Smart factories need advanced IoT solutions along with AI and ML
By OEM Update Editorial December 12, 2022 10:55 am IST
The Industrial Internet of Things enables linked equipment to collect data using sensors and gateways, which can then be analysed using advanced analytics and modern data management solutions.
Smart factories imply the highest level of digitalisation.
Smart factories mean the highest level of integration of digitalisation solutions to current processes. Digitalisation includes data collection, analysis and then insight creation from the collected data to improve the overall efficiency of the processes, perform diagnostics and monitor progress, among other things. The backbone of such a factory would be advanced IoT solutions and AI & ML algorithms for analysing the data. For instance: Companies moving towards automated micro-factories that require minimal human intervention can be controlled remotely and operate in decentralised locations allowing a robust supply chain and globalised operations.
Industry 5.0 undertakes a human-centric approach.
Industry 5.0 is a newly emerging idea with advantages for businesses, employees, and society. The key goals of this new framework are to empower employees and create an environment focused on people. This will enable and facilitate the transfer of knowledge from humans to robots, the adaptation of robot behaviour to meet the demands of humans, and the enhancement of working circumstances. There will be a dual transition where the digital systems will undertake a more human-centric approach. At the same time, humans will be upskilled to include digital knowledge, ultimately leading towards a more sustainable circular economy. For instance, an elementary-level example of such a scenario is robotic laparoscopic surgeries being done from remote locations.
Digitisation and robotics for efficient manufacturing and productivity
Digitalisation will allow the acquisition and analysis of data. This includes gathering and acquiring various kinds of useful data from throughout the industry, supply chain, and the globe. The Industrial Internet of Things (IIoT) enables linked equipment to collect data into the system using sensors and gateways. This data can be analysed using advanced analytics and modern data management solutions. Finally, once insights are gained, instructions can automatically be sent to machines and devices within the system. These automated devices are the ones that one would refer to as robotics. These devices can then implement the instruction immediately, solve the identified pain point and the overall efficiency of the process increases drastically.
5G technology advantage to make manufacturing productive
With the wide variety of processes and equipment involved, it will be challenging to incorporate the requirement in the limited communication band of the 4G network. 5G provides significant advantages, including ultra-low latency data transfer and communication, real-time feedback and the ability to incorporate customisations to suit the network requirements. Manufacturing is made more adaptable, mobile, and productive owing to the new 5G communication standard, which provides highly dependable, secure, high-speed data transmission with quick response times. Workers can obtain more information in their field of vision in real-time, for example, by wearing data glasses connected via 5G, which optimises how they monitor and operate machinery.
Digital twins optimise production using simulation.
Digital twins have been of widespread use across industries for decades. One of the most notable contributions would have to be in the Aircraft and Spacecraft industry in the form of simulators. The gap between the actual model and its digital twin is ever-decreasing with the advancement in technologies and mathematical models. In such an ideal scenario where the twin is able to mimic the real-life equipment closely, many benefits can be reaped, which include:
• Better R&D: the wealth of data produced regarding expected performance results facilitates more efficient product research and creation.
• Greater efficiency: continuously increasing the overall production capacity and ultimately achieving peak efficiency.
There is a high focus on sustainability and carbon neutrality. Owing to the COP26 pledges by various countries, OEMs are now moving towards a net-zero-carbon supply chain throughout their operations. Different drivers enabling this transition include Renewable Energy, Electric Transition, Carbon Capture, Reuse and Recycling of materials and increased efficiency of processes.
Another upcoming area is developments in the 3D printing space. This technological development opens doors for manufacturers who need more resources to rent or buy huge warehouse sites. 3D printers assist in reducing the expenses of creating prototypes for new products in addition to producing goods on demand.
Trends in virtual reality, such as Metaverse, are also having an impact on overall product design. Designers can alter things’ looks, feel, and functionalities using artificial reality before creating prototypes. This new pattern will reduce the resources needed to develop Industry 4.0.
Lastly, Industry 4.0 will provide many benefits for consumers. Data gathered from users is heavily influencing manufacturing processes. Products suited to the end user’s needs are being made using the data. This change will increase profits, and more products will be produced as needed. Fewer resources will be wasted when products are produced on demand based on consumer feedback, which reduces the need for storage space. Additionally, it will connect clients globally and provide them with more value.
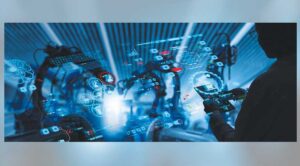
AI technology improves automated procedures.
The speed, power, and flexibility of operational systems that use AI technologies enable them to collect and analyse various data sets and offer timely insights and actionable recommendations. Artificial intelligence is constantly improving and informing automated procedures and intelligent systems in a smart factory. The ability of machine learning to do advanced predictive maintenance is one of the most important advantages it delivers to the smart factory. Ahead of a system failure, alarms can be sent by tracking and analysing production processes. Automated maintenance may be performed in some circumstances, or if it’s necessary, human intervention may be advised.
Digital manufacturing from the viewpoint of collaborative manufacturing
The advent of Industry 4.0 has made it essential for manufacturers to develop solutions that enable employee collaboration and connectivity across locations and job functions—especially when physical distance and stricter employee safety regulations proliferate.
Such a collaboration would enable the employees to access the company’s collective knowledge, consult with specialists remotely, and transform internet of things (IoT) data from the factory floor into long-lasting value will be made possible by the use of digital collaboration tools. Such a collaboration would significantly increase the production potential and create billions of dollars in value.
A manufacturing company becomes more resistant to market demands as its internal cooperation grows. Competitively strong collaborative manufacturing settings may endure various challenges, including labour and supply chain shortages, unforeseen inflationary costs, etc. Greater collaboration makes it possible to increase productivity with a connected workforce strategy.
Cookie Consent
We use cookies to personalize your experience. By continuing to visit this website you agree to our Terms & Conditions, Privacy Policy and Cookie Policy.