Indigenous CAM production aids global energy storage and EV markets
By OEM Update Editorial July 8, 2024 7:15 pm IST
Energy storage has gained prominence due to its rising requirements. India is set to revolutionise the global energy storage market through indigenous production of cathode active materials (CAM) and reduce import dependence. The technological innovations in CAM would also benefit the burgeoning EV market.
Prime Minister Narendra Modi pledged at the COP26 conference (2021) to achieve net zero emissions by 2070, a vital step required by the world’s third-largest CO2 emitter. This pledge hinges significantly on the electrification of India’s transportation sector, especially with the shift towards electric vehicles (EVs). This transition necessitates a substantial increase in lithium-ion (Li-ion) battery production, where cathode active materials (CAM) play a huge role. CAM drives the energy storage phenomenon in Li-ion batteries, essential for powering devices ranging from EVs to energy storage systems (ESS) and consumer electronics.
Our journey towards self-reliance in CAM production is a potential game-changer for the global energy storage market. With the advent of EVs, the demand for batteries is projected to soar, with industry forecasts indicating a compound annual growth rate (CAGR) of 35 percent for EV sales in India, reaching an annual volume of 27.2 million units by 2032.
Introduction to CAM
Cathode-active materials hold immense importance within lithium-ion batteries. They impact battery performance and drive the range of electric vehicles. CAMs are the core of lithium-ion batteries, forming about 51% of the value chain of these batteries. They are important for the efficient storage and release of electrical energy, which powers modern devices and applications, from smartphones and laptops to electric vehicles and renewable energy storage systems. CAMs are composed of metal oxides and are responsible for electrochemical processes. This process enables lithium-ion batteries to function, facilitating the movement of lithium ions between the cathode and anode during charging and discharging cycles. The most common cathode materials used in lithium-ion batteries include lithium cobalt oxide (LiCoO2), lithium manganese oxide (LiMn2O4), lithium iron phosphate (LiFePO4 or LFP), and lithium nickel manganese cobalt oxide (LiNiMnCoO2 or NMC). Each of these materials offers varying energy density levels, thermal stability, and cost-effectiveness.
A significant advancement in this field is the development of ternary cathode-active materials. These materials are composed of nickel, manganese, and cobalt. They offer superior energy density, thermal stability, and longevity performance compared to traditional cathode materials. This innovation is set to redefine energy storage technology by providing more efficient, durable, and sustainable power solutions. With their heavy reliance on lithium-ion batteries, the role of CAMs will become increasingly critical for the reliability and effectiveness of these energy storage systems.
CAM in lithium-ion batteries includes several chemicals with distinct advantages and disadvantages. LiCoO2 offers high energy density, making it ideal for smartphones and laptops, but it is expensive and has safety concerns due to thermal instability. LiMn2O4 provides good thermal stability and safety but suffers from lower energy density and a shorter lifespan. LiFePO4, or LFP, is known for its excellent thermal stability and safety, making it suitable for electric vehicles, though it has a lower energy density than other CAMs. LiNiMnCoO2, or NMC, balances high energy density and thermal stability, but cobalt’s cost and resource availability can be a significant drawback. These diverse chemistries allow for customised solutions in different applications, driving advancements in energy storage technology.
CAM production in India
The production of CAM in India is increasing, and it is aimed at reducing dependence on imports, particularly from China. India is positioning itself at the forefront of innovation in the energy storage industry, with a select number of players now engaged in manufacturing cathode materials. The collective aim is to manufacture cutting-edge battery materials for the rapidly growing demand for EVs and other energy storage applications.
For instance, Tata Chemicals Limited (TCL), a subsidiary of the Tata Group, has signed a Memorandum of Understanding (MoU) with the Indian Space Research Organisation (ISRO). Under this agreement, TCL will receive the transfer of ISRO’s lithium-ion cell technology, developed by the Vikram Sarabhai Space Centre (VSSC). Tata Chemicals will adapt this technology to explore its feasibility for manufacturing lithium-ion cells domestically in India. It was originally used to produce space-grade lithium-ion cells for rockets and satellites.
