Die and mould is adopting sustainable materials and procedures
By OEM Update Editorial January 31, 2024 7:30 pm IST
Rajeev Tembe, Regional Manager – Sales at Jyoti CNC Automation discusses the trend of adopting sustainable practices, 3D printing, digital twins, and Industry 4.0 in India’s die and mould industry and how these practices enhance economic profitability while fostering environmental responsibility.
How do advancements in die and mould technologies impact manufacturing efficiency in industries?
The die and mould technology advancements play a crucial role in enhancing manufacturing efficiency by improving precision, reducing lead times, cutting costs, enhancing resource utilisation, and enabling customisation. This, in turn, benefits the customer in a big way, pushing for competitiveness in the global market. At Jyoti, we have an extensive range of products that we have specifically developed to cater for the needs of the die and mould sector.
How do die and mould manufacturers leverage digital design and simulation to overcome challenges in producing complex components for the automotive industry?
Meeting the demand for complex components in the automotive industry can be challenging for die and mould manufacturers. To address these challenges, manufacturers may explore investments in advanced technologies, digital design and simulation, collaboration with automotive OEMs, training and innovation, adoption of Industry 4.0, etc. By adopting these strategies, die and mould manufacturers can overcome challenges and efficiently meet the demand for the production of complex components in the automotive industry. Continuous innovation, collaboration, digitisation and a focus on quality are key elements in addressing these challenges.
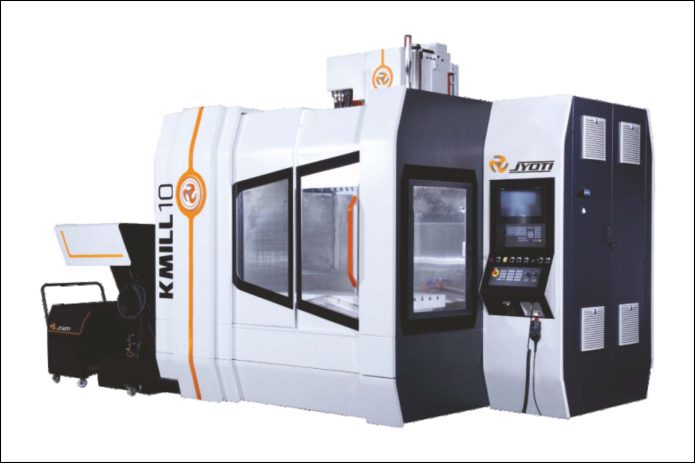
How does the applicability of 3D printing technology in industrial manufacturing benefit automakers?
The value of 3D printing technology expands beyond its usage as a tool for speedy prototyping as its applicability in the larger field of industrial manufacturing grows. When it comes to low-run moulding, 3D printing shows up as an affordable option with lots of benefits.
The fast prototyping and concept development facilitated by 3D printing help automakers create customised and on-demand car parts and expedite design revisions. There are still issues and restrictions with materials, such as limited material options and material strength and durability, even with the tremendous developments in 3D printing technology.
What challenges and benefits are associated with integrating sustainable practices in the injection moulding and die manufacturing industries?
A major trend in India’s die and mould manufacturing industry is the adoption of sustainable materials and procedures, which reflects a global shift toward socially and environmentally responsible production.
Climate change poses a significant challenge to global industrialisation and economic growth, with manufacturing playing a substantial role in environmental and economic issues. The injection moulding and die and mould manufacturing industries must embrace sustainable practices. It is no longer an option. Adopting sustainable practices enhances long-term economic profitability while simultaneously helping the environment. These sustainable initiatives include material selection, increased energy efficiency, trash reduction, and recycling. By adopting sustainable practices into these production methods, the industries prepare themselves for a more environmentally aware and responsible future.
How does the quality of digital twin models influence the effectiveness of intelligent upgrading and the digital evolution in die and mould manufacturing?A crucial advancement for intelligent upgrading and the digital revolution is the utilisation of digital twins. The effectiveness of digital twin applications is contingent upon the quality of the associated digital twin models. These models directly impact the calibre of services provided in various domains like prediction, optimisation, monitoring, and simulation.
Digital Twin models offer a means of analysing, predicting, and simulating various facets of die and mould manufacturing efficiency. They play a significant role in the design and construction of moulds by collecting diverse data throughout the entire process, from planning to delivery.
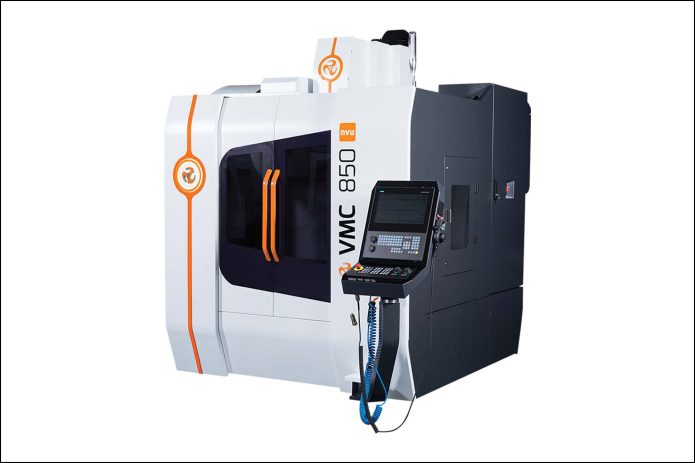
How have manufacturers integrated Industry 4.0 technologies like AI, ML, and data analytics in their networks for advancements?
Giant manufacturers have accelerated their efforts to integrate Industry 4.0 throughout their networks of manufacturing facilities during the last five years. Prominent manufacturers are currently appreciating the substantial benefits of AI, ML, and data and analytics. Moreover, many are still in the pilot phase, finding it difficult to get a satisfying return on investment or fully realise the promise of their transformation initiatives.
Manufacturers are investing much time and resources in their digital transformations. While a few are reaping the rewards of these expenditures, the majority need help scaling successful pilot projects or fully leveraging new tools and technologies to achieve significant returns.
How does injection moulding serve as a solution for the mass production of high-quality vehicle parts in the automotive sector?
One of the most popular plastics production techniques is injection moulding. This is justifiably so as it offers a realistic solution for mass manufacturing high-quality injection vehicle parts from a broad range of polymers. Automotive plastic injection moulding is a crucial production technique in the automotive sector, where quality, safety, and consistency are primary concerns.
Injection moulding provides a low-cost and scalable supply chain mechanism for various components in the automotive sector, including those found under the hoods and exterior and interior components. Die mould is compulsorily required for all plastic injection moulds and, thus, the machinery involved.
Cookie Consent
We use cookies to personalize your experience. By continuing to visit this website you agree to our Terms & Conditions, Privacy Policy and Cookie Policy.