Readying high-performance automotive parts while cutting waste with 3D printing
By OEM Update Editorial July 1, 2024 12:17 pm IST
Experience at Siemens, ARK Infosolutions, and Imaginarium has given Nimesh Soni, Manager—Business Development, India & East Asia at Siemens, firsthand insight into the driving forces behind the expansion of 3D printing and prototyping in the automotive industry. It customises high-performance parts and cuts wastage, thus saving costs.
How do you perceive the growth in the 3D printing and prototyping market?
The 3D printing and prototyping market is experiencing exponential growth fueled by technological advancements, cost reductions, and increased adoption across industries. There is a growing demand for customised parts, rapid prototyping needs, and the ability to create intricate designs that are difficult with traditional manufacturing. The expanding range of materials available for 3D printing, with improvements in printing speed and accuracy, further pushes this growth. Automotive, aerospace, medical, and dental industries are integrating 3D printing into their workflows to enhance innovation and reduce lead times.
What is the impact of 3D printing technology on the automotive industry?
3D printing is changing the dynamics of the automotive industry by enabling the production of lightweight, high-strength components, reducing prototyping and manufacturing costs, and fostering innovation. During my previous tenures, I spearheaded the implementation of metal additive manufacturing solutions for automotive clients, empowering them to create complex, high-performance parts with unprecedented design freedom. This technology enables on-demand production, reduces inventory costs, and improves supply chain efficiency, allowing for rapid iteration and customisation of vehicle components. Furthermore, 3D printing facilitates the creation of lightweight parts that fuel efficiency and reduce emissions, aligning with the industry’s sustainability goals.
