Virtual meets reality
By Staff Report January 9, 2025 7:01 pm IST
Digital twins create virtual replicas of physical systems, enabling manufacturers to simulate production before real-world implementation. This shift is characterised by data, automation, and connectivity to production. Sebastian Telégin, an AI expert, shares the transformation of the manufacturing industry due to the Industry 4.0 digital revolution.
The manufacturing industry is transforming due to the Industry 4.0 digital revolution. This shift is characterised by the increasing integration of data, automation, and connectivity into production. Manufacturers increasingly prioritise data-driven decision-making to enhance operations, improve efficiency, and maintain a competitive edge.
In 2015, manufacturing firms were navigating a maze of manual processes, paper trails, and gut-feeling decision-making, with efficiency and quality control often feeling like catching fire with bare hands. Today, the landscape has dramatically changed. Industry 4.0 has ushered in an era where data is the new oil, and connectivity is the pipeline that fuels operations. However, data requires careful analysis and context to transform into actionable insights driving value.
The technologies reshaping manufacturing
AI: The brain of modern manufacturing
Artificial intelligence (AI) is restructuring industries by providing predictive maintenance and quality assurance, making it an unsung hero of modern industry. For example, AI-driven systems implemented by Siemens and GE predict equipment failures with remarkable accuracy. Maintenance costs and downtime have been reduced by up to 37% in some cases.
AI does not replace human expertise but enhances it, allowing teams to tackle complex challenges while autonomously handling routine predictions.
IoT: The nervous system of the smart factory
The Internet of Things (IoT) connects machines, products, and even workers in an expansive data network. IoT is improving efficiency by transforming the responsiveness of manufacturing systems. For example, at Siemens’ Amberg plant, IoT sensors detect anomalies such as temperature fluctuations in assembly lines. These real-time alerts prevent defects that could lead to costly recalls, saving millions annually.
Digital twins: The mirror world
Digital twins create virtual replicas of physical systems, enabling manufacturers to simulate and optimise production before real-world implementation. For example, Rolls-Royce uses digital twins in its Engine Health Management system to monitor and predict potential issues in aircraft engines, enhancing safety and reducing downtime.Digital twins are distinct solutions that can be categorised into four types: component twins, asset twins, system unit twins, and process twins, each based on the complexity and scope of the physical entity they represent.
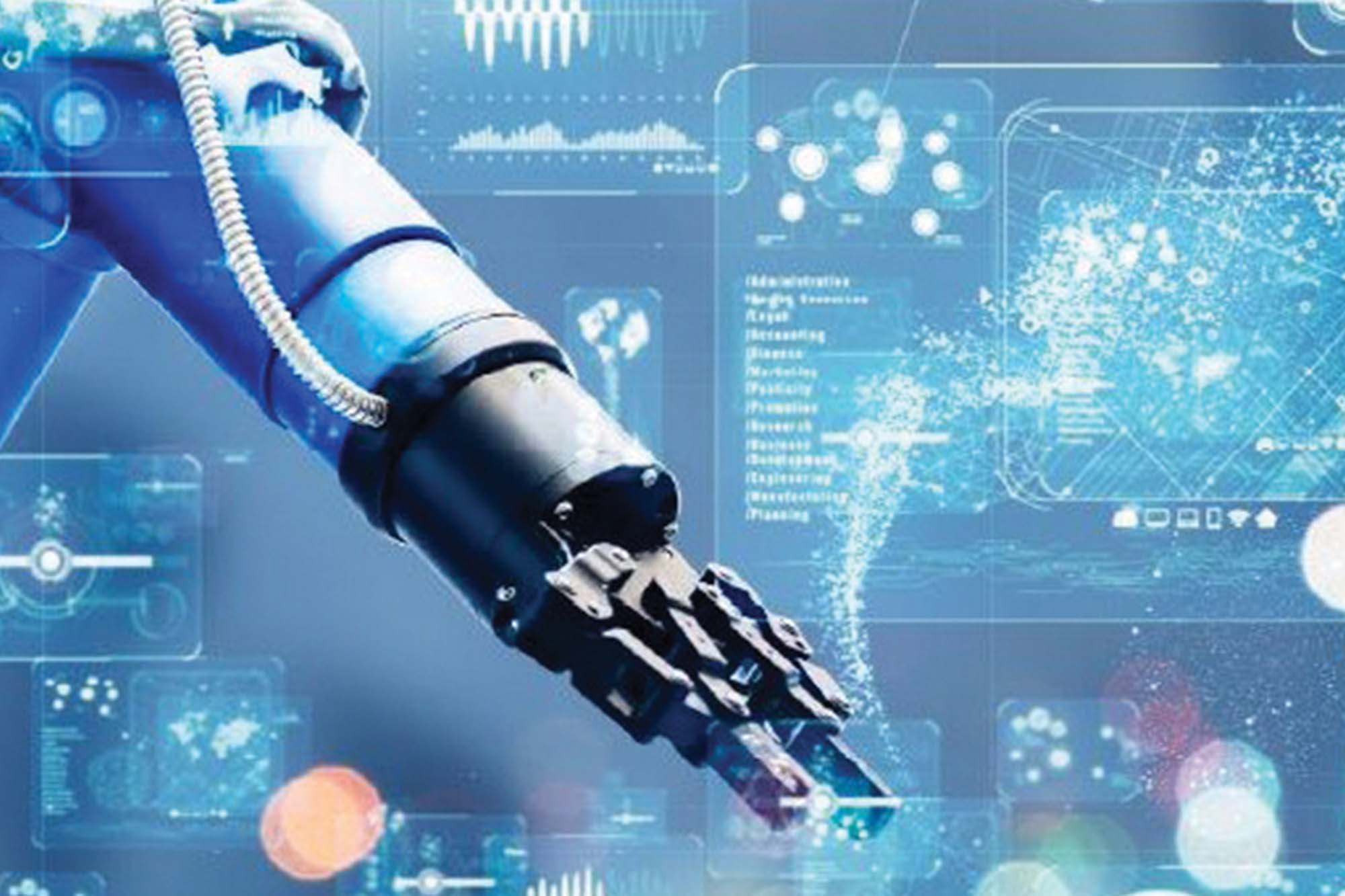
Similarly, Tesla’s Gigafactory leverages digital twins for process simulation, achieving automation rates of approximately 95%. This allows cars to roll off the assembly line every 40 seconds, setting a global benchmark for smart manufacturing.
Real stories of transformation
Rolls-Royce’s Engine Health Management system predicts maintenance issues before they occur, resulting in cost savings and enhanced safety.
Siemens’ Amberg plant, with over 75% automation and reliance on digital twins, the plant exemplifies how data-driven insights drive continuous improvement.
Small and Medium Enterprises (SMEs), a Midwest-based family business, implemented smart sensors and analytics, enabling them to compete against much larger competitors. Industry 4.0 is not exclusive to large manufacturing corporations.
The human element
Digital technologies have converted the fear of job displacement into a recognition of new opportunities for workers. Workers like Sarah—a long-time machine operator at a European manufacturing plant—initially resisted digital systems but soon became advocates. “It’s like having a superpower,” she said, referring to her newfound ability to predict machine issues before they come.
As we progress, the pace of change is not showing any signs of slowing down. Success in this new era requires more than just implementing technology—it demands a cultural shift toward adaptability and lifelong learning. The future of manufacturing is digital, and it’s rewriting what’s possible.
Cookie Consent
We use cookies to personalize your experience. By continuing to visit this website you agree to our Terms & Conditions, Privacy Policy and Cookie Policy.