Mastercam transforms CNC with automation and simplicity
By Staff Report December 30, 2024 5:57 pm IST
Mastercam has a strong grip on CAD/CAM software, making the work of die and mould manufacturers faster, more precise, and less error-prone. Vineet Seth, Managing Director—South Asia & Middle East at Mastercam APAC, shares how they also advance CNC efficiency with cutting-edge controller integrations, hybrid manufacturing tools, and Industry 4.0 support.
What recent advancements in CNC technology have impacted the efficiency of Mastercam?
We kept pace with the rapid advancements in CNC technology, ensuring users can take full advantage of the latest innovations. For example, the updates to integrate with modern controllers like Heidenhain TNC7 and Siemens Sinumerik One have been game changers. These collaborations allow for smoother post-processing, real-time adaptive machining, and improved precision, which is critical in industries that demand high accuracy.
Users benefit from faster setups, fewer errors, and tackling complex machining tasks. In addition to controllers, cutting tool technology has seen incredible progress, and we embraced this by partnering with industry leaders like Sandvik Coromant, GARR Tool, and Kennametal. These partnerships provide direct access to the latest tool libraries within Mastercam, complete with accurate geometries and application data. This makes programming efficient and delivers optimal performance on the shop floor. For instance, Sandvik’s CoroPlus Tool Library saves valuable time during tool setup and enhances machining outcomes.
Hybrid manufacturing is another area where we shine. With machines like Meltio combining additive and subtractive manufacturing, we introduced tools to program both processes in a unified environment. This hybrid capability simplifies workflows and allows manufacturers to create complex parts faster and more cost-effectively. We have also made advancements like digital twins and robotic machining through Robotmaster.
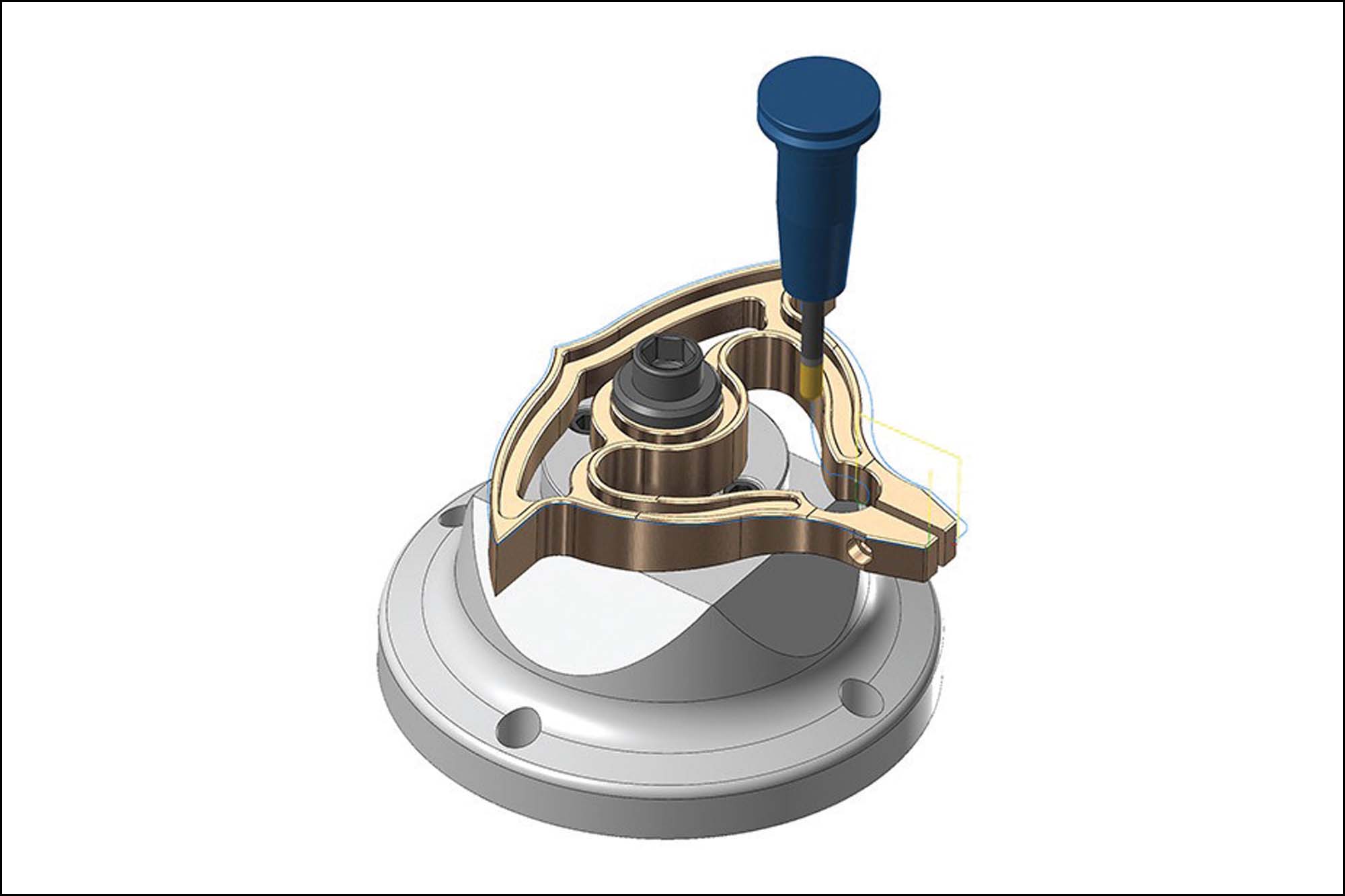
What makes Mastercam’s software intuitive and user-friendly for both experts and beginners?
