Redefining efficiency and sustainability
By OEM Update Editorial April 30, 2024 7:01 pm IST
According to Prashant Shetty, Director Commercial, Metal Cutting – India, Kennametal India Limited, the advancements in metal cutting techniques propel productivity in manufacturing across sectors. From high-speed machining solutions to innovative tooling for new materials, the industry is meeting challenges head-on for improved efficiency and sustainability
Precision and durability are paramount in the aerospace and defence sectors. Innovations in metal-cutting technology are meeting stringent demands for complex geometries and high-performance materials, ensuring optimal productivity and reliability in critical applications.
What are the latest advancements in metal cutting technology, and how do they enhance precision and efficiency in various industries?
Metal cutting technology is constantly evolving. The development of new processes to machine exotic materials has led to an increased demand for solutions that achieve higher performance parameters in terms of cycle time, speed of metal removal, accuracy, and precision, thus improving productivity in factories while optimizing cost per component. We are also witnessing new technologies evolving in the sectors where we operate, specifically in automotive. E-mobility has prompted the adoption of sustainable solutions and increased focus on and the use of alternative materials to improve performance and productivity. One of the newest innovations from Kennametal is the KENGold™ CVD coating technology, which provides a strong thermal barrier, improves edge toughness and allows for easy detection of wear due to its gold flank. Combined with the new KCP25C turning grade, KENGold provides increased versatility across a wide range of applications when machining steel. Our customers are experiencing consistently increased and reliable tool life.
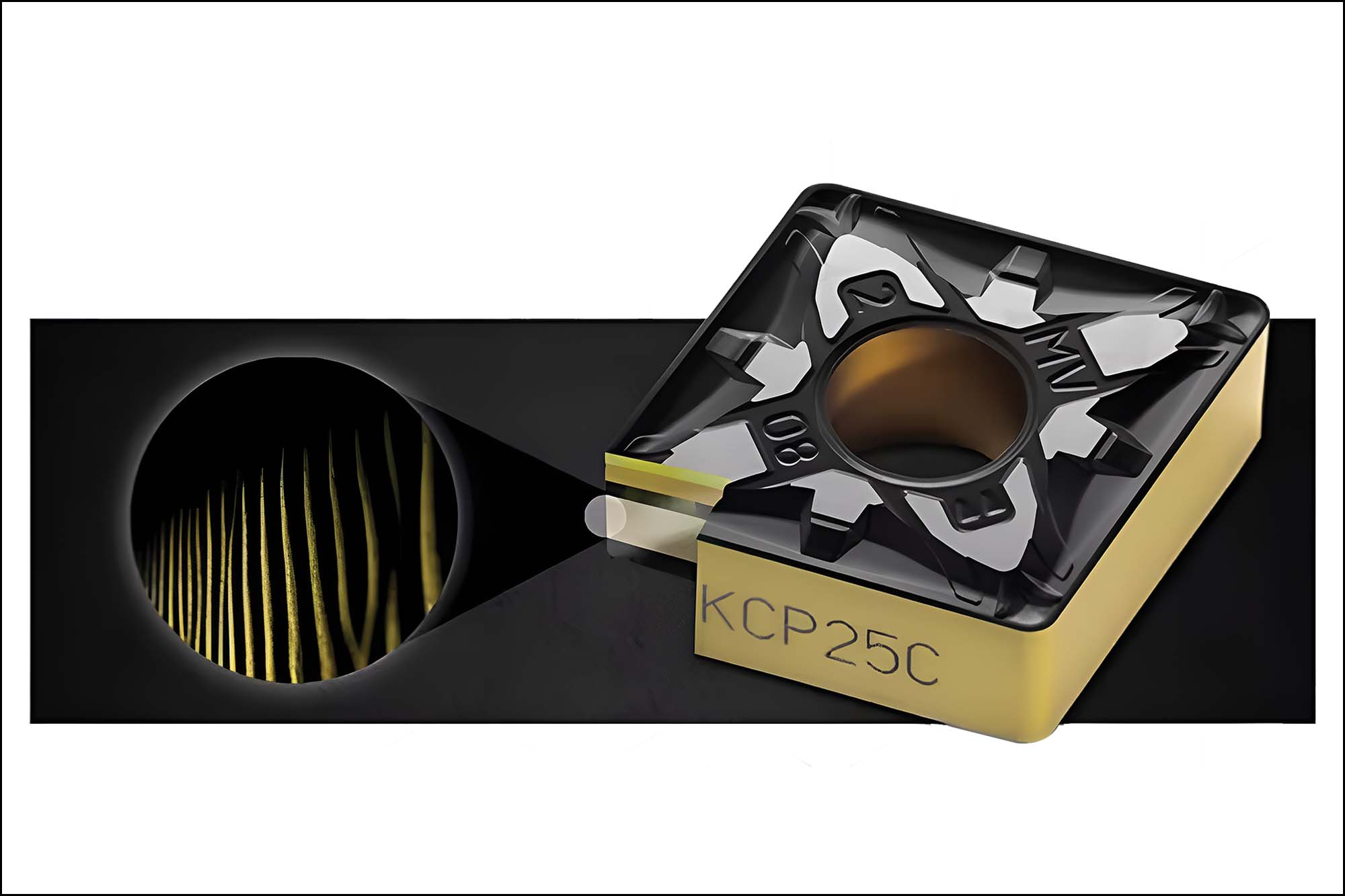
Could you share some insights into the challenges commonly faced during metal cutting processes, and how innovative solutions are overcoming these obstacles?
