MMC Hardmetal advanced materials resist heat, wear, and erosion
By Staff Report January 2, 2025 11:16 am IST
MMC Hardmetal is a leading provider of cutting tools and integrated solutions, serving diverse industries with precision and expertise. Renowned for its innovation and reliability, MMC Hardmetal has earned its reputation as a trusted partner in delivering exceptional results. Prashant Sardeshmukh, managing director of MMC Hardmetal India Pvt Ltd, shares insights with OEM Update into their cutting-edge R&D processes, designed to enhance the performance and extend the lifespan of their cutting tools.
What new materials is MMC Hardmetal using to enhance the performance and lifespan of cutting tools?
There have been many advancements in metallurgy in recent times. As a part of our R&D initiative, we always focus on developing new materials that can withstand high temperatures, wear and erosion without compromising sharpness and precision. To improve the cutting tools’ performance, efficiency and longevity, we constantly research and use super-hard materials like PCD and CBN, new alloys, cemented carbides, composites and coatings for machining difficult-to-cut materials.
How do advanced tool geometries contribute to reducing machining time?
Advanced tool geometries play a significant role in reducing machining time. They improve cutting efficiency and contribute to faster and better chip removal. They also help reduce tool wear and improve the overall efficiency of the machining.
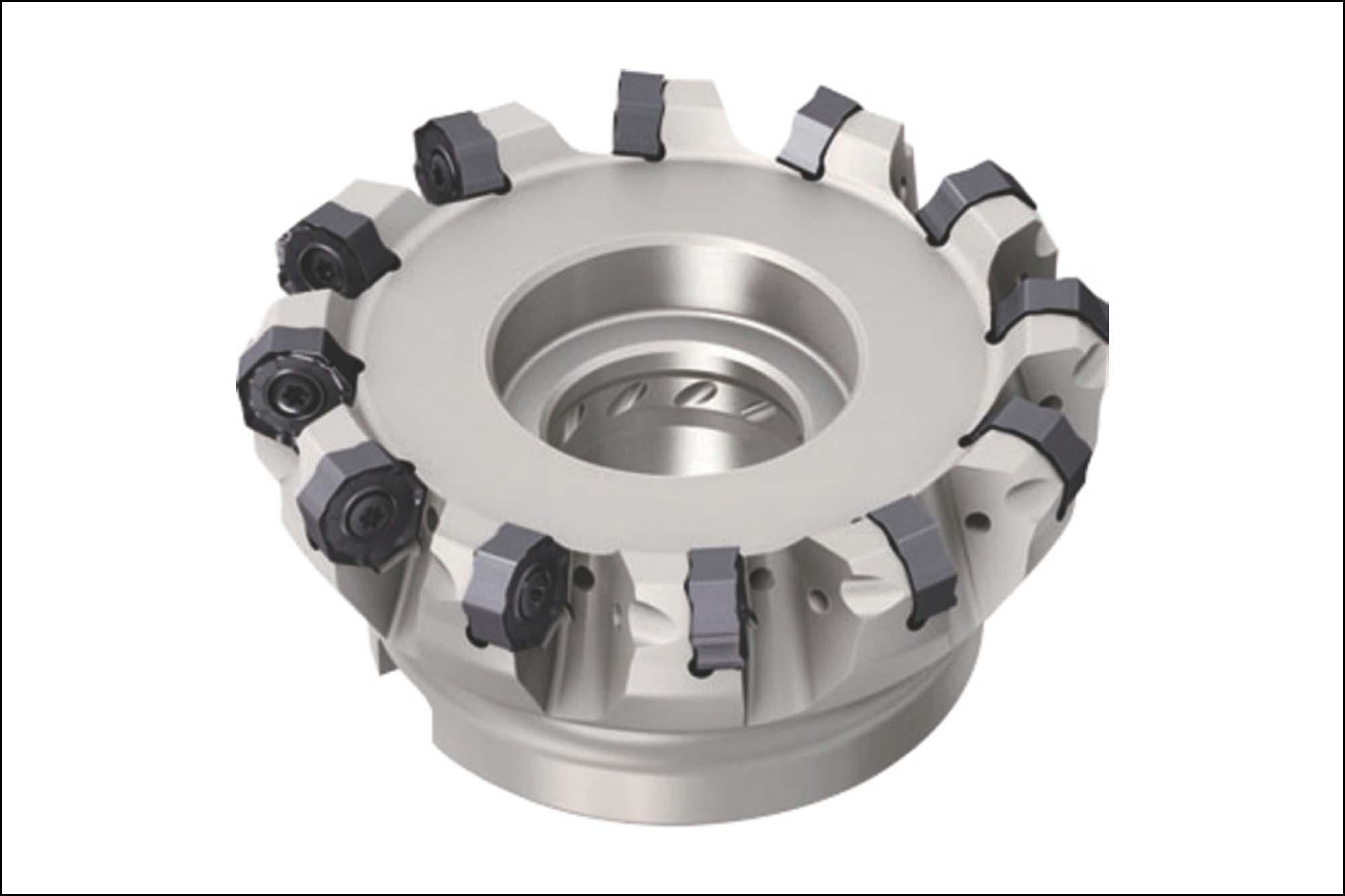
Advanced geometries help us achieve more precise and sharper cutting edges with optimised cutting angles. This innovation reduces cutting resistance, allowing the tool to penetrate the work material effortlessly. Improved machining time not only enhances efficiency but also helps reduce energy consumption. Additionally, the stability in cutting conditions ensures consistent cutting quality and speeds throughout the process.
What cooling techniques are used by MMC Hardmetal to improve tool life and reduce wear?
Several cooling techniques are involved to improve tool life and overall machining performance. They also reduce friction between the tool, workpiece and tool wear.
I can highlight techniques like Minimum Quantity Lubrication, a high-pressure coolant system for heat dissipation and efficient chip removal. There are internal coolant channels in tools. Certain tools like drills, end mills and inserts are designed to have internal coolant passages, which helps with the direct flow of the coolant to the cutting edge. This system can be useful for certain machining operations like deep-hole drilling and high-precision cutting. There are other techniques, such as cryogenic cooling, which involves liquid nitrogen, flood cooling with advanced fluids, nano-fluid-based coolants, and so on.