We rely on thoughtful designing and close partnerships with our users to develop solutions. The software’s interface, modelled on the familiar Windows ribbon style, ensures that even someone new to CAD/CAM can easily navigate it. Everything is laid out logically, so the workflow feels natural and easy to follow, whether you’re creating geometry, generating toolpaths, or running simulations. What sets Mastercam apart is how it balances simplicity for beginners with powerful features for experts. The software provides templates and pre-configured settings that minimise the learning curve for those just starting. For experienced users, it offers advanced customisation options, allowing them to tailor their workspace, create macros, and tweak processes to match their specific needs. Another key factor is the level of visual feedback that we provide. Users can preview toolpaths, simulate operations, and detect potential collisions before committing to a program, which reduces errors and boosts confidence. With a robust library of online resources, active user forums, and responsive support, these features make us approachable to everyone, regardless of their experience level.
How is Mastercam integrating with Industry 4.0 and supporting smart manufacturing practices?
We are deeply aligned with the principles of Industry 4.0. Open architecture is a big part of this, allowing users to customise and extend its capabilities through the SDK and API. This means manufacturers can create specialised tools or integrate Mastercam seamlessly with other systems like Verisurf for inspection, Robotmaster for robotic machining, or mConnect for IoT-enabled monitoring.
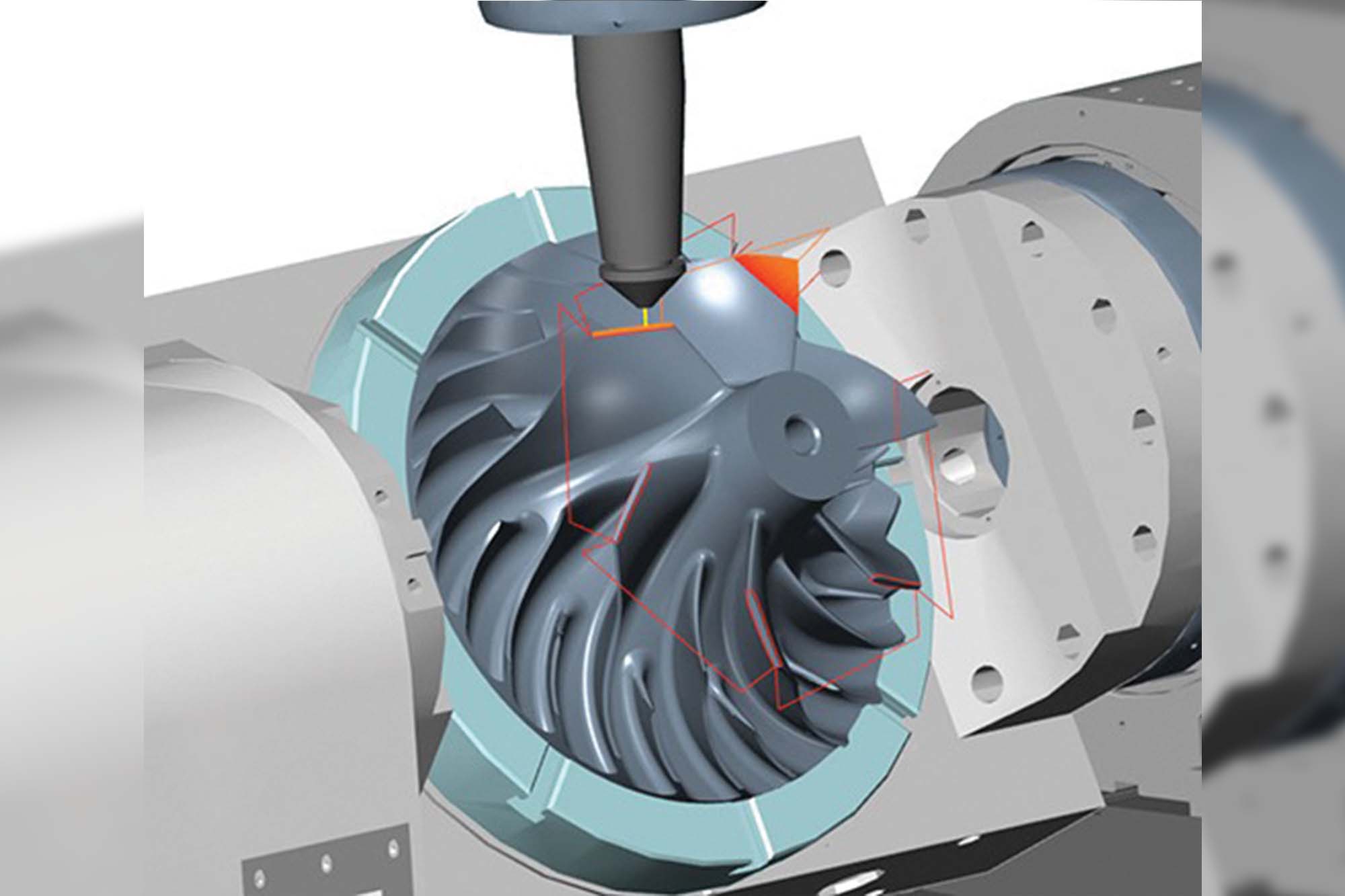
