Industrial automation strategies step up manufacturing and production lines
By OEM Update Editorial March 30, 2024 12:17 pm IST
Sameer Gandhi, Managing Director, Omron Automation India, says that adopting industrial automation presents numerous benefits for organisations, including increased productivity and improved safety standards. From training and integration issues to cybersecurity concerns, proactive strategies are essential for overcoming the obstacles and maximising the potential of automated systems.
How do PLCs enhance industrial automation systems’ efficiency, safety, and adaptability?
PLCs are a key component of industrial automation systems, providing the intelligence and control necessary to optimise production processes, improve efficiency, ensure consistency in product quality, and enhance overall safety in industrial settings. PLCs function by orchestrating control logic, enabling real-time operation, and ensuring adaptability through programmability. They are aptly called the backbone of all manufacturing.
PLCs serve various functions in industrial settings, starting with their role in implementing control logic for diverse processes. They manage machinery operations, monitor sensor inputs, and activate outputs to control actuators like motors and valves. Crucially, PLCs operate in real-time, processing inputs with precision to ensure quick response times and accurate timing, such as in manufacturing and production lines.
Their flexibility allows easy programming adjustments to adapt to different manufacturing processes without requiring physical rewiring. Additionally, PLCs facilitate communication with various industrial devices and systems, enabling centralised monitoring and control across the entire industrial setup. Designed for durability, some PLCs can withstand harsh environmental conditions and operate reliably over extended periods with minimal maintenance. Moreover, PLCs contribute to safety measures by implementing features such as emergency stop circuits and safety interlocks to protect equipment and operators from potential hazards.
How does sensor integration within industrial automation systems improve safety and operational efficiency?
Integrating sensors and actuators within industrial automation systems plays a key role in enhancing operational efficiency. It does this through real-time data acquisition, enabling process control, optimising maintenance schedules, enhancing energy efficiency, ensuring safety, and ultimately maximising productivity and quality in industrial settings.
Sensors primarily gather data from the industrial environment, encompassing parameters like temperature, pressure, position, speed, and other pertinent variables. This real-time data furnishes the automation system with insights to make informed decisions and forecast maintenance needs, averting unexpected breakdowns, minimising downtime, and refining maintenance schedules to bolster efficiency. Their ability to deliver precise and accurate measurements is indispensable for upholding quality standards and attaining optimal performance in industrial processes.
Furthermore, sensors furnish feedback to the automation system regarding the ongoing status of industrial processes. They detect unsafe conditions such as overloads, overheating, or obstructions and instigate appropriate responses to safeguard equipment, products, and personnel. This feedback loop facilitates real-time monitoring and control of processes, enabling swift adjustments to optimise efficiency and productivity.
Sensors are also utilised to monitor energy consumption in industrial processes and identify opportunities for energy savings. By analysing this data from sensors, automation systems can optimise energy usage, reduce waste, and improve overall energy efficiency in the industrial setting.
Under the purview of the automation system, actuators enact precise adjustments based on sensor feedback to ensure consistent and accurate operation. They can also be deployed to institute safety mechanisms, such as emergency stops, to prevent accidents and ensure a safe working environment.
