and managing carbon emissions. It enables customers to explore CO2 emissions related to bearing production and usage across various sectors. Moreover, it provides access to SKF’s application engineers for detailed insights on emissions linked to specific bearings, along with optimisation suggestions to reduce energy consumption and emissions in the future.
• SKF Enlight AI is an industrial analytics solution that uses automated machine learning (AutoML) to enhance machine health by identifying anomalies and predicting asset failures. This improves overall equipment effectiveness (OEE), boosting yield rates and operational savings based on the generated insights.
• SKF Insight Rail: A wireless condition monitoring system designed for railway applications, enabling real-time detection of wheel damages and track conditions. This facilitates predictive maintenance for railway assets, ensuring enhanced operational efficiency.
Additionally, ABB and SKF Group have initiated discussions for a potential collaboration in automating manufacturing processes. This partnership aims to explore solutions that enhance manufacturing capabilities, supporting clients in achieving increased production efficiency.
What is SKF India’s vision for the future, and how do you plan to drive innovation and efficiency in manufacturing processes?
Our purpose is “Together, we re-imagine rotation for a better tomorrow by creating intelligent and clean solutions for the people and planet. Guided by our purpose, we are committed to accelerating the sustainable transformation within the industry. We are dedicated to collaborating with customers, partners, and society to transcend traditional industry boundaries. Our focus on future growth involves continuous investment in R&D, digitalisation, and sustainability. We aim to strengthen customer relationships, expand our market presence, and bolster our organisational capabilities.
Recently, we unveiled our Open Innovation initiative in partnership with IncubateHub, aiming to foster innovation, tackle complex challenges, and enhance competitiveness, adaptability, and growth. This initiative invites startups, scale-ups, academic institutions, and industry experts to join forces in creating practical solutions for real-world customer issues.
SKF seeks to co-create clean technologies and value-added solutions through this collaboration, offering customers a competitive advantage while significantly contributing to sustainability efforts.
Cookie Consent
We use cookies to personalize your experience. By continuing to visit this website you agree to our Terms & Conditions, Privacy Policy and Cookie Policy.