The ability to integrate with these tools brings the shop floor into the digital age, making processes more transparent and efficient. For instance, Robotmaster extends our capabilities into robotic machining, which is becoming increasingly important for automation. Similarly, tools like Aplus make additive manufacturing workflows more accessible, enabling manufacturers to move towards hybrid and sustainable production models. We also support real-time monitoring, predictive maintenance, and process optimisation, all of which are central to smart manufacturing. Digital twins allow users to simulate and perfect operations before they begin, improving efficiency and reducing waste. As Industry 5.0 emerges, focusing on human-machine collaboration, we are already prepared with tools that support cobots and other collaborative manufacturing technologies.
How do CAD/CAM systems streamline die and mould production processes?
Like ours, CAD/CAM software makes die and mould production faster, more precise, and less error-prone through a combination of advanced toolpath strategies, high-performance algorithms, and intuitive workflows. For example, our Dynamic Motion technology optimises tool engagement by maintaining a constant chip load, which leads to faster material removal and longer tool life. For die and mould makers, this saves time and reduces production costs.
Surface finish is critical in this industry, and we deliver it with features like Accelerated Finishing, which ensures superior quality on complex surfaces. Multi-surface machining strategies and deburring capabilities further enhance the final product by addressing intricate geometries and fine details. The software also supports multi-axis machining, allowing users to create complex moulds and dies in fewer setups, which reduces lead times and potential errors.