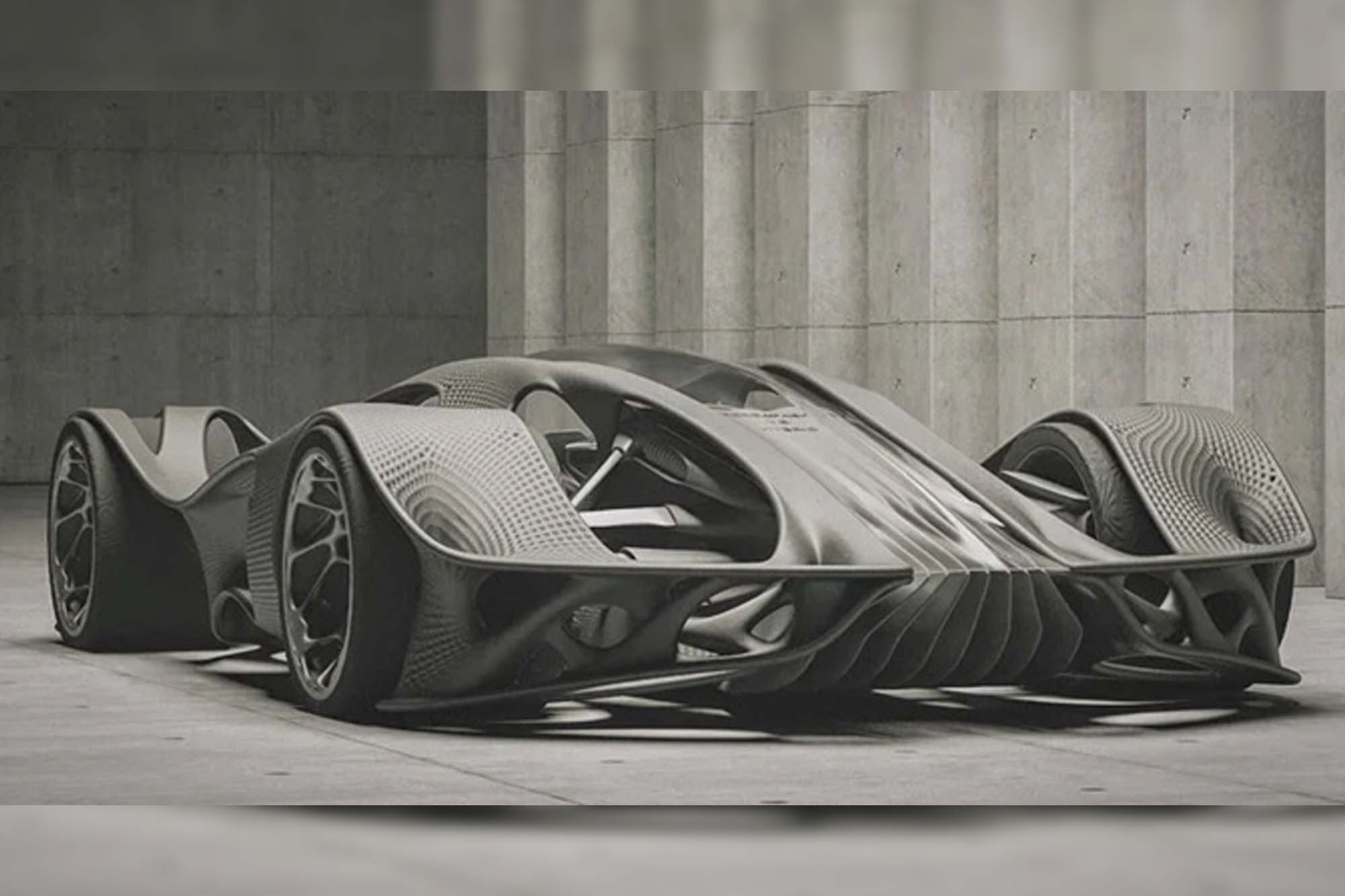
What have been your experience and contributions in the automotive sector, particularly related to 3D printing technologies?
I’ve actively engaged with the automotive sector throughout my career, driving the adoption of 3D printing technologies to transform manufacturing processes. At ARK Infosolutions, I managed the Metal Additive Manufacturing portfolio for SLM Solutions, providing tailored solutions for automotive clients. These solutions covered design optimisation, rapid prototyping, and end-use component production, enabling clients to use the full potential of 3D printing. At Imaginarium, we collaborated with leading automotive manufacturers to deliver high-quality 3D printed parts and components using cutting-edge technologies from brands like Formlabs, Ultimaker, and GE Additive. Our expertise in metal and polymer additive manufacturing helped automotive clients reduce lead times, improve part performance, and push the boundaries of design innovation.
What advancements and future trends can we expect in additive printing and prototyping?
The future of additive printing and prototyping is promising. A broader range of materials, including high-performance metals, composites, and bio-compatible materials, will become readily available for 3D printing. We can also expect faster printing speeds, increased accuracy, and the integration of 3D printing with traditional manufacturing methods, creating hybrid workflows that maximise efficiency and productivity. The rise of multi-material printing and enhanced precision is a testament to this ongoing evolution. Additionally, data-driven optimisation through AI and machine learning will ensure consistent quality and performance, further solidifying 3D printing’s position as a transformative technology.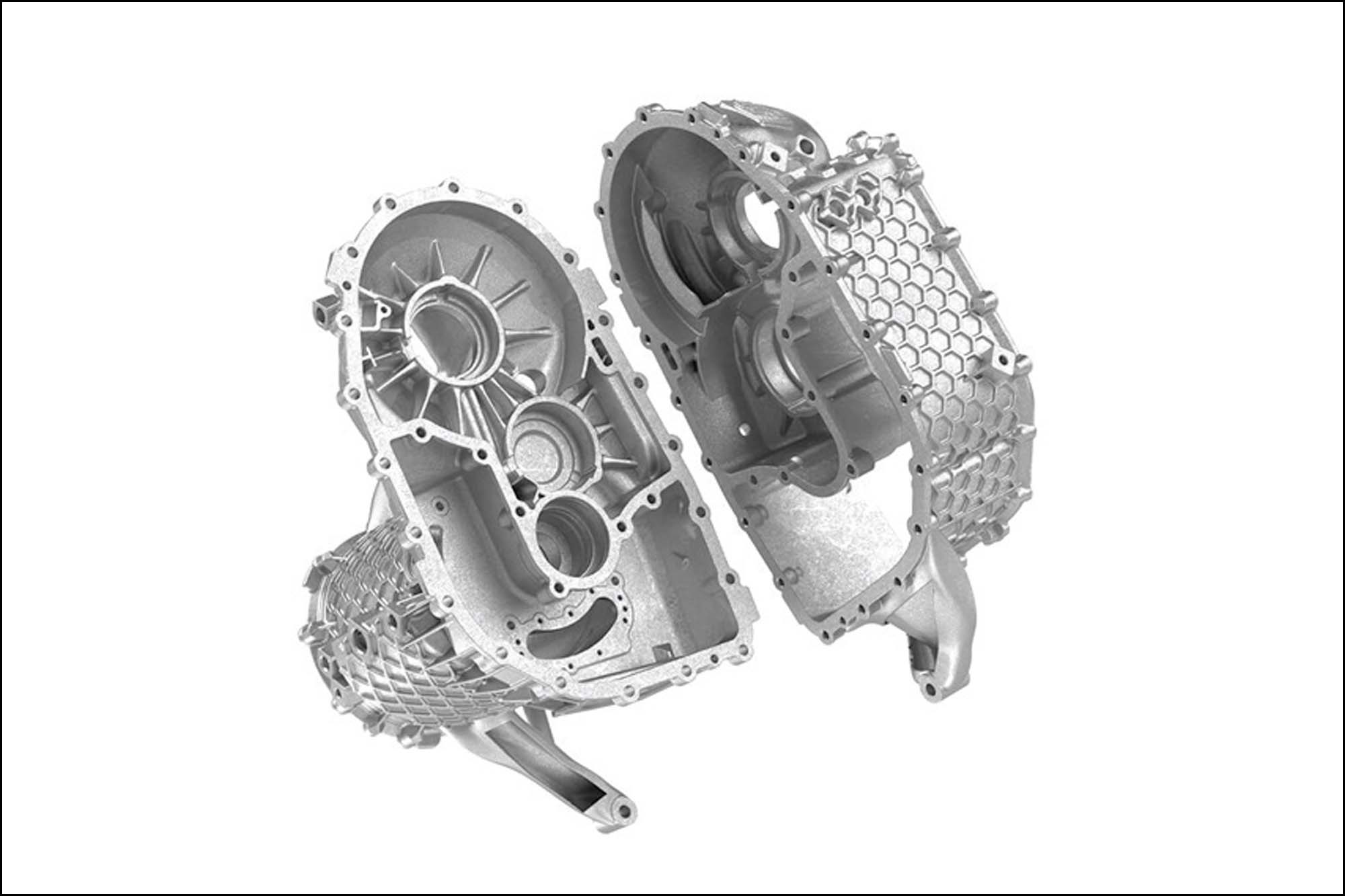
