Right lubrication enhances hot forging quality and productivity
By OEM Update Editorial January 12, 2024 7:29 pm IST
A forging die lubricant is a chemical compound designed with a specific formulation to conduct the forging process within the established limits and parameters set by the forging industry.
Lubrication is crucial in ensuring the quality and productivity of the hot forging process, which operates at exceptionally high temperatures. For instance, hot forging occurs at temperatures as high as 1250 degrees Celsius, while Al-alloys are forged at 360 to 520 degrees Celsius and Cu-alloys at 700 to 800 degrees Celsius.
These extreme temperatures are necessary to avoid strain hardening of the metal during deformation. Consequently, selecting the appropriate lubricants for specific application areas is essential to achieve optimal outcomes, making lubrication a challenging but indispensable task in the hot forging process.
A forging die lubricant is a chemical compound designed with a specific formulation to conduct the forging process within the established limits and parameters set by the forging industry.
Characteristics of ideal lubricants are as follows:
• Reduce the sliding friction between dies and the workpiece (Load and energy requirement will be reduced).
• Works as a parting agent between the die and workpiece. (Prevents sticking).
• Works as an insulator.
• It should develop a balanced gas pressure (Especially in hammer forging with the impression (this is called Dieseling effect).
• Should be Non-Abrasive and Non-corrosive.
• Shouldn’t create smoke (Pollution free).
• Availability with reasonable cost.
Water-based graphite lubricants: This type of die lubricant is a suspension that combines ultrafine graphite powder with specific additives and water. It is widely known and extensively used due to its popularity. The lubricant can be applied through spraying, brushing, or manual daubing. It is particularly suitable for demanding and essential press forging operations. Notably, this type of lubricant can be highly diluted in water, making it cost-effective for lubrication per tonnage while prolonging the die’s lifespan.
Water-based non-graphite lubricants: These lubricants are unique water-soluble polymer-based formulations, ideal for shallow cavity dies. They are widely regarded as the most cost-effective option because of their exceptional cooling and lubricating properties.
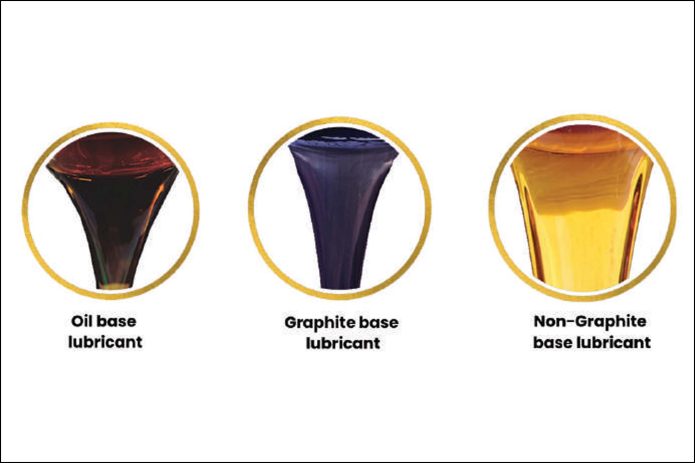
Other Products
Oil-based lubricant: For the lubrication demands in the forging process, special additives are blended with graphite, using either base oil or vegetable oil as a base. This creates the suspensions mentioned earlier. Some graphite-free variants still offer exceptional release properties and improved material flow. These versatile lubricants find utility in various applications, including deep cavity hammer forgings, heavy stainless-steel forgings, critical brass and aluminium forgings, and deep extrusions.
Spray guns & spraying equipment: Sunlub Technologies provides a comprehensive selection of die lubricants along with cost-effective application solutions through Spray Guns & Spraying Equipment. Their offerings include Single side & Dual side spray guns, Spray systems with pressure feeder tanks (45 & 75 Litres capacity), and Spray systems with open tanks (100 & 200 Litres capacity) equipped with AODD pumps. Sunlub Technologies maintains a widespread sales network throughout India to ensure efficient service and quick response.
For more information: Sunlub Technologies, Plot No. L-89, MIDC Industrial Area, Ahmednagar, Maharashtra – 414111
www.sunlubtechnologies.com; info@sunlubtechnologies.com
Cookie Consent
We use cookies to personalize your experience. By continuing to visit this website you agree to our Terms & Conditions, Privacy Policy and Cookie Policy.