Scanning the CNC systems to choose the best
By Staff Report January 16, 2025 12:00 pm IST
Autonomous CNC systems have influenced manufacturing by using AI and machine learning technologies. These technologies improve precision and accuracy, producing intricate components with minimal errors and increasing efficiency and productivity. We learn more about the CNC and how it impacts the manufacturing network.
—————————————————————————————
A waterjet is used to cut stones and metals. This task is aided by CNC (Computer Numerical Control), a manufacturing process that uses pre-programmed software to control machinery and tools. CNC controls the machines to deliver precision in many industries, including healthcare, jewellery, woodworking, and more.
CNC machines come in various options, including mills, routers, plasma cutting machines, lathes, laser cutters, water-jet cutters, electrical discharge machines (EDM), grinders, bending machines, drilling machines, robots, and 3D Printers.
The decision to opt for CNC machining depends on various factors, including the type of material, part complexity, production volume, and the desired finish quality. CNC machining is often preferred for producing high-precision parts from various materials, including metals, and is ideal for high-volume production. Mukul Gupta, General Manager – Technical Support & After Sales Machines, LGF Sysmac India Pvt. Ltd. shares that selecting the appropriate material is important, according to its intended use and mechanical property requirements that ease the manufacturing. The fabrication design of parts can be complex due to sharp corners and non-planar surfaces, making it beneficial to try encapsulating most features within a 2D surface. Tolerances and precision interface components have to be designed to withstand specified tolerances and precision that enable the proper functioning of components.
The construction of parts should enable the cutting tool to reach the required points without excessive setup and long machining time. The design should be optimised to conserve material and machining time, thereby reducing the manufacturing cost.
Cost-technological balance is essential.
The balance is the equilibrium. Parth Parmar, Sr. Technical Manager, Divine Engineering, shares that they achieved cost-technology equilibrium through early participation of multidisciplinary skills, life-cycle cost analysis (LCA), and optimised selection of materials based on sustainability, cost, performance, and innovative practices at Divine Engineering. These methods ensure all design areas are merged well for optimal cost and technology. The project’s decisions are made with an appropriate cost-to-technology ratio for cost-effectiveness while using advanced technology. Innovative practices also involve utilising the latest technologies and methodologies to improve design processes and minimise waste.
Mukul Gupta, General Manager – Technical Support & After Sales Machines, LGF Sysmac India Pvt. Ltd., shares that balancing cost and technology optimises production efficiency. Manufacturers can achieve this by evaluating the total cost of ownership (TCO) for CNC machining and 3D printing. This involves considering initial investment costs, operational expenses, material costs, and time to market. To follow this balance, it is essential to choose the right equipment for the job, adopt lean manufacturing practices, and leverage automation to reduce operational costs. Additionally, strategic investments in technology that offer flexibility and scalability can ensure that the technological advancements are aligned with budgetary constraints, allowing for greater profitability and competitiveness.