The increasing adoption of high-speed machining solutions requires cutting tools that deliver higher feed rates, depth of cut and faster metal removal. Multiple operations are combined into one, resulting in near-netshape components and enabling customers to optimise productivity. In response to these challenges, cutting tools must be robust, but also versatile with material-specific grades. Drill Fix PRO™ is a great example—a newly designed indexable drill by Kennametal that overdelivers when it comes to productivity. The platform’s versatility is also elevated with four cutting edges on its inboard and outboard inserts, resulting in an extended application range that also makes this tool incredibly cost-effective for our customers.
Another challenge is developing the right cutting tools for new materials—take the EV space which involves machining lightweight aluminum alloys. Kennametal is leveraging additive manufacturing to design for the EV market. Our innovative 3D-printed electric vehicle stator bore tool, RIQ™ Reamer, weighs half that of its conventionally-manufactured counterpart, while still meeting the accuracy, roundness and surface finish requirements for an aluminium motor body boring. This technology combined with a carbon-fiber body enables high productivity and reliability in the production of large-diameter, deep-bore electric motor housings. Additionally, this tool is capable of machining three diameters in one operation, ensuring the alignment and concentricity of the machined surfaces while reducing the cycle time significantly.
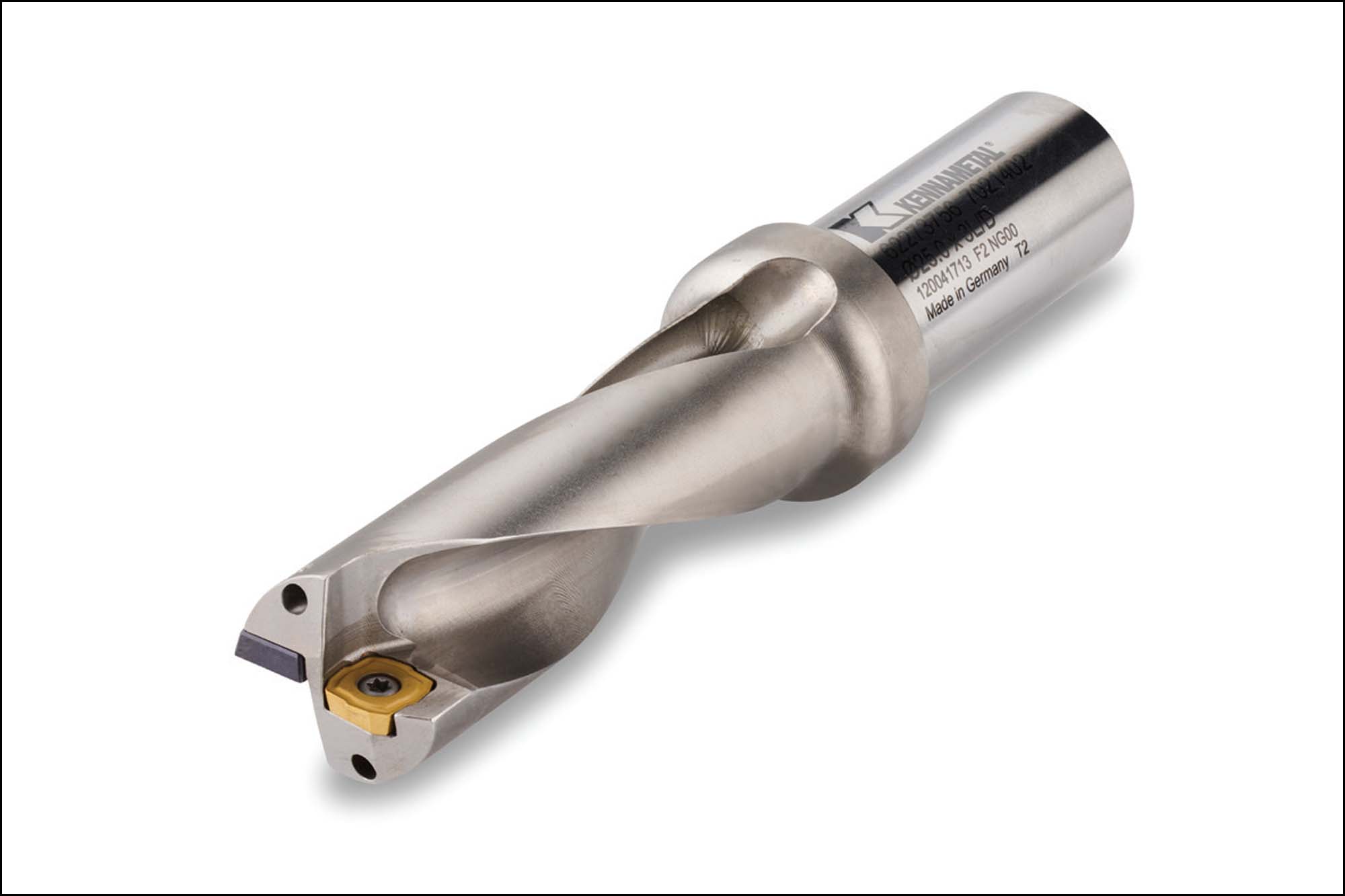
In what ways does the choice of cutting tools and techniques impact the quality and durability of metal components, particularly in demanding applications such as aerospace or automotive manufacturing?
Today, be it aerospace or automotive, we are increasingly seeing the utilisation of exotic new materials including titanium, inconel, monel and CFRP, among others. This has led to customers demanding advanced tooling solutions that deliver maximum metal removal rates and cutting speeds, as well as improved tool life and performance, while also ensuring that the metal process does not affect the material application. For example, materials like titanium or inconel can get work-hardened due