Recent success stories of CLOOS India
By Staff Report September 17, 2024 12:23 pm IST
CLOOS’s customised single-source welding technology solution has been redefining the welding industry for a decade. Sumon Mitra, COO of Cloos India Welding Technology, affirms that CLOOS is at the forefront of innovation with its comprehensive solutions.
Cloos successfully installed Robotic welding and cutting solution for the Crusher Rotor to Larsen & Toubro.
CLOOS Cutting Solution
Cutting technologies play an important role in modern production. The demand for it is continuously increasing, just like for welding. Cutting systems must become faster and more precise. The machining time for a component will be minimised, and the material will be used efficiently and with perfect production quality. At the same time, user-friendliness, production reliability and energy efficiency are crucial. Innovative cutting technologies are in demand to meet these increasing efficiency and quality requirements. It is important to match it perfectly with the respective task and to consider future projects when selecting a suitable cutting system. Therefore, CLOOS offered Larsen & Toubro Robotic a cutting solution with an automatic tool changer to resolve the issue of manual cutting quality and time. Cutting was dimensioned to 80 mm to 120 mm thickness star plate using Oxy-fuel flame cutting. On average, using robot technology for cutting saves manufacturing costs of 25 to 30 percent, with a considerable change in quality. Cloos offers the optimum machining technology for any available welding and
cutting task.
CLOOS welding Solution
Larsen & Toubro rely on CLOOS as a singlesource provider for welding the Crusher Rotor, completely changing their 3-stage welding process. They also benefit from the CLOOS Tandem Weld technology, which offers maximum deposition with lower heat input and an automatic tool changer for a single torch used on critical welding seams.
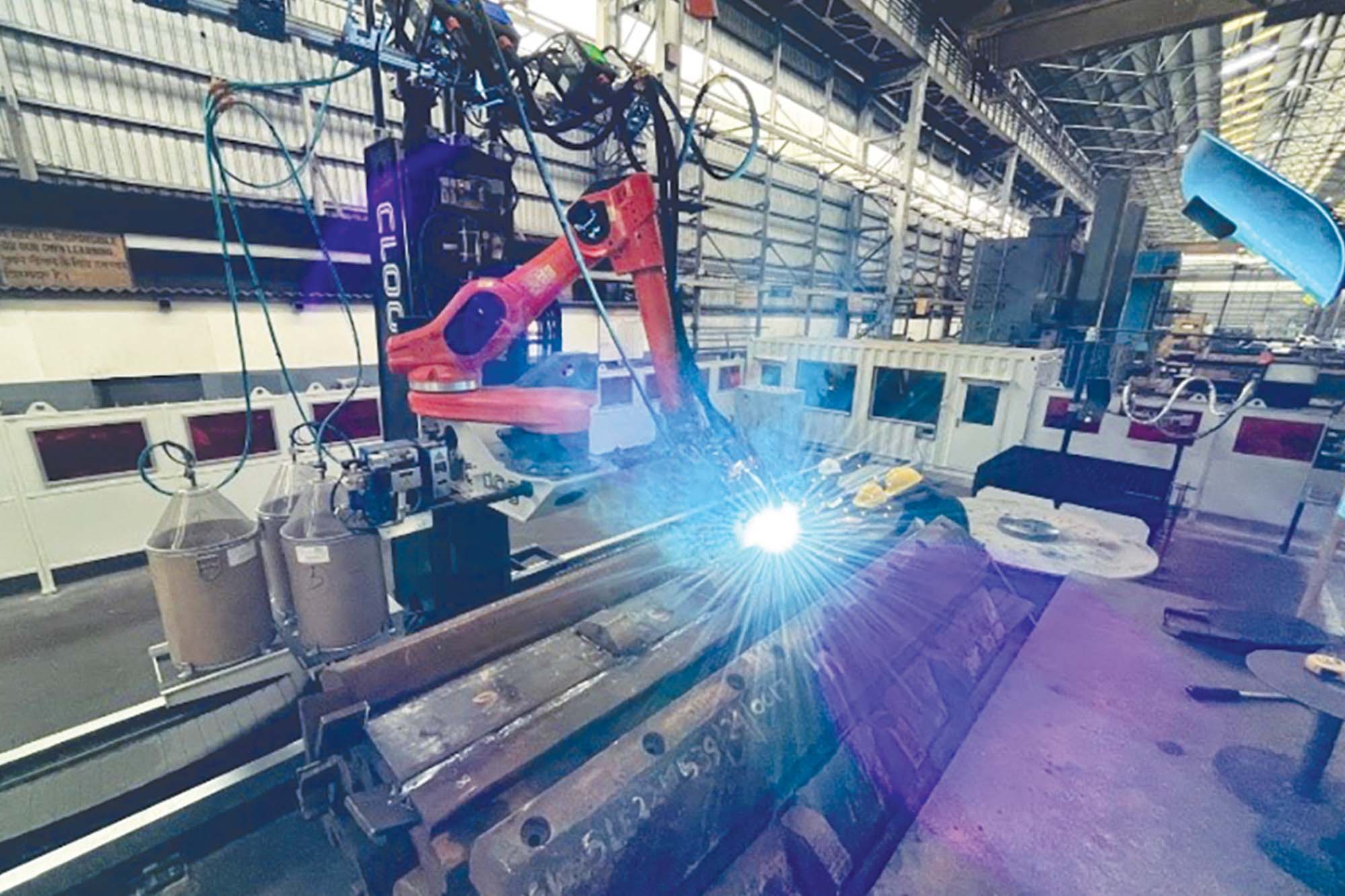
Transformer tank welding at Crompton Greaves
CLOOS successfully installed a Robotic welding solution for Transformer welding at Crompton Greaves. Cloos has already provided numerous robotic welding solutions for the transformer industry for a long time. To weld transformer tanks, Crompton Greaves relies on the know-how and expertise of Carl Cloos Schweisstechnik GmbH. The new welding system is nearly 22 m long and consists of two stations and a Cloos 7-axis robot, type QIROX QRC-410-E. It allows flexible processing of the different component types. This increases the efficiency and quality of the hall production.