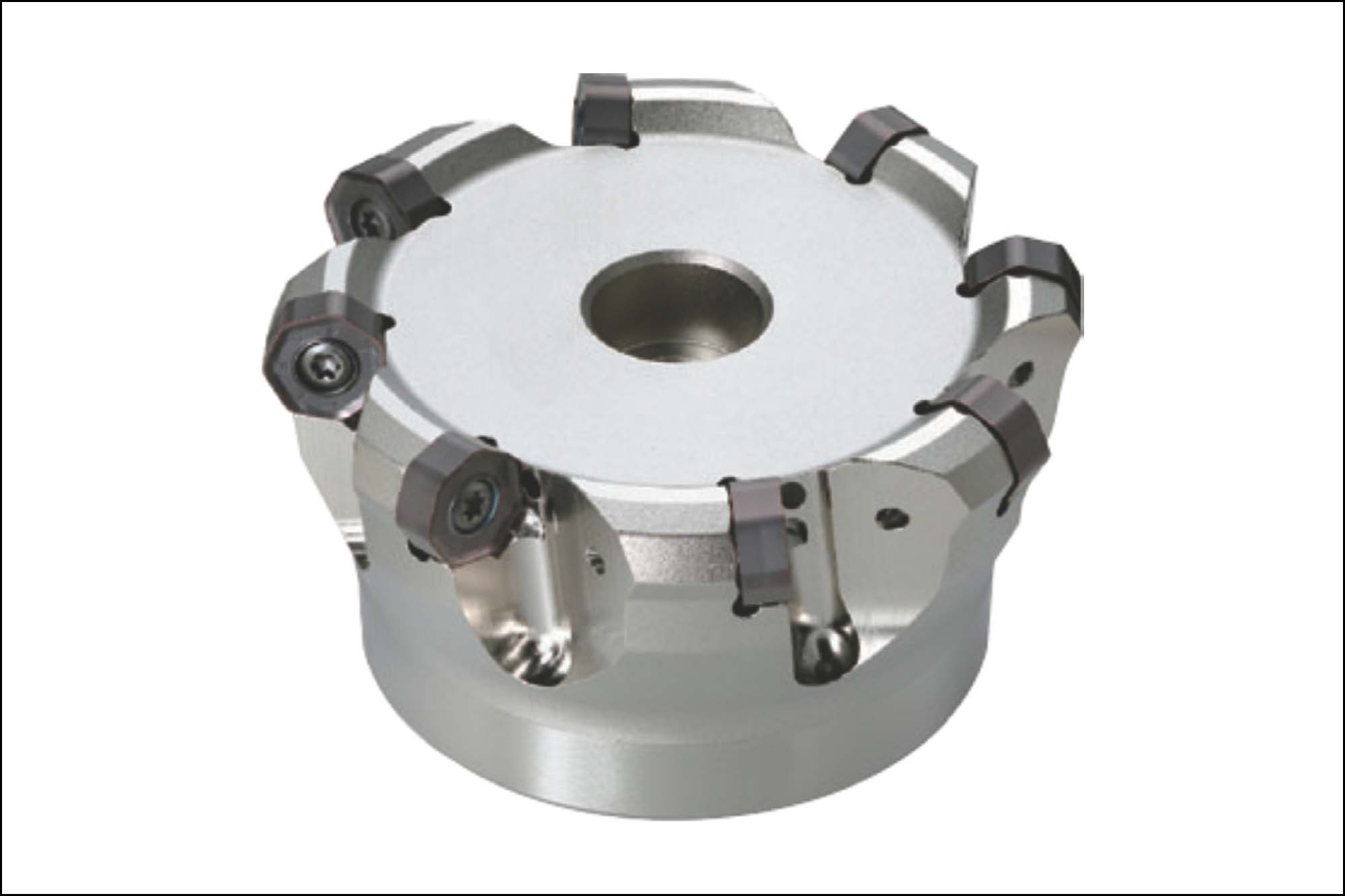
What advantages do superhard materials like CBN and PCD offer over traditional cutting tools in terms of wear resistance?
Materials like CBN and PCD are called super hard because they offer superior resistance compared to traditional cutting tool materials. Due to their hardness, thermal stability, and chemical resistance ability, we can consistently achieve cutting performance under extreme conditions. These attributes give them an edge over traditional materials, especially when it comes to high precision, improved performance, and high-speed machining processes.
How is nano-coating technology enhancing tool life and improving high-speed machining (HSM) performance?
Factors like high temperatures, cutting forces and material properties can affect the tool life and lower the performance in high-speed machining. Nano-coating technology satisfactorily addresses these issues. It enhances wear resistance, improves thermal stability and reduces friction. As a result, we get longer tool life. This ultimately leads to better machining efficiency vis-a-vis less downtime and cost savings. Therefore, nano-coating technology has become very popular and dependable for optimum performance in High-speed machining.
