Precision tooling solutions to improve performance and machining efficiency
By Staff Report August 31, 2024 11:37 am IST
Innovative tooling solutions, including digital modules, optimised geometries, and specialised coatings, are pushing the boundaries of precision and performance in drilling, boring, and reaming operations. They are driving improved chip control and overall machining efficiency for industries requiring high precision, such as aerospace and heavy equipment manufacturing.
How can the choice of cutting tool geometry impact the surface finish and tool life in drilling & boring operations?
The cutting geometry can impact the surface finish, but it is usually a minor change; geometry impacts the quality of chip formation more than the surface finish. If there is a challenge with the chips being too long and wrapping the tool, the finish can be degraded, but the problem is because of the long chip, not the geometry itself.
However, tool life can be affected by the geometry used. The geometry determines the chip flow through the cutting surface, so if the geometry is too confining, the forces exerted on the tool increase. These increased forces would cause the tool to break down faster than a geometry where the chip flows with less resistance. The geometry shape can impact tool life by being either a weaker or stronger cutting edge. It is well known that the sharper the cutting edge, the better the chip form, yet the sharper the edge is, the weaker the edge is – as well. This would mean that the weakened cutting edge would produce better chips but would likely break down quicker due to the smaller cross-section.
What innovations have you introduced in drilling, boring, and reaming tools to improve precision and efficiency?
We have introduced various innovations to improve precision and efficiency, including the Wohlhaupter 3ETECH+ digital readout module, ES-Bore fine-boring lay-down cartridges, and our newest products, the T-A Pro Y series and GEN3SYS XT Pro M geometry.
The 3ETECH+ digital is ideal for machinists looking to make diameter adjustments at the machine. With premium visibility of one-micron diameter adjustments, precision boring is easier. The enhanced digital readout module benefits aerospace, heavy equipment, and automotive. Advanced precision technology by Wohlhaupter has improved boring operations, and the new features of the 3ETECH+ take it even further. The tool now offers a backlit OLED display with a larger screen for better visibility alongside a rechargeable battery that can be powered via USB-C.
ES-Bore is a fine-bore lay-down cartridge that can easily be mounted onto the body of a custom tool. Its dimensions allow the cartridge to fit on existing bodies and replace current lay-down cartridges, providing 3ETECH+ functionality.
The new T-A Pro Y series upgrades the manufacturing process. It allows machinists to increase throughput in their cutting tool applications. Ultimately, users experience the benefits of the T-A Pro line at smaller diameters. The T-A Pro Y series upgrades machine shops to a superior system.
GEN3SYS XT Pro’s new M geometry is designed for improved chip formation while drilling high penetration rates within industries such as oil and gas, HVAC, automotive, construction, medical and pharmaceutical, and food and kitchenware. Adding the M geometry insert with Allied’s AM460 coating to the GEN3SYS XT Pro high penetration drilling system gives machinists access to an insert with industry-leading tool life in stainless steel applications.
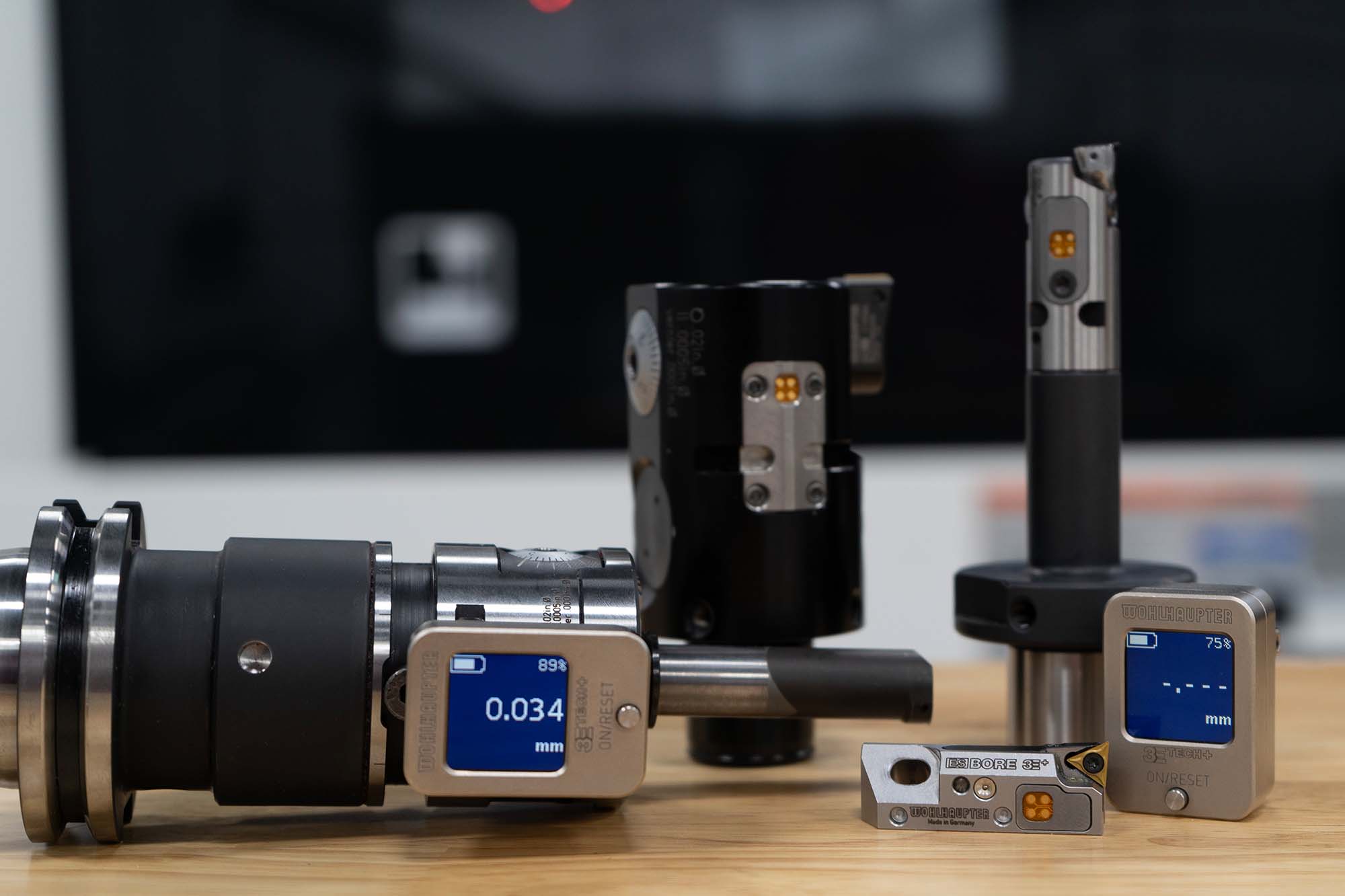
How do your cutting tools address the challenges of machining aerospace-grade alloys such as titanium and Inconel?
As a manufacturer of a wide range of homemaking and hole-finishing cutting tools, Allied devotes its advanced engineering and manufacturing capabilities to creating the widest selection of value-added tooling available to different metal-cutting industries globally.
