Inductive energy-saving technology for extruders, injection, and blow moulding machines
By OEM Update Editorial September 18, 2023 5:18 pm IST
The technological evolution of heating in industrial processes involves replacing obsolete dissipative systems (resistors) with advanced energy-saving solutions. The inductive extruders and plasticising barrels transform plastic machinery, elevating productivity and efficiency while reducing operational and maintenance expenses.
The rising energy cost and increasing global awareness about energy conservation drive the adoption of more efficient processes.
The principle of electromagnetic induction
Inductive technology is gaining popularity in various applications, exemplified by the shift from traditional gas cooktops to induction hobs in households. This technology utilises magnetic induction to safely and effectively transfer energy from a coil to a ferromagnetic material. The energy transferred to the load is transformed into heat generated inside the metal. This direct energy transfer maximises heating efficiency, reduces heating time, and minimises energy wastage.
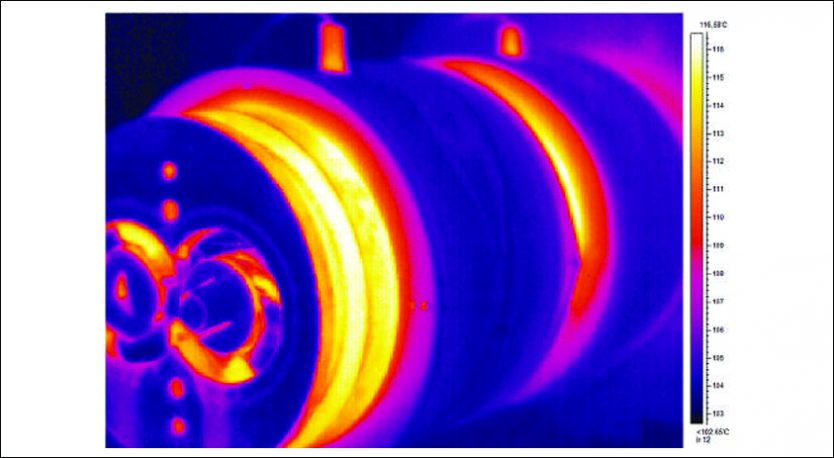
Induction technology for plastic machinery
In the realm of plastic machinery, Atos Induction has harnessed the benefits of magnetic induction to create an innovative heating solution for a common industrial process: plasticising systems. This Inductive technology applied to plasticising barrels offers several advantages over traditional resistive heating systems:
· Energy saving up to 30% on heating energy consumption
· Uniform heat distribution
· 30 percent less of installed electrical power respect equivalent machine with resistors
· Significantly faster heating, less than half time if compared to resistors
· High precision of temperature control, thanks to the absence of thermal inertia and instantaneous heat transfer of inductive technology
· Extended operational lifespan due to the reduced thermal stresses of the inductive coil.
The solution engineered by Atos Induction allows replacing heating elements in both new and existing machines, using the same timed or thermo-regulated control logic of traditional resistive systems.
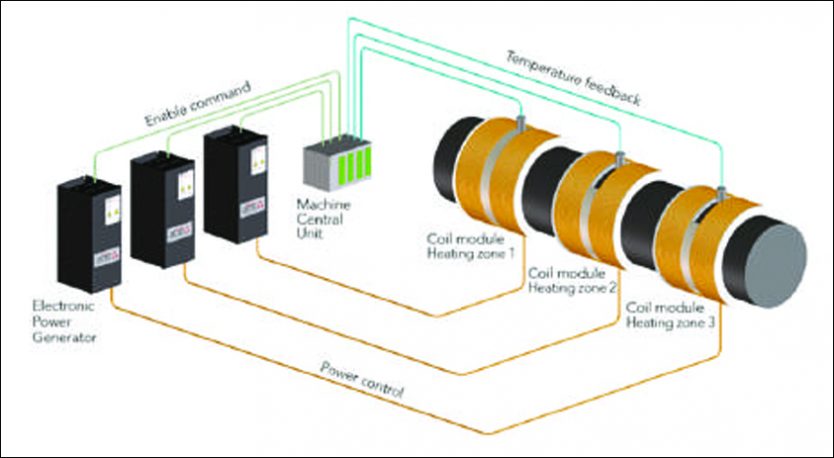
This solution typically involves one or more coils, depending on the number of barrel zones needing heating. An electronic power generator powers each coil. The machine’s central unit manages temperature regulation for each zone, adjusting the power generator based on temperature feedback.
