Compressors in aerospace manufacturing
By Staff Report September 17, 2024 11:47 am IST
Precision is the key in the aerospace industry. Screw air compressors are essential in supporting production processes in aerospace manufacturing facilities providing reliable compressed air for processes and improving efficiency
Screw air compressors provide a reliable source of compressed air, which is essential for a wide range of applications within the factory.
Roles of screw air compressors in aerospace production
Screw air compressors play a crucial role in aerospace production by providing the compressed air required for various applications. They power pneumatic tools like drills, grinders, rivets, and spray guns, which are widely used in aerospace manufacturing. Pneumatic tools are favoured because they are lighter, more durable, and offer better precision and control than electric tools.
In addition, Computer Numerical Control (CNC) machines, which are essential for the precision machining aerospace components, often require compressed air for various functions such as tool changes, cooling, and removing chips from the work area. Compressors ensure a continuous air supply to these machines, enabling uninterrupted production and high quality machining operations.
Compressed air is also used to power material handling and automation systems in aerospace manufacturing. It operates actuators, pneumatic cylinders, and other components that enhance the efficiency of automated systems, reducing the need for manual intervention and improving productivity.
Compressed air is indispensable in painting and surface treatment processes, such as sandblasting and powder coating. Screw air compressors provide clean, dry, and consistent air, crucial for achieving high-quality finishes and ensuring that coatings adhere properly and surfaces are treated uniformly.
Compressed air also supports assembly line operations by powering tasks like clamping, lifting, positioning parts, and specialised assembly tools. Compressor reliability ensures assembly lines run smoothly with minimal downtime, contributing to efficient production flow.Further, compressed air is used for cooling purposes in various manufacturing processes and for cleaning workpieces, tools, and machinery. Air compressors provide the necessary air volume and pressure to effectively cool and clean, helping maintain the quality of components and extending the life of tools and equipment.
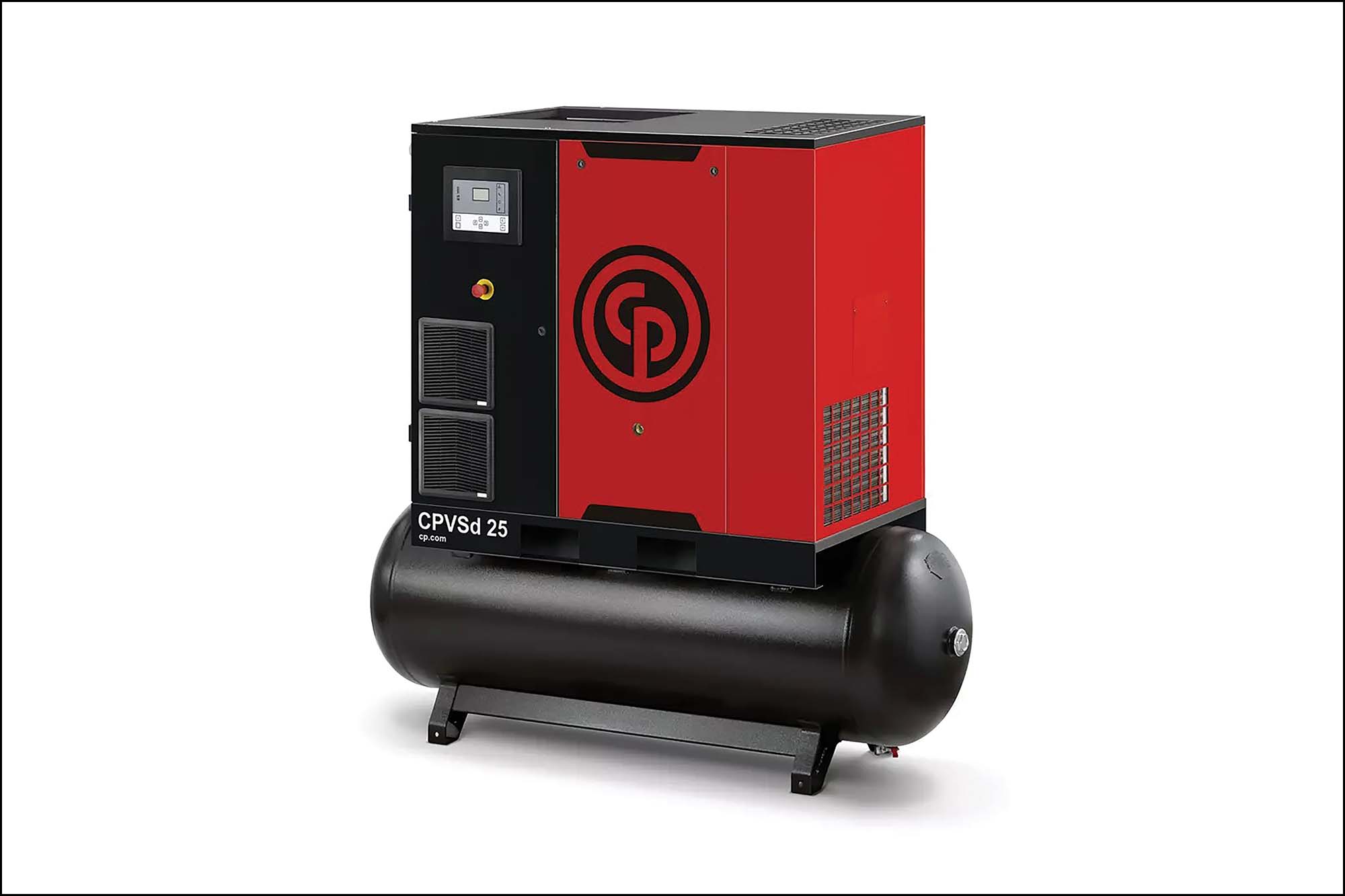
Advantages
Screw air compressors offer several advantages, making them suitable for aerospace manufacturing environments. They are designed for continuous, heavy-duty operation, allowing them to run around the clock. These compressors are also highly efficient, providing a stable supply of compressed air with minimal energy consumption, which is crucial for maintaining cost-effective aerospace production.
Another key benefit is their low maintenance requirements. Screw compressors have fewer moving parts compared to other types, resulting in reduced maintenance needs and reduced downtime, a factor in high-demand production settings. Their compact design allows for easy integration into various spaces in a factory, saving space while still delivering the necessary power.
In aerospace manufacturing, screw compressors are indispensable for ensuring that various production processes run smoothly and efficiently. They power essential tools and machinery, support automation, aid in surface treatment and assembly, and contribute to maintaining the high standards required in aerospace production. Their reliability, efficiency, and low maintenance make them a key component in any aerospace factory’s production line. Maintenance makes them a key element for any aerospace factory’s production line
Cookie Consent
We use cookies to personalize your experience. By continuing to visit this website you agree to our Terms & Conditions, Privacy Policy and Cookie Policy.