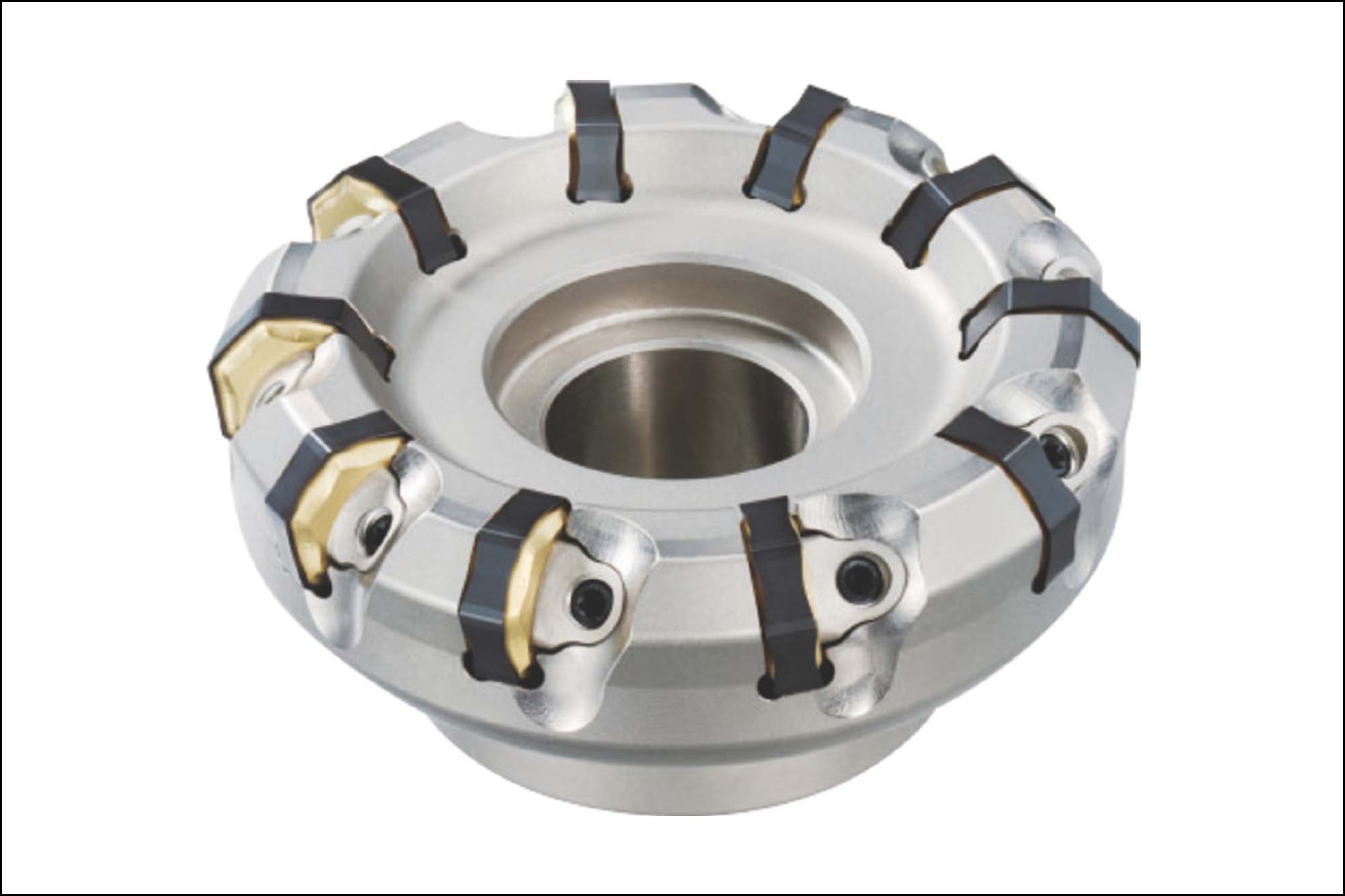
How are AI, ML, and IoT integrated into cutting tool management and monitoring systems at the MMC Hardmetal unit?
We use advanced technologies like AI, ML and IoT integrated to enhance efficiency, optimise performance and facilitate proper predictive maintenance in cutting operations. For example, AI is used and integrated for predictive analysis of tool data, machining performance data etc. It is also used to control cutting parameters, improve cutting performance and accomplish other things. ML or Machine Learning is used to detect tool wear, assess deviations, irregularities or abnormalities, and monitor the condition of cutting tools by data analysis. IoT comes into play in the case of real-time data collection and its analysis. It is also used for remote monitoring and to have smart tooling systems.
What role does IMTEX 2025 play in driving global collaborations and market expansion for cutting tool builders?