If you want to change your existing process of Transformer tank subassembly and full assembly welding, then rely on CLOOS’s excellent welding technology and customised Robotic welding solution, based on their 105 years of experience!
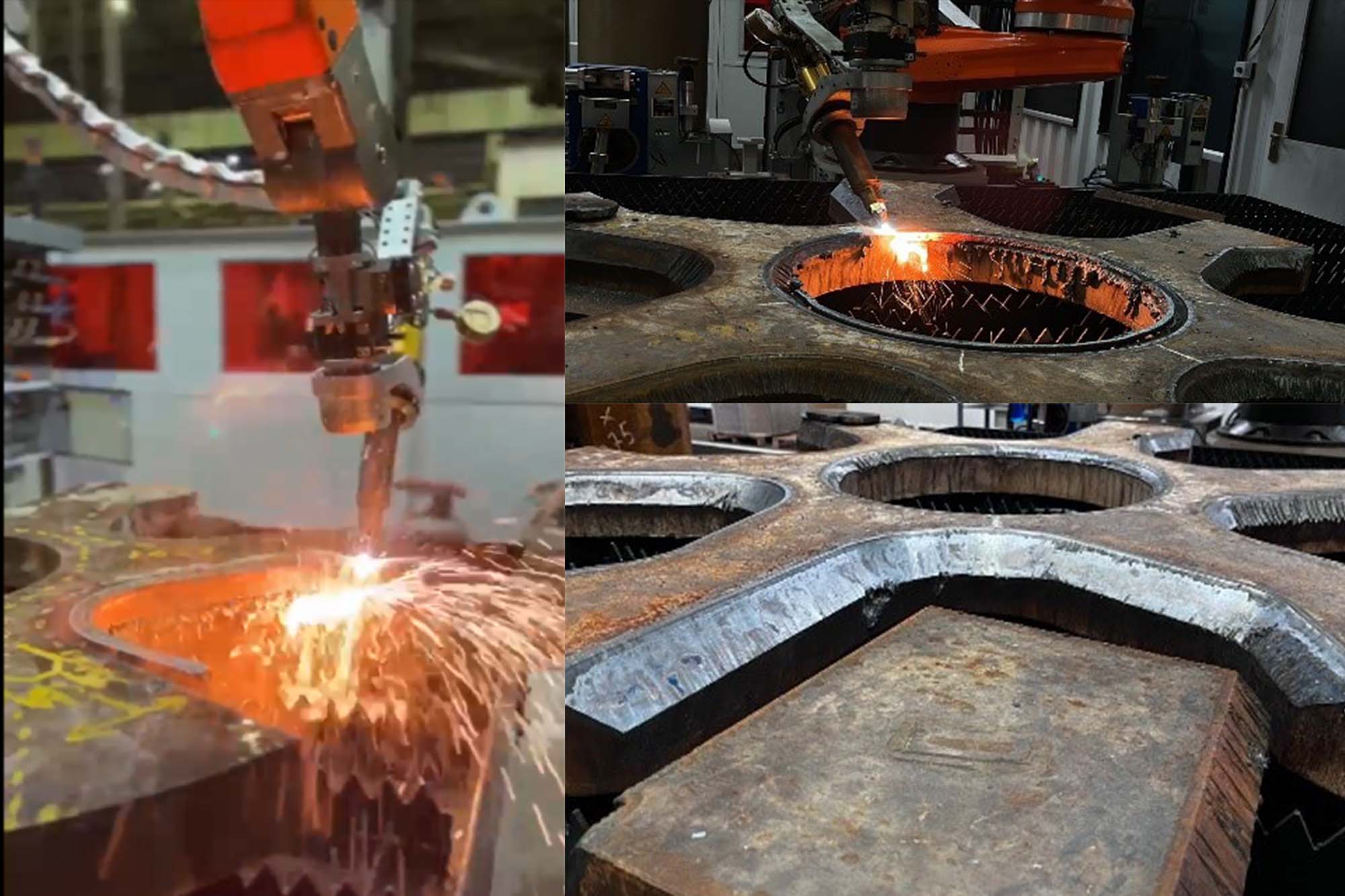
Speed Weld
CLOOS stable all-round Innovative welding process Speed Weld completely changed Recent success stories of CLOOS India CLOOS’s customised single-source welding technology solution has been redefining the welding industry for a decade. Sumon Mitra, COO of Cloos India Welding Technology, affirms that CLOOS is at the forefront of innovation with its comprehensive solutions. Sumon Mitra COO, Cloos India Welding TechnologyPvt. Ltd. ADVERTORIAL September 2024 n 53 welding quality in the many sectors’ low- or high-capacity range. Speed welding is used in all sectors of metal machining. The voltagecontrolled MIG/MAG pulsed arc process allows a very high arc pressure even under demanding conditions. With Speed Weld, you can achieve high welding speeds because of the powerful arc. It bestows the excellent weld quality due to the deep penetration. Users can avoid extensive reworks as spatters and undercuts are minimal.
