AI algorithms prevent faulty products, save time and cost
By OEM Update Editorial July 31, 2023 2:15 pm IST
Anil Kumar R, the Managing Director of Inovance Technology India, highlights the immense potential of IoT in empowering enterprises to monitor and manage crucial facets of industrial production efficiently.
How is Inovance’s easy Series PLC with EtherCAT integration contributing to the manufacturing industry’s transformation?
Smart automation is a crucial factor in enhancing efficiency by leveraging advanced technologies and intelligent systems to streamline processes and boost business productivity. A key advantage of smart automation in the manufacturing industry lies in its ability to perform repetitive tasks with unparalleled speed and precision without needing breaks like humans do. This ensures consistent production and yields high-quality results in a shorter timeframe. Smart manufacturing systems, such as resource management, enable real-time monitoring and predictive maintenance using IoT and AI, preventing equipment failures and reducing machine downtime.
Understanding the growing demand for smart automation, Inovance offers a comprehensive range of automation products, including AC drives, servo drives and motors, industrial robots, PLCs, CNCs, and HMIs. The compact EtherCAT-enabled Easy Series PLC is a recent addition designed to control simple to complex motion control applications using EtherCAT and Ethernet/IP. This PLC boasts easy programming, wiring, assembly, and commissioning and supports function block and encapsulation, code reusability, and scalability, empowering customers to achieve maximum efficiency. Notably, the Easy PLC series finds wide applicability in complex automation solutions across the textile, packaging, and printing industries.
How are smart technologies simplifying manufacturing processes and contributing to the goal of becoming a global manufacturing hub?
After introducing the “Make in India” initiative by the Indian government in 2014, the country has undergone a significant transformation, aiming to establish itself as a global manufacturing hub. The government’s focus on initiatives like “Make in India” and the integration of advanced technologies has led to the rapid growth of smart automation in the manufacturing sector.
In 2018, Prime Minister Narendra Modi launched Industry 4.0 as part of India’s national strategy, intending to utilise smart manufacturing to revolutionise the present and future of Indian manufacturing industries. As a result, various smart technologies like artificial intelligence (AI), machine learning, the Internet of Things (IoT), blockchain, and big data have been making strides in India, simplifying manufacturing processes from monitoring to operations.
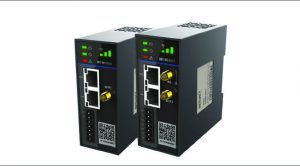
IoT
In what ways integration of IoT and robotics is boosting manufacturing efficiency and productivity?
Smart automation in production processes depends on various crucial technologies that aim to optimise efficiency, boost productivity, and facilitate intelligent decision-making. Among these technologies, the Internet of Things (IoT) plays a significant role by enabling businesses to monitor and manage various aspects of production, including machine performance, inventory levels, and environmental conditions. Additionally, robotics plays a vital part in performing complex tasks with unmatched precision, speed, and quality, leading to overall enhancements in productivity and efficiency. Furthermore, cyber security is of utmost importance in smart manufacturing, where interconnected systems are utilised, safeguarding against potential risks like data theft.
Implementing artificial intelligence systems for defect detection has the potential to enhance quality control processes in manufacturing and significantly boost productivity. These AI systems excel at analysing vast amounts of data with remarkable precision, allowing them to identify even the most minor defects that might be challenging for humans to spot. By detecting defects early in the production process, AI algorithms can prevent the creation of faulty products, saving both time and costs for manufacturers. Continuous training of AI-powered systems using machine learning techniques is essential to improve their efficiency and accuracy and fully harness their benefits. However, it’s crucial to acknowledge that AI-powered systems have limitations, as they rely solely on the training data and may struggle to identify complex or novel defects accurately. Therefore, ongoing maintenance and fine-tuning are necessary to achieve the best results. Combining human expertise and AI-powered algorithms is critical for driving quality improvements in the manufacturing sector.
Please discuss key features of the recent Inovance AC drive and how it helps achieve energy efficiency in manufacturing operations.
Inovance solutions have played a vital role in elevating the productivity and efficiency of numerous Indian manufacturers through their innovative and cutting-edge products. A recent success story involves a paper and plastic disposable product manufacturer in India, where Inovance’s MS1 series servo motors significantly enhanced productivity and precision in the production process. Using EtherCAT communications ensured effective control, resulting in remarkable speed and accuracy improvements. By incorporating Inovance’s servo drives, motors, and HMI, the manufacturer experienced optimised performance and reduced production times, showcasing Inovance’s commitment to transforming the manufacturing landscape with innovative solutions.
Inovance recently introduced the MD520 high-performance universal AC drive, representing a significant advancement in motor control technology. This versatile AC drive offers efficient control for AC asynchronous and PM synchronous motors, catering to various industrial applications. Designed with a focus on reliability and durability, the MD520 is built to withstand harsh industrial environments, ensuring uninterrupted operation and minimising customer downtime. Inovance’s MD520 helps achieve energy efficiency in industrial processes, with these energy savings potentially leading to reduced operating costs and a more sustainable manufacturing operation.
What are some of the potential challenges that businesses might face while adopting advanced technologies?
As the use of smart automation in manufacturing processes is quite new, there are a few potential challenges in adapting to smart production, such as-
- Cost of implementation: For any company to implement a smart automation system requires upfront investment and special training for employees to understand the operation and maintenance of the smart automation systems installed.
- Flexibility and scalability:The system needs to adjust and change according to growing business and production needs and market demands, which can include handling different products and production volumes.
- Security & Privacy:The smart automation system depends on collecting and analysing precise sets of data, which can raise concerns about the safety of sensitive and confidential information stored in the system and the potential risk of data theft.
- Workforce adaptation:The transition from traditional to smart automation will require employees to understand and adapt to smart automation processes. They also must learn new skills to work alongside the smart systems. Companies transitioning to smart automation should organise training programs and address other concerns of their employees to ensure the smooth functioning of their operations.
What advantages do Cobots bring to SMEs for enhanced efficiency and competitiveness?
Due to various challenges, traditional robots may need to be better suited for SMEs. This may be due to the lengthy installation times, high prohibitive costs for smaller companies, and the need for specialised expertise to operate them. On the other hand, a new generation of robots called cobots is emerging as an ideal solution for SMEs as they overcome these issues.
Cobots are revolutionising manufacturing and production processes primarily because they are incredibly easy to program. They often employ user-friendly software that can be customised to specific requirements without requiring specialised knowledge. Their collaborative nature, designed to work alongside human operators, sets cobots apart. They are compact, mobile, and adaptable, seamlessly integrating into existing operations and offering flexibility in their deployment. By leveraging cobots, human workers can focus on creative and problem-solving tasks, while cobots handle laborious and repetitive work. This results in an enhanced work environment, increased productivity, and higher output quality.
Cookie Consent
We use cookies to personalize your experience. By continuing to visit this website you agree to our Terms & Conditions, Privacy Policy and Cookie Policy.