GROB Machine Tools expands in India with focus on precision and AI
By Staff Report December 30, 2024 7:42 pm IST
GROB Machine Tools is expanding its manufacturing operations in India for various reasons. L J Naidu, Managing Director of GROB Machine Tools India, discusses that the dedicated investments in machine precision, AI integration, and R&D for the automotive and aerospace industries result in automation, e-mobility, and Industry 4.0 a reason.
What new technologies have GROB introduced for the machine tool industry?
Our patented machining concept integrated with GROB Net4 Industry is an intersection of automation and e-mobility, tailored to meet the evolving demands of modern manufacturing. This system harnesses Industry 4.0 principles, connecting machines, robots, and production systems into an intelligent, interconnected network that optimises manufacturing processes through real-time data exchange and predictive analytics. In the e-mobility context, where precision, efficiency, and scalability are critical, our machining solutions are used for manufacturing high-precision components such as electric motor housings, battery modules, and drivetrain parts. The patented machining techniques enhance production flexibility and reduce cycle times while maintaining tight tolerances necessary for high-performance electric vehicles. Through GROB Net4 Industry, manufacturers get seamless automation, adaptive production systems, and data-driven decision-making, enabling faster response to market demands and improved product quality. This holistic approach drives the efficiency and sustainability of e-mobility production for a broader shift toward smart, flexible manufacturing in the automotive and other advanced industries.
What new materials enhance the performance and lifespan of GROB’s tools and technology?
The continuous improvement and Finite Element Analysis (FEA) of the machine bed in our machines enhances manufacturing systems’ lifespan, stability, and performance. This machine bed is made from steel weld construction. By utilising FEA, we can simulate and analyse the structural integrity of the machine bed under various operational conditions, identify potential weaknesses, and optimise the design for better load distribution, rigidity, and durability. This data-driven approach allows for targeted improvements in the construction of the machine bed, minimising vibrations and ensuring high precision during machining. The robust steel weld construction provides a solid foundation, reducing wear and tear over time and improving the machine’s ability to handle heavy-duty operations. Continuous design improvements and advanced analytical techniques ensure that our machines deliver long-lasting, reliable performance, reducing maintenance costs and extending their operational lifespan.
Can you provide insights into GROB’s approach to maintaining the reliability and longevity of its machinery?
We invest in the R&D to develop machines’ reliability and performance longevity. We continuously try to advance our technology, ensuring that our machines incorporate the latest innovations in precision, efficiency, and durability, reducing user downtime and operational costs. In parallel, we emphasised training operators and maintenance personnel through comprehensive programs focusing on the importance of regular health checkups and preventative maintenance. This approach empowers operators to monitor the machine’s condition, detect early signs of wear or malfunction, and do routine maintenance tasks that prevent major failures. As part of our holistic training philosophy, this knowledge ensures that machines are kept in optimal condition, maximising their uptime and extending their operational lifespan. This combination of cutting-edge R&D and practical training creates a sustainable ecosystem where machines perform reliably over time, delivering consistent performance and high productivity for manufacturers.
