Smart tools and superhard materials shape the cutting technology of Ceratizit
By Staff Report December 30, 2024 8:53 pm IST
High-performance coatings, innovative geometries, and targeted cooling techniques are prerequisites for cutting tools. Vivek Tomar, Senior Vice President of Technical and Product Management at CERATIZIT India, shares how they utilise superhard materials like CBN and PCD and technologies like AI and IoT.
What new materials are you using to enhance the performance and lifespan of cutting tools?
Innovation in material science is a cornerstone of our approach to manufacturing cutting tools. We continually explore and develop new materials to ensure superior performance, extended tool life, and sustainability.
High-performance coatings enhance wear resistance, reduce friction, and improve heat dissipation during high-speed machining. Fine-grain carbides and cobalt-enriched carbide substrates enhance toughness and resistance to thermal cracking, especially in high-stress applications. We are integrating recycled tungsten carbide into our tools with recycled carbides, aligning with our commitment to sustainability without compromising performance.
We are committed to driving innovation in cutting tool materials to meet the evolving demands of industries from automotive and aerospace to energy and beyond.
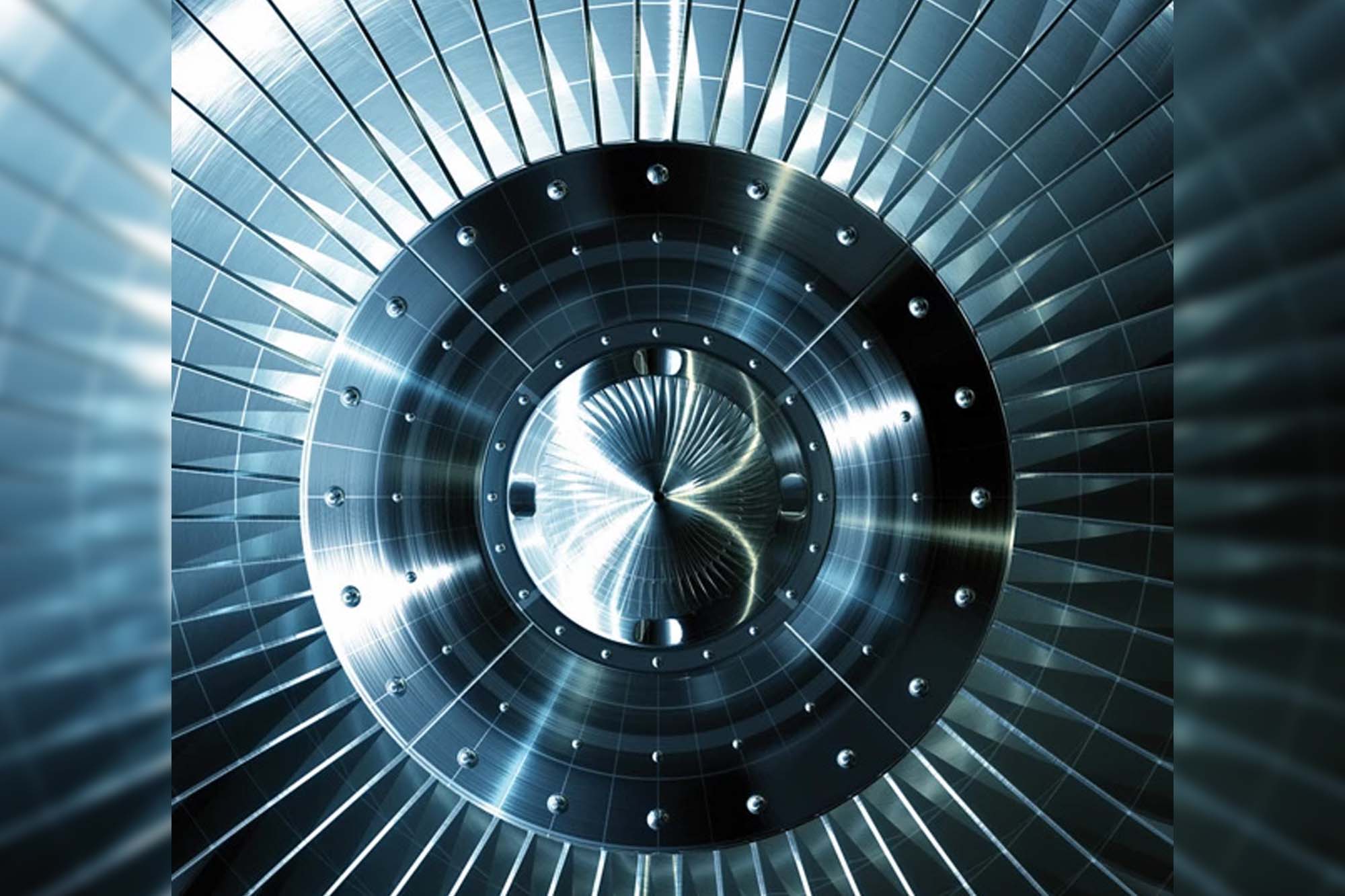
How do advanced tool geometries contribute to Ceratizit’s machining time reduction?