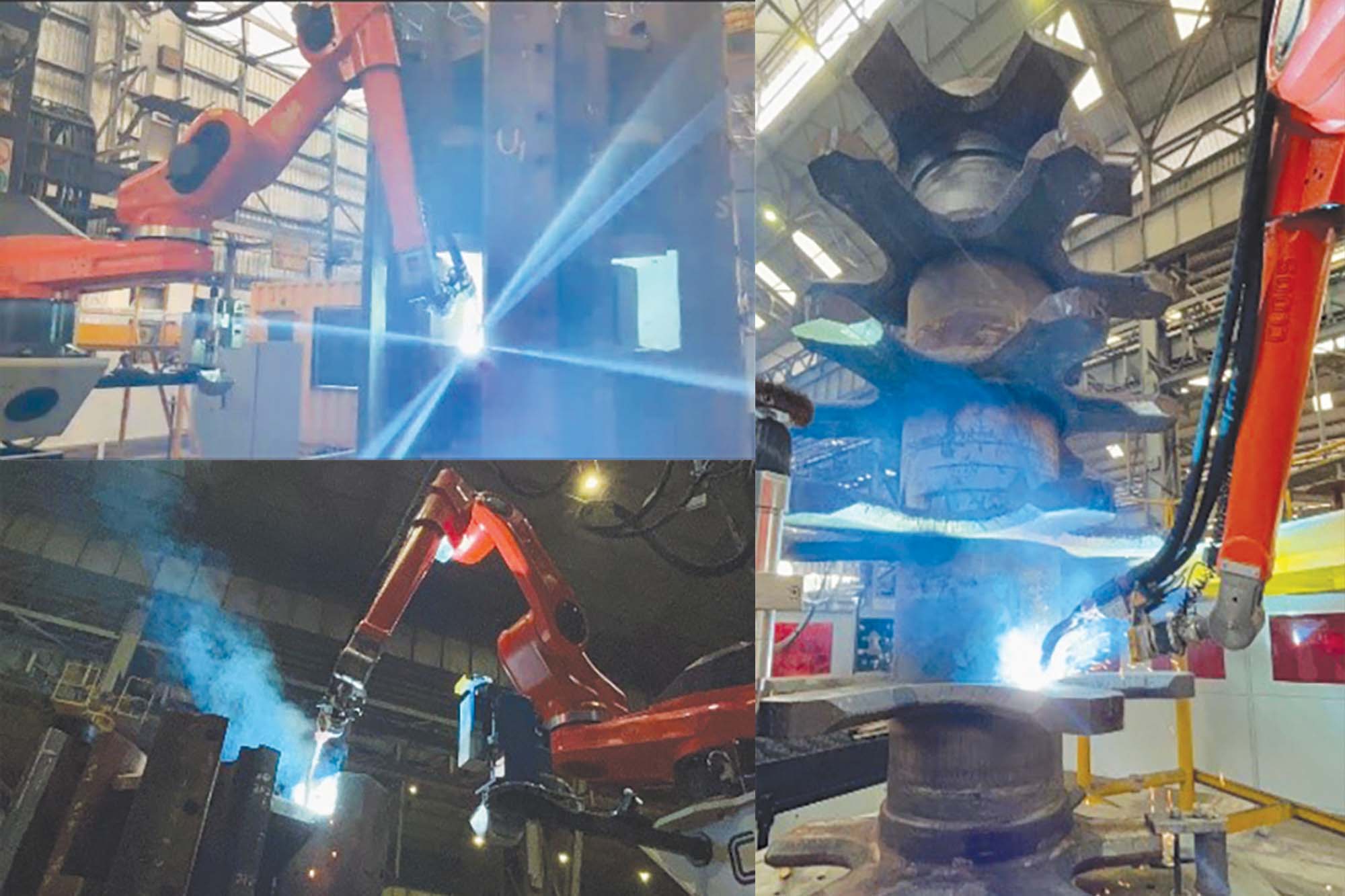
Benefits:
High welding speeds due to the powerful arcExcellent welding quality because of a deep penetration
Reduced rework thanks to the pulsed arc technology with regulated drop separation
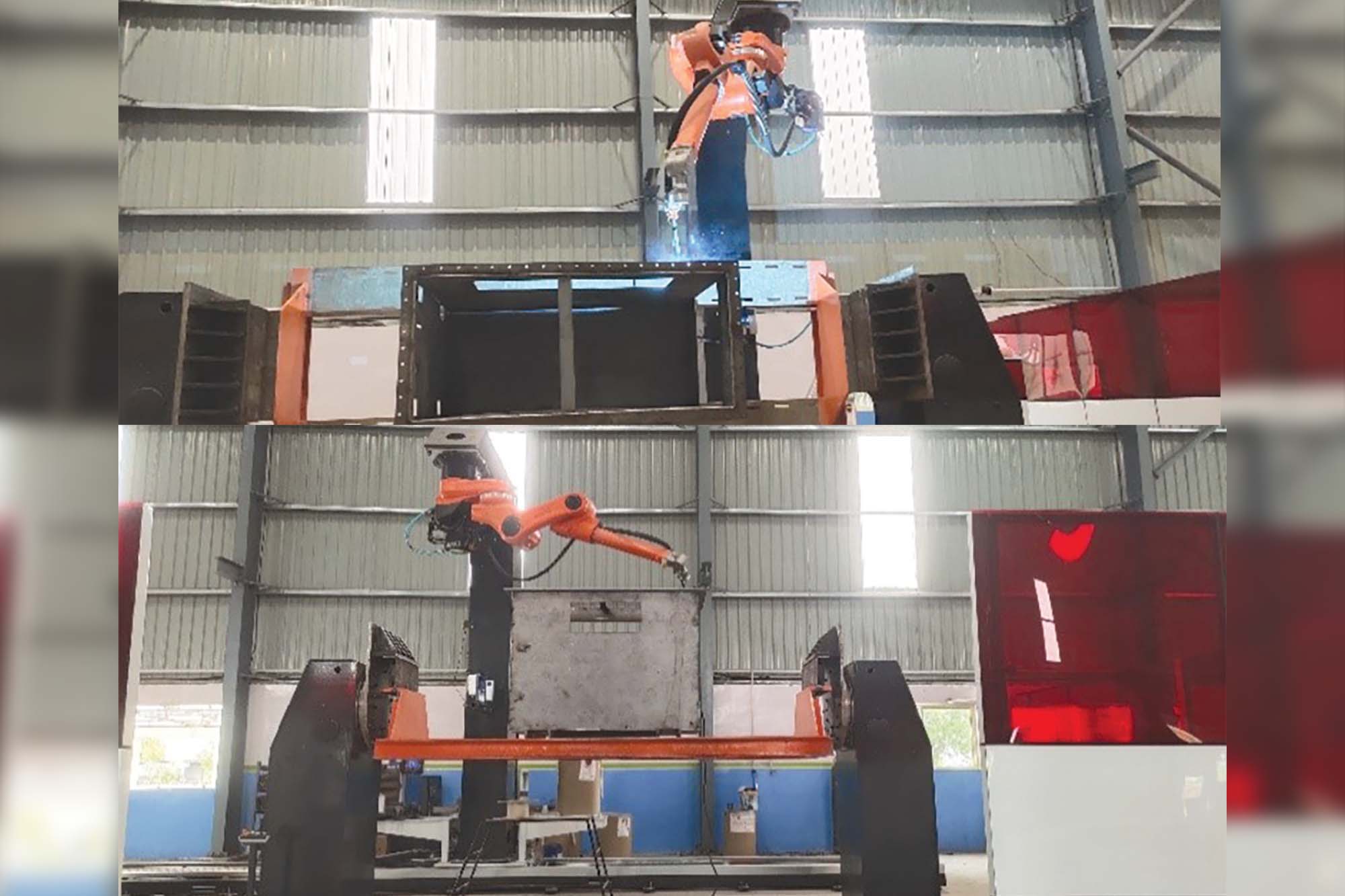
The benefit of CLOOS Arc Seam Tracking
During welding, the sensor precisely checks the torch position relative to the programmed path. This enables automated adjustment in the event of any deviations to ensure consistent, high-quality welding. Time loss is minimised because measuring and welding happen simultaneously with the arc sensor. At the same time, workpiece distortion, e.g. due to thermal expansion, is directly compensated for. The CLOOS arc sensor thus combines productivity with optimised quality.
