Digitising sourcing and manufacturing processes to ramp up your EV space
By OEM Update Editorial June 18, 2024 6:41 pm IST
Digitising sourcing and manufacturing processes in the EV industry assists operations management while boosting production capabilities in response to evolving market demands. Sonam Motwani, CEO and the Founder of Karkhana.io, shares her expertise in digitising manufacturing while navigating challenges.
Innovation is propelling growth in the fast-paced world of electric vehicles (EVs), with digitised sourcing and manufacturing processes emerging as a game changer. This digital transformation is more than implementing new technology; it is about altering how EV components are obtained, developed, and manufactured to simplify processes, improve efficiency, and increase output. This digital revolution provides several benefits, such as streamlining operations and improving efficiency and manufacturing capacities across the EV sector.
Challenge: Complexity in a new landscape
Digitising EV sourcing and manufacturing processes presents unique complexities to traditional automotive manufacturing. The intricate nature of EV components, such as batteries and electric motors, requires specialised expertise and stringent quality control measures. EV manufacturers collaborate with a diverse network of suppliers for advanced technology components, adding layers of complexity to supply chain management. The rapid pace of innovation in EVs further amplifies the challenge, necessitating continuous adaptation to evolving technologies and market dynamics. Despite these complexities, digital transformation offers opportunities for efficiency gains, cost optimisation, and accelerated innovation in the dynamic EV industry.
Digital transformation across the chain
Supply chain management receives a considerable boost from digitisation. Digital platforms provide visibility into the entire supply chain, from raw material sourcing to final product delivery. This visibility enables manufacturers to optimise inventory levels, minimise stockouts, and ensure timely component deliveries, ultimately reducing production delays and improving overall efficiency.
Another area where digitisation shines is efficient component sourcing. With digital platforms, EV manufacturers gain access to a vast network of suppliers. These platforms centralise supplier information, allowing manufacturers to quickly identify sources for required components at competitive prices, reducing the time and costs associated with sourcing.
Through digitisation, data-driven decision-making becomes a reality. Manufacturers gain valuable insights into inefficiencies, bottlenecks, and areas for improvement by collecting and analysing data throughout the manufacturing process. This data-driven approach allows for continuous optimisation of production processes, driving efficiency and innovation.
Digital manufacturing processes also enable greater customisation and personalisation of EVs. Manufacturers can easily modify product designs and configurations to meet specific customer requirements, catering to the growing demand for personalised vehicles.
Furthermore, digital manufacturing processes are inherently scalable and adaptable, allowing manufacturers to quickly respond to changing market demands. Whether ramping up production in response to increased demand or introducing new product variants, digital technologies enable manufacturers to adapt swiftly without significant retooling or reconfiguration.
