Schmersal emphasizes importance of IoT for predictive maintenance
By OEM Update Editorial July 31, 2023 12:55 pm IST
Marking a decade of presence in India, Schmersal Group embarks upon their successful journey with the dedicated R&D developments in ensuring safety and addressing customer demands.
How has Schmersal ensured the functionality of their devices and addressed customer demands?
Henning Carl: Ensuring the device’s functionality is a top priority for us. To achieve this, we have established our own injection molding area. This decision has allowed us to enhance our responsiveness to customer demands. As a result, our team and company have grown in expertise, specifically in the assembly and deeper processes.
Our next strategic move involved establishing partnerships with local suppliers who can provide technical support for crucial processes such as painting, die casting, and stamping, while we primarily focus on plastic parts manufacturing, injection machines, assembly, and the essential testing of the final product. Conducting 100% testing ourselves using our own equipment is vital, as it enables us to make necessary adjustments to meet customer requirements.
How does the company ensure compliance with different safety standards in various regions?
Henning Carl: Operating in various parts of the world poses a significant challenge for us, as each region has its own set of safety standards. Our R&D department plays a crucial role in ensuring that our products comply with these standards and obtain the necessary approvals from the respective notified bodies. When developing new products, R&D informs us about the specific requirements for each target market, such as UL certification. While this presents a challenge, the advantage of our global presence is that it allows us to gather valuable insights from different regions and offer our clients the opportunity to assemble machines tailored to their needs. Since our machines are not limited to a single location, but rather exported to various countries like Taiwan, Bangladesh, Europe, and the US, it is essential for us to be well-versed in the regulations. Our clients often seek our assistance in ensuring the safety of the machines they intend to export.
What challenges has Schmersal faced in managing their business in India?
Michael Ambros: India has witnessed significant progress in the field of production science. Despite facing internal challenges, such as the integration of various family members and managing a business that originated in Germany, the company has successfully brought together a talented team of professionals.
The company takes pride in its accomplishments over the past decade in India, particularly for being early adopters of initiatives like “Make in India.” Initially, there were difficulties pertaining to legal, tax, and governmental aspects, but these have now been resolved, and the company considers itself to be in a leading position in terms of safety in India. The main challenge ahead is to maintain a leading position in the market as new competitors emerge. It also gives us a push to establish local production facilities for both domestic and international markets.
How has Schmersal worked towards enhancing workplace safety?
Sagar Bhosale: Schmersal’s core mission is to enhance workplace safety. Over the past decade, the company has actively engaged in collaborations with industry partners, stakeholders, and government authorities to minimize accidents in the workplace.
Training plays a vital role in the overall safety process. It serves as the initial step where customers are educated about the potential hazards associated with their machines. Schmersal conducts comprehensive training sessions to create awareness about machine safety and the necessary measures to mitigate risks. This includes instructing on the appearance and operation of a safe machine, as well as providing guidance on maintenance and proper handling. Ongoing training remains essential even after safety measures have been implemented, particularly for advanced technical products that incorporate electronics and IoT capabilities. This ensures that customers can utilize them effectively and avoid future issues.
What are the unique demands of the safety market in India?
Sagar Bhosale: The safety market in India has unique demands, with customers seeking greater flexibility in their machines. Unlike standard products with stringent tolerances, Indian customers require more tolerance and flexibility, often requesting modifications to suit their specific needs. Schmersal meets these requirements by manufacturing products in Pune, where they have dedicated teams for research and development, vendor development, and supply chain management. This allows them to provide comprehensive solutions that directly fit the customers’ machines, meeting their individual specifications.
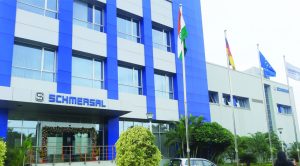
Schmersal
How does Schmersal contribute to the implementation of IoT for predictive maintenance?
Sagar Bhosale: Schmersal plays a significant role in the application of IoT for predictive maintenance, a widely adopted practice in various industries. The company collects machine data, transfers it to a gateway, and ultimately to the cloud. However, the value lies not only in obtaining data but also in analyzing it and taking actionable steps based on the insights gained. Schmersal’s IoT team in India has developed an ecosystem where they collaborate with analytics experts and other partners to offer comprehensive solutions to customers. This includes providing analytics dashboards and developing web and mobile applications for convenient access to the data. Schmersal’s IT professionals, through a global Competency Center, contribute to developing these user-friendly applications that enhance the customer experience.
How does Schmersal ensure consistency and quality across their manufacturing locations globally?
Sagar Bhosale: Schmersal maintains consistency in its solutions regardless of the manufacturing location, be it India, Germany, Brazil, or China. All products undergo the same international approvals to ensure uniformity. The company implements stringent production processes, including the use of identical machines for manufacturing switches, guaranteeing consistent quality. Due to the nature of safety products, thorough testing is conducted on each switch, evaluating it against a minimum of 10 to 15 parameters before it is deemed ready for delivery. Schmersal prioritizes strong consistency throughout the entire production and testing processes to ensure the reliability of their products.
An interesting fact, Schmersal’s testing machines for switches are interconnected globally, enabling quality personnel in Germany to monitor the quality control processes and progress in India. This interconnected system allows for real-time monitoring and ensures consistent quality standards are maintained across different locations.
How does Schmersal ensure consistent and standardized safety and automation solutions across different regions while accounting for unique regional requirements and regulations?
Sagar Bhosale: Schmersal ensures consistent and standardized safety solutions worldwide, including in India. Products manufactured in various countries meet the same international approvals, maintaining global uniformity. Production processes are also consistent, employing identical machines for switch manufacturing across regions, ensuring reliability.
Stringent testing is applied to all safety products. Each switch undergoes a comprehensive evaluation, meeting 10 to 15 parameters before delivery. This rigorous approach guarantees adherence to quality standards.
By emphasizing manufacturing consistency, thorough testing, and reliable delivery, Schmersal achieves consistency across regions. This enables us to meet diverse regional requirements and regulations while upholding the highest safety and quality standards.
Cookie Consent
We use cookies to personalize your experience. By continuing to visit this website you agree to our Terms & Conditions, Privacy Policy and Cookie Policy.