to machining with incorrect cutting tools or cutting parameters. The ideal scenario is to be ‘right the first time’ with minimum cost and lead time. Complex automotive parts or aerospace cutting applications require a deep understanding of the material, machines, fixtures, processes, cutting tools and programming techniques, among other factors. Kennametal offers end-to-end machining solutions. With our team of technical experts, we work with customers through the complete machining operation, including fixtures and 3D simulations.
With sustainability becoming a key focus across industries, how are metal-cutting methods evolving to reduce waste, energy consumption, and environmental impact?
The cutting tool industry as a whole is looking at tungsten carbide and exploring ways to establish a reverse supply chain to buy back material and reuse it. This would significantly bring down tungsten carbide mining costs and contribute to a circular economy. Recycling is an area where Kennametal has made significant advances. Globally last year, Kennametal’s end-of-life sintered carbide products and hard scrap carbide, on average, consisted of 90 per cent tungsten carbide, which is recyclable.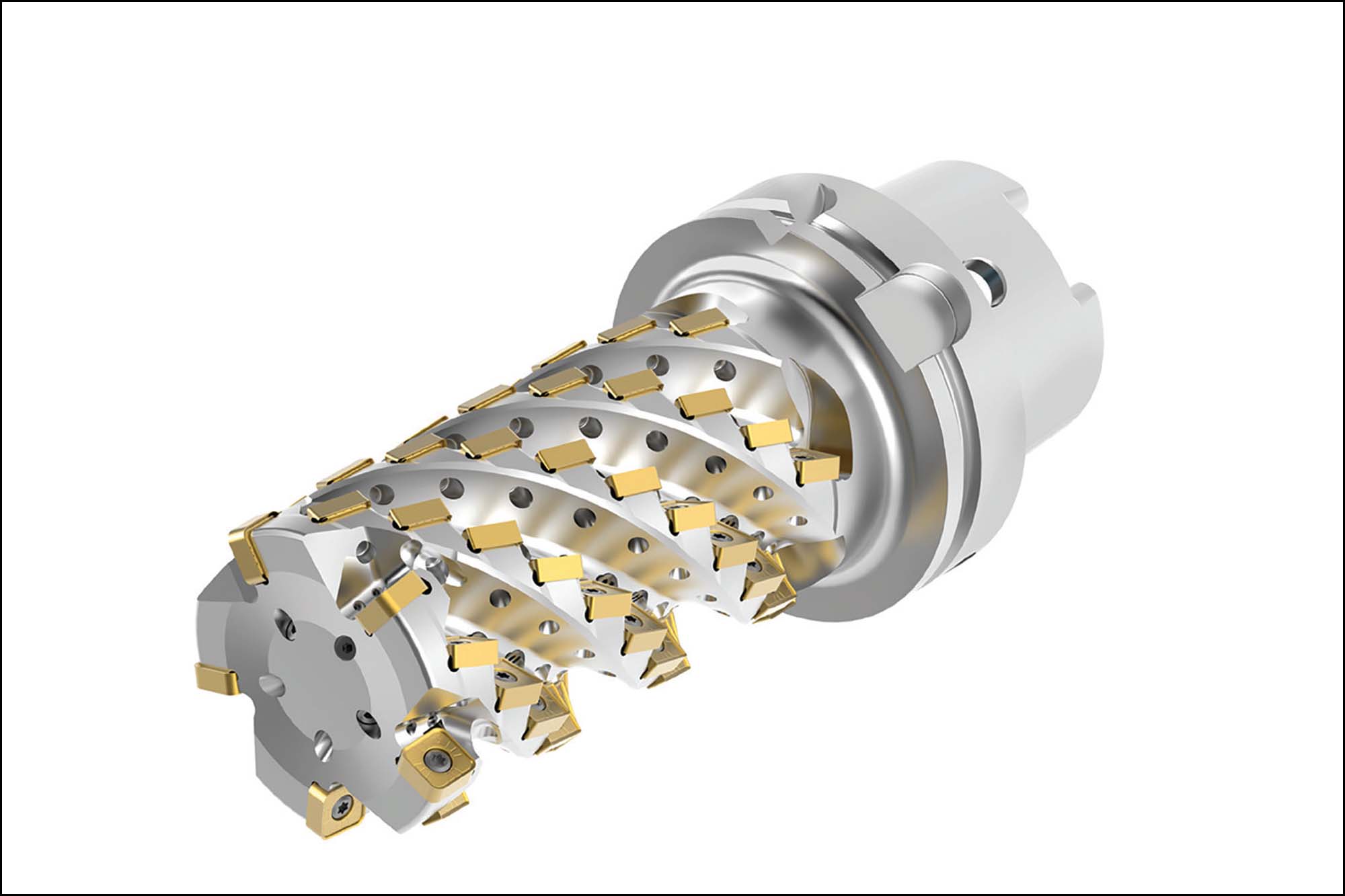
How is the automation and digitalization in modern metal-cutting processes shaping the future of manufacturing?
There is a growing interest in fast and accurate IoT-enabled machines capable of multi-tasking, which is essential for the growth of OEMs. Automation is also being used to drive productivity, efficiencies and quality; plus, manufacturers are using augmented and virtual reality technologies to run their production lines.
Kennametal is leveraging digitalization in its cutting tools technology through the concept of “digital twin” – a virtual model designed to represent a physical object or product accurately and precisely. A digital twin can be tested and validated before it is put into production, allowing engineers and process planners to identify failures. This “simulation” approach optimizes machining strategies and allows customers to streamline processes, drive productivity, control costs and reduce waste.
How does metal cutting technology contribute to the development of lightweight yet robust components for aerospace and defense applications, particularly in terms of materials like titanium and composites?
