Advanced cutting tool selection and technology enhance machining performance
By Staff Report August 31, 2024 11:35 am IST
Amit S Deo, Vice President – Sales and Marketing, Guhring, suggests that selecting the right cutting tool is critical in high-speed machining, impacting surface finish, tool life, and overall productivity, especially for challenging aerospace alloys like titanium and Inconel.
What factors are required when selecting milling tools for high-speed machining applications?
Selecting milling tools for high-speed machining involves several key factors to ensure optimal performance and efficiency. A few crucial considerations are tool material like carbide, cermet, PCD or CBN based on its wear resistance, higher tool life, better quality and ability to maintain a sharp cutting edge at high temperatures. Tool coatings can significantly enhance performance by reducing friction, improving hardness, and increasing tool life. Select a coating that matches the material machined and the specific cutting conditions. Guhring even has a specialised coating for high-speed machining of Aluminium components called Zenit.
The design of several flutes and cutting-edge geometry should be optimised for high-speed cutting. For example, tools with fewer flutes can provide higher chip removal rates, while tools with specific geometries (like high-rake angles) can reduce cutting forces and improve surface finish. Chip removal also plays a role in high-speed machining; chip breakers are needed to break long chips.
In the context of machine compatibility, it should be ensured that the chosen tools are compatible with your CNC machine’s capabilities, including spindle speed, feed rate, and power. High-speed machining often requires precise control over these parameters to achieve the desired results. The machine should also have a spindle through coolant with pressure >30 bars. Mist or MQL offers is on advantages.
The workpiece material plays a crucial role, as different materials like aluminium, steel, titanium, composites, and Inconel have distinct cutting characteristics, requiring specific tool properties. For instance, tools designed for machining aluminium may need different coatings and geometries than those used for stainless steel or titanium.
Tool life and cost are also important factors. Although high-speed machining tools often have a higher initial cost, their enhanced productivity and longer tool life can justify the investment. Vibration and stability become critical at higher speeds, as excessive vibrations can compromise surface finish and shorten tool life. Choosing tools with good rigidity while ensuring your setup minimises vibrations through effective clamping and support is essential.
Lastly, selecting a reliable tool manufacturer is vital. Companies like Guhring offer high-quality tools and valuable support in tool selection, application advice, and troubleshooting, helping to optimise machining performance.
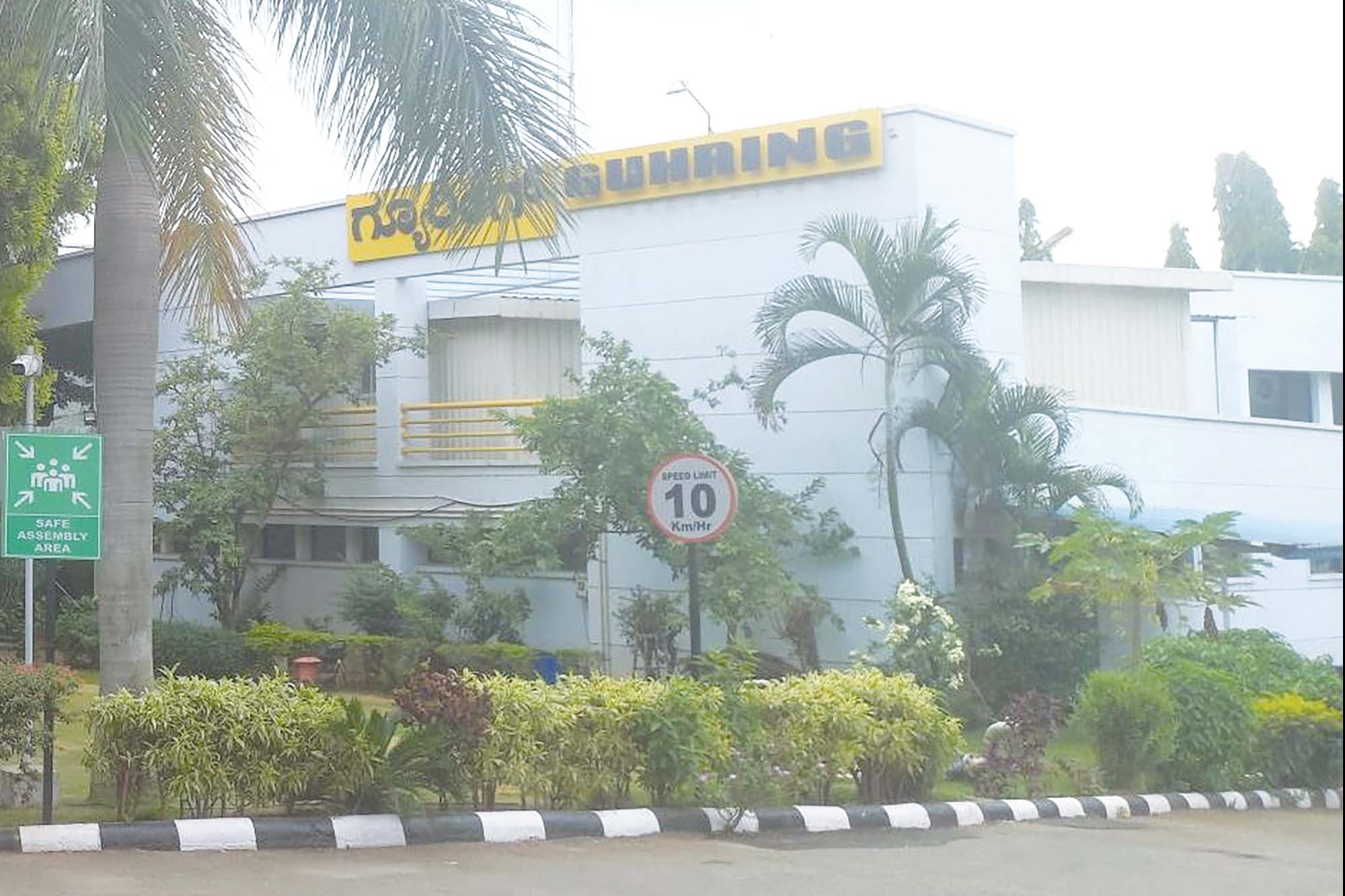
How can the choice of cutting tool geometry impact the surface finish and tool life in milling operations?
