AI to enhance equipment utilisation and QC
By OEM Update Editorial June 12, 2023 10:32 am IST
According to Bheemsingh Melchisedec, the Director of Operations at ELGi Equipments, integrating AI into an IoT systemfor industrial equipment enables the equipment to autonomously evaluate data, analyse it, make decisions, and notify management to take necessary actions.
How has ELGi’s adoption of renewable energy and efficient resource management strategies contributed to reducing environmental impact?
Recognising the climate crisis’s economic, environmental, and social impacts early, ELGi introduced renewable energy projects more than two decades ago to eliminate greenhouse gas emissions from our manufacturing operations. We have long prioritised efficient resource management, implementing various strategies to recycle water and minimise waste generation. Our goal is to achieve resource-neutral operations by the end of the current decade, focusing on reducing freshwater usage by 50 percent and minimising waste generated in our processes.
Some of the practices already implemented at our manufacturing facilities have greatly contributed to enhancing energy efficiency and minimising our carbon footprint. To replace conventional energy meters, smart meters can detect loads based on amperage, identify idle machinery, and optimise load distribution. This adoption of smart meters has led to annual electricity savings of approximately 1.5 million units.
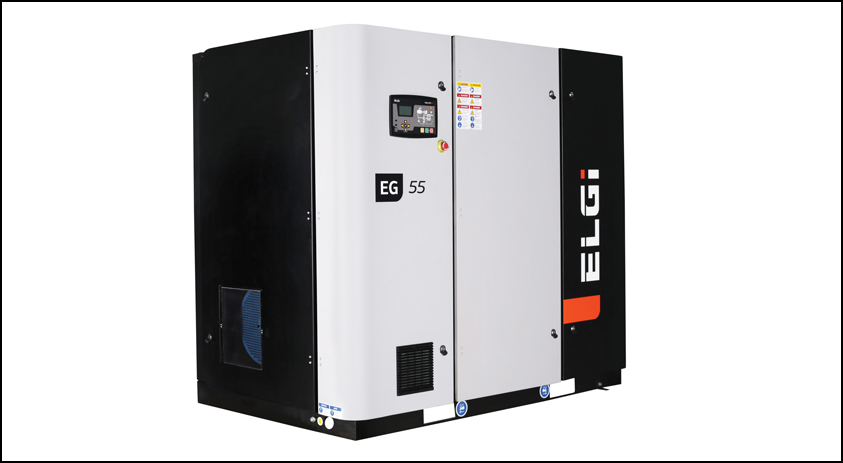
ELGi also has an Energy Management System (EnMS) encompassing 145 interconnected IoT-enabled machines at its Air Compressor Plant (ACP). Using advanced statistical tools, these machines analyse collected data to identify potential energy-saving opportunities. Implementing this IoT-enabled energy management system has led to a remarkable 24 percent improvement in energy efficiency within our plant operations. As a result, we have achieved annual energy savings of approximately 1.02 MW, leading to substantial cost reductions in energy expenditure.
How has your focus on energy efficiency and green certifications impacted their compressors’ design, manufacturing, and performance?
Regarding ELGi products, the primary objective is to develop energy-efficient compressors that promote optimal energy consumption and reduce energy expenses for our customers. ELGi also received Green Product certifications for more than 28 of our compressors. These certifications validate that environmentally friendly practices have been implemented throughout the entire product lifecycle, encompassing the sourcing of raw materials, design and manufacturing processes, and even disposal methods. ELGi’s screw compressors have large premium efficiency airends equipped with in-house developed η-Vprofile rotors, with 4/5 lobe combinations that rotate in opposing directions. These airends are designed to run at slow speeds with reduced pressure losses, offering high volumetric efficiency and lower energy consumption.
Among other facilities deployed, ELGi’s Heat Recovery Systems (HRS) allow businesses to harness up to 96 percent of the heat that would otherwise go to waste during the compression process. This captured heat is then utilised to warm air or water for various applications. As a result, there is a substantial reduction in the requirement for additional heating systems powered by conventional sources, leading to a significant decrease in CO2 emissions and overall energy consumption.
How does Industry 4.0 help in fuelling the transformation of Indian manufacturing?
The adoption of Industry 4.0 technologies holds significant advantages for the manufacturing sector. It enables the creation of a connected ecosystem comprising systems, devices, people, and data. Real-time data access allows for faster decision-making and, in some cases, autonomous decision-making capabilities. Industry 4.0 allows managing and monitoring energy usage in manufacturing facilities efficiently, resulting in substantial energy savings and a reduced carbon footprint. Furthermore, it facilitates the implementation of data-driven production processes that simultaneously optimise equipment utilisation, preventive maintenance, and quality control. All relevant stakeholders will have instant access to critical manufacturing processes, from raw material sourcing to various production-related activities. The remote monitoring and control of manufacturing equipment made possible by Industry 4.0 will enhance flexibility and productivity to a great extent.
Using IoT sensors in workplace safety regulations reduces potential health risks and establishes a secure working environment. It enables faster production operations and minimises human errors in manufacturing processes. By leveraging IoT devices, manufacturers can predict optimal maintenance schedules and proactively address equipment issues, reducing downtime.
How can integrating real-time analytics, AI, and industrial IoT systems help manufacturers optimise productivity?
With real-time analytics and AI integration, manufacturers can efficiently collect and analyse large volumes of data, enabling them to make data-driven decisions promptly. When AI is incorporated into industrial IoT systems, the equipment can autonomously review and analyse data, make informed judgments, and alert management for appropriate actions to ensure equipment and process maintenance. This technology also facilitates swift updates and revisions to standard operating procedures and training materials, increasing their value and relevance to user teams. This approach is crucial in achieving productivity enhancements through the “Do More with Less” principle.
Cookie Consent
We use cookies to personalize your experience. By continuing to visit this website you agree to our Terms & Conditions, Privacy Policy and Cookie Policy.