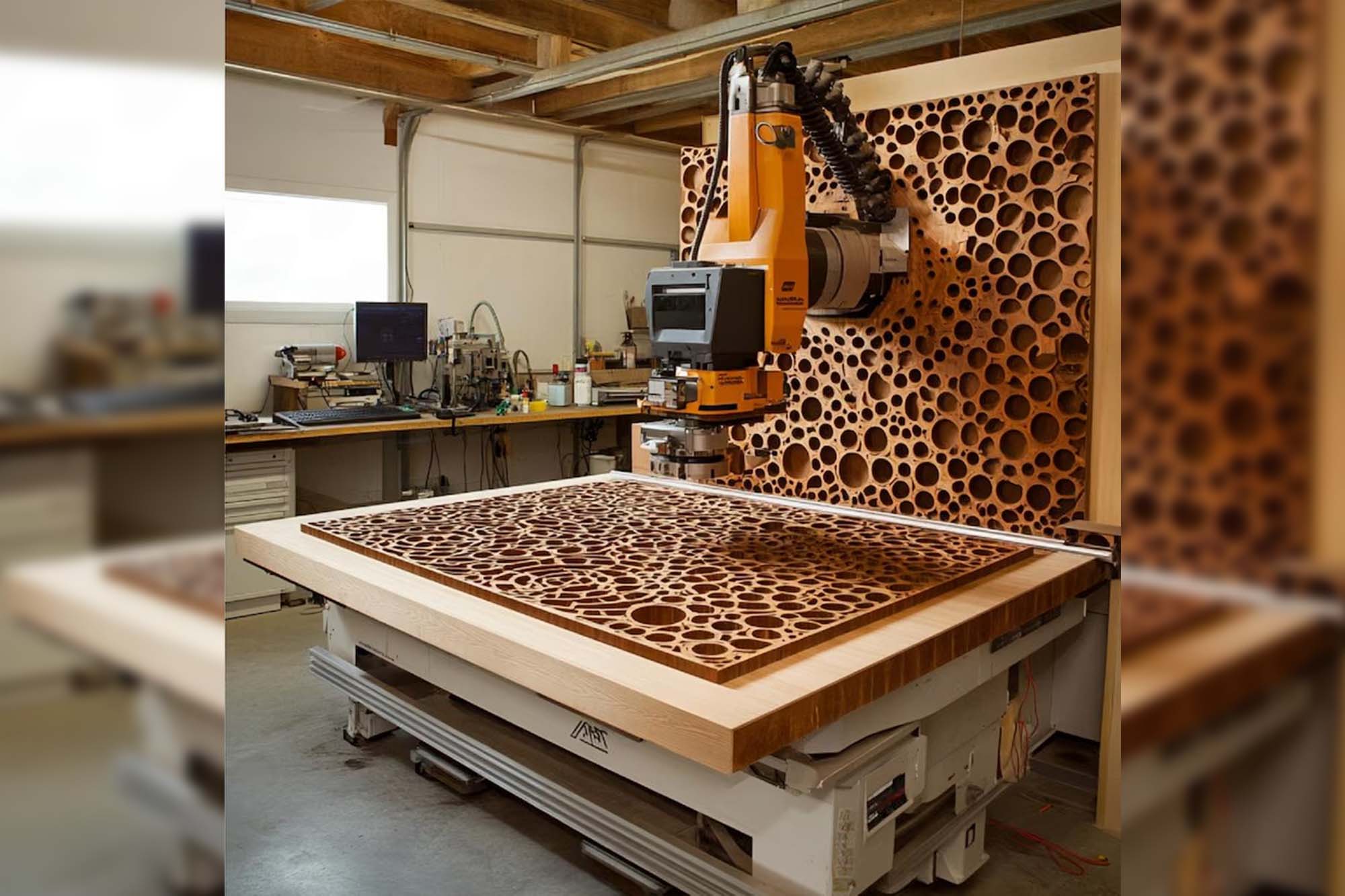
AI and machine learning
The future of CNC machining is moving towards greater automation and autonomy through AI and machine learning. Autonomous CNC systems are expected to become more adaptive and intelligent, with the ability to optimise machining parameters in real-time based on input from sensors and machine learning algorithms. These systems could detect and correct errors during production, adjust tooling and settings automatically, and predict maintenance needs to prevent downtime. In the long term, this would allow for continuous improvement in precision, reduce human error, and improve overall machine uptime and efficiency.
AI and machine learning technologies improve precision and accuracy, enabling the production of intricate components with minimal errors and increased efficiency and productivity. AI-driven automation reduces downtime, optimises tool usage, and accelerates machining processes. By integrating adaptive algorithms into CNC systems, we can deliver consistent results while minimising waste, making them indispensable for modern manufacturing needs.
AI-powered systems can continuously monitor and analyse production data to identify bottlenecks and inefficiencies. By making real-time adjustments to process parameters, AI can improve overall efficiency and productivity, and AI-enabled CNC machines can adapt to changing conditions, such as variations in material properties or tool wear, ensuring consistent output quality and maximising throughput. AI-powered automation reduces the need for human intervention in routine tasks, freeing up skilled workers to focus on more complex and strategic activities.