Tool geometry enhances productivity and efficiency during machining operations. We significantly reduce machining time while maintaining superior quality with innovative geometries.
Advanced rake angles and chip breakers ensure smooth and consistent chip evacuation, minimising interruptions and increasing the speed of material removal. This reduces cycle times, especially in high-volume production environments. Our high-feed cutters are designed to be stable during machining and can manoeuvre at much faster feed rates.
Specialised insert designs maximise material engagement, allowing faster material removal rates. Geometries tailored for specific materials, such as aluminium or titanium, ensure optimal performance and reduced machining time.
We deliver solutions that enhance productivity, process stability and cost efficiency by focusing on advanced tool geometries.
What cooling techniques do you use to improve tool life and reduce wear?
Cooling solutions optimise tool performance, extend tool life, and minimise wear during machining. Our cutting-edge cooling techniques are designed to meet the demands of modern manufacturing.
When it comes to cooling lubrication, a little more may be required – but certainly not aimlessly and uncontrollably, because the efficient use of resources and sustainability make simple flood lubrication a thing of the past. The Direct Cooling (DC) range from CERATIZIT offers accurate and targeted cooling rather than flood lubrication of the general area – and it delivers the ultimate precision.
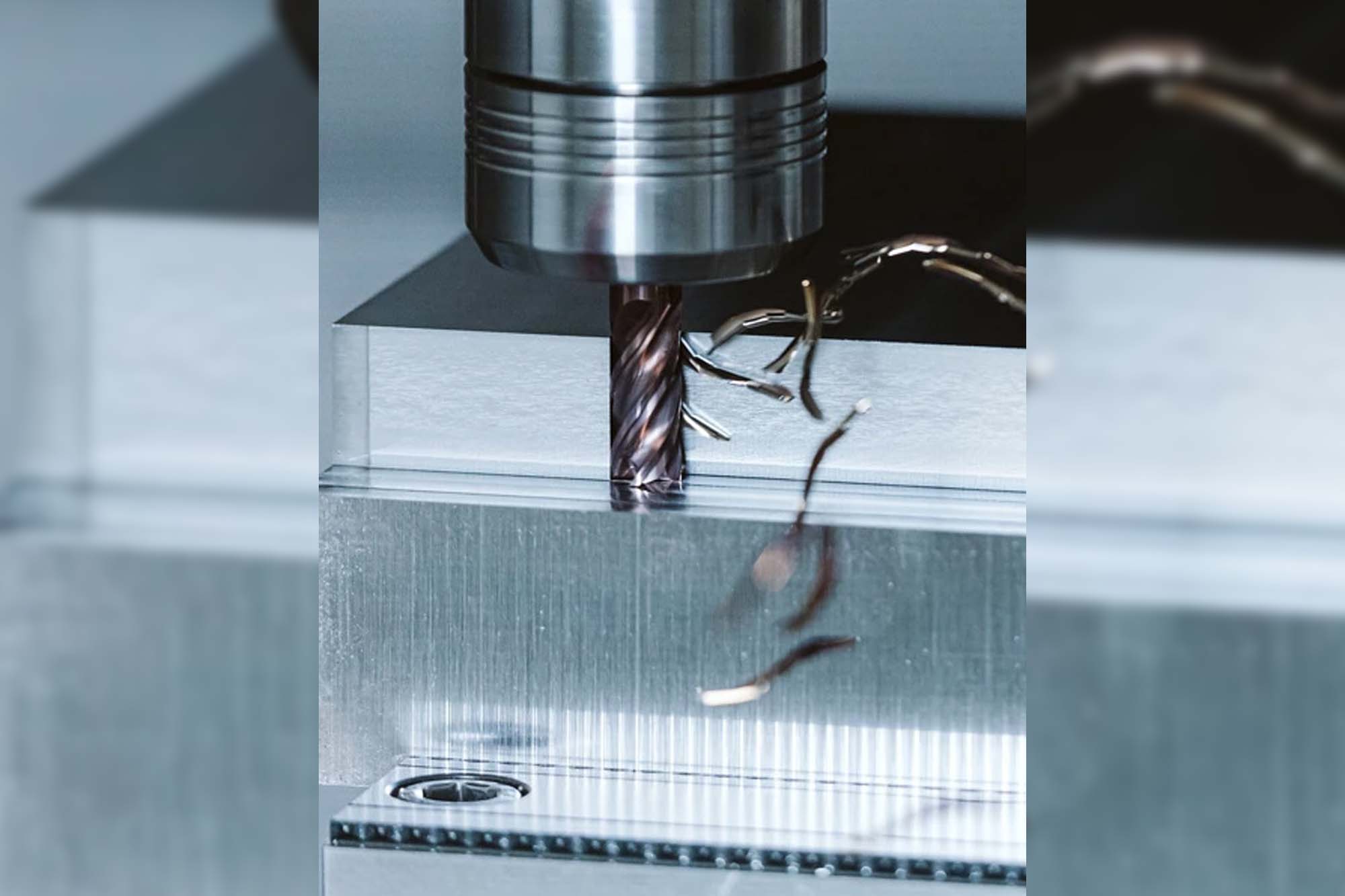
Tool holders with Direct Cooling (DC) are equipped with two inner holes that guide the coolant to where it has the greatest impact: directly on the cutting edge. One hole targets the rake face from above, and the other the flank from below. The precision flank cooling of the DC tool holder makes the difference: it extends tool life by more than 50% compared to cooling that is targeted exclusively at the rake face.
Accurately controlled rather than sporadic, CERATIZIT introduces a new dimension in cooling for cutting tool edges.
What advantages do superhard materials like CBN and PCD offer over traditional cutting tools?CBN and PCD deliver exceptional wear resistance and operational efficiency, especially in demanding machining conditions. Each material is uniquely suited for specific applications and tailored uses.
With superior hardness and toughness, PCD excels in machining non-ferrous materials like aluminium, copper, composites, and abrasive plastics. Its resistance to abrasive wear outperforms traditional carbide tools. The superior thermal conductivity of PCD and the high-temperature stability of CBN enable higher cutting speeds and feeds, reducing cycle times and boosting productivity.