India currently has limited battery component manufacturers, making it reliant on imports. A robust domestic supply chain will reduce import costs, enhance energy security, and promote innovation within the country. It will also create jobs, stimulate local economies, and position India as a competitive player in the global battery market. The move will strengthen India’s technological capabilities and provide a self-reliant energy future.
India’s strategy for CAM production requires producing a sustainable ecosystem. This holistic approach includes support for upstream suppliers, such as pre-CAM producers, and downstream participants, including battery recyclers. Expanding the scope of the PLI scheme for Advanced Chemistry Cell (ACC) to include smaller players and introducing incentives for the entire value chain would prove useful.
Environmental challenges
The rapid expansion of the Li-ion battery industry poses significant environmental challenges with the extraction of primary materials such as lithium, nickel, cobalt, and manganese. The industry is turning towards recycling as a sustainable solution for CAM to address these challenges. Recycling conserves natural resources by reducing the need for primary extraction while curbing energy consumption and lowering greenhouse gas emissions. It reduces waste and pollution and fosters a closed-loop production system. The system ensures a stable supply chain of critical materials and promotes a circular economy approach.The production of lithium-ion batteries involves extracting lithium, a finite resource often found in fragile ecosystems. The mining process can cause deforestation, soil erosion, and water contamination. Recycling lithium-ion batteries is essential for both environmental and economic reasons. Recycling also reduces the need for resource-intensive mining and minimises environmental impact while preventing the release of toxic substances. Leading lithium recycling companies in India include Attero Recycling, Tata Chemicals, and Lohum Cleantech.
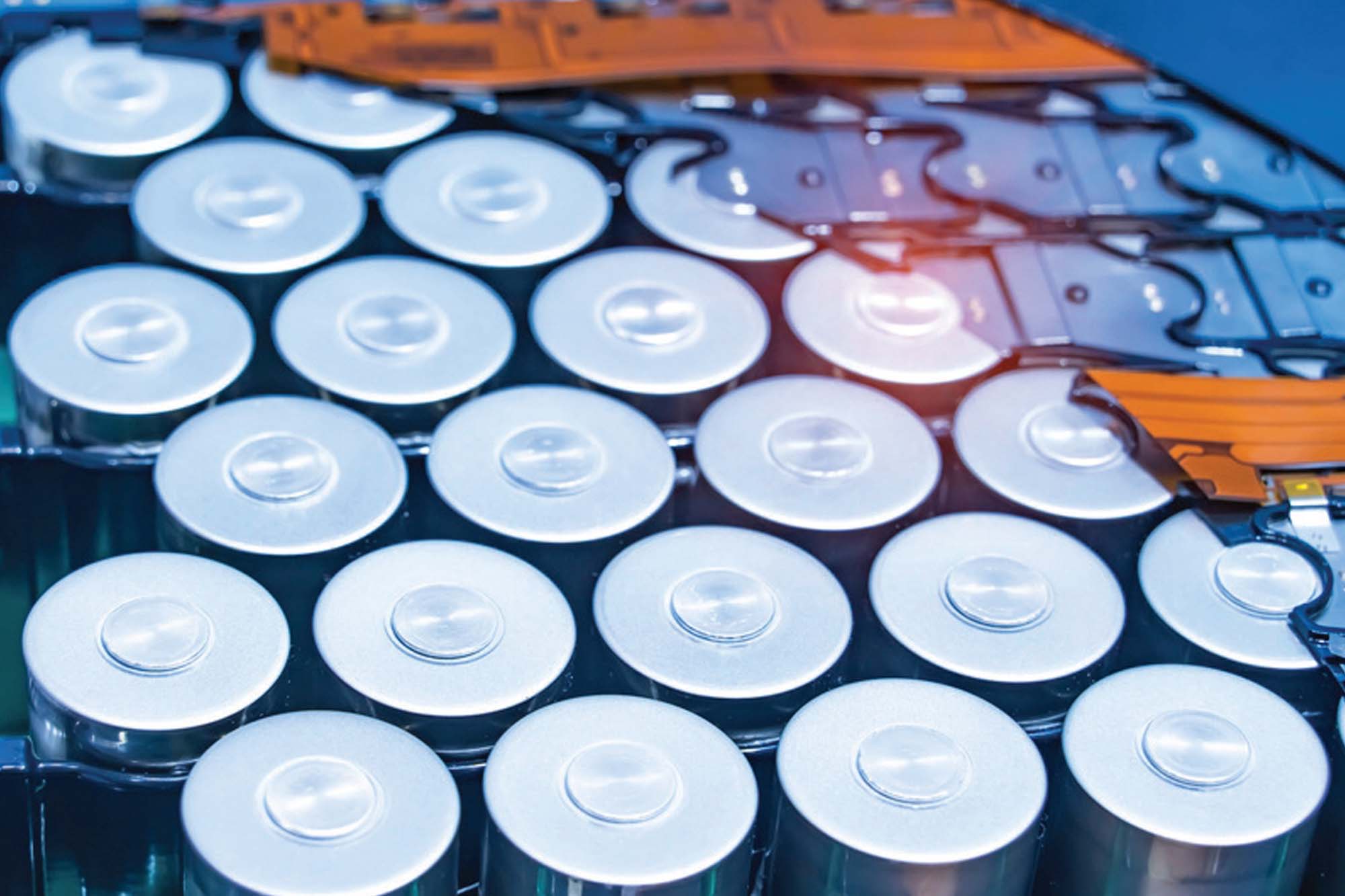
Global trends in battery recycling
Europe and China are leading the charge in battery recycling, supported by robust regulatory frameworks and policies. Europe mandates producers to manage the end-of-life of their batteries responsibly. In contrast, China, the largest EV and battery market, requires manufacturers to recycle a large chunk of used batteries by 2025. The Department of Energy in the United States has focused on developing recycling technologies to promote sustainability.