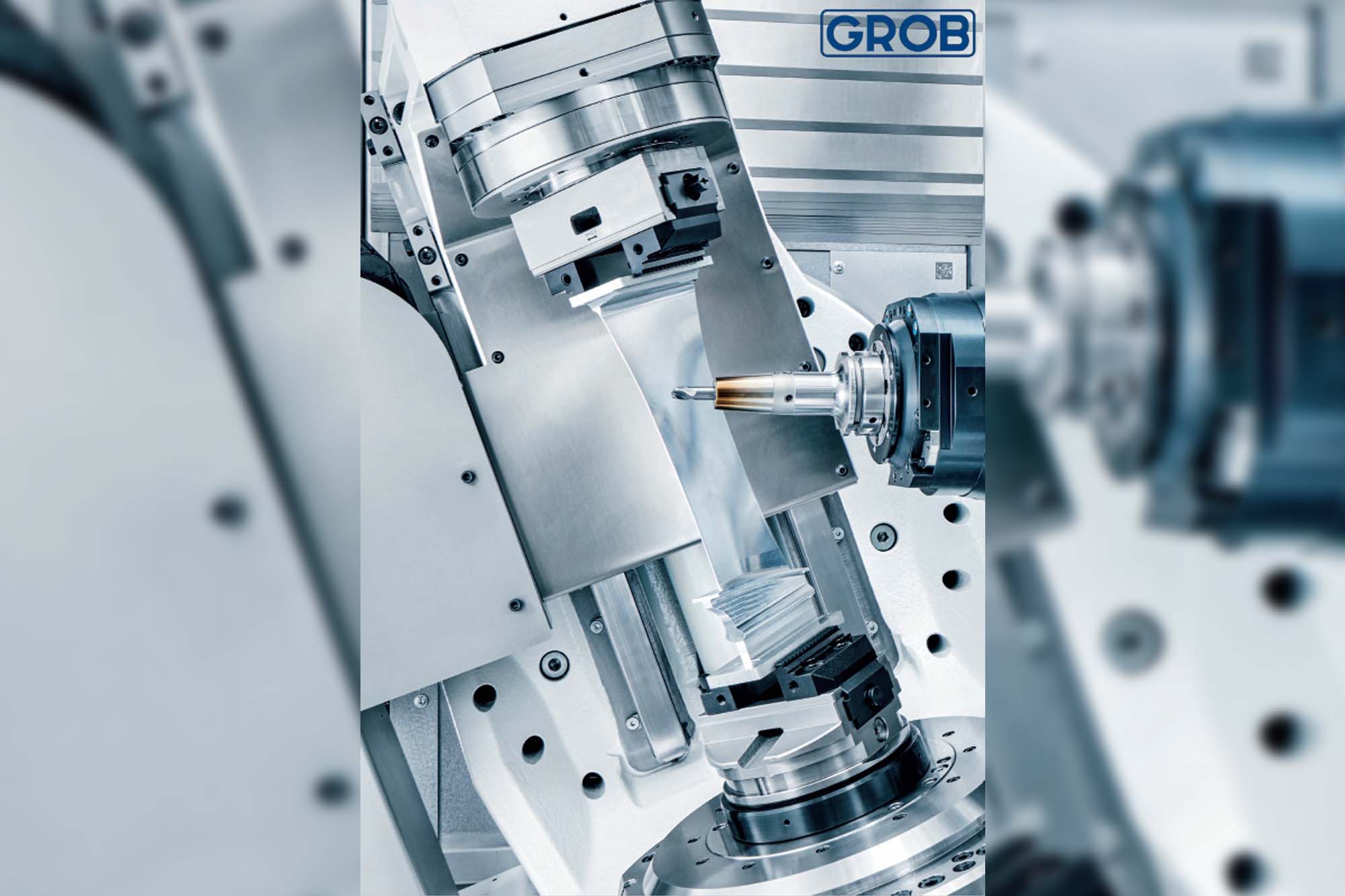
How are AI, ML, and IoT being integrated into GROB’S machines for management and monitoring systems?
GROB Net4 Industry is a core standard feature integrated into all our machines, serving as an advanced system for monitoring machine performance in real-time. This digital platform provides continuous, data-driven insights into various aspects of the machine’s operation, including machine utilisation, cycle times, tool wear, and overall health. With this data, GROB Net4 Industry helps manufacturers detect inefficiencies, predict maintenance needs, and optimise production processes, increasing productivity and reducing downtime. The system is designed for easy access by customers through a user-friendly interface, allowing operators and maintenance teams to remotely monitor machine status and receive alerts or diagnostics at any time. This seamless connectivity enhances transparency and control, enabling proactive decision-making and immediate responses to potential issues.
What designing changes and R&D go into making the machines suit the automotive and aerospace industries?
We have made significant R&D investments to design and produce machines that meet the stringent requirements of the automotive and aerospace industries. These sectors demand high precision, reliability, and versatility due to the complex geometries, tight tolerances, and safety-critical applications involved. To address these challenges, we enhanced our machine rigidity and stability through advanced finite element analysis (FEA) and optimised thermal management systems for consistent performance during long machining cycles. In addition, we have developed specialised tooling systems and modular setups that allow for greater flexibility in manufacturing a wide range of parts, from automotive engine components to aerospace turbine blades.
We prioritise automation, incorporating advanced robotics and Industry 4.0 capabilities to improve efficiency, reduce human error, and ensure precise control over every stage of the production process. Through these efforts, we have created reliable, high-performance machines that can meet the exacting standards of the automotive and aerospace industries, enhancing productivity, quality, and sustainability in these high-demand sectors.
What is your outlook for the Indian machine tool industry? What improvements and changes can give it a push?
The Indian machine tool industry holds a promising outlook, driven by the country’s growing manufacturing sector, increasing foreign direct investment (FDI), and the strategic push to become a global export hub. With a strong focus on Make in India and an expanding industrial base, India is positioning itself as a key player in the global supply chain. We recognised this potential and thus have established our 6th manufacturing plant in Bangalore to cater to the growing demand and export machines globally. This expansion reflects our confidence in India’s future as a manufacturing powerhouse, where the combination of competitive labour costs, technological advancements, and a large domestic market creates vast opportunities. To further accelerate the growth of the Indian machine tool industry, there needs to be a focus on improving technology adoption, skilling the workforce, and enhancing infrastructure. Investments in automation, digitalisation (Industry 4.0), and supply chain efficiency would increase productivity and boost India’s capability to produce high-precision, high-quality components for industries like automotive, aerospace, and defence.
Cookie Consent
We use cookies to personalize your experience. By continuing to visit this website you agree to our Terms & Conditions, Privacy Policy and Cookie Policy.