Integrating superhard materials like CBN and PCD into our tool solutions ensures exceptional wear resistance, operational efficiency, and customer satisfaction across diverse industries.
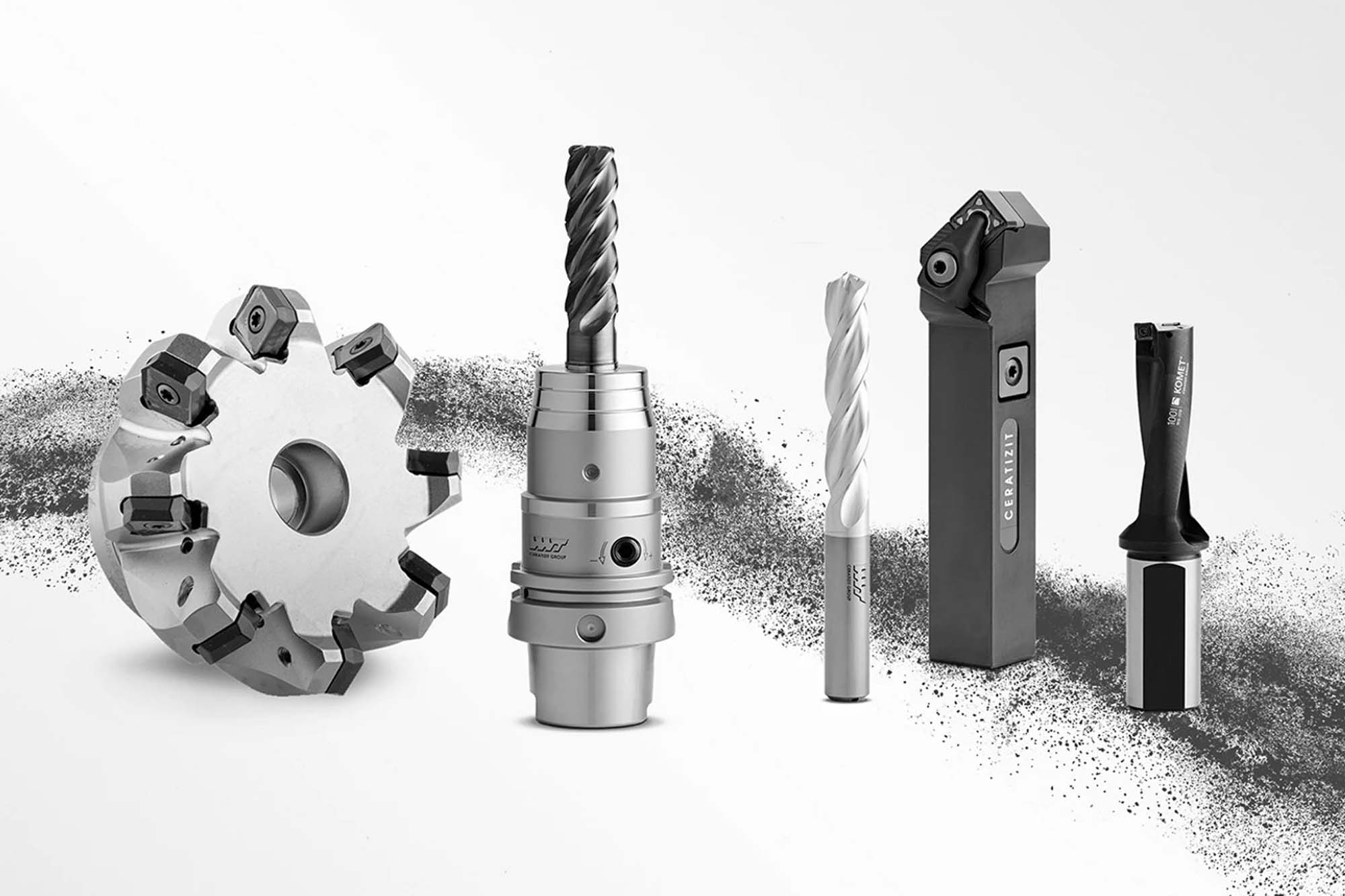
How is Ceratizit using AI, ML, IoT, and other advanced technology to cut tool management and monitoring systems?
Our tool monitoring system is at the forefront of leveraging cutting-edge technologies. Our products like CERAsmart ToolScope & Cockpit revolutionise cutting tool management and monitoring systems. They improve productivity, amplify tool performance, and ensure data-driven decision-making for our customers.
The CERAsmart label bundles CERATIZIT’s digital process optimisation solutions and the production chain.
AI models with ML algorithms are the trend nowadays across different domains for measuring and enhancing process efficiency. Building on our CERAsmart ToolScope and Cockpit, which leverage Industry 4.0 technology, we enable the digital monitoring of manufacturing processes directly on the machines. The collected data is then interpreted and analysed to achieve enhanced process optimisation.