With Nanotech Energy, BASF, a global chemical company, launched a closed-loop battery recycling system in North America. This system is aimed at reducing the carbon footprint associated with battery production while focusing on recovering valuable metals from end-of-life batteries. The company uses recycled materials such as lithium, cobalt, and manganese to produce cathode active materials instead of depending on mined metals for new lithium-ion batteries. BASF and Nanotech Energy are collaborating with American Battery Technology Company (ABTC), a battery recycling startup, and TODA Advanced Materials, a manufacturer of precursor cathode active materials (PCAM) used in lithium-ion batteries.
Domestic EV battery production
The transition of India to becoming self-sufficient in EV battery production is gaining momentum. India is now investing heavily in local cell manufacturing facilities, whereas historically, it relied on imports from Greater China, South Korea, and Japan. It is predicted that 13% of total EV battery cell demand will be sourced domestically, with the rest still imported by 2030. However, the Indian government’s proactive stance on electrification, through policies like the Production-Linked Incentive (PLI) scheme for advanced chemistry cell (ACC) battery storage and the Faster Adoption of Manufacturing Electric Vehicles (FAME) scheme, is encouraging investments and strategic partnerships.
EV battery chemistry and mineral sourcing
The choice of cathode material for EV batteries influences performance, cost, and environmental impact. In India, LFP (Lithium Iron Phosphate) and LMFP (Lithium Manganese Iron Phosphate) chemistries dominate in lower vehicle segments due to their thermal stability and cost-effectiveness. By 2030, high-nickel NCM (Nickel Cobalt Manganese) is expected to capture a greater market share in higher vehicle segments due to its higher energy density, making it suitable for longer-range travel. Mid-nickel NCM and NCMA (Nickel Cobalt Manganese Aluminium) are also gaining traction in mid-range vehicle segments.
The ethical sourcing of battery minerals is growing. Narratives around lithium, nickel, and cobalt are scrutinised under ESG (Environmental, Social, and Governance) principles, compelling suppliers and corporations to balance cost efficiency with ethical responsibility. India has the potential to localise mineral supply by an estimated 5.9 million metric tonnes with lithium reserves in Jammu and Kashmir. However, the complexities of extraction and environmental impact in these mountainous regions pose significant challenges.
Conclusion
CAM production in India can be a game-changer for the global energy storage market. India can reduce import dependence, promote a circular economy, and contribute to the supply chain of critical battery materials with indigenous production. The commitment to sustainability and technological advancement will position India as a leader in the energy storage industry.
Cookie Consent
We use cookies to personalize your experience. By continuing to visit this website you agree to our Terms & Conditions, Privacy Policy and Cookie Policy.