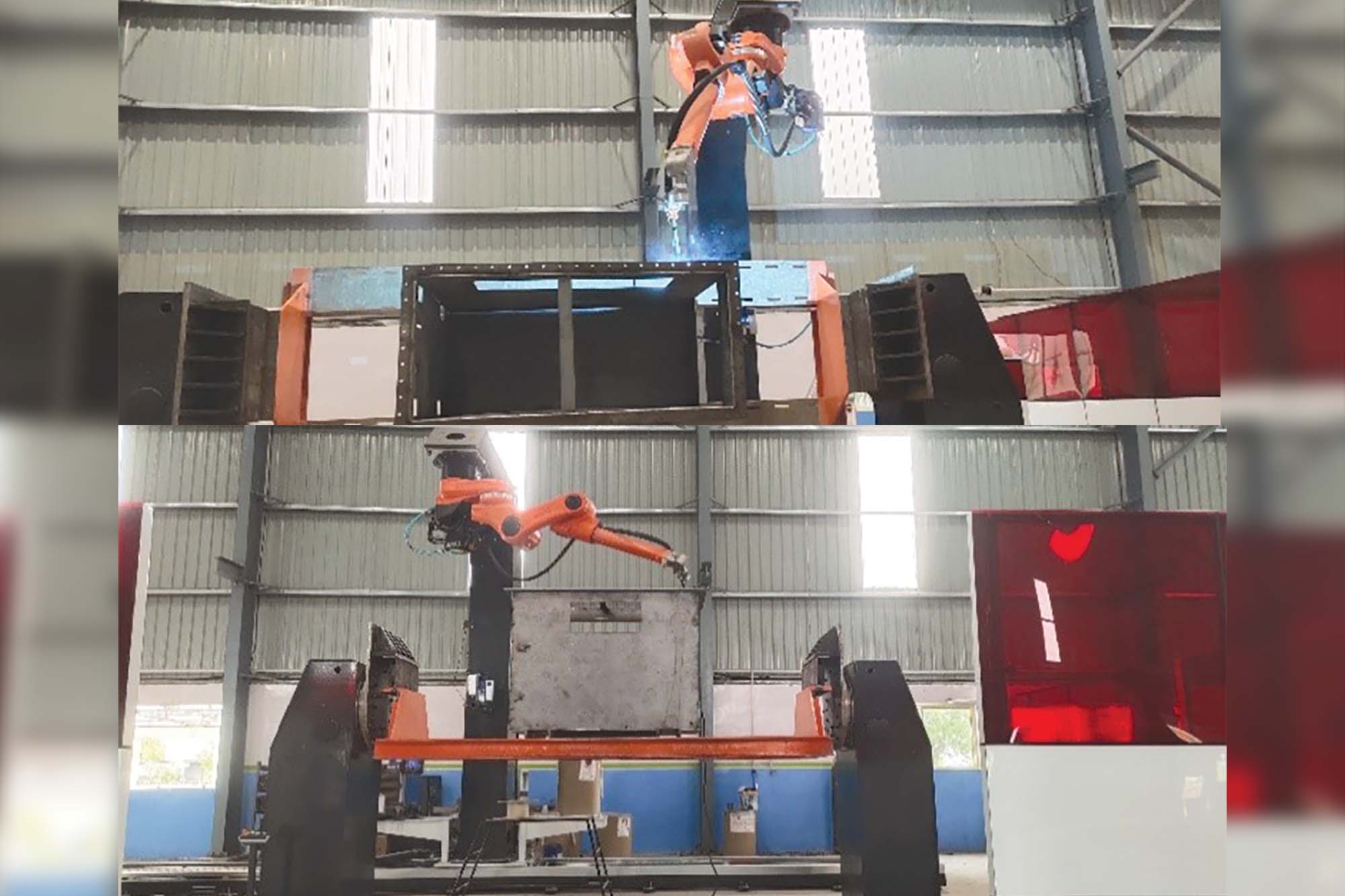
First Robotic welding system in the Indian shipping industry
GRSE trusted CLOOS and installed the first Robotic welding system in the Indian shipping industry. CLOOS’ offline Roboplan software overcomes the challenge of nonrepetitive ship panel welding. Using the TEACH process is less time-consuming than generating a new program in the robot system. As a result, system utilisation is increased, the production process is optimised, and welding production becomes more flexible.
