Life cycle assessment of MWF systems
By OEM Update Editorial October 5, 2023 6:51 pm IST
The case study highlights the use of HYCUT in metalworking, leading to a significantly lower environmental impact than a conventional, mineral oil-based coolant system used for the same purpose. Internal recycling becomes possible, leading to substantially more sustainable use of cooling lubricants in the machining process chain.
Life cycle assessment of metal removal fluid systems in metalworking applications
Cooling lubricants (MWF) are widespread in industrial metalworking because their cooling, lubricating, and flushing effects enable a high-performance and economical machining process. Typically, conventional water-miscible or non-water-miscible cooling lubricants based on mineral oil are used for this purpose. However, mineral oil extraction, production, use, and disposal involve many adverse ecological impacts. Furthermore, the choice of cooling lubricants also plays a crucial role in determining the sustainability of the machining process chain.
Assessment of environmental impacts based on the example of crankshaft production.
A significant portion of the cooling lubricant is removed due to adhesion to the workpiece. Depending on the type of cooling lubricant used in the subsequent process stage, a time-consuming intermediate wash may be required. To eliminate the need for this inconvenience, Oemeta has developed the multi-purpose oil HYCUT, which can be used as either a non-water-miscible machining oil or a water-miscible emulsion. Unlike conventional cooling lubricants, it has been developed based on renewable raw materials, offering environmental benefits.
In collaboration with the Institute for Machine Tools and Production Technology at TU Braunschweig in Germany, the potential environmental impacts of the Oemeta HYCUT product series were tested through a life cycle assessment and compared to those of a conventional mineral oil-based reference lubricant system.
Application of the life cycle assessment method at an Austrian engine plant
To arrive at a holistic assessment of a product’s environmental impact, the entire life cycle is considered, encompassing everything from the extraction of raw materials and production to usage and final disposal. This comprehensive analysis factors in the resources consumed and the emissions produced throughout the life cycle, converting them into environmental impacts.
This LCA was carried out as a case study at a German car manufacturer’s engine plant in Austria. The process chain for crankshaft production was under scrutiny here: this involves the most diverse machining processes, including milling, turning, deep drilling and grinding. The process chain also involves frequent changes between water-miscible and non-water-miscible MWFs (see Figure 1).
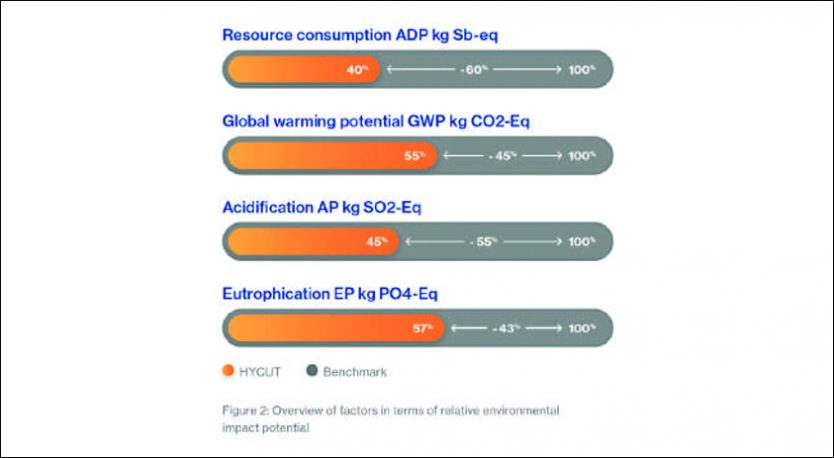
Oemeta HYCUT offers a sound ecological balance.
In practice, the process chain already utilizes the ester-based multi-purpose oil HYCUT, formulated so that water-miscible and non-water-miscible components are compatible. Consequently, mutual entrainment of cooling lubricant adhesions on parts is not a problem, as with conventional cooling lubricants. Compared to mineral oil-based reference products, using this cooling lubricant along the entire production line is much more efficient, as it significantly reduces the need for intermediate washing and minimizes waste of the MRF.