CAD/CAM systemsComputer-aided design (CAD) software allows engineers to create precise 3D models of parts, ensuring accuracy and visualising the final product. CAD tools enable designers to optimise part designs for manufacturability, reducing material waste and machining time. CAD models can also be used to create digital prototypes for early design validation and testing.
Computer-aided manufacturing (CAM) software automatically generates tool paths, defining the precise movements of the CNC machine’s cutting tool to machine parts. CAM systems offer a variety of machining strategies, such as roughing, finishing, drilling, and milling, to optimise the machining process based on part geometry and material properties. We recommend network segmentation, strict access control policies, and regular firmware and software updates to power cybersecurity innovations.
John Xu, General Manager of Jiantong Hardware Manufacturing Co., Ltd., thinks that the design-to-production process converts the digital design into machine-able G-code instructions for CNC machines, using CAD software engineered the Excel standards and serves as the foundation for the CNC machining process. Toolpath optimisation involves developing efficient machining strategies to reduce material waste and cycle time, utilising CAM software for optimal material removal and waste reduction. Simulation provides virtual previews of machining processes to detect errors before production. These simulations help to detect potential errors, collisions, or inefficiencies in the toolpath by reducing the risk of mistakes. By validating the machining process, operators ensure quality and accuracy in production. Customisability allows precise adjustments to match machine capabilities and material properties, enhancing efficiency and consistency across multiple production runs. In short, CAD/CAM systems are indispensable for modern CNC programming and setup, bridging the gap between design and manufacturing while improving efficiency, accuracy, and flexibility.
Cybersecurity innovations
With the growing connectivity of CNC machines, cybersecurity has become a critical concern. To safeguard networked CNCs, manufacturers should implement multi-layered security measures, such as robust firewalls, encryption protocols, and regular software updates to protect against external threats. Further, employing intrusion detection systems (IDS) and access control mechanisms can ensure that only authorised personnel can interact with the CNC systems. Manufacturers should also consider segmenting their networks to limit exposure and prevent the spread of potential breaches. Investing in cybersecurity innovations, such as AI-powered threat detection, can further enhance the protection of networked CNC machines.