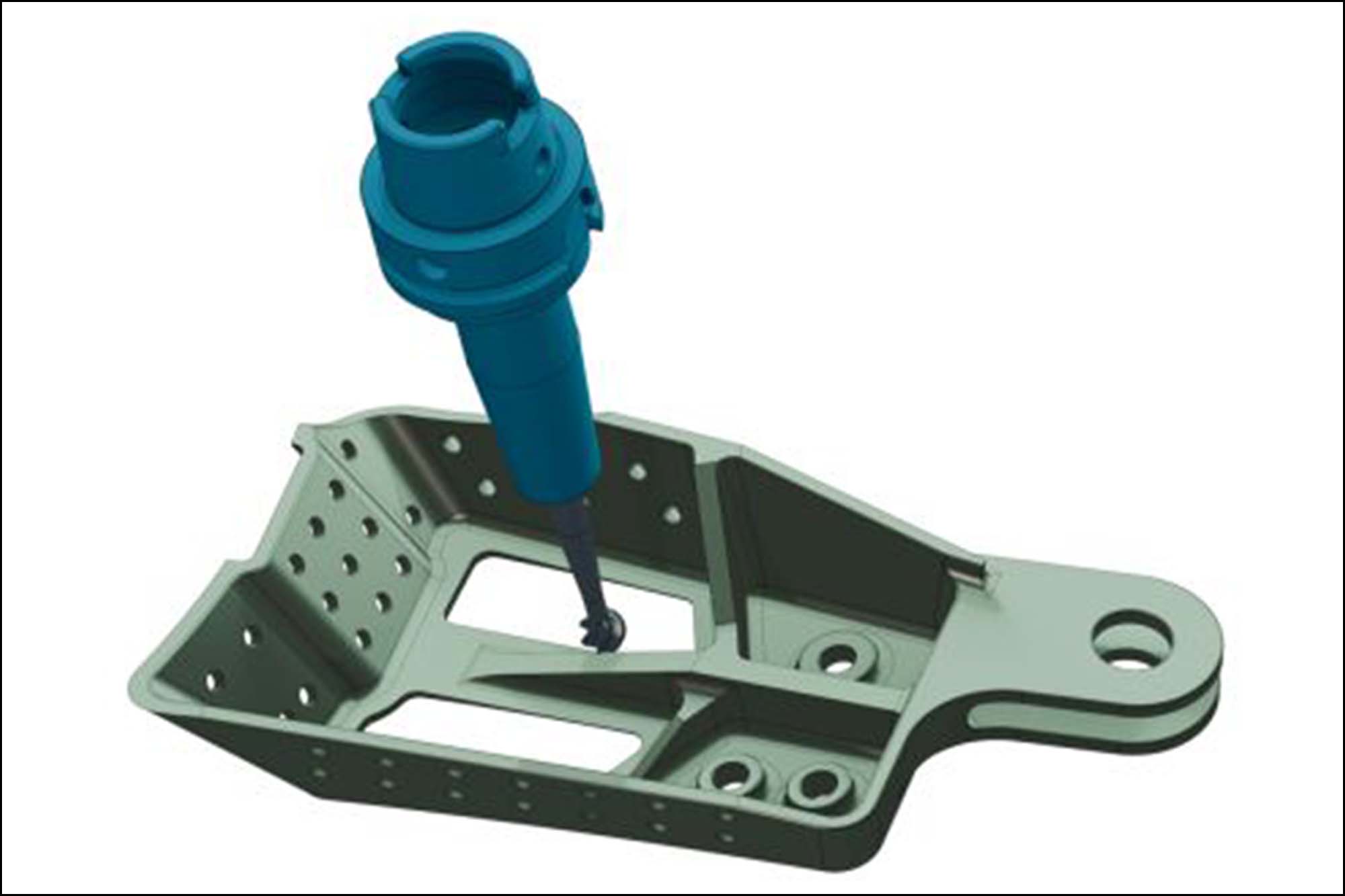
Our simulation tools play a big role in ensuring our success. Users can avoid costly mistakes by visualising toolpaths and identifying potential issues before machining begins. Our workflows are designed to guide users through the process seamlessly, whether working with a simple 2D die or a complex 5-axis mould. This, coupled with robust support for hard-to-machine materials like titanium, makes Mastercam an invaluable tool for die and mould production.
How are your CAD/CAM systems improving CNC programming and setup for manufacturers?
Mastercam transforms CNC programming and setup by automating repetitive tasks, simplifying complex operations, and providing tools that enhance precision and efficiency. One of its standout features is the extensive library of pre-configured templates, tool libraries, and post-processors, which reduces programming time. Users can rely on these resources to get started quickly while tailoring them to specific machines or processes.

The software’s simulation and verification tools ensure that programs are error-free before they reach the machine. This saves manufacturers from costly mistakes, minimises downtime, and improves productivity. For example, toolpaths generated with Dynamic Motion technology reduce cycle times and extend tool life by optimising cutting conditions. These benefits are especially valuable for manufacturers dealing with high-volume or high-precision work.
Setup sheets generated by Mastercam provide machinists with detailed instructions, making it easier to set up machines accurately and efficiently. The software’s ability to handle complex multi-axis and mill-turn operations ensures that even the most challenging jobs can be easily completed. Real-world customer feedback highlights how we have helped them reduce scrap rates, improve turnaround times, and tackle projects they previously thought impossible.
Cookie Consent
We use cookies to personalize your experience. By continuing to visit this website you agree to our Terms & Conditions, Privacy Policy and Cookie Policy.