The electronic power generator self-adapts the current modulation according to the characteristics of the ferromagnetic material to be heated to achieve maximum efficiency in any working condition.
The inductive coil is wound on highly insulating materials to minimise heat loss from the barrel to the environment. When a large area of the plasticising cylinder operates at a single temperature, inductive coils simplify the machine control scheme and reduce the installed electrical components since a single coil can cover lengths up to 700 mm.
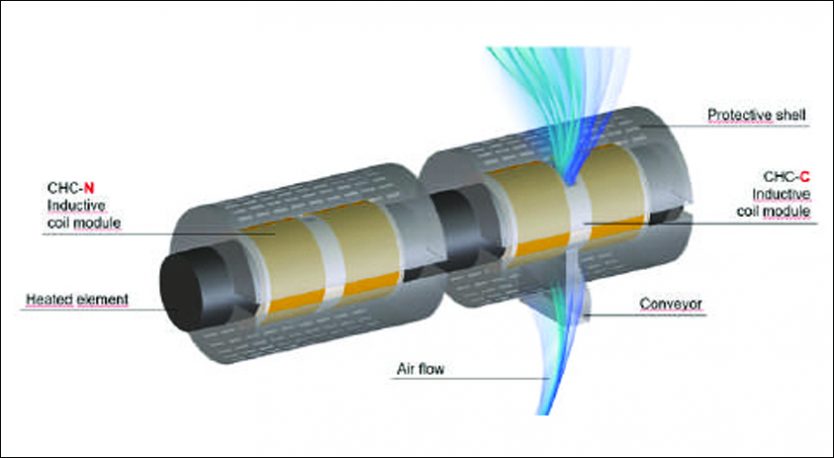
The modular construction technology of the inductive coils allows an easy installation on both cooled and uncooled plasticising barrels:
· CHC-N coils are designed for temperature sensor installation and are suitable for those zones of the plasticising barrel that do not require cooling.
· CHC-C coils are provided with openings for airflow and temperature sensor installation. The special internal structure allows air to be conveyed directly over the plasticising barrel, guaranteeing faster cooling than resistive systems.
Inductive energy-saving solutions
The focus on environmental pollution and the current escalation of energy prices is driving markets towards more efficient technologies and solutions. Comparative analyses performed on a 300-ton plastic injection machine revealed that the energy consumption of inductive coils had been lower than 30 percent concerning ceramic resistors, leading to annual savings of 28 MWh.
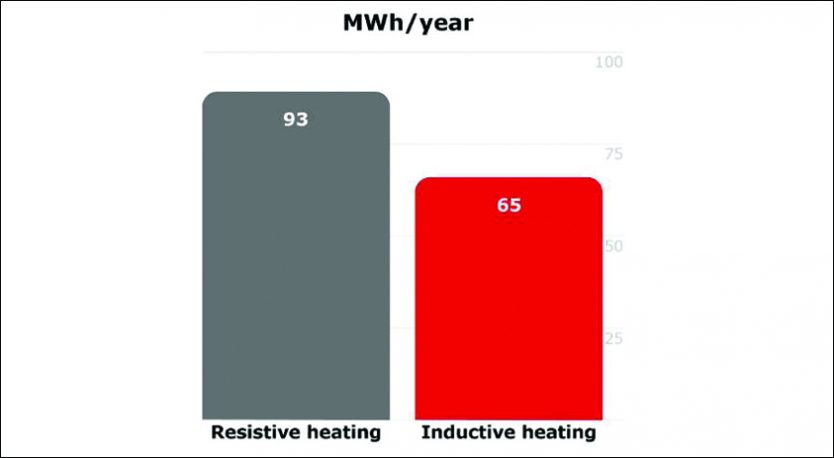
Energy consumption of 300 tons plastic injection moulding machine with traditional heating system and inductive heating system
Atos Induction offers energy-saving solutions to equip the next generation of induction-based plastic injection and inductive extruder machines.
For more information, visit: www.atosinduction.com
Cookie Consent
We use cookies to personalize your experience. By continuing to visit this website you agree to our Terms & Conditions, Privacy Policy and Cookie Policy.