Different geometries enable varied cutting capabilities
By Staff Report January 2, 2025 11:29 am IST
Dormer Pramet has developed applications that deliver exceptional toughness and edge strength, enabling high cutting speeds without compromising flexibility. Amit Raina, Dormer Pramet’s Country Manager for India, shares insights on designing various products, focusing on various geometries.
What new materials have Dormer Pramet introduced to improve the performance and lifespan of cutting tools?
Early this year, we introduced a range of products designed to enhance operational versatility and ensure certainty in application processes.
Among these are the highly productive multi-application E397 and E398 taps. These taps are crafted from a unique Powder Metallurgy High-Speed Steel substrate (HSS-E-PM), which provides exceptional toughness and edge strength, enabling high cutting speeds without compromising flexibility. Additionally, these taps feature a TiCN (Titanium Carbonitride) coating, which offers several benefits, including a low coefficient of friction to protect against adhesion and cold welding and the ability to maintain high cutting speeds, ultimately reducing cycle times.
The focus on advanced materials and coatings is part of our ongoing effort to deliver tools that perform reliably in diverse and demanding applications.
What are the latest innovations by Dormer Pramet in cutting tool technology to support modern manufacturing processes?
As a part of our 2024 range of solutions, one of the latest advancements we’ve made is the development of high-performance drills, particularly engineered to excel in a wide range of materials, including carbon steels. These drills feature a specifically designed split point for self-centring along with a Titanium Nitride (TiN) tip coating, applied exclusively to the cutting zone that ensures extended tool life while enhancing cost efficiency by offering longer-lasting performance without compromising productivity.
A key technological breakthrough in these drills is the integration of CTW grinding technology, which enables multiple regrinds without loss of chip evacuation performance owing to a continuously thinned web along the entire flute length. The combination of advanced flute geometry and a 120° point angle makes these drills highly versatile and suitable for CNC and conventional machines. Moreover, these drills are adaptable to a broad spectrum of applications, providing significant efficiency, precision, and tool longevity benefits.
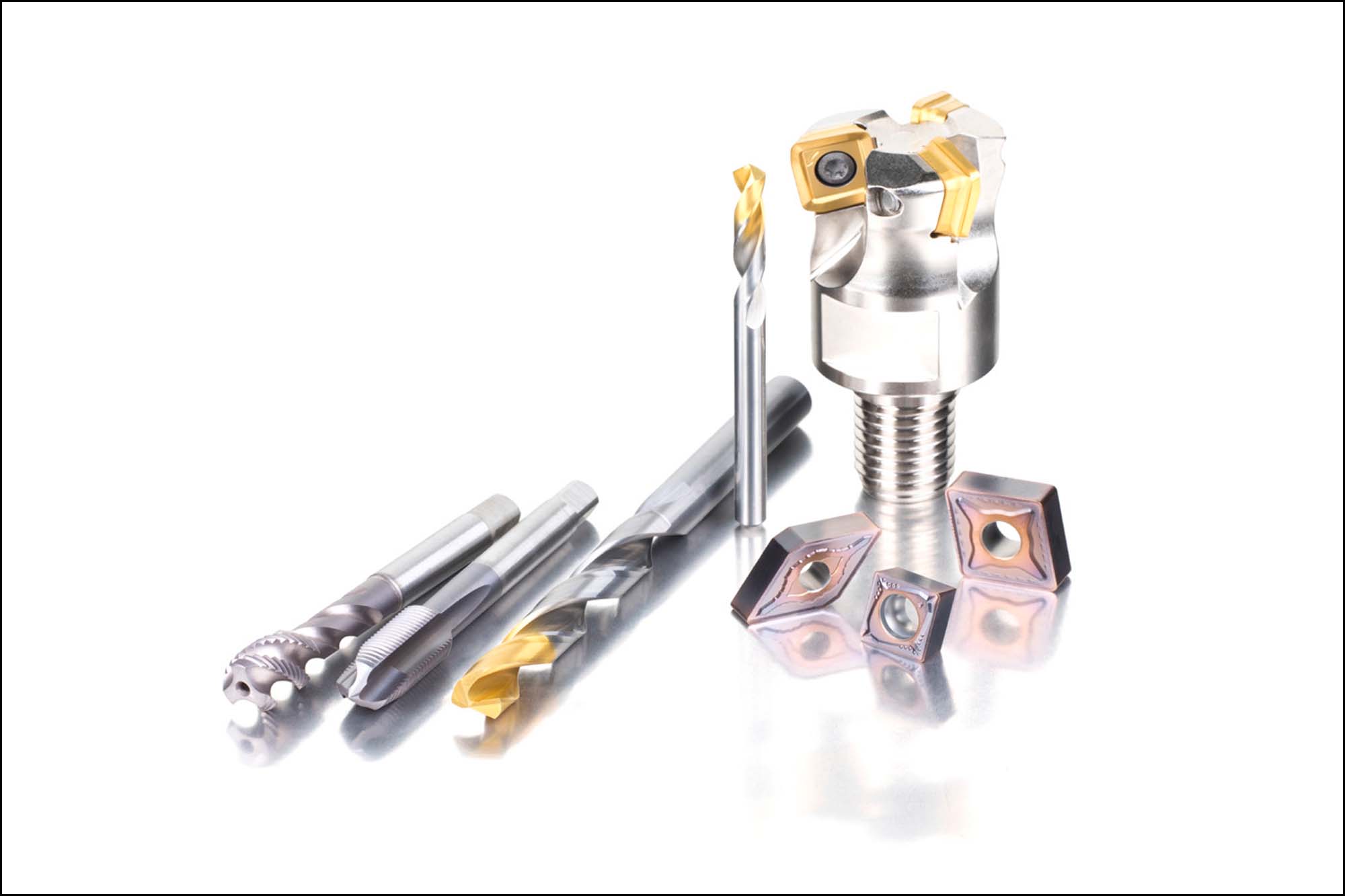
As a part of our commitment to addressing modern manufacturing trends, we are expanding our portfolio to include tools designed for additive manufacturing processes to support the growing demand for lightweight in industries.
How do advanced tool geometries contribute to Dormer’s machining time reduction?