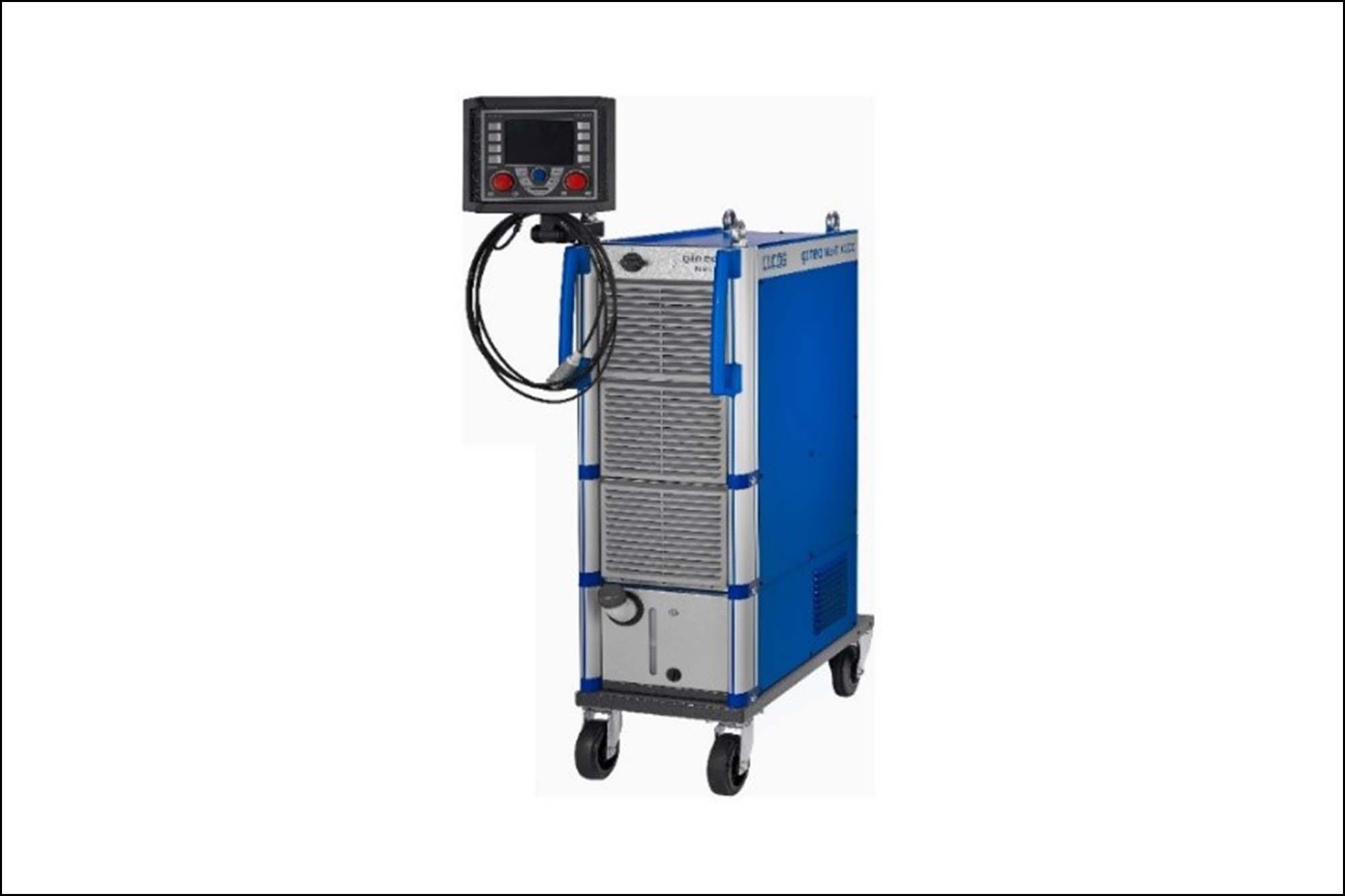
For manual and robotic welding
CLOOS welding machine for manual and robotic welding with numerous processes per the demand of various industries. The QINEO NexT Premium has all important components and functions” on board,” so you are prepared for the future. The heart of the QINEO NexT is an inverter power unit developed by CLOOS that clocks at high frequency. This allows for even better arc control and excellent results. The unique welding characteristics enable you to solve complex welding tasks perfectly. Many optional components and functions make the QINEO NexT your power source in the way required for automated and manual welding.