In particular, re-using the washing agent from the workpiece cleaning operation as a cooling lubricant for the machining processes positively affects the life cycle assessment. Planners tailored the production chain design to the specific lubricant to take full advantage of the multi-purpose oil. Normally, several systems are required to clean the workpieces, for example, but this was not necessary here. Using the HYCUT system in all environmental impact categories under review results in significantly lower environmental impacts (40-60 %) over the entire life cycle than in the case of the reference system (see Figure 2).
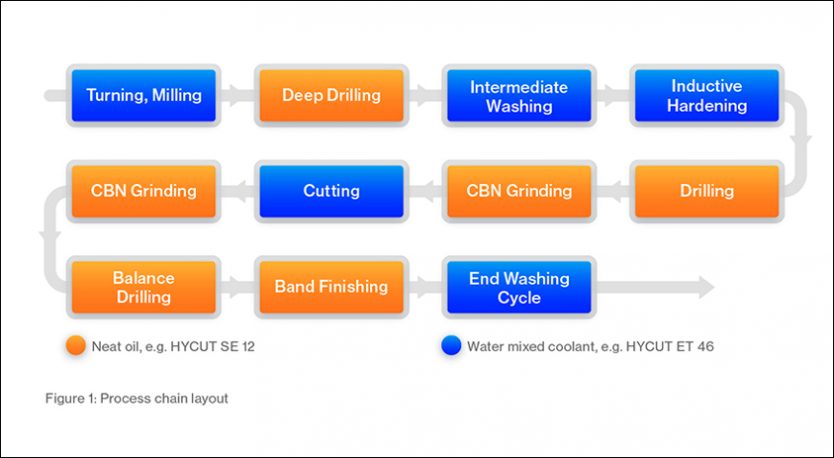
Comparisons regarding global warming potential (GWP) savings.
Regarding Global Warming Potential (GWP), the case in question generated savings of approximately 470 t CO2-eq in annual production – equivalent to the environmental impact caused by driving 158 passenger cars for one year[1] (see Figure 3). The absolute figures are case-specific and depend on the comparative basis, the system, and the processes under consideration. In contrast, the relative figures indicate the general comparative tendency.
The life cycle assessment thus showed that using HYCUT in metalworking leads to a significantly lower environmental impact than a conventional mineral oil-based coolant system used for the same purpose.
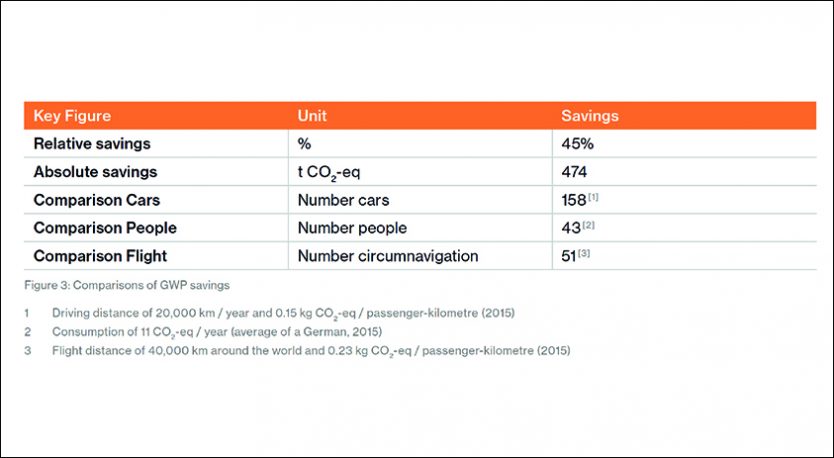
For more info: barthwal@oemeta.com
in.oemeta.com
Cookie Consent
We use cookies to personalize your experience. By continuing to visit this website you agree to our Terms & Conditions, Privacy Policy and Cookie Policy.