With the aerospace industry specifically, Allied Machine has a variety of drills, boring tools, thread mills, port contour cutters, and reamers that excel in applications related to the industry. One of those cutting tool solutions is the T-A PCD insert. The sharp cutting edge that provides clearance cutting and reduces delamination is what allows the polycrystalline diamond (PCD) inserts to generate such high success in aerospace applications dealing with carbon fibre. While other tools encounter massive tearing when exiting the hole in carbon fibre, the PCD insert geometry, precise OD corner prep and Notch Point technology encounter minimal delamination. It produces a near-perfect tight tolerance and smooth hole elements critical in the aerospace industry.
How do advanced materials and coatings in your tools enhance performance and reduce costs?
Over the last 50 years, coatings have revolutionised cutting tools. Without them, there is much less wear or heat resistance during a machining application, but the benefits of running tools coated instead of uncoated are numerous. Not only do you have better tool life with coated tools, but coatings also provide thermal barriers, which allow you to run faster. Coatings take the surface hardness of your tool and increase it while adding a level of lubricity to the tools. Ultimately, you have much less friction in the cut, and the lubricity gained from the coating also helps to eliminate the built-up edge, among other issues that you could face with uncoated tools.
Different coatings have different properties in wear resistance and hardness. The benefits depend highly on the application. There are coatings with higher lubricity. Exemplifying this is P, K and N grade inserts with different material grades with coatings to excel within their materials groups. The benefits you get from coated tools depend on what you are trying to machine and the material you are cutting because certain coatings work better in certain materials.
TiN, TiCN, or TiAlN coatings are universal. You can use them in every type of application; however, coatings have become more material-specific. These material-specific coatings focus on achieving the next level of heat resistance, hardness, and wearability through different combinations and configurations of chemical elements, causing innovators to continue pushing the envelope with coatings.
Coatings are beneficial for cutting tools for heat and wear resistance alone. Combining different elements like aluminium, titanium, chromium or silica nitride in a coating system with different layering techniques created the coatings that exist today, which is the same concept used and created new coating innovations. Nevertheless, while choosing the coating involves a complex chemical understanding, having ISO-specific geometries within the industry has removed most of the guesswork and begun the transition of not needing to analyse the best coating to cut with.
What measures are you taking to improve the sustainability and energy efficiency of your machining tools?
Most recently, Allied Machine & Engineering has installed solar panels at one of its locations in the United States. This solar panel project will impact numerous areas of the environment. Not only will the solar panels offset 1,112 tons of CO2 per year, the estimated amount of carbon dioxide that will not be released into the air, but installing solar panels is also equivalent to planting 25,878 trees. Trees consume CO2, so the project is reducing the CO2 emitted into the air, equivalent to the CO2 consumption of 25,878 trees. Lastly, to diversify our energy sources, this project will prevent the consumption of 2,345 barrels of oil due to solar energy sources instead of conventional electric generation sources such as coal or natural gas. Installing these solar panels aligns with Allied environmental stewardship, and we plan to continue to reduce our carbon footprint with future projects.
Cookie Consent
We use cookies to personalize your experience. By continuing to visit this website you agree to our Terms & Conditions, Privacy Policy and Cookie Policy.