Based on the tool geometries, we determine the optimal feed rate and how to manage chip removal effectively. Different geometries offer varying capabilities in terms of cutting parameters.
In roughing operations, where a significant amount of material needs to be removed, most of the machining time is consumed due to the more significant number of cuts required. To optimise the process, Dormer Pramet’s advanced and robust geometries play a crucial role in increasing feed and depth of cut, significantly reducing cutting time. These 3D geometries effectively distribute the cutting forces, producing an optimum wear pattern with higher tool life.What cooling techniques do you use to improve tool life and reduce wear?
Coolant depends on the material we are machining, but when it is important to use coolant, we recommend at least 8 to 10 % concentration of coolant oil, which reduces the temperature at the cutting zone and ensures a smooth flow of chips.
Dormer Pramet has a different combination of grades and geometries, which perform even better without coolant than tools that require coolant.
How is Dormer using AI, ML, IoT and other advanced technology in cutting tool management and monitoring systems?
The integration of digitalisation and AI is shaping the future of cutting tool management, and we use these opportunities to enhance operational efficiency and precision. For instance, a recent innovation introduced is an autonomous inspection station that leverages AI to optimise quality control. This station uses cameras, lights, and a unique AI-based algorithm to detect and address defects in real time, preventing non-conforming pieces and ensuring consistent quality standards.
At our Ankleshwar plant, we have invested in robotic machinery to enhance production efficiency and maintain high-quality standards.
As these digitalisation trends continue to advance, our efforts are also focused on introducing innovative technologies.
What role does IMTEX 2025 play in driving global collaborations and market expansion for cutting tool builders?
Based on our insights and having observed the participation in previous editions, we believe that IMTEX 2025 is one of the most significant events in the manufacturing and machining industry. It’s one of the most sought-after exhibitions and an ideal platform for businesses like ours to showcase the latest innovations, network with industry leaders, and engage with key stakeholders. In fact, in the upcoming edition of this exhibition, we are thrilled to announce that we will be the gold sponsor at the event.
We look forward to interacting with our existing and prospective partners and customers, fostering meaningful collaborations and strengthening relationships at this prestigious event.
Cookie Consent
We use cookies to personalize your experience. By continuing to visit this website you agree to our Terms & Conditions, Privacy Policy and Cookie Policy.