Automated MELSS line with industry 4.0 for BLDC motors from MELSS
By Staff Report August 9, 2024 6:16 pm IST
Brushless DC (BLDC) motors are used in various applications. Innovation in BLDC motor design is driving its use in many different applications. Automating the assembly of BLDC motors enhances production efficiency, ensures consistency, and reduces labour costs.
I nnovation in BLDC motor design is driving its use in many different applications. Recently, there has been an increase in market demand for BLDC motors. Subsequently, many manufacturers are moving away from traditional manual assembly and adopting automated lines.
Brushless DC (BLDC) motors find applications in Inverter ACs, Inverter Refrigerators, Electric Vehicles and Ceiling Fans because of their high efficiency, reliability, and longevity. Automating the assembly of BLDC motors enhances production efficiency, ensures consistency, and reduces labour costs.
Automated assembly process for BLDC Motor
MELSS has meticulously designed, manufactured and commissioned a Special Purpose Machine (SPM) that automates the assembly process for the BLDC motor. This purpose-built multi-station design aligns with specific customer requirements for the assembly process, ensuring precision at every step. The automation setup incorporates multiple technologies involving both 4-axis and 6-axis Robots, Multi-axis Gantry systems, feeding systems like bowl-feeders and carousels and precision dispensing systems, all linked to a conveyor system with pallet return function. Preset control commands ensure the stability, speed and accuracy of automated processes. By working on the Takt time, only the optimum manpower use enables consistency, accuracy, and high throughput without human fatigue.
Traceability allows close monitoring and tracking of the details of the various input materials. Interlocking and Poke-Yoke reduce errors in assembly. As a result, product information across shifts, batches, suppliers and workforce can be tracked to provide comprehensive reports and management dashboards that allow real-time performance monitoring. This monitoring can improve the OEE of the operations in the long run, which is critical to managing the cost of the product. The automated assembly process not only ensures immediate benefits in terms of efficiency and cost reduction but also promises long-term advantages in terms of product quality and performance, giving you confidence in your investment.
The separate stator and rotor sub-assembly lines are joined in the Main assembly process designed by MELSS. The automation process begins with preparing and supplying components, including stators, rotors, bearings, windings, and electronic controllers. Automated systems ensure precise handling and delivery of these components to the assembly line using vibratory feeders, conveyor belts, or robotic arms for a continuous supply with minimised downtime. Automated systems ensure the free movement of the rotor within the stator without friction before assembling them within the motor housing.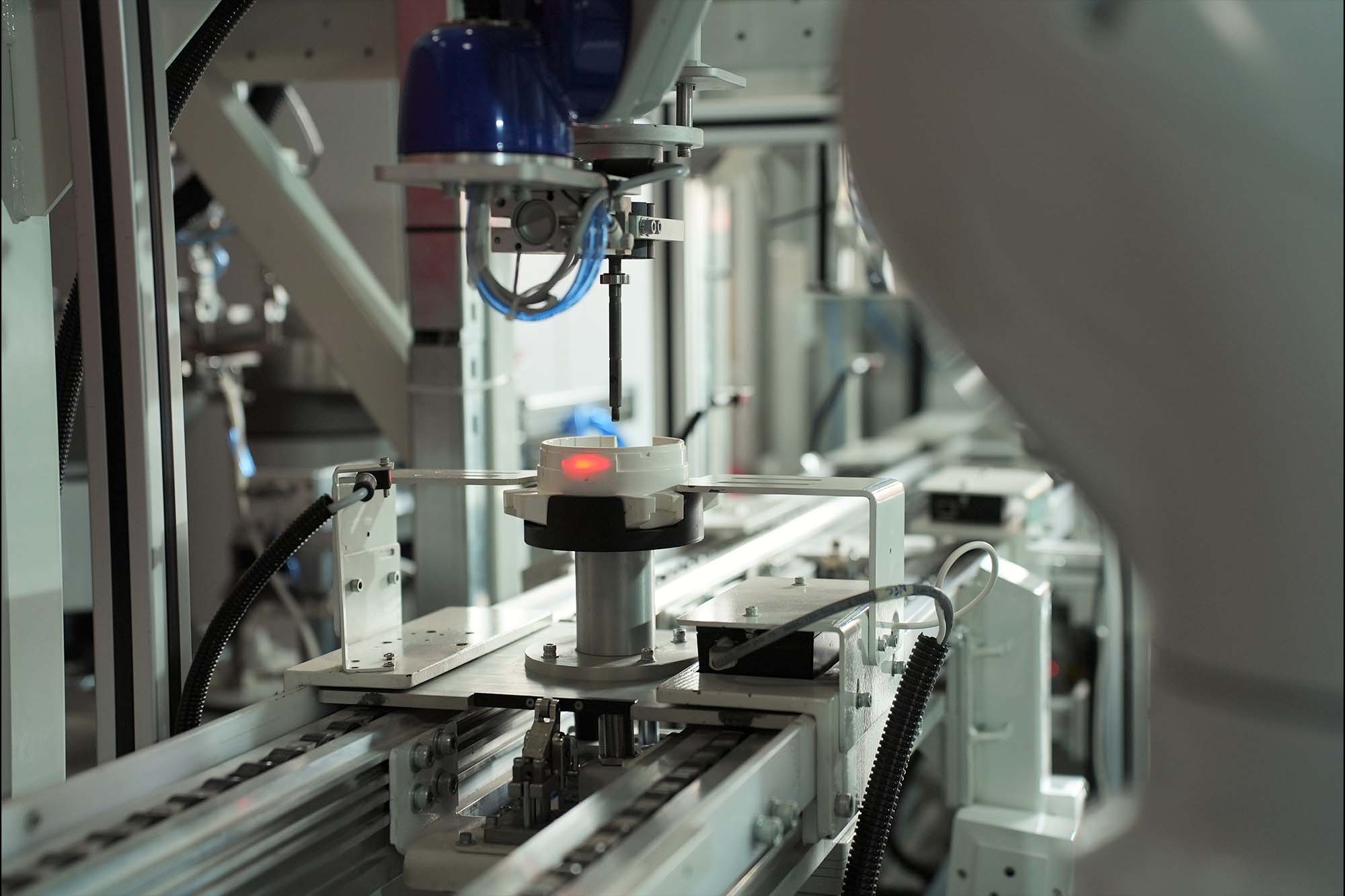
Automation for quality assurance
Automation involves placing many small-sized components like washers, bushes and e-clips, Rotors, PCBs, endcaps, etc. Picking and placing these components in precise orientation and positions is accomplished using a combination of positional Gantry systems and Robotic arms. The electronic control board is attached and wired to the motor windings. Automated soldering systems and robotic arms perform these tasks to ensure reliable electrical connections. This line designed by MELSS can cater to large throughput volumes with precision. All this automation means an improvement in repeatability and reproducibility. It implies meeting the quality standards for the product.
At MELSS, we value our customers’ unique requirements and work closely with them to custom design cost-effective solutions that suit their needs and ensure manageable Return on Investment. We believe in a collaborative approach, where our customers are an integral part of the design process, ensuring that the final product meets their expectations and requirements.
Contact MELSS at +91 7825873001 to learn about the details of our cutting-edge equipment, and we will work with you to help design the shop floor for the future.
Cookie Consent
We use cookies to personalize your experience. By continuing to visit this website you agree to our Terms & Conditions, Privacy Policy and Cookie Policy.