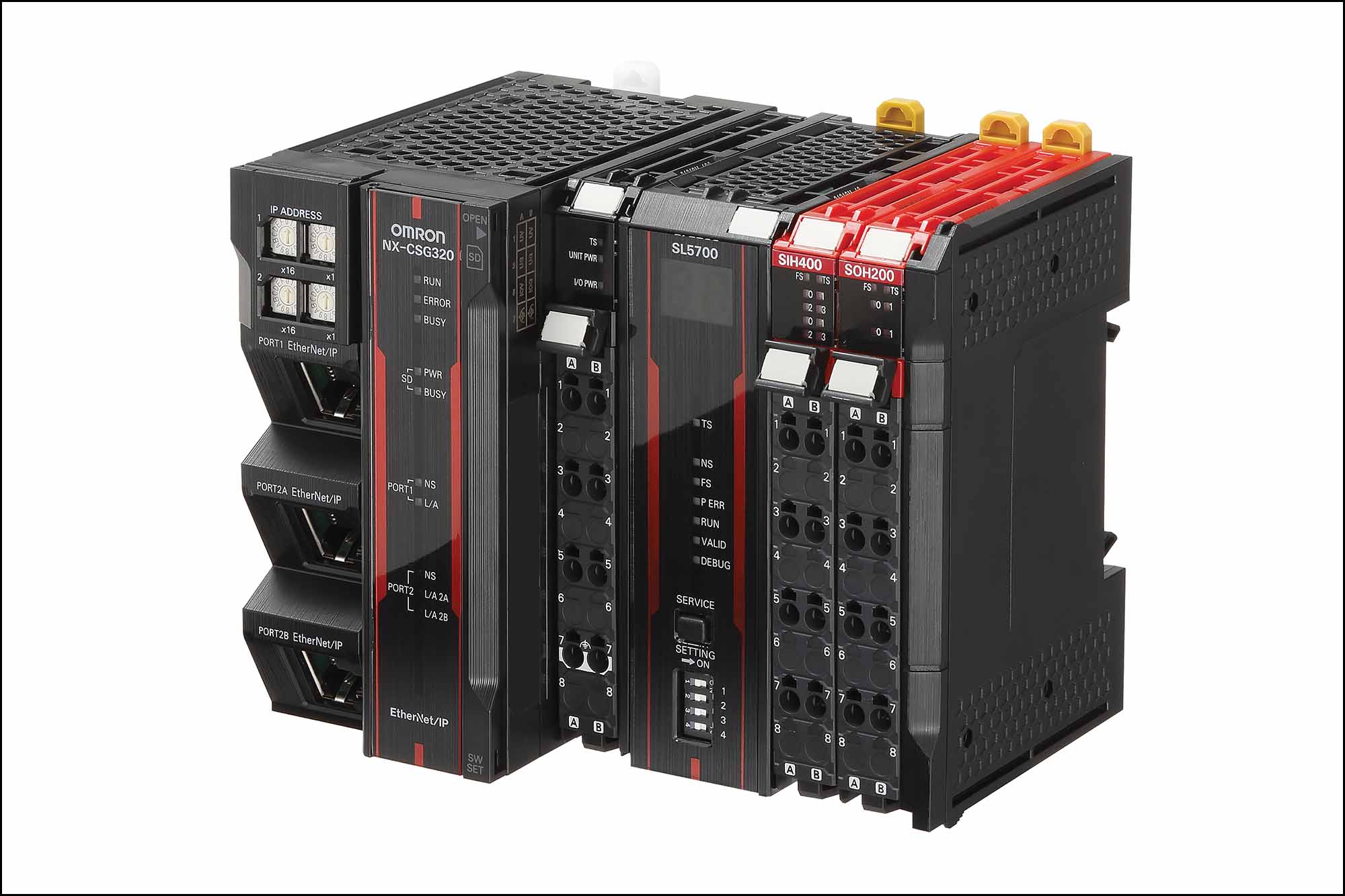
How do implementations of SCADA contribute to the monitoring and controlling of industrial processes?
SCADA (Supervisory Control and Data Acquisition) systems are crucial in overseeing and managing industrial processes through real-time data collection, monitoring, control functionalities, alarm handling, historical data examination, integration with diverse systems, and remote access features. These can typically connect to several PLCs over a network and provide a consolidated control and operations window for plant operations.
SCADA systems serve multiple purposes within industrial operations. They start by acquiring data from various sensors and devices distributed throughout the industrial environment. This data encompasses parameters such as temperature, pressure, and flow rates, providing operators with a real-time, comprehensive overview of industrial processes.
Moving forward, SCADA systems offer real-time monitoring capabilities through visualisations, trend analysis, alarms, and reports. This enables operators to centrally oversee the status of processes, equipment, and critical parameters, allowing them to detect and address issues or deviations swiftly.