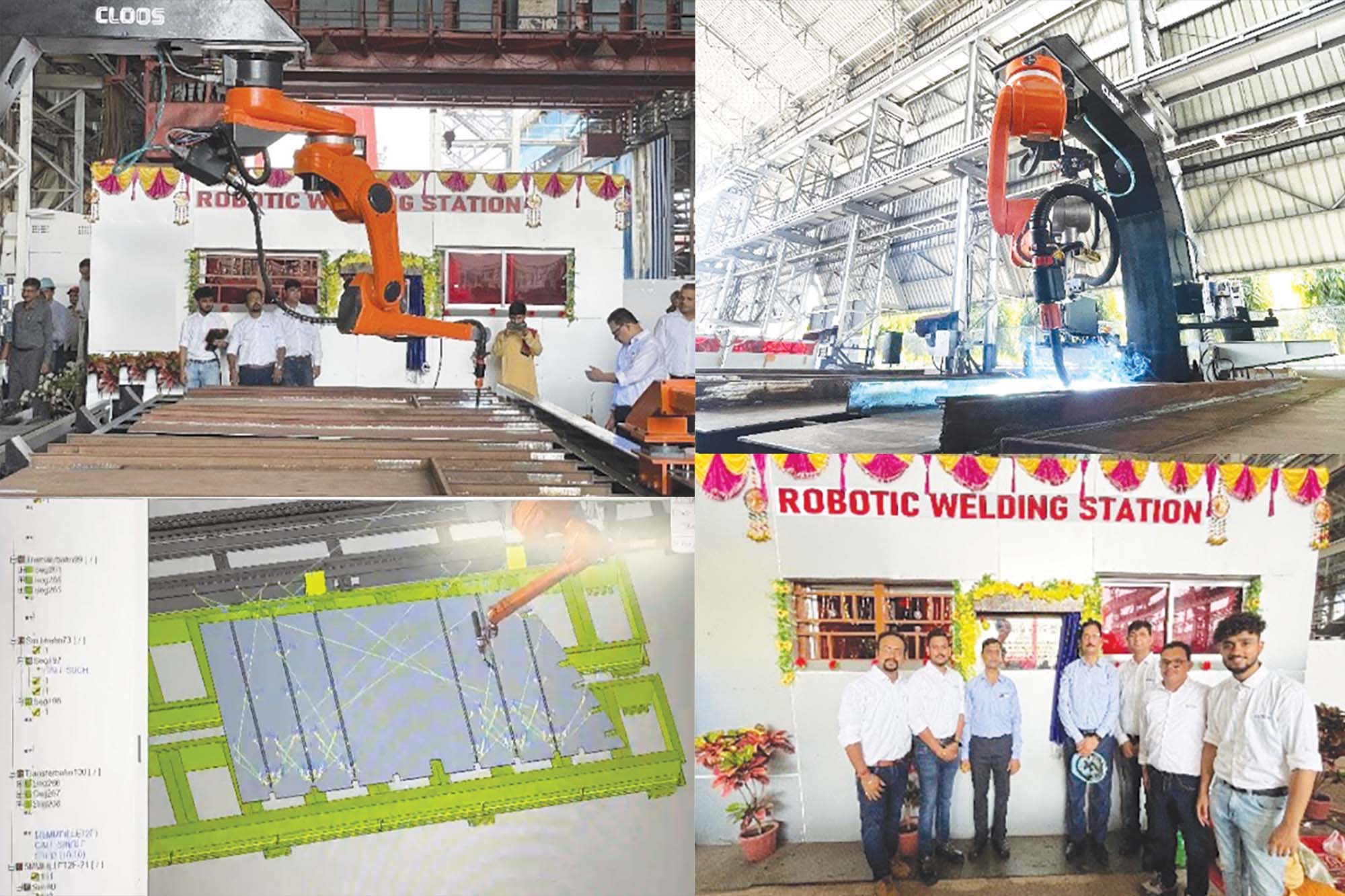
Contact:
Cloos India Welding Technology Private Limited
Ground & 1st Floor,Plot No. 114/1/3,General
Block, Midc Bhosari, Pune, Maharashtra
411026 India
Website:- www.cloos.de
Email :- contact@cloos.in,
Mobile:-7003545907 / 9168383939
Cookie Consent
We use cookies to personalize your experience. By continuing to visit this website you agree to our Terms & Conditions, Privacy Policy and Cookie Policy.