Quality control also benefits significantly from digitisation. Real-time monitoring of manufacturing processes and quality parameters enables manufacturers to track key performance indicators and identify defects or deviations early on. By taking corrective actions promptly, manufacturers can maintain high-quality standards throughout the production process.Digital tools, such as Computer-Aided Design (CAD) software and virtual prototyping, enhance design and prototyping processes. These tools enable rapid iteration of EV components, reducing the time and resources required for physical prototyping and accelerating the product development cycle.
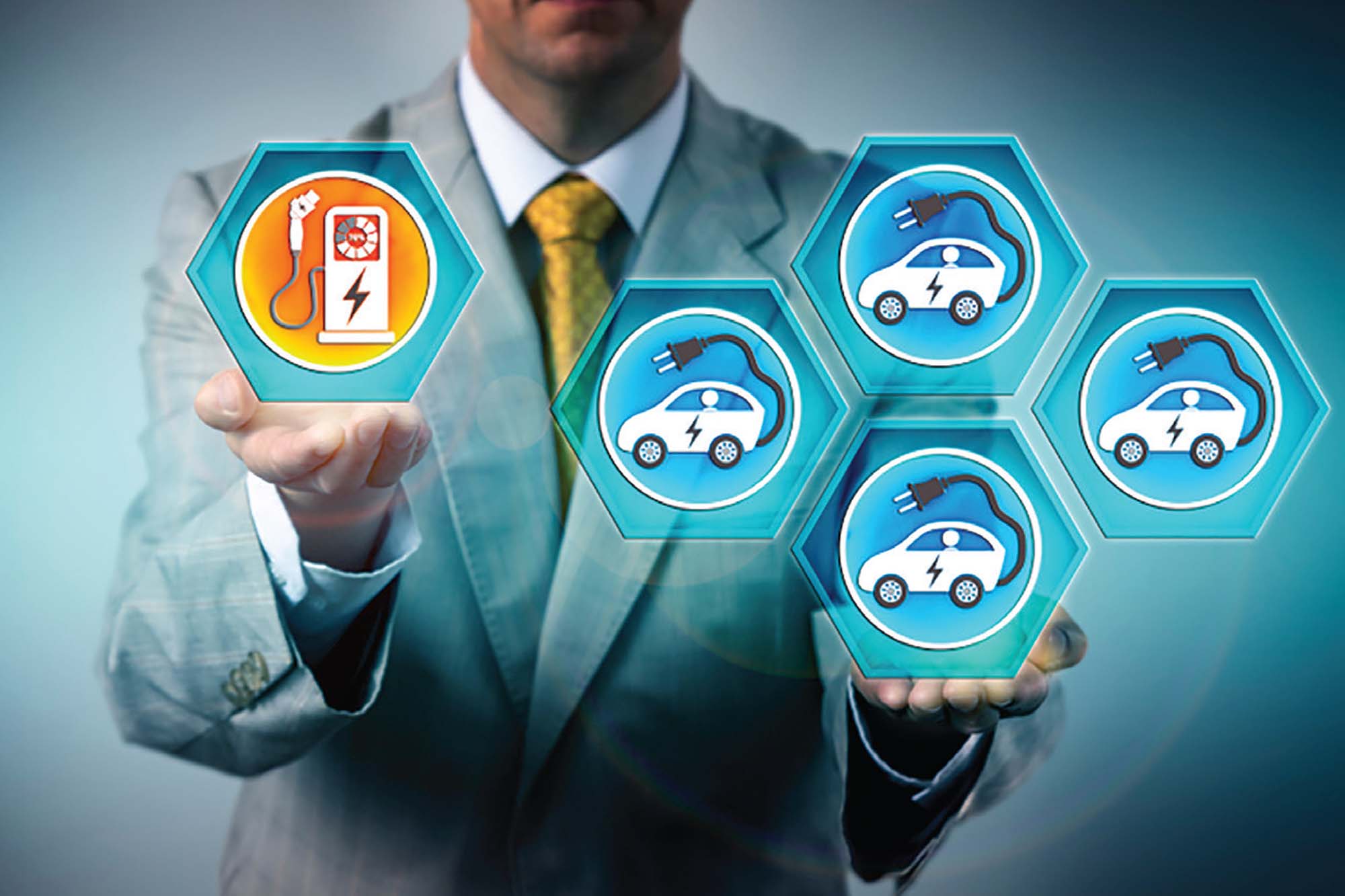
Predictive maintenance, made possible by IoT-enabled sensors and data analytics, minimises unplanned downtime by allowing manufacturers to monitor the health and performance of EV components in real-time. By analysing data on equipment usage, temperature, and other parameters, manufacturers can predict maintenance needs and schedule proactive maintenance.
Energy efficiency and sustainability are central tenets of the EV industry, and digitisation is crucial in achieving these goals. By optimising energy consumption and resource utilisation in manufacturing processes, digital technologies help reduce the carbon footprint of manufacturing operations, aligning with environmental objectives.
One of the most significant advantages of digitisation in the EV space is streamlined communication and collaboration. Digital platforms facilitate seamless interaction among stakeholders, including suppliers, manufacturers, and designers. Real-time messaging, file sharing, and collaboration tools ensure everyone is synchronised, minimising misunderstandings and delays. This enhanced communication lays the foundation for efficient collaboration throughout the production process.
The road ahead
Digitisation is not a solo endeavour. Effective implementation requires collaboration between EV manufacturers, suppliers, and logistics providers. Companies like Karkhana.io exemplify the potential of digital platforms to transform the EV industry. By linking manufacturers with a broad array of trusted suppliers and offering live updates on the manufacturing journey, manufacturers can make informed decisions, streamline processes, and foster innovation within the EV sector. The EV industry can forge a fully digital ecosystem through collaboration and the adoption of unified data exchange standards.
Furthermore, digitisation paves the way for a sustainable EV production process. Manufacturers can reduce their environmental footprint with thoughtful resource allocation and minimising waste. Additionally, real-time data on supply chains can help identify ethically sourced materials, promoting responsible practices within the industry.
In conclusion, digitising sourcing and manufacturing processes drives efficiency and production capabilities in the electric vehicle industry. By embracing digital technologies, EV manufacturers can achieve greater operational efficiency, higher productivity, and increased competitiveness in a rapidly evolving market.
Cookie Consent
We use cookies to personalize your experience. By continuing to visit this website you agree to our Terms & Conditions, Privacy Policy and Cookie Policy.