Moreover, SCADA systems provide control functionality, empowering operators to manage industrial processes and equipment remotely. Operators can use the SCADA interface to adjust setpoints, initiate equipment actions, and control valves, ensuring optimal operation and efficiency.
In addition, SCADA systems excel in alarm management, promptly notifying operators of abnormal conditions or critical events within industrial processes. These alarms can be tailored based on predefined thresholds, enabling operators to respond to issues and prevent potential disruptions or failures promptly.
Furthermore, SCADA systems store historical data from industrial processes, facilitating trend analysis, pattern identification, and performance optimisation over time. This aids in process improvement, efficiency enhancement, and informed decision-making for future operations.SCADA systems integrate seamlessly with other systems, such as PLCs, MES, ERP, and maintenance management systems. This integration fosters smooth data exchange and coordination between different organisational departments and functions.
Finally, SCADA systems often support remote access capabilities, allowing authorised personnel to monitor and control industrial processes from any location with internet connectivity. This flexibility enables swift issue response, enhances operational efficiency, and reduces the need for on-site presence.
How do digital technologies enhance efficiency and quality control in manufacturing processes?
AI and ML technologies are crucial in enhancing decision-making processes and predictive maintenance within the manufacturing sector. They enable proactive maintenance strategies, streamline operations, automate quality control, optimise supply chain management, and offer valuable insights to support data-driven decision-making. By harnessing these technologies, manufacturers can boost efficiency, cut costs, elevate product quality, and maintain competitiveness amidst the dynamic manufacturing landscape.
These technologies leverage algorithms to scrutinise sensor data from machinery and equipment, detecting anomalies or unusual patterns that may signify potential failures. Early identification of such anomalies allows for predicting future equipment failures, facilitating proactive maintenance scheduling to avert unexpected downtime. Furthermore, AI systems extend beyond predictive capabilities to provide prescriptive insights, offering recommendations for optimising processes or addressing issues.
These recommendations stem from data analysis, pattern recognition, and consideration of various factors to suggest the best course of action.
Manufacturers benefit from data-driven decisions to enhance productivity, quality, and resource utilisation. Examples include computer vision and machine learning for quality inspection and defect detection during manufacturing processes. Manufacturers can ensure consistent product quality and minimise defects by automating quality control tasks.
ML also proves invaluable in analysing data to forecast supplier performance, identify risks, and optimise sourcing strategies.
How can the challenges faced in adopting industrial automation be addressed, and how can the benefits of automated systems be maximised?
Industrial automation offers organisations manifold advantages, including heightened productivity, enhanced quality, cost reduction, and improved safety standards. Nevertheless, several challenges must be tackled to ensure seamless implementation.
Firstly, adequate training and upskilling programs must equip employees with the requisite competencies for operating and maintaining automated systems. Additionally, addressing concerns and resistance to change through transparent communication and comprehensive training sessions is integral to the Change Management process.
Another challenge lies in integrating new solutions with existing systems. Collaborating with vendors and experts to devise a seamless integration plan is crucial for minimising disruptions and maximising the benefits of automation.
Furthermore, robust cybersecurity measures are essential to safeguard automated systems against cyber threats and attacks. It is imperative to regularly update software and firmware to address vulnerabilities and ensure system security.
Conducting a thorough cost-benefit analysis is also vital to assessing the return on investment (ROI) of automation projects. This involves considering long-term benefits such as heightened efficiency, reduced downtime, and enhanced quality alongside upfront costs. Developing a proactive maintenance strategy is equally crucial to ensuring the reliability and longevity of automated systems.
By proactively addressing these challenges and implementing best practices, organisations can effectively navigate the adoption of industrial automation and maximise the benefits of automated systems in their operations.
Cookie Consent
We use cookies to personalize your experience. By continuing to visit this website you agree to our Terms & Conditions, Privacy Policy and Cookie Policy.