The geometry of a cutting tool plays a crucial role in determining both the surface finish and tool life in milling operations. Cutting tool geometry involves several aspects that directly impact machining performance. The rake angle minimises cutting forces and friction, improving the surface finish and extending tool life. It also aids in better chip flow and heat dissipation. A negative rake angle may increase cutting forces and generate a rough surface. It is beneficial to machine materials.
The clearance angle, also known as the relief angle, prevents the tool from rubbing against the workpiece, reducing friction and improving the surface finish. More clearance can prevent excessive heat and poor surface quality.
The design of flutes affects chip removal and coolant flow. Even the number of flutes affects the surface finish. Tools with fewer flutes (e.g., 2-flute end mills) can handle larger chip loads and are better for roughing operations where chip removal is crucial. They might need to provide a better surface finish for finishing operations. Flutes (e.g., 4 or 6) offer a smoother finish and are suited for finishing operations but may have reduced chip-carrying capacity.
Cutting-edge geometry also influences performance. A small cutting-edge radius can produce a finer surface finish but might lead to quicker tool wear due to increased cutting forces. A larger radius increases tool life by reducing cutting stresses but may produce a rougher surface finish. The helix angle affects how the tool engages with the material. Higher helix angles (e.g., 30° to 45°) provide smoother cutting action and better surface finish due to improved shearing. However, lower helix angles can lead to a rougher finish but might be suitable for applications.
Ball nose end mills are used for contouring and 3D surface finishing. They provide a smooth surface finish for complex geometries but may wear faster due to the continuous engagement of the cutting edge. Finally, Flat End Mills are best for producing flat surfaces and achieving accuracy in cutting. They are used for roughing and finishing operations on flat surfaces.
How do your cutting tools address the challenges of machining aerospace-grade alloys such as titanium and Inconel?
Machining aerospace-grade alloys like Titanium and Inconel presents unique challenges due to their high strength, heat resistance, and hardness.
Addressing the challenges of machining demanding materials like Titanium and Inconel requires specialised cutting tools and advanced techniques. Tool materials play a crucial role; Tungsten Carbide is often used for machining Titanium and Inconel due to its high hardness and wear resistance. Carbide tools maintain sharpness at high temperatures and resist deformation under heavy cutting forces. It can be used in specific applications where toughness is a priority.
Newer generations go beyond options like TiN, TiCN, and TiAlN. Coatings incorporating Chromium (Cr), Silicon (Si), and Zirconium offer enhanced wear and heat resistance. Guhring has developed proprietary coatings like Signum, Raptor, and Perox that are specifically designed for improved performance.
