Schmersal unveils cutting-edge 3D camera technology
By OEM Update Editorial January 25, 2024 6:44 pm IST
Schmersal Group’s latest addition, the AM-T100 3D camera, leverages Time-of-Flight technology for real-time, millimeter-accurate imaging. Redefining automation enables object detection, fill-level assessments, and dynamic spatial monitoring in industrial settings.
A safety technology provider’s range now encompasses a 3D camera capturing real-time processes, expanding their optoelectronic system components for intralogistics and automation. High-performance optoelectronic sensors are indispensable in industrial automation, detecting items on machines and conveyors and increasingly ensuring machine safety. Non-contact safety barriers, grids, and curtains offer advantages over traditional hazardous area safeguarding with doors. They also grant operators a clear process view and allow system flexibility with functions like muting or blanking specific safeguard areas.
Optoelectronics system
A safety technology supplier has broadened its product line by incorporating a 3D camera that records live processes. This expands its range of optoelectronic system elements for intralogistics and automation. High-performance optoelectronic sensors are critical in industrial automation and are used to detect components and load carriers on machines and conveyor belts. These sensors are increasingly vital for machine safety. Non-contact safety light barriers, grids, and curtains offer advantages surpassing traditional safeguarding methods with doors in hazardous areas. They provide operators with a clear view of processes and enable additional workflow flexibility through functions such as muting or blanking specific areas of the safety system.
The AM-T100 camera resulted from a collaborative project with a longstanding development partner. This allowed Schmersal to incorporate the customer’s specifications directly into the camera’s development while leveraging the partner’s expertise in camera technology.
The AM-T100 is equipped with a Sony DepthSense sensor. It uses time-of-flight (TOF) technology, the runtime measurement of emitted light pulses within the infrared range (850 Nm), reflected by the detected objects. This enables high-speed creation of a 3D scene image with millimetre accuracy available as a point cloud. With an image frame rate of up to 60 fps, this kind of 3D ToF camera can determine the positions and dimensions of objects in real-time, e.g., the robot’s position and stacking height of the palletised boxes. All this needs is one recording.
Additionally, the camera can peer inside containers or sizable load carriers, identifying their current fill level. Furthermore, it enables the measurement of volume for general cargo and oversees the overview of staging areas in production, assembly, storage, and order-picking processes from an elevated perspective. Other uses include the capture of dimensions and surface quality. With IR illumination and an image resolution of 640 x 480 pixels, the AM-T100 achieves a visual range of 67° x 51° at a range of 8.3 metres.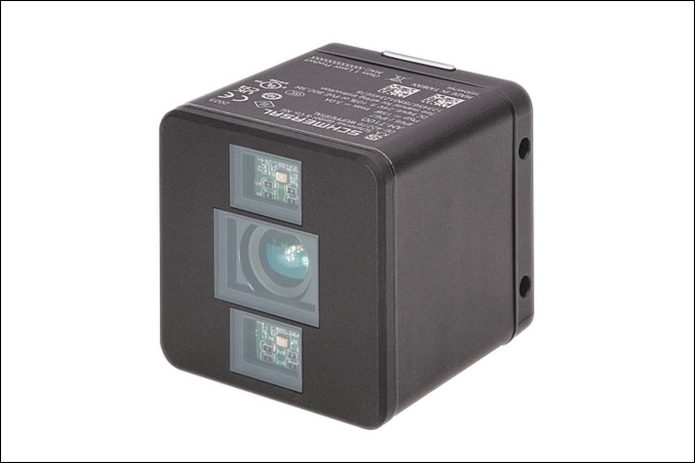
Enhanced performance through dynamic software capabilities
What boosts the performance of the 3D camera is its software, which allows the user to define and monitor things like 3D zones within a space in real time and as a moving image.
If the camera detects an object within the zone, it will switch digital outputs. In addition, digital inputs allow for switching back and forth between different 3D zones. An integrated Software Development Kit (SDK) supports software developers and system integrators with software configuration and application creation.
High-performance algorithms can pre-filter the data so that the AM-T100 can be adapted to different ambient conditions. The image data are captured and transmitted via GeniCam so that they can be analysed by common image processing software. An Ethernet interface enables rapid and extensive data transmission and a 24 V power supply if required (Power over Ethernet).
The camera introduces numerous automation solutions in logistics and assembly lines, establishing the prerequisites for swiftly and accurately capturing the present state within a process. This aids in forming an exact representation of the current status, enabling subsequent actions in processing, assembling, and managing products, containers, and packaging units to commence efficiently.
Cookie Consent
We use cookies to personalize your experience. By continuing to visit this website you agree to our Terms & Conditions, Privacy Policy and Cookie Policy.