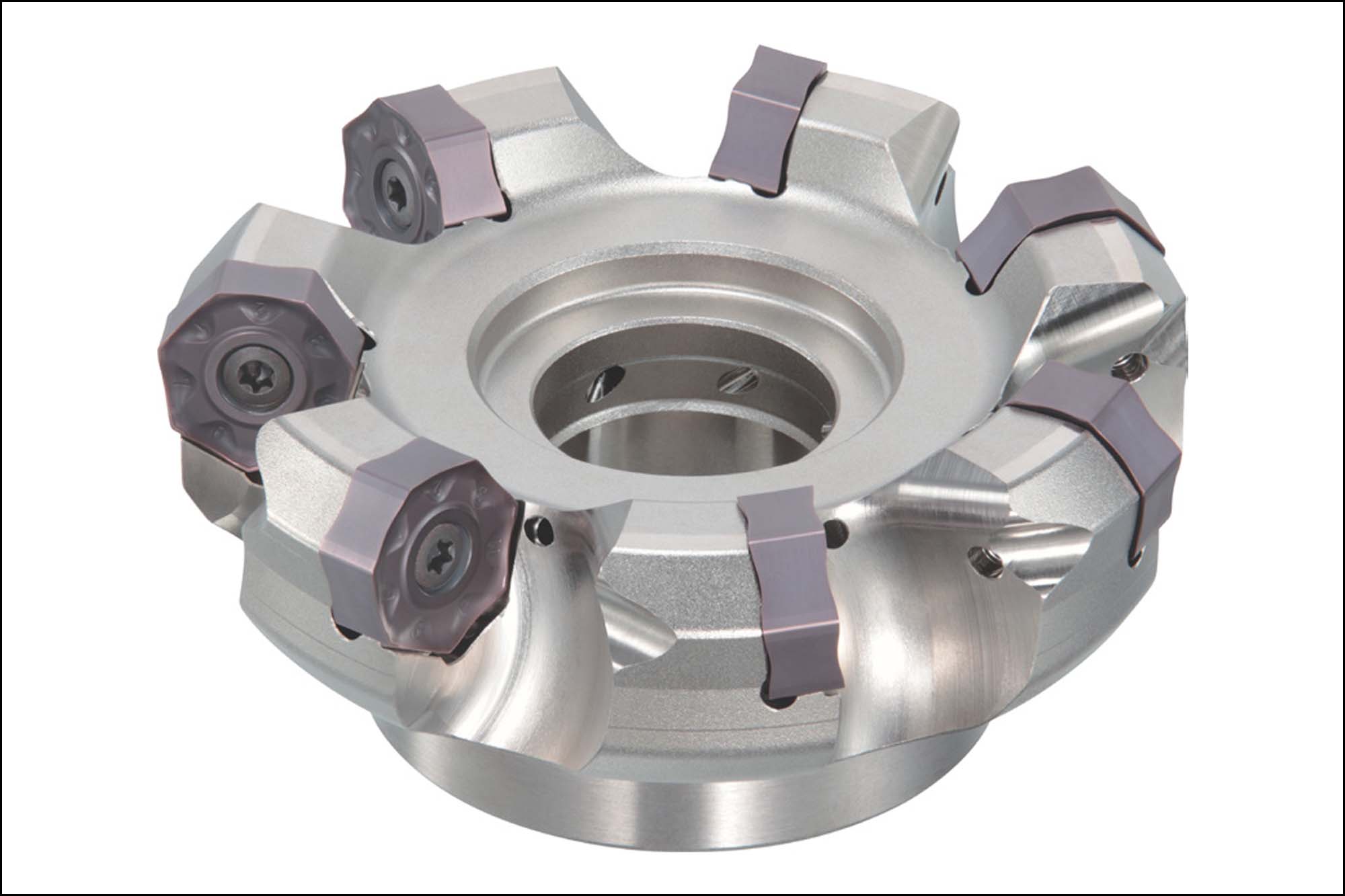
IMTEX has always played a vital role in this direction. IMTEX 2025 will be a major platform for many players involved in cutting tools, machine tools, and manufacturing technologies. They will have excellent opportunities to display innovations and build partnerships to explore new avenues. It will help us expand our market reach and gain some foothold in new market segments.
Cookie Consent
We use cookies to personalize your experience. By continuing to visit this website you agree to our Terms & Conditions, Privacy Policy and Cookie Policy.