The geometry of cutting tools is equally important. Positive rake angles reduce cutting forces and heat generation. Tools with a slightly negative rake for materials like Inconel might be used to improve durability and minimise edge chipping.Edge geometry and flute design also play a critical role. A combination of sharp edges and a controlled edge radius for aerospace alloys can help manage heat and wear. Tools with a high helix angle can improve chip removal and reduce the likelihood of recutting chips. Tools are also designed considering coolant systems and lubricants, ensuring tool rigidity, the type of chip formation, and its removal. Optimal speed, feed, and depth of cut are always the centre of focus.
In high-temperature machining environments, such as aerospace manufacturing, milling tools require advanced coatings to enhance performance and longevity. These coatings are designed to withstand extreme conditions, reduce friction, and improve overall tool life. Here are some of the advanced coating materials used in these applications.
Aluminum Titanium Nitride (AlTiN) is known for its hardness, high oxidation resistance, and thermal stability. It maintains its properties at temperatures up to 1,000°C (1,832°F), making it highly suitable for high-speed and high-temperature machining. It helps reduce friction and improve war resistance, which is particularly valuable when machining aerospace materials like Inconel and Titanium alloys.
Another is Titanium Carbonitride (TiCN), which offers excellent hardness and wear resistance combined with a low coefficient of friction. It provides a tough, abrasion-resistant layer that performs well in challenging conditions.
Multi-layer coatings combine different materials to take advantage of each layer’s unique properties. The coatings provide hardness, thermal stability, and wear resistance. These layers can have a combination of TiN, TiCN, AlTiN, SiN, SiC, etc. Finally, Ceramic coatings, such as those made from Titanium Aluminum Carbide (TiAlC) or Zirconium Carbide (ZrC), offer high hardness and thermal stability. They provide excellent wear resistance and thermal stability, making them suitable for machining aerospace-grade alloys under severe conditions.
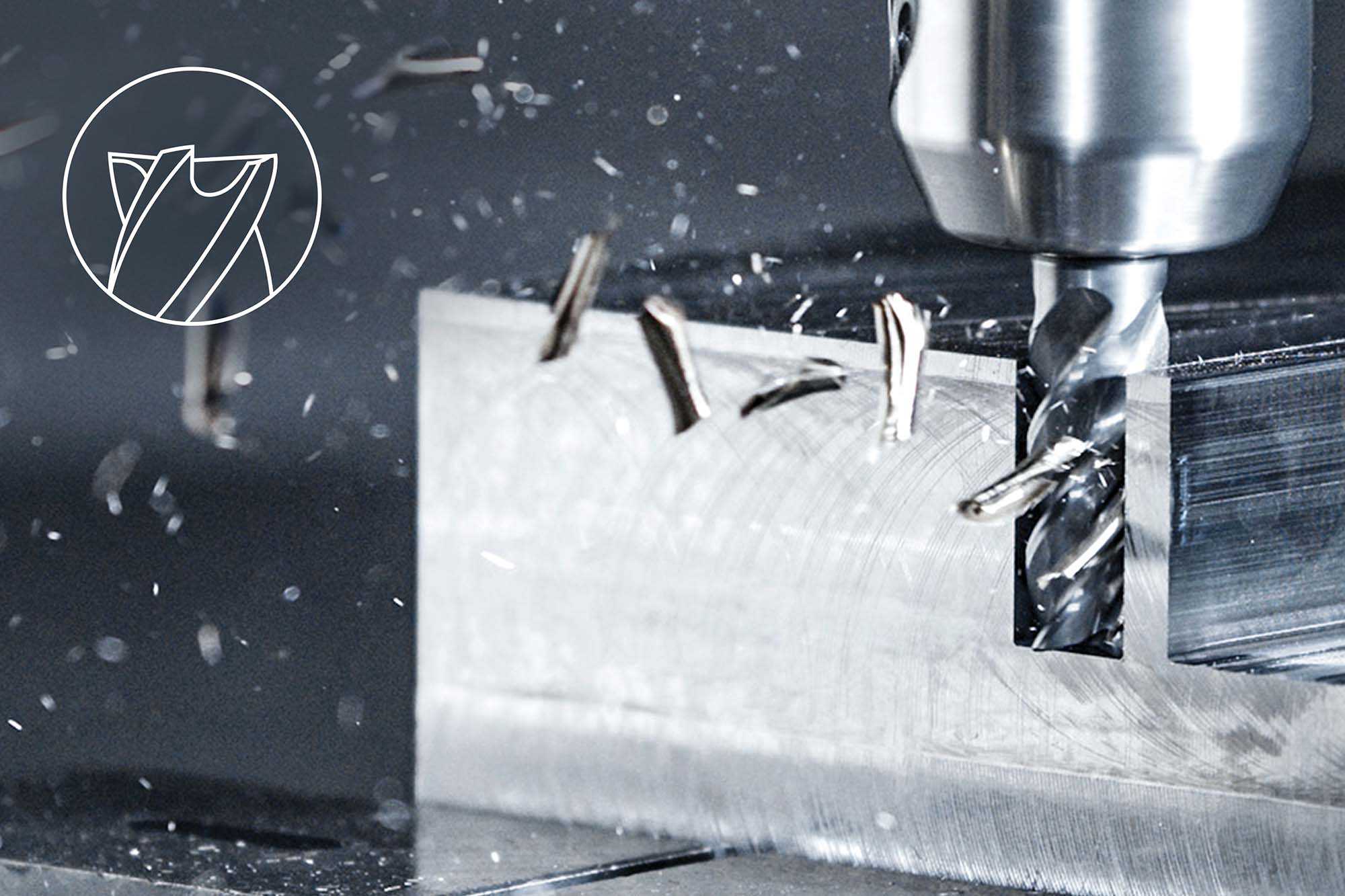
Could you elaborate on initiatives taken for Atmanirbharta in the production facility?
“Atmanirbharta,” or self-reliance, is a significant initiative in India aimed at enhancing domestic production capabilities and reducing reliance on imports. Guhring has undertaken various strategies and initiatives to achieve Atmanirbharta.
Guhring is a role model when we talk about atmanirbharta, as we have a fully integrated plant in the real sense. We have our carbide processing rods, manufacturing machines, quality inspection equipment, coating technology, and plant. The technology transfer is 100%. Guhring can access any process and draw across all 70 manufacturing locations globally to produce the same tool in India.
We have a common ERP platform for processing and e-learning at all levels in-house. Many products are developed locally and established at the customer’s place.
