Lean manufacturing for aerospace components production
By Staff Report August 31, 2024 5:29 pm IST
Anuj Jhunjhunwala, CEO, describes JJG Machining Group’s journey from conventional lathes to advanced CNC technology as a dedication to precision and efficiency in aerospace and defence manufacturing. He says we ensure superior quality and reliability by leveraging machinery, lean practices, and a commitment to Atmanirbharta.
How has JJG Aero Pvt Ltd transitioned from simple turned parts to becoming a key player in aerospace and defence manufacturing?
Our journey began with conventional multi-spindle lathes, where we specialised in producing simple turned parts. Over time, we strategically enhanced our technological capabilities by incorporating CNC-controlled turning to improve precision and efficiency. As our expertise grew, we adopted more advanced equipment, such as multi-axis Swiss-style CNC lathes. It allowed us to handle more complex geometries with greater accuracy. This progression continued with fixed-head turn-mill machines, enabling us to diversify machining operations. In milling, we initially focused on 3 to 4-axis machining, which got enhanced to the 4+1 axis, and we have now fully embraced 5-axis machining capabilities. This evolution in our machining technology has positioned us as a key player in aerospace manufacturing, capable of meeting the demands of high product mix and low-volume production that are standard in this industry.
How do your equipment and lean manufacturing techniques improve precision and efficiency for aerospace and defence components?
Our commitment to precision and efficiency is exhibited by our investment in state-of-the-art machinery from leading manufacturers such as Mazak and Takisawa for turning operations and Makino and Mazak for milling. These machines are known for their durability and exceptional accuracy, enabling us to produce high-precision components with the correct specifications. In parallel, we have implemented lean manufacturing techniques across our production processes, which allow us to minimise waste, reduce non-value-adding activities, and streamline workflows. By decreasing inefficiencies and cutting down on waiting times, we not only enhance productivity but also maintain a high level of quality, ensuring that our aerospace components meet industry standards.
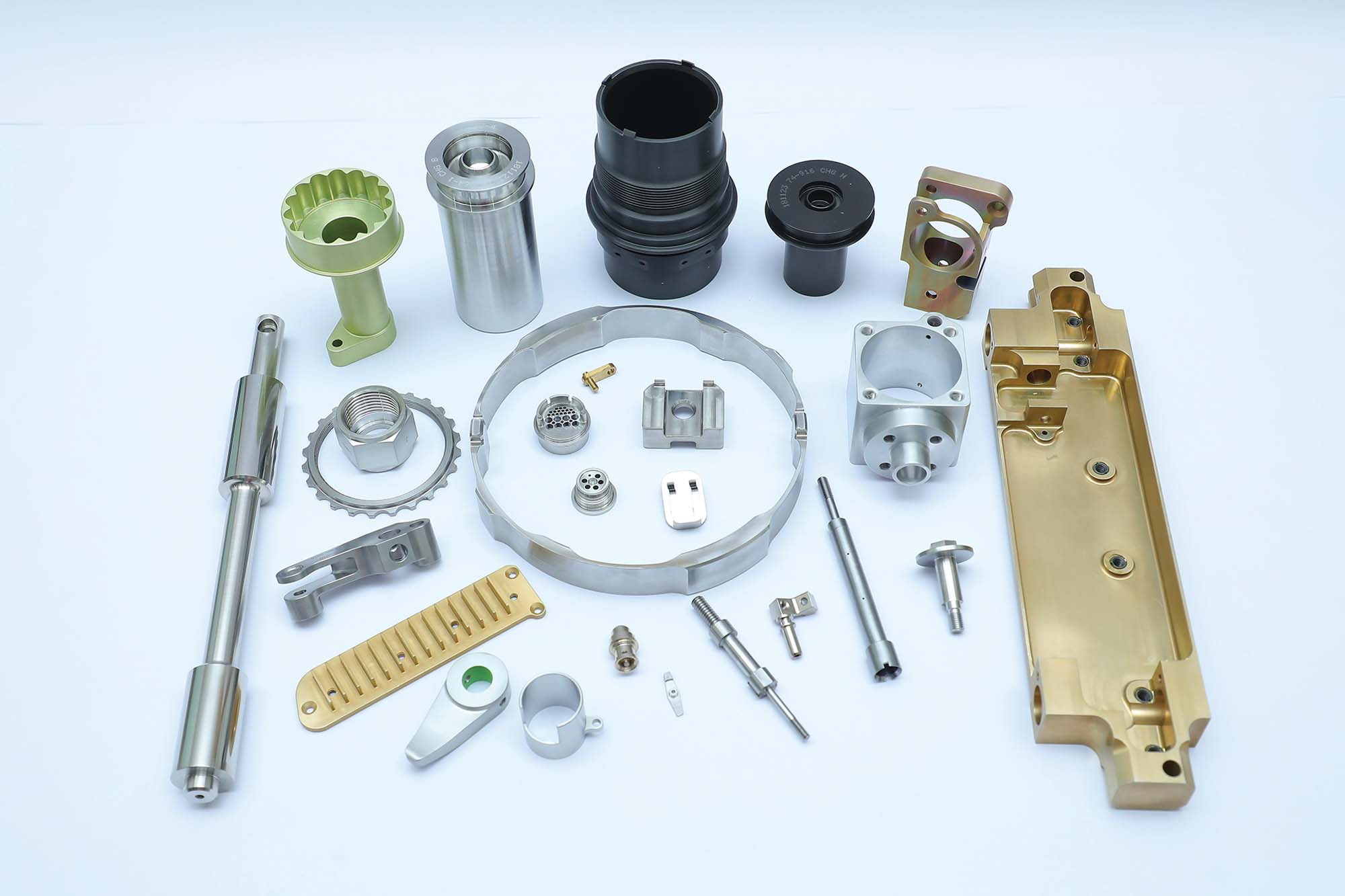
How do your in-house Special processes ensure the quality and reliability of components for the aerospace and defence sectors?
Our in-house Special processes, particularly in aerospace and defence, mark a crucial aspect of our operations, where quality and reliability are paramount. Unlike many manufacturers relying on external service providers for these critical processes, we have developed extensive in-house expertise over two decades. It allows us to maintain complete control over the quality and consistency of our components, ensuring that every part meets rigorous industry standards. Additionally, our processes are fully accredited by regulatory and certification bodies, including PRI, demonstrating our compliance with the highest levels of industry regulation. This autonomy enhances our reliability and reduces lead times and dependency on external vendors, giving us a significant competitive edge in delivering high-quality, dependable products to our clients.
Could you elaborate on initiatives taken for Atmanirbharta in the production facility?
As part of our commitment to the self-reliant India initiative, we are working with OEMs to facilitate the approval and integration of locally sourced raw materials. These raw materials are our primary imported input, but we focus on reducing this dependency by collaborating with domestic suppliers to meet the required standards. Once this transition to local procurement is established, our production will feature an exceedingly high percentage of local content, with estimates indicating that it will reach close to 97-98 percent. It supports the broader national goal of self-reliance and enhances our sustainability by reducing reliance on international supply chains and fostering the growth of the domestic manufacturing ecosystem.
Cookie Consent
We use cookies to personalize your experience. By continuing to visit this website you agree to our Terms & Conditions, Privacy Policy and Cookie Policy.