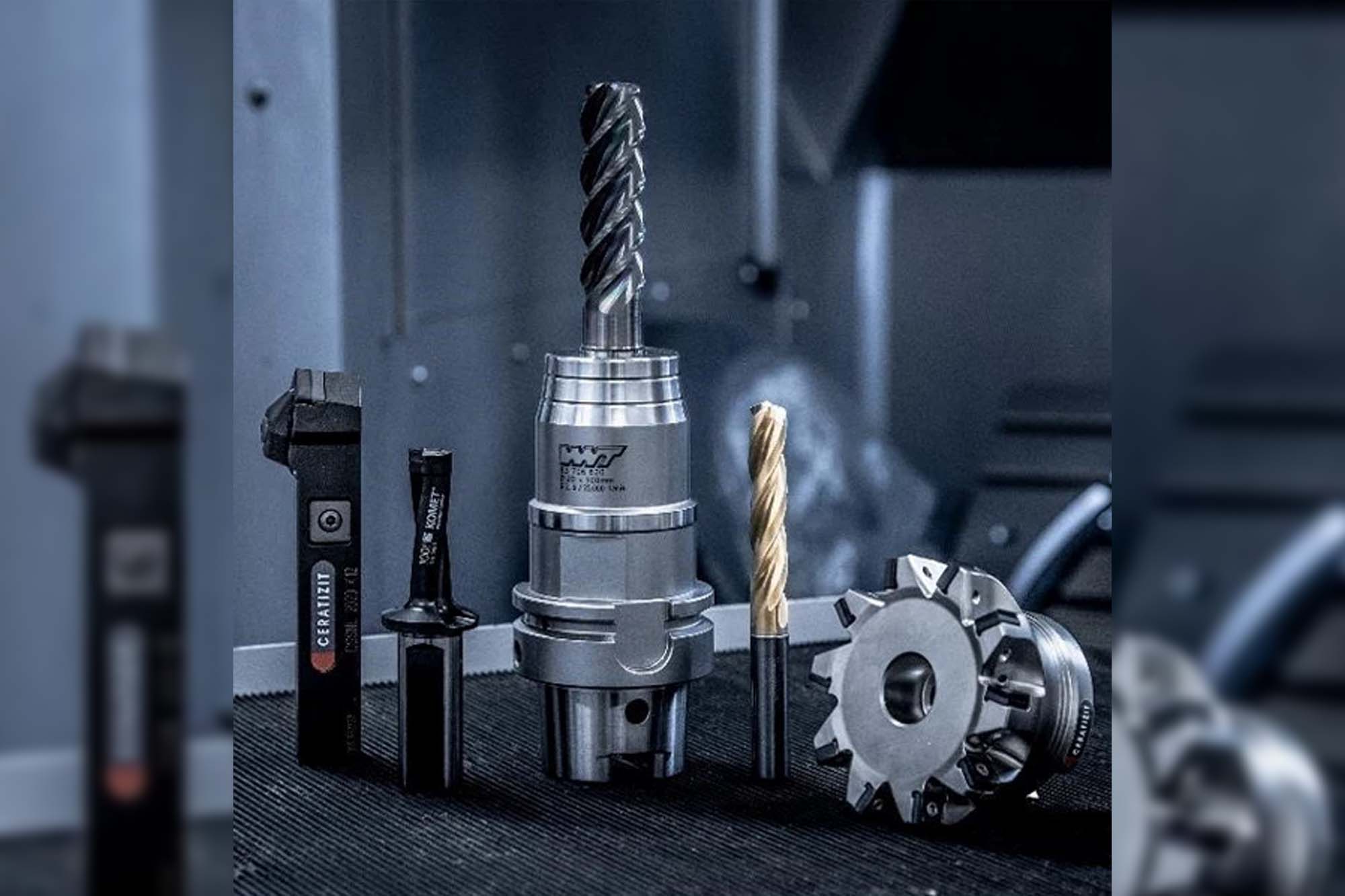
Whereas, from the product portfolio side, we rely on tools like ‘Blueflex’, a digital fine boring bar. We also have refined several back-end processes to serve our customers with more agility. We are already celebrating the ‘Year of AI’, where several projects involving global cross-functional teams take up issues like troubleshooting with case management, complaint handling, opportunity pipeline management, modelling chatbots and CRM with the background of statistical data-driven decision making and error analysis. We do have deputed teams to deal with the Data mining with the trial report against the new tools in the market through our “MY TOOL TEST” forum.
What are you expecting from IMTEX 2025 for global collaborations and market expansion for cutting tool builders?
Today, IMTEX is more than just an exhibition; it is a strategic enabler for cutting tool builders to expand their global footprint, accelerate innovation, and build lasting industry partnerships.
Facilitating global collaborations and showcasing cutting tool innovations will expand market reach and create new networking opportunities. IMTEX will play an important role in positioning India as a manufacturing hub.
Ceratizit looks forward to leveraging this platform to connect with stakeholders, showcase sustainable solutions, and contribute to shaping the future of machining.
Cookie Consent
We use cookies to personalize your experience. By continuing to visit this website you agree to our Terms & Conditions, Privacy Policy and Cookie Policy.