What emerging technologies are shaping the future of machine tools used in the aerospace sector?
Emerging technologies are transforming the aerospace sector, driving advancements in machine tools and manufacturing processes. Several key technologies shape the future of machine tools in the aerospace sector.
Additive manufacturing, or 3D printing, is revolutionising aerospace production by enabling the creation of complex geometries and lightweight structures. It allows for the direct manufacturing of parts with intricate designs that would be difficult or impossible to achieve with traditional methods. The new materials for additive manufacturing, such as high-strength alloys and composites, enhance the performance and application range of 3D-printed aerospace components.
Advanced CNC machining is evolving with the introduction of multi-axis systems, like 5-axis and 6-axis machines, which enable more complex and precise machining of aerospace components. The machines reduce the need for multiple setups while enhancing accuracy and surface finish. High-speed machining (HSM) technologies increase productivity and surface quality, particularly for challenging materials like Titanium and inconel commonly used in aerospace.
Automation and robotics also play a pivotal role. Robotic arms are increasingly used for drilling, assembling, and material handling tasks, offering high precision and repeatability. Integrated work cells that combine various machines and automated material handling systems streamline production processes, reduce human intervention, and enhance consistency and efficiency.
Artificial Intelligence (AI) and machine learning are transforming machine tools through predictive maintenance and real-time optimisation. AI and machine learning algorithms analyse data from machine tools to predict potential failures and schedule maintenance before issues arise, minimising downtime and extending tool life. AI-driven systems optimise cutting parameters in real-time based on material properties and tool conditions, improving efficiency and quality.
Advancements in materials and coatings are equally critical. High-performance coatings, including advanced ceramics and nano-coatings, significantly enhance tool life and performance in the extreme conditions typical of aerospace applications. Innovations in composite materials, such as carbon fibre and ceramic matrix composites, are being integrated into machine tools to improve strength, durability, and thermal resistance.
Micro-manufacturing is also gaining importance, enabling the production of precise miniature components essential for aerospace applications like sensors and micro-actuators. Furthermore, high-energy beam machining, such as laser and electron beam technologies, is utilised for cutting and welding aerospace materials with high precision and minimal thermal distortion. These advancements are pushing the boundaries of what is possible in aerospace manufacturing.
Cookie Consent
We use cookies to personalize your experience. By continuing to visit this website you agree to our Terms & Conditions, Privacy Policy and Cookie Policy.