Parth Parmar suggests Network Segmentation, as it can physically or logically isolate CNC networks to create a separate network segment for CNC machines to limit potential attack vectors. He suggests that users can implement strict access control policies, restricting access to authorised personnel only and using network monitoring tools to detect and respond to suspicious activity.
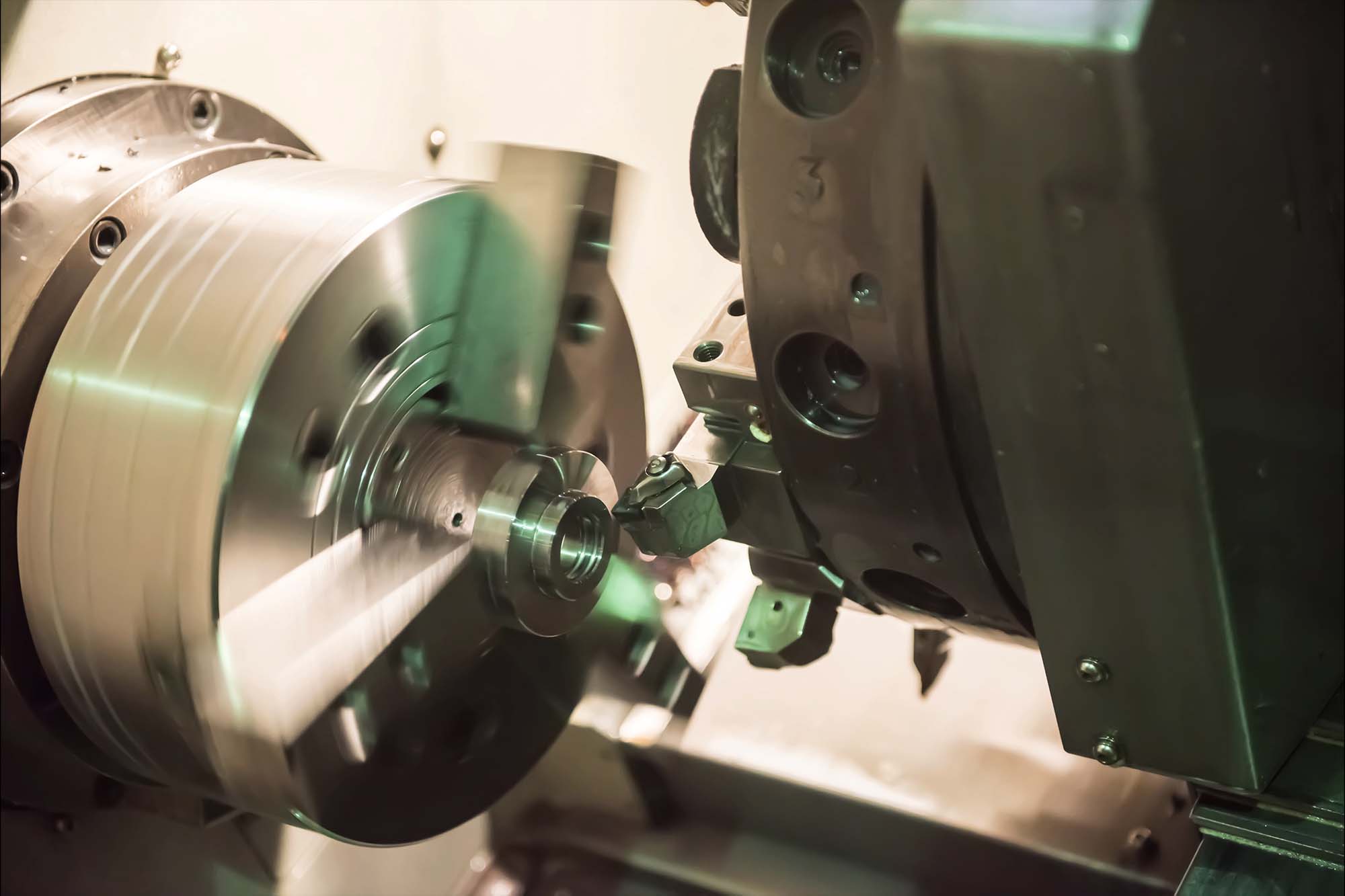
Hardware and software security are important for maintaining the integrity of CNC machines. Regularly updating firmware and software helps address vulnerabilities and deliver optimal performance. Strengthening security can be achieved by changing default passwords and configurations, as these are often targets for unauthorised access. Implementing strong password policies for all user accounts further enhances protection. Additionally, promptly applying security patches mitigates known vulnerabilities and reduces potential risks, safeguarding the hardware and software from threats.
CNC systems combine with AI, machine learning, and CAD/CAM to smoothen the manufacturing process with enhanced precision, efficiency, and adaptability. These innovations are empowering manufacturers to meet modern demands that are smarter and more efficient, although prone to cyber risks.
—————————————————————————
Parth Parmar, Sr. Technical Manager, Divine Engineering
“CAD/CAM are important in CNC programming and setup. Computer-aided design (CAD) software allows engineers to create precise 3D models of parts, ensuring accuracy and visualising the final product. CAM software automatically generates tool paths, defining the precise movements of the CNC machine’s cutting tool to machine parts.”
Mukul Gupta, General Manager – Technical Support & After Sales Machines, LGF Sysmac India Pvt. Ltd.
“CNC machining is ideal for high-volume production and producing high-precision parts from various materials, while 3D printing offers rapid prototyping and complex geometries advantages.”
John Xu, General Manager, Jiantong Hardware Manufacturing Co., Ltd.
“Manufacturers can achieve a cost-technological balance by optimising production processes through CNC machining and 3D printing technologies.”
Cookie Consent
We use cookies to personalize your experience. By continuing to visit this website you agree to our Terms & Conditions, Privacy Policy and Cookie Policy.