Some challenges associated with machining aerospace components include the high-chemical reactivity of Heat Resistant Alloys (HRAs) that can cause the chip to weld to the tool leading to cratering and premature tool failure. In addition, the chip tool contact area is relatively small, resulting in large stress concentration due to these higher cutting forces and temperatures contributing to premature failure of the cutting tool.
Even carbon fiber-reinforced plastics (CFRPs) that are extensively used in aircraft structures are extremely abrasive causing cutting tools to wear quickly and distort the surface quality in these materials. Thus, the machining of critical components for aeroengines and structures at optimal production rates requires reliable, high precision tooling for roughing and finishing operations. The entire process needs to be secured to avoid any damage to the part – this requires a) thermal and mechanical stress management in the machining zone and b) tooling designed with heat resistance substrate and coating, along with high pressure coolant delivery.
What specific advancements in metal cutting techniques have emerged to meet the stringent requirements of complex geometries and high-performance materials in aero and defense sector?
Aerospace customers today demand advanced tooling solutions that ensure precision, maximum metal removal rates, higher cutting speeds and maximum flexibility while delivering excellent tool life. At Kennametal, we work closely with customers to understand their machining challenges and propose the best solution. Our HARVI™ Ultra 8X helical milling cutter is designed to deliver the highest productivity at the lowest possible cost per edge. It can consistently remove up to 20 cubic inches of titanium per minute with a tool life of one hour or more. The flutes and the coolant nozzles assure maximum chip flow, removing a high quantity of material without chips getting jammed. And double-sided inserts reduce cost per edge while increasing speeds and feeds beyond what was previously possible.
Cookie Consent
We use cookies to personalize your experience. By continuing to visit this website you agree to our Terms & Conditions, Privacy Policy and Cookie Policy.