How are manufacturers using 3D printing to improve production processes and reduce costs?
Manufacturers across various industries, including automotive, use 3D printing to streamline production processes and reduce costs. At Imaginarium, we facilitated the rapid creation of custom tools, jigs, fixtures, and end-use parts for automotive manufacturers to produce components on demand and closer to the point of use. This reduces the need for traditional tooling, which can be time-consuming and expensive. Manufacturers can respond quickly to market demands, minimise inventory costs, and expedite delivery times by rapidly iterating designs and producing small batches of parts. Consolidating multiple parts into single, 3D-printed components further simplifies assembly and streamlines production lines, leading to cost savings and improved efficiency.
How do 3D printing technologies contribute to design flexibility and waste reduction in manufacturing?
The adoption of 3D printing technologies is a catalyst for advancements in design flexibility and waste reduction. The power of 3D printing can be harnessed to create complex geometries, organic shapes, and customised components that were previously unattainable through traditional methods. This newfound design freedom allows engineers and designers to create parts for performance, weight, and functionality, leading to innovative and efficient product designs. Additionally, 3D printing’s additive nature reduces waste by using only the necessary material for each part. This sustainable approach aligns with the growing emphasis on environmental responsibility in manufacturing, making 3D printing a key enabler of a more circular and resource-efficient economy.
Cookie Consent
We use cookies to personalize your experience. By continuing to visit this website you agree to our Terms & Conditions, Privacy Policy and Cookie Policy.